Coefficient of friction testing is a key part of material selection and quality control for many applications. There are different ways to measure the coefficient of friction, but all essentially involve measuring the force while moving one item relative to another. This can be used to measure both static friction and kinetic friction.
The article below covers each of these aspects in more detail.
What Is the Coefficient of Friction Testing?
Coefficient of friction (CoF) testing is a means of quantifying the resistance to sliding between two surfaces. This testing is commonly carried out in a multitude of industries including textiles, coatings, flooring, and automotive.
It is used extensively in the packaging industry, where plastic films are tested. For plastic film testing, a weighted sled is caused to move over a flat plane. The coefficient of friction is the ratio of the force applied in the direction of motion (horizontal) to the force perpendicular to that acting vertically down, (i.e., weight). In these cases, it is usually measured film to film (both the sled and the plane have the material being tested), but can also be measured between the film and another material.
In the bearing industry, CoF testing is neccessary for determining the friction of materials for use in bearing surfaces. In bearing applications, the frictional characteristics directly affect efficiency, wear, and operational lifespan. Bearings are designed to minimize friction while supporting rotational or linear motion, making precise CoF measurements essential for both material selection, and lubrication strategies.
How Does Coefficient of Friction Testing Work?
Coefficient of friction testing measures both static and kinetic friction. The test essentially works by causing a weight (sled) to slide over a flat surface (plane) and measuring either the force needed to initiate movement (static) or during continuous movement (kinetic).
Different geometric arrangements can be used to create this movement. The most widely used is a horizontal plane, which can be performed with a dedicated friction testing machine or a universal testing machine. The plane can be stationary with a moving sled, or the sled can be stationary against a moving plane. The material to be tested is typically used to cover the surfaces of both the sled and the plane. As they are caused to move relative to each other, the horizontal force on the sled is measured accurately.
Another arrangement for testing the coefficient of friction is the inclined plane method. This uses a plane that can be tilted, with a stationary sled that rests on top of it. The angle of the plane is increased until it is steep enough that the sled moves. The critical angle is used to calculate the static coefficient of friction.
Certain materials and applications may not be suited to these arrangements, so other test methods do exist for these cases.
These include pin-on-disk/ball-on-disk tribometer tests and ring-on-ring/flat-on-flat tests, used for evaluating friction in bearings, coatings, or lubricated contacts.
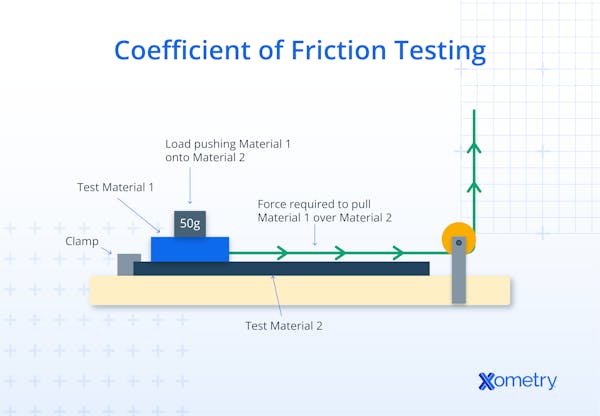
What Requires Coefficient of Friction Testing?
Coefficient of friction testing is applied to a wide range of materials and situations but is particularly relevant whenever friction is an important part of the proper operation of the material.
It can be applied to rubbers and road surfaces when developing tires for road vehicles or landing gear for aircraft.
It is used in plastic films and paper products used for packaging to ensure that they can be handled and stacked without sliding. It is used in the paper industry when developing new materials for printing - having the optimal friction coefficient on paper ensures that paper feed friction is minimized for smooth, high-speed printing operations. The electronics industry uses CoF testing, when evaluating touchscreens, as well as connectors and wear resistance of various coatings. Also, the sporting goods sector uses coefficient of friction testing to optimize grip and surface interactions for athletic performance.
How Is the Coefficient of Friction Measured?
The coefficient of friction of a material is measured by determining the frictional force required to move an object relative to a surface. This measurement is carried out according to a standardized procedure that is specific to the type of material being measured — for instance, ISO 8295 or ASTM D1894 for plastic films.
These standards have either a moving sled (weighted block) and a stationary plane, or a stationary sled and a moving plane. As the sled and plane move relative to each other, frictional force is recorded to determine the coefficient of friction. However, there are some other methods and measuring devices for coefficient of friction, such as an inclined-plane apparatus, that gradually increases the angle until the object begins to slide, determining the static coefficient of friction.
Is Coefficient of Friction Testing Applicable to Ceramic Coating?
Yes, coefficient of friction testing is applicable to ceramic coating materials. Ceramic coatings can be applied to either decrease the coefficient of friction (such as in bearing applications) or to increase the coefficient of friction (for non-slip ceramic tiles).
