The goal of design for manufacturing (DFM) is to optimize a product's design to save costs, improve efficiency, and streamline the manufacturing process. It entails taking production capabilities and limitations into account from the very beginning of the design process to ensure that the product can be manufactured effectively and inexpensively.
DFM includes several concepts, including choosing easily obtainable and reasonably priced materials, reducing the number of parts, and designing with simplicity of assembly in mind. Enterprises can reduce manufacturing delays, enhance product quality, and eventually obtain a competitive advantage in the market by incorporating DFM principles into the design process.
This article will discuss DFM, what it is, its process, and examples.
What Is Design for Manufacturing?
Design for manufacturing (DFM) is the systematic method of designing parts, components, or products with the primary objective of simplifying manufacturing processes while enhancing product quality and reducing costs. It involves streamlining design elements to facilitate efficient production, minimizing complexity, and optimizing materials and processes. Often interchangeably referred to as design for manufacturing and assembly (DFMA), DFM integrates principles of both manufacturability and assembly into the product design phase.
What Is the Importance of Design for Manufacturing?
Design for manufacturing (DFM) is important because it can save manufacturing costs and complexity by a large margin while maintaining good product quality. Businesses may reduce material waste, improve production procedures, and boost overall efficiency by designing with ease of manufacture in mind. In addition to lowering costs, this strategy promotes a quicker time to market and increased industry competitiveness.
What Is the Purpose of Design for Manufacturing?
The purpose of design for manufacturing (DFM) is to streamline the production process by designing parts, components, or products in a way that facilitates efficient manufacturing while simultaneously enhancing product quality and reducing costs. By simplifying and optimizing the product design, DFM aims to achieve better manufacturability, leading to improved overall product performance and competitiveness in the market.
How Does DFM Differ From Traditional Product Design Methods?
Manufacturability factors are integrated into DFM designs from the beginning, setting them apart from conventional techniques. Simplifying, improving, and refining the design to improve ease of manufacturing is the main focus of DFM, in contrast to traditional methods that prioritize functional elements.
Can DFM Be Applied to All Manufacturing Industries?
Yes, DFM can be applied to all manufacturing industries. DFM principles can add value to product designs regardless of the industry by focusing on optimizing the design for ease of manufacturing. Whether it's automotive, electronics, aerospace, or consumer goods, incorporating DFM tactics can streamline production processes, reduce costs, and improve product quality. This universal applicability of DFM underscores its versatility and effectiveness in enhancing manufacturability across diverse manufacturing sectors.
What Are the Principles of Design for Manufacturing?
The principles of design for manufacturing (DFM) are as follows:
- Process: Selecting the appropriate manufacturing process based on factors such as: quantity, material, surface complexity, and required tolerances.
- Design: Ensuring that the part or product design conforms to good manufacturing principles for the selected manufacturing process, such as: constant wall thickness, appropriate draft angles, and consideration of features like ribs and transitions.
- Material: Choosing the right material for the part or product based on properties such as: mechanical strength, thermal resistance, electrical conductivity, and flammability.
- Environment: Designing the part or product to withstand the intended environmental conditions, ensuring its functionality and longevity.
- Compliance/Testing: Ensuring that the product complies with safety and quality standards through appropriate testing and certification processes.
These principles guide the DFM process, helping to optimize product designs for efficient manufacturing while maintaining quality standards.
How Does Design for Manufacturing Work?
Design for manufacturing (DFM) is the process of efficiently engineering or designing a product, usually in the product design phase, to lower production costs. DFM reduces the requirement for expensive production changes by preventing errors and discrepancies through early resolution of manufacturability concerns.
Where Is Design for Manufacturing Used?
Design for manufacturing (DFM) is used in various industries and sectors, including:
- Automotive: DFM is utilized to streamline the production of vehicles, ensuring efficient manufacturing processes and cost-effective designs.
- Electronics: In the electronics industry, DFM principles are applied to optimize the design and manufacturing of electronic components and devices.
- Aerospace: DFM is employed to enhance the manufacturability of aerospace components and systems, leading to improved efficiency and reduced costs.
- Consumer Goods: DFM techniques are utilized to design and manufacture consumer products, such as: appliances, furniture, and gadgets, for cost-effective production and enhanced quality.
- Medical Devices: In the medical industry, DFM is used to develop medical devices and equipment with optimized designs for efficient manufacturing and regulatory compliance.
Can CAD Modeling Be Used To Simulate Manufacturing Processes in DFM?
Yes, you can use CAD in DFM for manufacturing simulations. CAD tools analyze material choices, part orientation, tooling needs, and production tolerances to include DFM concepts. Furthermore, CAD models can be translated into machine instructions for CNC (Computer Numerical Control) mills and 3D printers using computer-aided manufacturing (CAM) software. This enables virtual testing and process optimization of manufacturing procedures before the start of actual production.
What Is the Process of Designing a Product for Manufacturing?
The process of designing a product for manufacturing involves the following steps:
- Define the product specifications, including: functionality, performance, and regulatory requirements.
- Generate and evaluate multiple design concepts to meet the identified requirements.
- Develop a detailed design based on the chosen concept, including: dimensions, materials, and manufacturing methods.
- Conduct simulations, prototyping, and testing to ensure the design meets performance and quality standards.
- Incorporate DFM principles to optimize the design for efficient and cost-effective manufacturing.
- Plan the production process, including: selecting suppliers, scheduling, and resource allocation.
- Build prototypes for further testing and validation before full-scale production.
- Implement the finalized design into mass production, monitoring quality and making any necessary adjustments.
- Gather feedback from manufacturing and make iterative improvements to the design and production process.
What Is the Application of the Manufacturing Design Process?
