Form milling is a specialized milling technique that involves creating a cutter specifically designed for machining a particular profile. Unlike standard milling cutters, form milling cutters can be manufactured to any specific shape required for special profiles—from simple radii and bevels to intricate patterns. This makes the technique highly versatile and enables the production of complex and unique components with relatively short machine times.
This article will discuss what form milling is, how it works, its types, and its advantages and disadvantages.
What Is Form Milling?
Form milling is a manual and, more commonly, CNC milling technique used to create irregular, consistent, and generally complex contours. It involves the use of customized form milling cutters, which are designed specifically for the job at hand. These cutters are often manufactured with unique profiles that suit various applications' particular profile needs. There are also many types of standard form milling cutters, for concave and convex curves, thread profiles, edge beads (such as Roman coving), etc. Form milling is a process with applicability to high-volume production due to the time and cost involved in manufacturing custom cutters. It is also an essential tool in low-volume and high-value production of unique features and forms.
What Is the Purpose of Form Milling?
Form milling serves in machining complex components with irregular and unusual contours. It offers precision and versatility in producing parts that adhere to specific specifications. Form milling is widely used in various industries in which intricate shapes and profiles are required, such as: aerospace, automotive, and medical industries. This technique allows manufacturers to create custom-designed parts with high accuracy and repeatability. However, form milling can be time-consuming and expensive due to the need for custom cutters, making it less suitable for low-volume or shirt delivery cycle production. Despite these limitations, form milling remains a valuable tool for achieving complex designs and shapes in industries in which precision is paramount.
How Does Form Milling Work?
Form milling involves several steps to create complex components with irregular contours. The first step is to design the part in CAD software, creating a 3D model of the component with the desired shape, dimensions, and features. The CAD data is translated into a cutter path and tool selection program, using computer-aided manufacturing (CAM) software. The CAM software takes the 3D model and generates G-code.
The form milling cutter is loaded into the CNC milling machine, along with any required standard cutters. The workpiece or billet is set up on the milling machine. It is securely clamped in a vise, to the bed or fixtured to ensure stability during milling. The position and orientation of the workpiece need to be correctly aligned with the milling machine's axes.
Before commencing cutting, the cutting parameters must be defined. These parameters include: the spindle speed, feed rate, depth of cut, and cutting direction. The milling process can begin once the setup and cutting parameters are finalized and the G-code has been “dry” run. The machine selects the cutter from its rest position and moves the form mill through its assigned toolpath, removing material and creating the desired shape. It is necessary to inspect the cut part for accuracy and perform any post-processing that may be required to complete the part.
How Does Form Milling Differ From Other Types of Milling?
Form milling involves the use of custom cutters that are designed to match the shape of the component being produced. These cutters may perform the entire machining process or they may be used in combination with standard bits, depending on the requirements of the design. Form milling is an intrinsically precise process that can achieve tight tolerances and high-quality surface finishes.
The tooling schedule for a new form milling task can be extended if custom tools are required, as these can be slow to produce. Standard form mill cutters for basic profile features are, however, widely available. They also cost considerably more than standard tools.
The process is often faster than more common types of milling methods of achieving the same profile. The often slower feed speeds used in form milling are generally more than compensated by the simplicity of the toolpaths used and the absence of tool changes, as the complex profile is cut with a single tool in progressive passes.
What Are the Different Types of Form Milling Cutters?
Listed and discussed below are the different types of form milling cutters:
1. Concave Cutters
Concave form milling cutters are available in a range of curvature radii and sector depths. The form milling process employs a concave cutter to create convex contours on workpieces. These cutters are designed with a curved concave profile on their cutting edges that matches the desired shape of the convex feature that they cut.
The concave form milling cutter is typically made from high-speed steel (HSS) or a carrier tool that accommodates tungsten-carbide inserts for greater durability and cutting efficiency. The cutter has multiple flutes or insert teeth that remove material. The number of flutes/cutters can vary depending on the complexity of the desired concave shape and the overall size of the tool.
Concave form milling cutters are used in various industries, including: automotive, aerospace, mold-making, and precision engineering. These cutters enable the production of intricate convex features with high precision, tight tolerances, and excellent surface finishes. The use of concave form milling cutters allows manufacturers to create complex components with convex profile features efficiently and accurately.
2. Convex Cutters
Convex form milling cutters are similarly available in a range of curvature radii, though the tips are generally half-round in profile. In this case, the process employs a convex cutter to create concave features. The cut feature section profile precisely matches (and mirrors) the cutting edges of the teeth/inserts of the cutter. The convex form milling cutter is also typically made from HSS, as is a carrier tool that accommodates tungsten-carbide inserts. Like most cutters, they have multiple flutes or insert teeth.