However, different testing apparatuses are typically used to measure the coefficient of friction for coated ceramics — various tribometers, including ball-on-disc machines, are often used. With this arrangement, a ball (typically steel) is pressed with a known normal force onto a surface moving in a controlled manner, such as a rotating or reciprocating disc of the test material. Coefficient of friction testing can be used to establish the optimum composition of a ceramic coating for the desired application. Coefficient of friction testing can be used to establish the optimum composition of a ceramic coating for the desired application.
What Is the Coefficient of Friction Testing Procedure?
To test the kinetic coefficient of friction, the following procedure is followed:
- Select the material that is to be tested. Depending on the details of the standardized test, you may need to prepare two pieces — one for the sled and another for the plane. The material should be clean and without creases or blemishes.
- Prepare the testing equipment. The CoF tester must be on a flat, completely level surface. The various test parameters will need to be entered into the tester, such as sliding speed and applied load.
- Run the test with the sled moving relative to the flat plane while the frictional force required to move the sled is recorded.
- Measure the normal force. It is important to confirm the normal force, the force acting perpendicular to the moving surface. This is essentially the weight of the sled.
- Calculate the coefficient of friction. The CoF is simply the drag force (frictional force) divided by the normal force. Typically, the average drag force over the test required to keep the sled moving is used in the calculation of the coefficient of friction
To test the static coefficient of friction, the force required to initiate the movement of the sled is required:
- Select the material to be tested. Prepare two pieces of the material—one for the sled and another for the plane. The materials should be clean and free from defects such as creases or blemishes.
- Prepare the testing equipment. The CoF tester must be placed on a flat, level surface. Ensure that the sled is positioned at rest against the plane. Enter the relevant test parameters into the tester, such as the applied load.
- Run the test. Gradually apply force to the sled, either manually or using a controlled mechanism, until the sled begins to move relative to the plane. The force required to initiate motion is recorded.
- Measure the normal force. Confirm the normal force, which is the force acting vertically downward on the sled (typically its weight).
- Calculate the static coefficient of friction. The static CoF is calculated as the force required to initiate movement (the frictional force) divided by the normal force (the weight acting downward).
What Are the Benefits of Coefficient of Friction Testing?
There are multiple benefits to carrying out coefficient of friction testing, such as:
- Is commonly used as a quality control tool. In this way, it ensures that the end user’s experience of the material is consistent and reliable, including how easily that material slides, or how well it grips.
- Depending on the application, safety may be enhanced with a less slippery surface (such as floor tiles) or with a more slippery surface (such as airbags). Testing the coefficient of friction of these materials allows for improvements to be made.
- New materials are developed, or tweaks can be made to a material’s composition to target improved properties. Where friction is an important property, CoF testing is invaluable in optimizing that property.
What Are the Challenges of Coefficient of Friction Testing?
No testing is perfect; there are always limitations and challenges in obtaining meaningful results. Some challenges with coefficient of friction testing are described below:
- Is not an inherent physical property of a material, like density or melting point. Rather, it is the product of multiple microscopic interactions and conditions and, therefore, does not communicate the nature of the frictional behavior but oversimplifies it into a single number.
- The arrangement of the coefficient of friction test may not effectively represent the real-world application. For instance, the contact area may be a different size or shape, the perpendicular pressure may be different, and the speed of movement may be significantly faster or slower. A standardized CoF test will not replicate these conditions.
- Environmental factors such as temperature and humidity can affect the performance of some materials.
- In some applications, lubrication is expected to be used. Controlling for this lubrication can be very difficult in a test environment, thereby introducing uncertainties.
What Is the Use of Coefficient of Friction Testing?
The primary use of coefficient of friction (CoF) testing is to assess how a material will interact with other surfaces under various conditions. It provides insights into the ease or difficulty of relative motion between two surfaces, which can affect performance in applications such as machinery, transport, and handling. For example, CoF testing is used to understand how materials will perform in sliding, stacking, or moving scenarios, such as in bearings, conveyor systems, and mechanical joints.
A secondary use of CoF testing is for quality control. For the reasons above, it is necessary to control packing materials within a certain reliable specification. Therefore, CoF testing can be carried out regularly to ensure the material will behave exactly as the user expects.
What Are Industry Applications of Coefficient of Friction Testing?
Various industries and applications rely on a predictable coefficient of friction. Some are explained below:
- Automotive: Various automotive components work on friction, such as disc brakes, tires, and clutches. The materials used in these components are optimized for their frictional force.
- Packaging: It is important to understand the friction of packaging materials, as it affects how well packages can be stacked, handled, and moved. If they slide too easily, it can be hazardous and damaging to the packages.
- Textiles: Different fabrics naturally have very different friction coefficients (consider silk compared with denim). The friction of fabrics is important to understand in clothing, and also in industrial textiles, such as seat covers.
- Construction: Particularly with flooring materials, the coefficient of friction is a crucial property for safety to avoid injury due to slipping.
- Sports Equipment: The friction of material is essentially the “grip” that material provides and, therefore, is a key part of the design of clubs, balls, and shoes.
What Are Different Types of Friction?
