High-speed steel (HSS) is a special kind of tool steel known for its extraordinary hardness, toughness, and tolerance to high temperatures. Its distinctive compositions (iron, carbon, tungsten, chromium, molybdenum, and other elements) allow tools made from high-speed steels to tolerate high mechanical loads and keep their cutting edge even at high temperatures.
This article goes into greater detail about the make-up, characteristics, and varied applications of high-speed steel.
What Is High-Speed Steel?
High-speed steels (HSS) form a class of iron-based alloys that excel in cutting applications compared to traditional high-carbon steels. They are exceptionally hard, abrasion-resistant, and resistant to softening at high temperatures. These characteristics, which come from the alloy additions and particular heat treatments, enable HSS to cut materials effectively and quickly.
What Is the Origin of High-Speed Steel?
In 1868, Robert Mushet's invention of self-hardening steel, known as Mushet Steel or R Mushet's Special Steel, marked a significant development in the history of steel. This innovative steel, with a secret chemical composition that included an 8% tungsten content, exhibited the ability to harden when forged and cooled. It found extensive use in engineering tools. In 1870, Samuel Osborn & Company in Sheffield, UK, acquired the rights to mass-produce this special steel. Later, in 1910, Crucible Steel Co. in New Jersey pioneered high-speed steel, a milestone in steel technology for its superior cutting abilities. Another important breakthrough occurred in 1937 when W. Breelor created tungsten molybdenum HSS M2 in the USA, further advancing the capabilities of high-speed steel.
How Is High-Speed Steel Made?
High-speed steel (HSS) undergoes a meticulously controlled series of steps to achieve its exceptional properties. It starts with refining and alloying the steel, followed by forging and rolling it into saleable forms. Heat treatment is a critical aspect of HSS production, involving phases like annealing, austenitization, and martensitic transformation. Annealing reduces hardness, followed by austenization, where high heat alters the crystal structure for carbon absorption. Martensite forms when steel is rapidly cooled, making it hard but brittle. HSS is an alloy of carbon and iron, with additional elements added for specific characteristics. Molecular modification through heat treatment rearranges the atomic structure, providing the steel with desired properties. This process requires precision and uniformity at each stage, and it includes steps like pre-heating, heating (austenitization), quenching, and tempering. Depending on the steel type and intended use, additional treatments such as cryogenic freezing may be necessary to achieve the desired properties. Factors like temperature and time must be carefully controlled to ensure quality, as variations can lead to either expansion or shrinkage in the final product, impacting its mechanical properties.
What Are the Different Types of High-Speed Steels?
Listed below are the types of high-speed steels:
1. Molybdenum High-Speed Steels
Molybdenum high-speed steel is primarily an iron-based alloy distinguished by its notable incorporation of molybdenum, which is comparatively higher in concentration compared to other high-speed steels (HSS). Additionally, it contains a substantial proportion of carbon, typically ranging from 0.8 to 1.5, depending on the specific grade, as well as various other elements known for their carbide-forming properties. Molybdenum high-speed steels, such as M10 and M50, are iron-based alloys known for their exceptional toughness and cutting capabilities. Also, M10 and M50 are the exclusive grades within the category of molybdenum high-speed steels that do not contain tungsten or cobalt. Its bending strength and great wear resistance make it useful in a variety of tools, including drill bits and reamers.
2. Cobalt High-Speed Steels
Cobalt high-speed steels, often referred to as "super" high-speed steels, are alloyed with more than 5% cobalt, making them excel in hot hardness and wear resistance. Typically, these steels contain tungsten, chromium, molybdenum, vanadium, and high carbon levels. Notable grades within this category include M35 and M42. These cobalt high-speed steels prove highly effective for demanding tasks like rough or hogging cuts, excelling in applications involving high temperatures. However, they are less suitable for finishing cuts in lower-temperature scenarios. Their exceptional performance shines when cutting materials with continuous chips, such as cast iron or non-ferrous metals.
The choice to use cobalt high-speed steels is justified when deep cuts and fast cutting speeds are required, or when dealing with hard and scaly materials. Additionally, M42 has high heat-treated hardness (68 to 70 HRC) and substantial cobalt content, which imparts exceptional hot hardness. Consequently, tools made from M42 super high-speed steel maintain sharp and hard cutting edges, making them ideal for heavy-duty and high-production cutting applications.
