Dislocation creep is one of several time-dependent plastic deformation mechanisms that occur in materials under applied loads at elevated temperatures. It causes permanent deformation through the motion of linear defects through a material's crystal lattice. Dislocation motion in a crystal lattice is responsible for plastic deformation and work hardening of metals at low temperatures. The added energy available inside the material at higher temperatures, however, makes it easier for planes of atoms to move past each other at lower stresses than at room temperature. These atomic movements accumulate into measurable displacement, or strain, in a component. It can result in the rupture of the material after enough strain has accumulated.
It is important for engineers to consider creep in their designs. The selection of appropriate materials for long-term use in high-temperature conditions, and knowledge of their behavior in a given service environment, can avoid loss of function or failure of key components due to accumulated creep damage. Several strategies can be used to mitigate the effects of dislocation creep such as: altering part geometry, using a material with a higher melting point, introducing precipitates at grain boundaries, using materials with larger grain sizes, and reducing working temperatures and loads. This article will define and describe dislocation creep, review its importance for engineers and manufacturers, and review strategies for minimizing or preventing time-dependent deformation in high-temperature conditions.
What Is Dislocation Creep?
Dislocation creep is one of a group of time-dependent plastic deformation mechanisms that occur under conditions of continuously applied load at elevated temperatures. It is facilitated by the movement of dislocations, or linear defects in the regular lattice of a crystalline solid. While there are many types of dislocations, one type of dislocation, the “edge” dislocation, is the easiest to understand. An edge dislocation can be thought of as an extra half-plane of atoms extending through part of the regular lattice. In dislocation creep, dislocations move through the crystal until they either reach the surface of the material and disappear, leaving a one-atom high step in the surface, or until their motion is blocked, or pinned, by a grain boundary or by intersecting other dislocations.
Dislocation creep can proceed either lateral to the slip plane (dislocation glide) or perpendicular to it (dislocation climb). Dislocation glide is the main mechanism by which metal atoms move to produce observable plastic deformation at ambient temperature. The generation and pinning of dislocations account for the strain hardening of materials observed in strengthening by cold work. At high enough temperatures (usually about half the melting temperature of a material), dislocations move out of the crystal structure more easily. The dislocation glide plus climb produces the observable strain called dislocation creep. How Does Dislocation Creep Occur?
Dislocation creep occurs when the edges of microstructural irregularities move through the structure over time under the influence of applied stress at elevated temperatures. Dislocations are generated by plastic deformation and travel through the microstructure either by “gliding” or “climbing.” Dislocations can be removed by a process called “recovery,” which occurs at temperatures elevated enough to allow easy motion and reconfiguration of dislocations into new lattice substructures. The list below describes the steps in the steps in dislocation creep:
- Dislocation creep starts when stress is constantly applied to a material. At lower temperatures, dislocation glide is the dominant dislocation motion mechanism. Dislocation glide occurs at all temperatures, nearly up to the material’s melting point. Lower temperatures less than half the material’s melting temperature can also cause dislocations to pile up, form tangles, encounter obstacles such as: solute atoms, or become pinned by grain boundaries or precipitates. This results in strain hardening, or work hardening. At higher temperatures, the rate of dislocation recovery balances the rate of work hardening, and strain continues to accumulate under the application of constant stress. Materials with more irregularities in their microstructure are more likely to experience dislocation creep since atoms have more opportunities to relocate. This results in strain hardening, or work hardening.
- Depending on the operating temperature, when a material experiences sufficiently high stresses, atoms dislocate in the microstructure via glide or climb. Glide is the movement of dislocations in a lateral direction while climb is the vertical movement of dislocations. While glide can occur at all temperatures, climb occurs more frequently as temperatures increase.
- When stresses close to the yield stress are constantly applied, dislocation motion regularly occurs. Consequently, materials plastically deform due to the extensive glide or climb dislocations occurring in the microstructure. Creep failure, or accumulated deformation caused by dislocation creep, can compromise the strength of the material and pose a safety hazard.
For more information, see our guide on Creep (Deformation).
What Are the Factors of Dislocation Creep?
Several factors affect the degree of dislocation creep experienced by a material. The list below highlights the most important factors controlling the rate of dislocation creep:
- Temperature: As temperatures increase, atoms in the microstructure of a material gain vibrational energy. This increases the mobility of point and linear defects in the microstructure (vacancies and dislocations). It enables faster rates of plastic deformation in the form of dislocation creep.
- Stress: Applied stress increases the creep rate and, depending on the material’s strain rate and operating temperatures, results in changes in the creep mechanism from diffusion creep to dislocation climb or glide. As stress is applied, materials experiencing dislocation creep deform along grain boundaries.
- Strain Rate: Strain rate is the amount of deformation per unit of time. It is a major factor in causing dislocation creep. Higher strain rates lead to more severe dislocation creep at a given high temperature.
- Grain Size: Materials with smaller grains are more susceptible to dislocation creep while materials with larger grains are more resistant to dislocation creep. Smaller grain sizes act as obstacles to dislocation glide and inhibit the spread of dislocations at room temperature. Smaller grains actually contribute to creep deformation at higher temperatures above what is called a material’s equicohesive temperature.
- Crystal Structure: The crystal structure of a material influences the rate of dislocation creep. More densely-packed crystal structures, such as face-centered cubic (FCC) and hexagonal close-packed (HCP), are more resistant to creep than less dense structures like body-centered cubic (BCC) crystals. This is because FCC structures tend to have more grain boundaries since there are more potential nucleation sites when an FCC material is cooled from high temperatures.
- Chemical Composition: The chemical composition of a material influences the likelihood of dislocation creep due to the size and arrangement of atoms in a material’s microstructure.
When Was Dislocation Creep Proposed?
