Material testing is performed to better understand a material’s properties and behaviors in specific environments and under specific loading conditions. The type of testing used will vary depending on the material type, service environment, and loading experienced in service. All parts are either loaded in tension, compression, shear, torsion, or a mixture of each. Various methods of testing help manufacturers understand a material’s properties and behaviors to select the right material for a given application.
In addition, manufacturers can test production samples to ensure high production quality. This ensures that the product is fit for its intended application and guarantees customer satisfaction. Due to variability in testing, standards are created by international standards organizations to guide how to properly perform material testing.
This article will discuss the different types of material testing and their significance.
1. Tensile Strength
A tensile test is designed to assess the modulus of a material in tension, which is when a material is pulled apart from either end. Tensile tests can be used to determine the tensile strength, yield strength, strain hardening, and ductility of a material. Tensile strength indicates the maximum stress a material can withstand before failure or deformation. The tensile test can also determine the ultimate tensile strength when a material fails, and so determines the limits of a material.
Tensile strength testing is one of the most widely used tests and can be used in any industry to test any solid material. In tensile testing, the material, usually in the approximate shape of a dog bone, is gripped from either end and pulled apart at a constant rate. An extensometer in series with the test load determines the elongation of the material and plots it against the applied stress to create a stress/strain curve graph. The standard for tensile testing will depend on the material being used. ASTM E8 and ISO 6892-1 are standards used for metals, whereas ASTM D638 and ISO 527-1 are standards for plastics.
For more information, see our full guide on What is Tensile Strength?
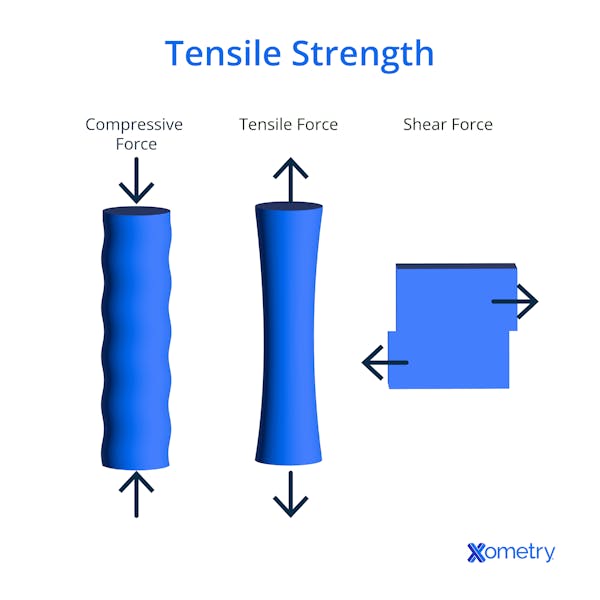
2. Compression
Compression testing is designed to determine the strength of a material that is pushed together from either end, the opposite of a tensile test. A compression test is performed by a universal testing machine with a compression tool. Compression testing is important in finding out the buckling behavior of metal and the crushing behavior of cardboard. A compression test is commonly used on springs, medical implants and stents, foam packing, and pipework.
In a compression test, the material is placed between two plates, which form the compression tooling for the universal test machine. One of the two plates moves towards the other at a constant rate. Stress is applied to the material under compression, and the testing machine records the applied stress and deformation to plot a stress/strain curve. The most tested materials in compressive testing are foams and plastics, but compressive testing is also used for metals and composites. The standards for compression testing include ASTM D695 for rigid plastics, ASTM D3574-C for foams, ISO 844 for cellular plastics, and ASTM F1306 for penetration resistance of films and laminates.
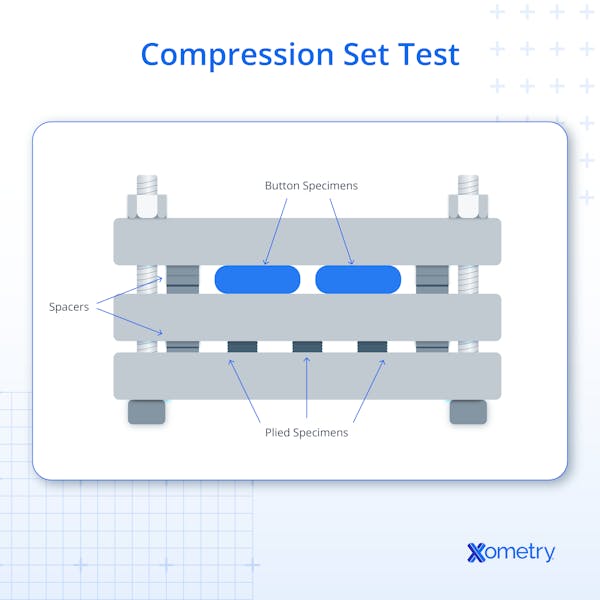
3. Flexure/Bend Strength
A flexure test, also known as a bend test or three-point bend test, is used to determine the tensile and compressive strength properties of a material at the same time. Flexure testing is important for testing brittle materials as measuring the tensile strength of brittle materials can be difficult due to the failure behavior. Flexure testing is crucial to testing surface material properties and can determine the stiffness, flexure stress and strain, and strength of a material.