3. Tungsten High-Speed Steel
T1 tungsten high-speed steel is a member of the “T” series alloys. It contains 17.25 - 18.75% tungsten, along with chromium, vanadium, and carbon. Notably, T15 with 5% cobalt has remarkable wear resistance, toughness, and strength which correlates to bend strength. Its prolonged tool life makes it suitable for cold work tooling. M4 and T15 are gaining popularity for milling cutters due to their ease of grinding and regrinding. What sets T15 apart is its significantly higher vanadium content compared to other high-speed steels (HSS). Tungsten high-speed steel, in general, boasts a high tungsten content and minimal molybdenum presence. Despite remarkable technological advancements and material innovations, enhancing the performance of cold work tooling still relies on the timeless principles of metallurgy that have served tool and die shops for generations. For those seeking improved results, it's essential to revisit three critical aspects: material selection for the tooling, precise heat treatment procedures, and preservation of surface quality.
4. Tungsten-Molybdenum High-Speed Steels
Tungsten-molybdenum high-speed steels, such as the "M" series alloys (M1, M2, M3, M4, M7, M52, M62), are distinguished by their composition, primarily containing tungsten (W) and molybdenum (Mo). Unlike some other high-speed steels, they do not contain cobalt (Co). These alloys offer advantages similar to those of their tungsten-rich counterparts but with a focus on reduced weight due to the lower density of molybdenum. While these alloys have a reduced tungsten content, they compensate for it with a higher proportion of molybdenum. However, it's worth noting that the alloy melting temperature is lower for higher molybdenum grades. As a consequence, they may experience some loss in hot hardness compared to tungsten-rich alloys due to their reduced heat resistance at high temperatures. This is a trade-off to consider when selecting the appropriate high-speed steel for specific tooling applications.
The most prevalent and extensively used variety of high-speed steels (HSS) is molybdenum HSS. M2 stands out in particular as the "standard," widely used industrial HSS. The uneven distribution of carbide particles in the finished product is a recurring problem in the production of tool steels. The huge temperature difference between the liquid and solid states, which for alloys like M2 can be as high as 130°C, is the root cause of this problem. As a result, the material solidifies under the influence of this extreme temperature contrast, which causes the separation of carbon and alloying elements. As a result of this segregation phenomenon, carbide bands eventually emerge.
How Is High-Speed Steel Different From Regular Steel?
High-speed steel, such as tungsten-type high-speed steel (M2), differs significantly from regular steel like W1 due to its alloy composition. M2 contains tungsten, molybdenum, chromium, vanadium, and other essential elements. This alloying enhances its hardness and yield strength, making it tougher and more resilient. In contrast, W1 is plain carbon steel, which requires quenching in water to transform into martensite, resulting in a shallow quench depth, leading to a hard outer layer and a softer inner core, potentially contributing to toughness. M2's higher alloy content introduces substantial substitution solution strengthening, making it challenging to surpass in strength by plain carbon steel. Consequently, high-speed steel like M2 is preferred for applications demanding exceptional hardness and durability.
Is High-Speed Steel a High-Alloy Steel?
Yes, high-speed steel (HSS) is indeed a high-alloy steel. Its composition is meticulously engineered to excel in cutting tools, allowing it to maintain sharp edges even under the extreme conditions encountered when machining the toughest materials. HSS is the preferred choice for industrial applications demanding precision, durability, and efficiency. It shines when cutting hard or abrasive materials, executing aggressive cuts, and operating at elevated temperatures. Notably, HSS embodies the essence of "high-speed," delivering both efficiency and economic benefits, making it indispensable for various cutting tasks.
What Are the Chemical Compositions of High-Speed Steels?
High-speed steel (HSS) incorporates various essential elements in its composition, each serving a distinct purpose. For example, tungsten contributes to hardness and wear resistance, ensuring durability while chromium adds hardness, corrosion resistance, and stability at high temperatures. Table 1 below shows the chemical composition of HSS:
Chemical | Tungsten % | Chromium % | Vanadium % | Carbon % | Cobalt |
---|---|---|---|---|---|
Chemical Tungsten HSS T5 | Tungsten % 17.50-19.00 | Chromium % 3.75-5.00 | Vanadium % I.80-2.40 | Carbon % 0.75-0.85 | Cobalt 7-9.5 |
Chemical Molybdenum HSS M1 | Tungsten % 1.40-2.10 | Chromium % 3.50-4.00 | Vanadium % 1.00-1.35 | Carbon % 078-0.88 | Cobalt — |
Chemical Cobalt HSS M42 | Tungsten % 1.6 | Chromium % 3.9 | Vanadium % 1.2 | Carbon % 1.1 | Cobalt 8.25 |
What Is the Carbon Content of High-Speed Steels?
High-speed steel like T1, a tungsten high-speed steel, typically contains 0.65% to 0.8% carbon. This adds to its hardness and wear resistance. The two properties are essential for cutting and machining applications.