The application of the manufacturing design process involves:
- Design for Manufacturing (DFM): Considering manufacturing constraints during product design to optimize manufacturing efficiency.
- Design for Assembly (DFA): Optimizing parts or subsystems for ease of assembly, reducing manufacturing costs and assembly time.
- Integration of CAD, CAM, and FEA Tools: Utilizing computer-aided design, manufacturing, and finite element analysis for efficient product development.
- Optimization of Manufacturing Procedures: Minimizing manufacturing time and costs while maintaining quality.
- Reduction of Manufacturing Costs: Identifying opportunities to reduce costs through design improvements.
What Are the Advantages of Design for Manufacturing?
The benefits of DFM, include:
- Helps in identifying potential manufacturing constraints early in the design phase, such as: material availability, tooling limitations, and production capabilities.
- Companies can minimize production costs associated with rework, scrap, and production delays.
- Ensures that products are designed in a way that is compatible with the manufacturing process, reducing the likelihood of defects and improving overall product quality.
- Designing products with assembly in mind can streamline the assembly process, reducing assembly time and labor costs.
- Considering manufacturing constraints during the design phase can help optimize the supply chain by ensuring that components and materials are readily available and compatible with the manufacturing process.
- Companies can accelerate the product development process and bring products to market more quickly.
What Is the Benefit of Using Design for Manufacturing With 3D Printing?
The benefits of using 3D printing in design for manufacturing are rapid prototyping, enabling designers to quickly iterate and test designs before full-scale production. This accelerates the product development cycle, reduces time-to-market, and lowers costs associated with traditional prototyping methods.
What Are the Disadvantages of Design for Manufacturing?
Disadvantages of design for manufacturing (DFM) include:
- High risk of project delay and cost increase due to redesign.
- Manufacturing costs increase due to redesign requests being denied.
- Reduced practicality for optimizations, leading to higher cost-per-unit manufacturing.
What Are the Common Challenges Faced in Implementing DFM?
The obstacles to implementing design for manufacturing (DFM) in PCB design include: inappropriate component footprints, insufficient copper-to-edge clearance, improper component clearances, unoptimized panelization, and component positioning concerns. These obstacles may result in: material waste, short circuits, assembly issues, and higher production costs. Overcoming these obstacles and providing effective production procedures and premium final goods depend heavily on performing comprehensive DFM inspections and adhering to industry standards.
What Are the Applications of Design for Manufacturing?
The applications of design for manufacturing (DFM) include:
- Streamlining Manufacturing Processes: DFM ensures that product designs are optimized for efficient and cost-effective production.
- Enhancing Product Quality: By considering manufacturing constraints early in the design phase, DFM helps minimize errors and defects in the final product.
- Reducing Production Costs: DFM techniques aim to eliminate unnecessary complexities and inefficiencies, leading to lower manufacturing costs.
- Accelerating Time-to-Market: Addressing manufacturing considerations early speeds up the product development process and enables quicker market entry.
How Does Design for Manufacturing Contribute to Product Innovation and Efficiency?
Design for manufacturing (DFM) contributes to product innovation and efficiency by integrating manufacturing considerations into the design process. This approach allows for the identification and elimination of potential manufacturing constraints early on, fostering innovation through more feasible designs. By optimizing designs for manufacturing, DFM enhances efficiency by streamlining production processes and reducing costs.
How Long Does Design for Manufacturing Take?
The duration of a design for manufacturing (DFM) process varies based on the complexity of the product and the manufacturing needs. It can take about two weeks to finish on average. This schedule enables careful examination and modifications to ensure that the finished design is best suited for economical and successful manufacturing procedures.
What Are the Examples of Design for Manufacturing?
Some examples of design for manufacturing are:
- Tank Gun Sight Design: DFM reduced the number of distinct parts required for assembly of an American tank gun sight from 24 to 8, significantly cutting manufacturing time.
- Snap-fit Components: Designing products with snap-fit components reduces the need for screws, bolts, or fasteners, streamlining assembly and decreasing material costs.
- Medical Implants: DFM principles applied to the design and production of medical implants, like hip and knee replacements, ensure efficient manufacturing and high product quality.
- Casting Optimization: DFM can improve the casting process by optimizing product form and geometry, reducing casting errors.
What Is the Difference Between DFM and DFA?
DFM addresses aspects such as: material selection, part complexity, and manufacturing tolerances to optimize product design to support productive and economical manufacturing processes. By creating products with simple-to-assemble parts, cutting down on assembly time, and lowering the number of parts needed for assembly, DFA (Design for Assembly) seeks to streamline the assembly process.
Summary
This article presented DFM, explained it, and discussed its process and various examples. To learn more about DFM, contact a Xometry representative.
Xometry provides a wide range of manufacturing capabilities, including machining and other value-added services for all of your prototyping and production needs. Visit our website to learn more or to request a free, no-obligation quote.
Disclaimer
The content appearing on this webpage is for informational purposes only. Xometry makes no representation or warranty of any kind, be it expressed or implied, as to the accuracy, completeness, or validity of the information. Any performance parameters, geometric tolerances, specific design features, quality and types of materials, or processes should not be inferred to represent what will be delivered by third-party suppliers or manufacturers through Xometry’s network. Buyers seeking quotes for parts are responsible for defining the specific requirements for those parts. Please refer to our terms and conditions for more information.
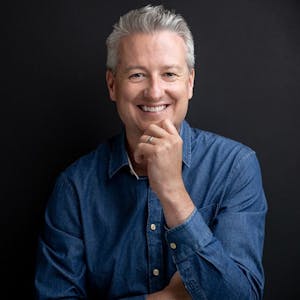