Convex cutters of this type are widely used across most sectors that demand CNC-milled parts with complex profiles. These cutters deliver convex cuts of great precision, tight tolerances, repeatability, and fine surface quality.
3. Corner Rounding Cutters
Corner rounding cutters are a type of form milling cutter used to create rounded corners on components during the milling process. These cutters have a concave quarter-circular profile with a radius that matches the desired corner size. They are typically made from HSS but are also available as HSS carriers that accommodate multiple tungsten-carbide insert cutters for durability and precision.
In form milling, corner rounding cutters are loaded into the CNC milling machine and serve to gradually remove material from a 90° (or more acute) corner to create a smooth radius that blends the two faces. This process is repeated for each corner/edge that requires rounding.
Corner rounding cutters provide an efficient and accurate method for achieving rounded corners with many fewer passes and no aliasing/steps that would generally be expected to result from the use of standard cutters.
How To Choose a Form Milling Cutter?
The selection of form milling cutters falls into two distinct categories. Many off-the-shelf profiles are available for simple shapes such as: radii, gear teeth, and threads. Selection and acquisition are quick and relatively low cost, compared with custom profiles. Such custom profiles must be manufactured to order and must be carefully specified to allow the required form/profile to be extracted from the workpiece. Selection between HSS and insert type cutters is a critical decision that must be carefully considered. Insert tools have a longer life and can handle harder materials. HSS cutters are more easily made and lower cost, but will wear and may not be sharpenable due to profile complexity.
What Is the Importance of Choosing the Right Form Milling Cutter?
Choosing the right form milling cutter is critical as it allows for the creation of the required shape of the feature with high precision. Form milling differs from other types of milling in that it uses specialized cutters whose teeth/inserts are profiled to match the inverse of the shape being produced. This enables the production of complex components with irregular contours using fewer passes and tool changes/orientation moves.
By selecting the appropriate form milling cutter, manufacturers can achieve greater control and accuracy in the milling process, particularly when the custom cutter encompasses several aspects of the desired shape in one tool.
When To Use a Form Milling Cutter?
Form milling cutters are best suited to creating components with intricate and irregular shapes, such as: turbine blades, gears, and molds. They allow for precise replication of complex contours, ensuring accurate dimensions and a high-quality surface finish. Form milling cutters are a preferred option when manufacturing components that do not have standard shapes, such as those with complex compound curvature. The cutters are made to exactly match the specific shape and dimensions of the feature, providing the necessary accuracy and repeatability as an intrinsically tooled function rather than a program execution.
Form milling cutters are capable of achieving tight tolerances and high precision with lower machining effort and skill, producing components of exceptional accuracy. If you need to produce a large number of components with the same shape, form milling cutters are a cost-effective option, delivering consistent results throughout a fast production run.
What Materials Are Suitable for Form Milling?
Form milling can be performed on a wide variety of materials, including: metals, composites, and plastics. Metals that can be used include: aluminum and aluminum alloys, steel and stainless steel alloys, cast iron (gray, nodular, and malleable), brass, bronze, titanium, and chromium alloys. Form milling has the same range of applicability in metal cutting that other forms of milling process enjoy. The limitations that apply generally relate to the hardness of the target material. For example, tool steels can be considered form-millable, but hardened steels are not.
Plastics used include: ABS (acrylonitrile butadiene styrene), PVC (polyvinyl chloride), Nylon (6, 66, 11), PC (polycarbonate), POM (acetal homopolymer and copolymers), PBT (polybutylene terephthalate), and various rubbers (harder rubbers machine more easily, but cryogenic machining allows soft rubbers to be precisely processed in specialist equipment).
Composites can include: carbon fiber, Kevlar®, GRP (glass-reinforced polyester), cermets, and others. Other materials can also be form milled, such as: carbon (for the preparation of complex electrodes for electrical discharge machining) and glass (machining glass is a highly specialist sector with unique skills).
What Are Examples of Industries That Utilize Form Milling?
Form milling is utilized in various industries to create intricate components and parts, such as:
- Aerospace manufacturers use form milling to produce aircraft components such as: turbine blades, engine casings, and wing structures.
- The automotive industry uses form milling for tasks like: manufacturing camshafts, gear teeth, transmission components, and aspects of engine blocks.
- In the medical industry, form milling is used to produce intricate parts for medical devices and implants, including: orthopedic implants, dental prostheses, and surgical instruments.
- Form milling is crucial in tool and molding/casting die making for creating molds, dies, and stamping tools with intricate contours. These tools are used in various industries, including: automotive, aerospace, and consumer goods manufacturing.
- Form milling is used to manufacture electronic device components like: smartphone casings, connectors, and heat sinks.
What Are the Advantages of Form Milling?