What Are the Properties of High-Speed Steels?
Table 2 outlines the properties of high-speed steel (HSS):
Property | Description |
---|---|
Property Density | Description 7.6 g/cm³ |
Property Yield Strength | Description 1000 MPa |
Property Hardness | Description 64 HRC |
Property Magnetism | Description Magnetic |
Property Thermal conductivity | Description 41 W/(m.k) |
Property Ultimate tensile strength | Description 1200 Mpa |
In What Product Forms Is High-Speed Steel Available?
Depending on the use, different product forms of high-speed steel (HSS) come in a range of thicknesses. The high-speed steel round bar, for instance, is a typical product form and normally comes in thicknesses ranging from 3 to 4 inches, or around 76 to 101 mm. These round bars' high hardness and heat resistance make them ideal for a variety of cutting and machining tasks. Additionally, HSS is accessible in the form of sheets, rods, and cutting tools, each designed to meet particular industrial requirements.
Are High-Speed Steels Harder Than Tool Steels?
Yes, high-speed steels (HSS) are generally harder than tool steels. The high-speed steels are specifically designed to withstand higher temperatures and maintain their hardness at high cutting speeds. High-speed tool steels have tungsten and molybdenum contents that sum to at least 7%, and at least 0.6% carbon. They may also contain additions of vanadium, carbon, and other elements. These alloys offer superior strength and hardness compared to traditional tool steels. Nonetheless, tool steels exhibit excellent hot toughness and exceptional resistance to wear when exposed to elevated temperatures.
Is High-Speed Steel Comparable to M2 Tool Steel?
Yes. M2 steel is one of the high-speed steels, so its characteristics are similar to those of other alloys in the group. In fact, M2 is one of the most popular grades of high-speed steel. It is well-suited for a variety of cutting applications due to its hardness, wear resistance, and heat resistance.
What Is the Machinability Rating of a Typical High-Speed Steel?
The machinability rating of M1-M62 molybdenum-based high-speed steels is typically in the range of 20-40%. The machinability rating of M1-M62 molybdenum-based high-speed steels, typically in the range of 20-40%, represents the percentage relative to a baseline material, which is usually a standard reference material like AISI 1112 steel. This means that these steels are 20-40% more difficult to machine compared to the baseline material. This percentage reflects the moderate difficulty in machining due to their high hardness, wear resistance, and alloying elements . These properties lead to increased tool wear and heat generation during cutting processes. To mitigate these issues, selecting the right cutting tools, optimizing cutting parameters, and employing effective coolant/lubrication strategies are crucial. Proper tool geometry also plays a role in achieving desired machining results while maintaining tool life and workpiece quality.
What Are the Characteristics of High-Speed Steels?
The characteristics of HSS include extraordinary hardness and abrasion resistance. This makes the high-speed steel group of alloys a popular option for industrial cutting tools, including milling cutters, broaches, tool bits, saw blades, taps, and drills. Different HSS alloy grades offer the user many ways to adjust the trade-offs among strength, toughness, hot hardness, and abrasion resistance.
Are High-Speed Steels Rust-Proof?
No, high-speed steel (HSS) is not rust-proof. It contains alloying components, such as chromium, which can improve its corrosion resistance in comparison to standard carbon steel. HSS can nevertheless corrode in severe settings and when exposed to moisture. HSS tools can benefit from proper storage, upkeep, and protection using coatings or oil to help prevent rust.
Can High-Speed Steels Be Welded?
Yes, high-speed steel (HSS) can be welded. After welding, it's often necessary to perform heat treatments like soft annealing, tempering, or stress relief annealing depending on the specific requirements and condition of the tool. These heat treatments help modify the properties of the welded HSS tool to ensure functionality and durability. Soft annealing is particularly recommended to reduce the risk of cracking during subsequent heat treatment and machining. Steel containing a high carbon content is generally regarded as having limited weldability. Tool steels, which normally have carbon content ranging from 0.3% to 2.5%, present welding challenges, mainly because of the presence of alloying elements among other factors.
Can You Bend High-Speed Steels?
Yes, high-speed steel (HSS) can be bent, but it's best done before the HSS undergoes heat treatment to reach its final strength and hardness. Any bending of HSS should be performed while it's in an annealed state and at high temperatures. For example, M42 high-speed steel should not be forged below 930 °C. After bending, the material would need to be hardened to restore its desired properties. Bending HSS after heat treatment is generally not recommended due to its increased hardness.
Are High-Speed Steels Stronger Than Titanium?