There are essentially two types of friction:
- Static: Static friction is the force that needs to be overcome between two surfaces before there can be relative movement between the surfaces. It is called static friction because it is when the surfaces are at rest relative to each other. The static friction force to be overcome before moving is typically higher than the frictional force once there is movement. In CoF testing, the coefficient of static friction is calculated as the maximum force on the sled just before it starts to move against the plane, divided by the normal force (usually the weight of the sled).
- Kinetic: Kinetic friction (also termed dynamic friction) is the force between two surfaces while remaining in motion relative to each other. This is the force that continues to act in the opposite direction to the direction of movement, restricting that movement. Kinetic friction is generally lower than static friction — there is less resistance to movement once that movement has begun. In CoF testing, the coefficient of kinetic friction is measured as the average frictional force acting on the sled while moving during the test, divided by the normal force (the weight of the sled).
What Are the Factors That Affect Coefficient of Friction?
As with any material testing, several factors can affect the coefficient of friction testing. The main factors are explained below:
- Any oil, detergents, or other contaminants on the sample will directly affect the coefficient of friction measurement. The sample must be confirmed to be free of any contamination, including dust or dirt. The sample should also not be wrinkled or damaged, which could affect the results.
- The result will be affected if the testing table is not perfectly level. This is something that needs to be checked and confirmed regularly.
- Environmental factors such as temperature and humidity should be within a controlled range and should not fluctuate widely during testing.
- The texture and smoothness of the material's surface can significantly influence the frictional measurement. A rough surface may result in higher friction, while a smoother surface typically yields lower friction.
What Is the ASTM Standard of Coefficient of Friction?
The ASTM standard for testing the coefficient of friction of plastic films and sheets is ASTM D1894. It uses a universal testing machine, with a horizontal plane attachment and a sled of known weight. The testing standard requires that both the plane and the sled are fitted with specimens of the same material to be tested — it does not allow for CoF testing of dissimilar materials.
What Is the ISO Standard for Coefficient of Friction?
The ISO standard for measuring the coefficient of friction is ISO 8295. This standard is specifically for application in plastic film and sheeting, using a horizontal plane and sled (which can be performed on a universal testing machine). ISO 8295 is broader than the equivalent ASTM standard, as it provides for testing the coefficient of friction of a material against a dissimilar material, i.e., the plane material can be glass, steel, or another material.
What Does the Coefficient of Friction Results Mean?
A coefficient of friction result is simply the frictional force that needs to be overcome during movement divided by the downward-acting force of the test sled. This means that a smaller coefficient of friction is measured when a smaller frictional force is present, i.e., a low coefficient of friction means that there is less friction experienced by that material and that it slides easily.
Conversely, a high coefficient of friction indicates a high frictional force and that the tested material does not slip easily.
What Is the Role of Coefficient of Friction Testing for Safety and Compliance?
Coefficient of friction testing plays a role in ensuring safety and compliance. Some critical applications rely on friction to operate safely. For instance, road surfaces should allow tires to grip, and flooring materials should not be slippery, even if they get wet. In applications like these, a certain minimum acceptable coefficient of friction should be adhered to. CoF testing is therefore also necessary to ensure compliance. Regular testing against the required standard will ensure the accepted safety standards are maintained.
Is Coefficient of Friction Testing Accurate?
Yes, coefficient of friction testing is considered to be accurate. Although some factors can affect the results obtained by the testing, these factors can generally be controlled or accounted for. These include aspects such as the temperature at which the test is undertaken, and the cleanliness and integrity of the material samples. So long as effort is taken to carry out the test carefully and according to the details of the agreed standard, the results can be considered accurate.
Is the Coefficient of Friction Test Known Globally?
Yes, the coefficient of friction test is known globally. There are multiple international standards for coefficient of friction testing, with the ISO and ASTM standards being the most widely used. However, there are also standards from other international organizations such as TAPPI (the Technical Association of the Pulp and Paper Industry) for paper and cardboard packaging materials. Coefficient of friction testing allows for internationally standardized testing and interpretation of results.
Summary
This article presented coefficient of friction testing, explained it, and discussed its procedure and various benefits. To learn more about coefficient of friction testing, contact a Xometry representative.
Xometry provides a wide range of manufacturing capabilities and other value-added services for all of your prototyping and production needs. Visit our website to learn more or to request a free, no-obligation quote.
Disclaimer
The content appearing on this webpage is for informational purposes only. Xometry makes no representation or warranty of any kind, be it expressed or implied, as to the accuracy, completeness, or validity of the information. Any performance parameters, geometric tolerances, specific design features, quality and types of materials, or processes should not be inferred to represent what will be delivered by third-party suppliers or manufacturers through Xometry’s network. Buyers seeking quotes for parts are responsible for defining the specific requirements for those parts. Please refer to our terms and conditions for more information.
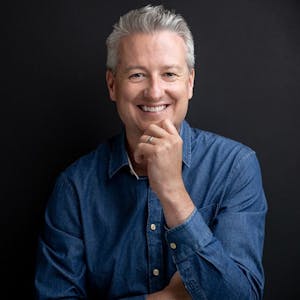