Creep is the change in length or shape over an extended period of time due to a continuously applied static stress. It is an undesirable deformation that can be accelerated by the application of heat. Other factors that affect creep are the material type and age. There are various mechanisms through which creep can occur, each having different characteristics. Creep mechanisms include: Harper–Dorn Creep, Coble Creep, Nabarro–Herring Creep, Glide-Controlled Creep, Climb-Controlled Creep, and Solute Drag Creep.
To prevent these creep mechanisms from occurring, proper material selection must take place to use materials that are sufficiently creep resistant for the chosen application. Another method of increasing creep resistance is adding reinforcement to the polymer.
This article will discuss the definition of creep in polymers, how it occurs, the factors that affect it, the types of creep, and how it can be prevented.
What Is Creep in Polymers?
Creep in a polymer is the change in strain of a material due to constant pressure. A change in the dimension of a polymer can be identified over time due to the stress a material is under. The deformation of a polymer in the creep process is time-dependent as the loading is so small that it will not affect the polymer over a short period of time. The deformation in creep consists of both elastic and plastic deformation, the latter of which will permanently deform the polymer. For more information, see our guide on the Properties of Polymers.
How Does Creep in Polymers Occur?
Creep occurs through the deformation of the molecular chain in polymers and the viscoelastic flow. In order for creep to occur, a load is required—small enough to not instantly deform the material, but not so little that it does not stress the material. The deformation happens at a comparatively slow rate that causes a material to fail before its yield point. The reason why creep can occur in polymers is a combination of temperatures, stress levels, and material properties.
What Are the Factors of Creep in Polymers?
One of the most important factors affecting the creep of polymers is time. The longer the polymers are under stress, the greater the plastic deformation. Other factors affecting creep are:
- Temperature.
- Load.
- Polymer material type.
- Age of material.
What Are the Processes of Creep in Polymers?
Creep in polymers is the time-dependent deformation of a given polymer. When a load is applied to the polymer, there will be an elastic deformation and a plastic deformation. Elastic deformation is non-permanent after the load is removed, whereas plastic deformation is semi-permanent. In plastic deformation, the material will restore to its original size and shape over a long period of time after the load is removed. Additionally, depending on the temperature of the material and the intensity of the load, the polymer will deform over a matter of seconds and minutes, or over hours and days. The former is referred to as plastic flow and the latter is creep.
In both cases, deformation occurs due to the reorientation of the polymer chains. For low-intensity loads and relatively low temperatures, the elastic stress within the polymer will balance the applied load and will limit the total deformation. However, for higher loads and temperatures the polymer chains will rupture causing material failure. There are a number of mechanisms through which creep can occur in polymers. The six mechanisms are:
- Harper–Dorn Creep.
- Coble Creep (Grain Boundary Diffusion).
- Nabarro–Herring Creep.
- Glide-Controlled Dislocation Creep.
- Climb-Controlled Dislocation Creep.
- Solute Drag Creep.
What Are the Types of Creep?
Creep can be broken down into the six categories listed below:
1. Harper–Dorn Creep
Harper–Dorn Creep occurs through dislocation. In a similar creep mechanism such as Nabarro-Herring creep, the strain rate would decrease for a single crystal. However, for Harper-Dorn creep, the rate remains the same. During Harper-Dorn creep, the creep increased linearly with the applied stress. This type of creep occurs through the intergranular dislocation process. Harper-Dorn creep can only be initiated when there is a low dislocation density. The grain size must be between 0.5 mm and 3.3 mm for this type of creep to occur.
2. Coble Creep or Grain Boundary Diffusion
Coble creep is a form of creep that involves defects including: dislocation cores and grain boundaries. Importantly, coble creep does not occur through the grain itself. In coble creep, diffusion between the compression areas and areas of vacancies in tension occurs through the grain boundary. This form of creep occurs when a material is exposed to tensile stress at high heat.
3. Nabarro–Herring Creep or Bulk Diffusion
Nabarro–Herring creep occurs due to lattice diffusion. Lattice diffusion is when areas of compression and the vacancies of tension swap while remaining internal to the grain structure. Most importantly, this form of creep occurs primarily when susceptible materials are exposed to high temperatures and low stress. It is a result of atoms diffusing within a grain’s crystal lattice due to the vacancies that occur as temperatures increase. For more information, see our guide on Nabarro–Herring creep.