Yes, high-speed steel (HSS) is generally stronger than titanium when considering tensile yield strengths. While titanium offers more strength per unit mass, steel, including HSS, is a better choice for applications where overall strength is a primary concern. Steel is commonly used in construction and various industries due to its high tensile strength, while titanium is favored in automotive and aerospace designs where a balance between strength and weight is crucial. The choice between the two materials depends on the specific requirements of the application.
What Are the Uses of High-Speed Steels?
High-speed steels (HSS) encompass a family of tough tool steels utilized in various cutting tool applications, including:
- Drills
- Taps
- Milling cutters
- Lathe tools
- End mills
- Reamers
- Broaches
- Saw blades
- Chisels
- Punches
How Long Will High-Speed Steels Last?
Tools made of high-speed steel (HSS) can have a long lifespan if they are treated with proper care. HSS tools are strong and heat-resistant, making them durable choices. For example, HSS drill bits, when handled with care, have been known to last for many years. This proper care includes optimizing feeds and speeds for the material being machined, ensuring proper lubrication at the work/tool interface, and regularly sharpening the tools as needed. These practices help maintain their sharpness and effectiveness over an extended period.
How Much Do High-Speed Steels Cost?
The cost of high-speed steels (HSS) varies based on the specific type and grade. For example, tungsten high-speed steel (T1 HSS) can cost between $8.00 and $10.00 per kg, while M35 high-speed may range from $799.00 to $900.00 per kg.
What Are the Most Common Forms of High-Speed Steels?
Solid bars or rods are the most common forms of high-speed steels (HSS). Bar stock serves as the starting point for the creation of a variety of cutting tools, including drills, end mills, and reamers.
Can High-Speed Steels Be Used in Electrical Wires?
No, high-speed steel (HSS) is not typically used in electrical wires. HSS is primarily employed in cutting tools due to its hardness and heat resistance, not in conducting electricity . It lacks the electrical conductivity required for use in electrical wires. Copper and aluminum are the more common materials used for conducting electricity due to their excellent conductivity properties.
What Are the Advantages of High-Speed Steels?
High-speed steels (HSS) offer numerous advantages, such as:
- Withstands high temperatures (600-620 °C).
- Withstands shock and impact forces.
- High cutting speeds – faster to cut with than traditional alloys like bronze or cast iron.
- Hardness suited for cutting and drilling hard materials.
- Wear resistance for extended tool life.
- It can create precise cuts in various materials.
What Are the Disadvantages of High-Speed Steels?
The disadvantages of high-speed steels (HSS) include:
- High brittleness.
- Low vibration resistance.
- Reduced wear resistance in high-temperature conditions.
What Is the Difference Between High-Speed Steel and Carbide?
Carbide tooling offers superior efficiency, retains sharpness at high temperatures, and boasts a broader cutting speed range and increased rigidity compared to HSS. It excels in various cutting applications, delivering exceptional surface finishes. Carbide is the preferred choice for machining cast iron, plastics, and nonferrous materials, thanks to its outstanding performance attributes.
What Is the Difference Between High-Speed Steel and Carbon Steel?
High-speed steel (HSS) and carbon steel taps differ significantly, starting with their composition. HSS taps are composed of a specific alloy designed for exceptional durability. In contrast, carbon steel taps are softer and dull quickly due to their composition. HSS taps maintain their sharpness and are less prone to breaking. Despite being more expensive, HSS offers faster cutting, prolonged sharpness, and superior overall durability. These distinctions arise from the fundamental differences in their composition, making HSS a preferred choice for demanding machining tasks.
Summary
This article presented high-speed steel, explained it, and discussed its various properties and uses. To learn more about high speed steel, contact a Xometry representative.
Xometry provides a wide range of manufacturing capabilities and other value-added services for all of your prototyping and production needs. Visit our website to learn more or to request a free, no-obligation quote.
Disclaimer
The content appearing on this webpage is for informational purposes only. Xometry makes no representation or warranty of any kind, be it expressed or implied, as to the accuracy, completeness, or validity of the information. Any performance parameters, geometric tolerances, specific design features, quality and types of materials, or processes should not be inferred to represent what will be delivered by third-party suppliers or manufacturers through Xometry’s network. Buyers seeking quotes for parts are responsible for defining the specific requirements for those parts. Please refer to our terms and conditions for more information.
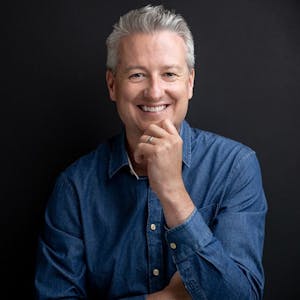