What is Acetal Plastic?
POM plastic (polyacetal) is a semi-crystalline thermoplastic that is based on the formaldehyde molecule. For this reason, it can also be found as polyformaldehyde, polyethylene glycol, or polyoxymethylene glycol. Its polymers consist of carbon functional groups bonded to two -OR groups, leading to an exceptional blend of mechanical and chemical properties.
Acetal plastic is commonly used as an alternative to metals, thus it finds applications in mechanical gears, electrical components, automotive products, sports equipment, medical products, food equipment, hardware, construction tools, and much more.
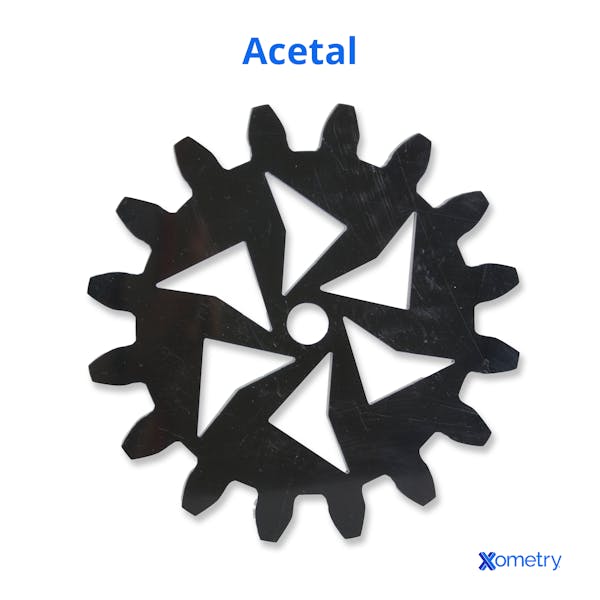
Property | ASTM Test | Value |
---|---|---|
Property Density | ASTM Test - | Value 1.39-1.43 g/cm3 |
Property Tensile Strength | ASTM Test D638 | Value 10,000 psi |
Property Flexural Modulus of Elasticity | ASTM Test D790 | Value 420 ksi |
Property Tensile Modulus of Elasticity | ASTM Test D638 | Value 450 ksi |
Property Water absorption (when immersed for 24 hrs) | ASTM Test D570 | Value 0.25% |
Property Heat Deflection Temperature (66 psi & 264 psi) | ASTM Test D648 | Value 336 °F & 257 °F |
Property Coefficient of Friction | ASTM Test Dynamic | Value 0.20 |
Data Source: Acetal Material Properties | Curbell Plastics
How Acetal is Formed
The formation of Acetal plastics begins by distilling hydrocarbon chains into smaller parts and then polymerizing them using catalysts. The method of formulation will depend on the type of acetal plastic and is generally split into homopolymer acetal and copolymer acetal processes.
The organic chemistry of acetal polymers can give even scientists a headache—but a brief description of the process used for the formulation of this semi-crystalline thermoplastic follows below.
The Differences Between Copolymer and Homopolymer Acetal Plastics
In the acetal homopolymer plastic process, aqueous formaldehyde building blocks are mixed with alcohols. They react together to form hemiformal, which is then distilled/dehydrated to release the formaldehyde. These monomers are polymerized in the presence of a catalyst to ultimately form the acetal homopolymer.
The copolymer process is much more involved; it first begins when formaldehyde is acid-catalyzed to form 1,3,5-trioxane. Separately, co-monomers dioxolane or ethylene oxide are formed by reacting ethylene glycol with aqueous formaldehyde in catalysis. The trioxane and dioxolane are polymerized together (again, in catalysis), and the resulting polymer is stabilized via melt or solution hydrolysis to remove unstable byproducts and introduce fillers, lubricants, stabilizers, etc.
Below is a table showing a brief comparison between acetal homopolymer vs. copolymer. In general, one would choose homopolymers over copolymers for their increased mechanical properties, while copolymers are generally more stable.
Acetal homopolymers | Acetal copolymers |
---|---|
Acetal homopolymers More structurally regular | Acetal copolymers Enhanced performance in long-term applications (better creep and fatigue resistance) |
Acetal homopolymers Molding cycles are shorter | Acetal copolymers More stable in alkaline environments and in chemical attacks |
Acetal homopolymers Enhanced mechanical characteristics (tensile strength, impact strength) | Acetal copolymers Minimal odor/gas release |
Acetal homopolymers Stiffer and stronger | Acetal copolymers Wider range of processing temps/times |
Acetal homopolymers Allows for thin wall designs and lighter parts | Acetal copolymers Better protected from UV exposure |
Acetal homopolymers Comes in a variety of viscosities | Acetal copolymers More dimensionally stable |
Acetal homopolymers Generally cheaper | Acetal copolymers Good color retention and requires no heavy metals for coloring |
Advantages of Acetal Plastic
- Exhibits dimensional stability and creep resistance when machined or worked
- Low friction coefficient (or “slippy”), leading to resistance to wear and abrasion
- Low moisture absorption in both wet and dry environments
- High tensile strength and rigidity
- Chemically resistant to fuels and organic solvents
- Low smoke emission
- Highly aesthetic surface finishes
- FDA approved and is 100% recyclable
- Can be impregnated/ blended with graphite, rubbers, glass-filled, nanocomposites, metals, etc., for additional unique material properties.