4. Glide-Controlled Dislocation Creep
Glide-controlled dislocation creep can occur at relatively low temperatures. It is a process by which the material strain changes as a result of pressure. This type of creep works by remaining within the same slip plane. Internal stress is caused by atomic displacements near a dislocation. The tensile and compressive forces around the dislocations interact with one another and are able to move around.
5. Climb-Controlled Dislocation Creep
As with glide-controlled dislocation creep, atomic displacements near dislocations result in internal stress on the material. Climb-controlled dislocation creep involves the creation and subsequent migration of point defects. The importance of this type of creep is that it is temperature-activated, only taking effect at much higher temperatures.
6. Solute Drag Creep
Solute drag creep occurs due to both dislocation and diffusion flow. At low temperatures, any dislocations are hard to move. However, with an increase in temperature, any solute atoms present may form around a dislocation and relieve the elastic stress of the dislocation. The atmosphere of solute atoms around the dislocation creates resistance to dislocation gliding. But if the force experienced is high, then the dislocations break away from the solute atoms. At higher temperatures, the solute atoms can be dragged with the dislocations at slow rates, meaning the resistance force of the solute atoms is overcome.
How Can Creep in Polymers Be Prevented?
Choosing materials with a high creep resistance and melting point can prevent creep in polymers. An example of a highly creep-resistant polymer is polycarbonate. One preventative measure is the inclusion of ceramic reinforcement to alter the creep resistance and creep mechanism. This can be done through spray forming techniques and co-injection methods to increase the resilience to creeping.
How Does Temperature Affect Creep in Polymers?
Lower temperatures generally reduce the speed of the creeping process in polymers. Different environmental temperatures must be taken into consideration and calculated as there is a direct correlation between higher temperatures and faster rates of creep deformation. With an increase in temperature, polymer chains become further apart. This creates more space and kinetic energy, allowing them to slide past one another and become more easily disentangled. Some polymers can experience creep at room temperatures, while metals only tend to do so at roughly 40% of their melting temperature. For more information, see our guide on What is Heat Creep.
Does Creep Occur in Polymers?
Yes, creeping occurs in polymers as a result of the deformation of the polymer molecules when exposed to stress. This stress (compressive, shear, tensile, or flexural) causes polymers to deform permanently over a prolonged period. Creep-susceptible materials include polypropylene. Items such as: pipes, machinery parts, and plastic furniture may deform due to creep if subject to unsuitable temperature and stress conditions over an extended period of time. Creep in polymers is more common with amorphous polymers as opposed to crystalline polymers as the former’s molecular chains can slip in relation to each other more easily.
Is Creep Harmful?
Yes. Creep can be harmful to the structural integrity of constructions—for example, in mass concrete structures, such as dams—and can be the primary cause of cracking in the structure. While the extent of harm is dependent on things such as: structural design, service conditions, and construction material, creep can result in stress redistribution, prestress loss, serviceability problems, and in worst-case scenarios, failure of structural elements.
Summary
This article presented the creep of polymers, explained what it is, and discussed its various applications. To learn more about polymers, contact a Xometry representative.
Xometry provides a wide range of manufacturing capabilities, and other value-added services for all of your prototyping and production needs. Visit our website to learn more or to request a free, no-obligation quote.
Disclaimer
The content appearing on this webpage is for informational purposes only. Xometry makes no representation or warranty of any kind, be it expressed or implied, as to the accuracy, completeness, or validity of the information. Any performance parameters, geometric tolerances, specific design features, quality and types of materials, or processes should not be inferred to represent what will be delivered by third-party suppliers or manufacturers through Xometry’s network. Buyers seeking quotes for parts are responsible for defining the specific requirements for those parts. Please refer to our terms and conditions for more information.
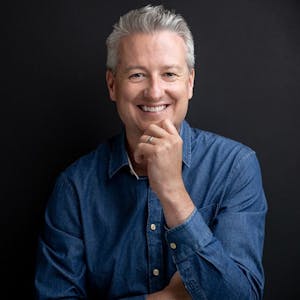