Form milling offers several advantages in CNC machining operations:
- Allows for the shaping of irregular contours, including curves and straight lines, using specialized and custom form milling cutters.
- Eliminates the need for multiple milling processes, saving time in production.
- Offers precise and consistent results, ensuring high-precision components with intricate designs and shapes.
- Helps in reducing overall costs by eliminating the need for additional post-processing operations.
What Are the Disadvantages of Form Milling?
The disadvantages of form milling include:
- Similar to other milling processes, form milling requires extensive setup time before use, making individual components high cost and benefitting production costs on larger batches. Additionally, complex programming in G-code and delays in acquiring custom tools will extend this setup time considerably.
- Can be more expensive to set up, compared to some other machining processes. This is a product of the lower availability of standard form tools and the high cost of customized form tools.
- Not considered suitable for low-value and low-volume component production due to the complexity of setup and programming.
- May result in non-uniform cutting force and vibration, which can impact the quality of the machined components.
Are There Precautions in Using Form Milling?
Yes, there are precautions to consider when using form milling, most of which are typical for all milling operations. Form milling requires careful setup to ensure accurate shaping and contouring. Proper alignment of the workpiece and cutter is crucial to achieving the desired results. Form milling can be a costly process when specialized tools or equipment are required. It is important to consider the cost-effectiveness of form milling for each specific application.
Form milling can generate significant cutting forces and vibrations, which can affect the stability of the workpiece and the quality of the surface finish. Proper tool selection, machine setup, and cutting parameters should be considered to minimize these issues.
What Is the Difference Between Form Milling and End Milling?
Form milling and end milling are both machining processes used to remove material from a workpiece, but they differ in their approach and application. Form milling uses a specially designed cutter to create complex and irregular shapes or contours on the workpiece. The form milling cutter has multiple cutting edges that follow the desired shape, allowing for efficient production of intricate geometries. These cutting edges can be on the face of the tool AND the sides, to suit the required form. This process is commonly used in industries such as: automotive, aerospace, and medical, in which precise and unique shapes are required.
End milling, on the other hand, is a more versatile process that uses a cylindrical cutter, known as an end mill, to remove material from the surface of a workpiece using primarily the tool end cutting faces. The end mill has cutting edges on its periphery and bottom, allowing it to cut both axially and transversely. It is primarily used for creating flat surfaces, slots, and pockets, and is suitable for a wide range of materials.
What Is the Difference Between Form Milling and Profile Milling?
Form milling and profile milling are both machining processes used to produce components with intricate designs and shapes. In essence, they are alternative methods each with its applicabilities.
In form milling, specialized form milling cutters with multiple cutting faces that have complex profiles are used. These cutters are designed to reflect the desired shape of the component. Profile milling uses standard end mills or ball mills with a cylindrical shape, making many more passes to closely approximate the required shape.
Form milling involves following a specific contour or shape to create the desired component. The cutter moves along a predetermined path, cutting the material to match the shape of the cutter. Progressive cuts generally increase the cut penetration in one axis only, with identical traverses of the other axes. This means the depth of the cut is increased, but the position of the cutter is otherwise unaltered. Profile milling involves cutting along the outline or profile of the component to remove material and create the desired shape, using many overlapping cuts that are sequenced across multiple axes.
Form milling is common in industries such as: automotive, aerospace, and medical whenever complex contours and shapes are required. It is ideal for producing components with complex or irregular shapes, such as: turbine blades, gear parts, or engine components. Profile milling is more versatile and can be used for creating flat surfaces, slots, pockets, and more complex compound curvatures.
Summary
This article presented form milling, explained it, and discussed how it works and its different types. To learn more about form milling, contact a Xometry representative.
Xometry provides a wide range of manufacturing capabilities, including machining and other value-added services for all of your prototyping and production needs. Visit our website to learn more or to request a free, no-obligation quote.
Copyright and Trademark Notice
- Kevlar® is a trademark of E. I. du Pont de Nemours and Company
Disclaimer
The content appearing on this webpage is for informational purposes only. Xometry makes no representation or warranty of any kind, be it expressed or implied, as to the accuracy, completeness, or validity of the information. Any performance parameters, geometric tolerances, specific design features, quality and types of materials, or processes should not be inferred to represent what will be delivered by third-party suppliers or manufacturers through Xometry’s network. Buyers seeking quotes for parts are responsible for defining the specific requirements for those parts. Please refer to our terms and conditions for more information.
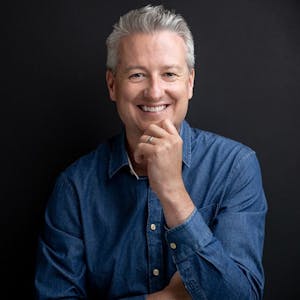