Disadvantages of Acetal Plastic
- Chemically weak to strong acids, bases, and oxidizers
- Prone to quick-burning (without flame retardants) due to high oxygen concentration
- Shrinks in mold significantly
- Poor resistance to UV radiation without additives; will degrade in color and strength if left in the sun
- Difficult to bond/glue without significant surface treatment
- Must manage temperatures when working/machining due to small working range
- Harder to machine than metals
- Toxic if inhaled/ingested in liquid form
Common Uses of Acetal Plastic in Manufacturing
- Mechanical components such as gears, pumps, valves, nuts, fasteners, etc.
- Food equipment such as pumps, conveyors, tanks, etc.
- Automotive components such as power window components, door locks, knobs, indicators, etc.
- Medical device components
- Fixtures, plumbing parts, bearings
Common Alternatives to Acetal Plastic
Acetal plastic comes in a variety of blends and similar formulations, making it easy to find an alternative if it doesn’t exactly fit the necessary material profile. Below is a brief exploration into other plastics that can function in the place of acetal plastics, given some key considerations.
Delrin: Delrin is a brand-specific POM homopolymer from DuPont and is widely utilized in industry. It is distinct from general acetal plastic, as acetal plastic is typically in a copolymer form, while Delrin is a specific homopolymer blend from DuPont. Delrin is generally specified in industrial applications such as valve components, pumps, gears, insulators, rollers, etc.
Nylon: Nylon is a thermoplastic that sports higher temperature resistance, tensile strength, stiffness, and lower costs than acetal plastic, making it a common alternative. Nylon can generally be used in place of acetal plastics; however, it is less dimensionally stable, less chemically/wear-resistant, and much more affected by humidity and moisture. Nylon is used throughout general-purpose applications and can be found in clothing, consumer goods, electronics, etc.
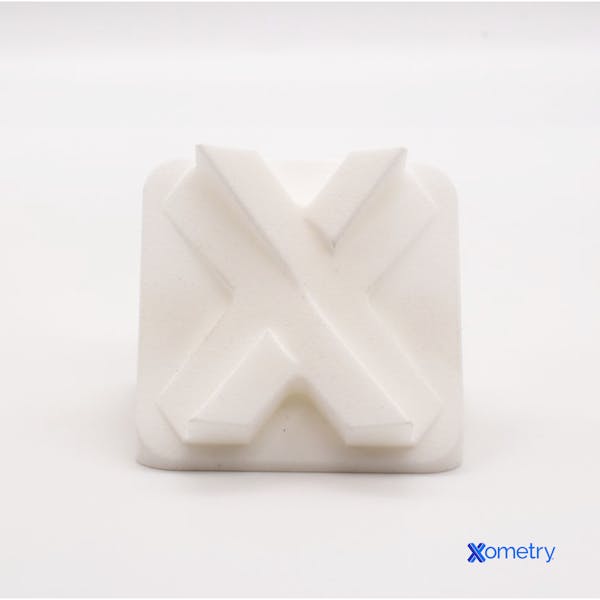
Summary
Polybutylene Terephthalate (PBT): PBT is sometimes exchangeable with acetal plastics, as it is nearly identical in mechanical characteristics. The primary consideration with PBT is that it will require more dehumidification and cannot be used in wet environments and has lower shrinkage than acetals. PBT is commonly used in electronics, sports clothing, bathroom fixtures, computer keyboards, household appliance components, etc.
Xometry provides 3D printing services and plastic injection molding services for all of your production needs. Get your quote today!
Disclaimer
The content appearing on this webpage is for informational purposes only. Xometry makes no representation or warranty of any kind, be it expressed or implied, as to the accuracy, completeness, or validity of the information. Any performance parameters, geometric tolerances, specific design features, quality and types of materials, or processes should not be inferred to represent what will be delivered by third-party suppliers or manufacturers through Xometry’s network. Buyers seeking quotes for parts are responsible for defining the specific requirements for those parts. Please refer to our terms and conditions for more information.
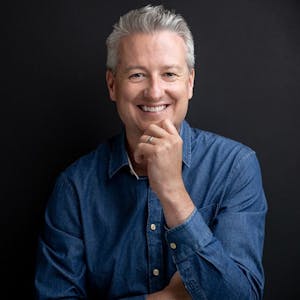