Dislocation creep was theorized in the mid-20th century by a handful of scientists and engineers namely: N.F. Mott and Johannes Weertman. N.F. Mott published his studies on dislocation creep in the research journal Royal Society of London Series A, Mathematical and Physical Sciences in 1953. In his work, Mott stated that dislocations are formed during crystal growth and formed the foundation for the understanding of dislocation climb. Meanwhile, while he was a professor at Northwestern University, Johannes Weertman conducted numerous experiments to investigate the mechanical properties of metals, particularly high-temperature creep, and dislocation theory. Both Mott’s and Weertman’s work contributed to the present-day understanding of the mechanisms behind dislocation creep.
What Is the Importance of Dislocation Creep in Manufacturing Processes?
Dislocation creep is important in manufacturing processes because it impacts both manufacturing quality and product performance during use. In manufacturing, components in fabrication machines often experience high loads at elevated temperatures and are susceptible to dislocation creep. Additionally, creep-resistant alloys can be difficult to form in manufacturing because of the alloying elements present in the material. The slow deformation of machinery components can impact the machinery's efficiency and product quality. Therefore, creep directly impacts the manufacturing tools and methods needed to produce parts.
How Can Dislocation Creep Be Prevented?
Several strategies can minimize dislocation creep. Some of the methods used to reduce dislocation creep are listed below:
- Reduce Applied Loads: Reducing the load applied to a component reduces stress. Consequently, dislocations are less likely to proliferate through the material’s microstructure. However, reducing the loads applied to a part is not always possible in a given application.
- Reduce Operating Temperatures: Reducing operating temperatures reduces the mobility of dislocations and inhibits the diffusion of vacancies. Dislocation glide and climb, which depend on temperature-activated processes, are required for dislocation creep. However, as with the strategy of minimizing applied stresses, it is not always possible to reduce the service temperature for a specific application.
- Use a Material With Larger Grain Sizes: At room temperature, small grain size means dislocations have more obstacles to overcome to spread throughout a material’s microstructure. However, in creep conditions at higher temperatures, smaller grains actually lead to more creep deformation. This is because grain boundaries become weaker at higher temperatures. Therefore, using a material with larger grains may help to prevent dislocation creep.
How Does Dislocation Creep Compare to Diffusion Creep?
Dislocation creep and diffusion creep are two types of creep that share many similarities. In dislocation creep, deformation is facilitated by the movement of dislocations throughout a material’s crystal structure by dislocation slide or climb and can occur at all temperatures. Diffusion creep, on the other hand, is dominated by the movement of vacancies throughout the microstructure, both along grain boundaries and through the crystal lattice, and happens at temperatures between 40-90% of a material’s melting point. Therefore, diffusion creep tends to occur at higher temperatures but at lower stresses compared to dislocation creep since atomic diffusion can more readily occur due to lower activation energy at grain boundaries.
How Is the Dislocation Creep Rate Derived?
Creep behavior is generally divided into three stages. While dislocation glide occurs in all three stages, the second stage, also referred to as "power law creep," is the one most associated with dislocation creep. Dislocation creep is defined for that purpose as the thermally activated, time-dependent motion and climb of dislocations under constant stress. The equation for dislocation creep rate is shown below:
ε˙=Aσ^nexp(−Q/RT)
Where:
A = constant, which accounts for the particular creep mechanism
σ = applied von Mises stress
n = stress exponent
Q = activation energy
R = universal gas constant
T = absolute temperature in Kelvin
Activation energy is defined as the minimum amount of energy needed to start a chemical reaction.
Does Dislocation Creep Only Occur on Polymers?
No. Dislocation creep can occur in any type of material, including polymers, metals, and ceramics. For more information, see our guide on What is a Polymer.
Is Dislocation Creep Caused by High Temperature?
No, dislocation creep is not caused by high temperature alone. Dislocation creep is plastic deformation that occurs over a period of time at high temperatures during the application of constant stress. Factors other than time, temperature, and stress also influence the rate of dislocation creep, including: the grain size, crystal structure, and chemical composition.
Is Dislocation Creep Safe?
No, dislocation creep can be hazardous and can pose a risk to both personal health and property.
Does Creep Help Relieve Strain?
No, creep does not help relieve strain. Creep is a time-dependent form of deformation. Therefore, creep actually contributes to strain and can make strain caused by plastic deformation worse.
What Is the Difference Between Dislocation Creep and Solute Drag Creep?
Dislocation creep is a type of creep characterized by the movement of dislocations throughout the microstructure. Solute drag creep is a type of diffusion creep characterized by the diffusion of solute atoms, which are often substitutional in nature, a material’s microstructure.
Summary
This article presented dislocation creep, explained it, and discussed its importance and prevention. To learn more about dislocation creep, contact a Xometry representative.
Xometry provides a wide range of manufacturing capabilities and other value-added services for all of your prototyping and production needs. Visit our website to learn more or to request a free, no-obligation quote.
Disclaimer
The content appearing on this webpage is for informational purposes only. Xometry makes no representation or warranty of any kind, be it expressed or implied, as to the accuracy, completeness, or validity of the information. Any performance parameters, geometric tolerances, specific design features, quality and types of materials, or processes should not be inferred to represent what will be delivered by third-party suppliers or manufacturers through Xometry’s network. Buyers seeking quotes for parts are responsible for defining the specific requirements for those parts. Please refer to our terms and conditions for more information.
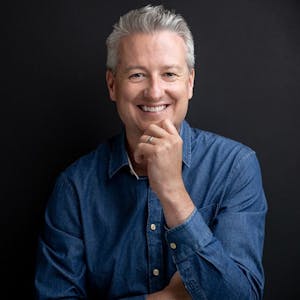