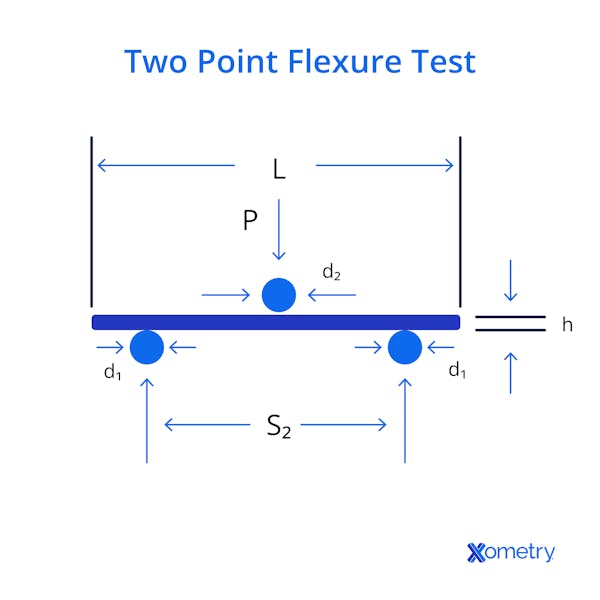
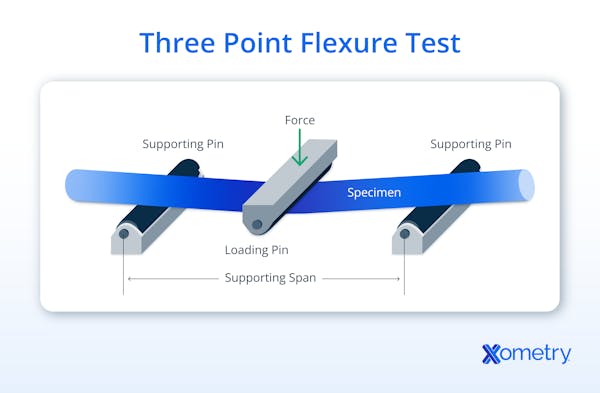
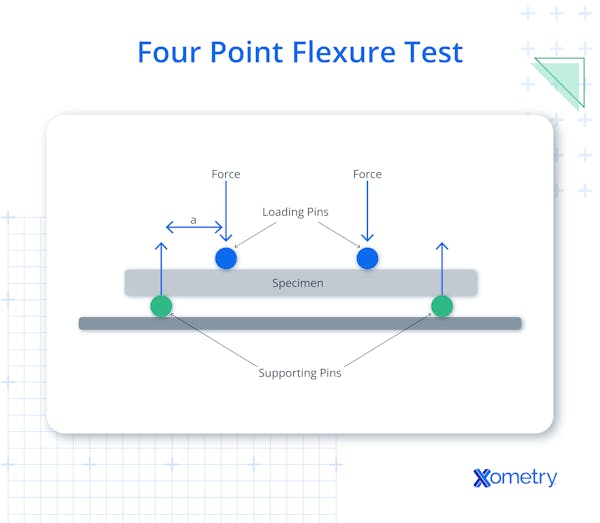
An illustration of a two point flexure test
A flexure test can be performed with a two-, three-, or four-point flexure test. In a two-point test, the specimen is gripped at one end, and then a load is applied to the other end of the material. In a three-point test, the specimen is gripped at both ends, and the load is applied in the middle. A four-point test also grips the specimen at both ends but applies the load at two points between the ends; the force is applied in an even and balanced way. There are many standards for flexure testing; however, some well-used ones are ASTM C67-08 for testing brick, ASTM E855 for metallic spring materials, BS EN 2746:1998 for glass-reinforced plastics, and BS EN ISO 7438:2005 for metallic materials.
4. Coefficient of Friction
Coefficient of friction testing is used to determine the resistance between two surfaces when they move against each other. The coefficient of friction is the ratio between the force required to slide the material against the force perpendicular to the surface. The lower the coefficient of friction, the lower the resistance to sliding. The most common use of coefficient of friction testing is to determine the friction of packaging materials to understand how the material will perform during shipping. It can also be used to determine the wear properties of components.
In a coefficient of friction test, a material of a known weight is pulled along a horizontal surface, and its resistance to the pull is measured. The coefficient can then be determined using the resistance and the weight (force acting perpendicular to the surface). Coefficient of friction testing is used for testing plastic films, lubricant fluids, and metals. The standards for testing the coefficient of friction are ISO 8295 and ASTM D1894 for plastic films, and ASTM D4172 for lubricant testing.
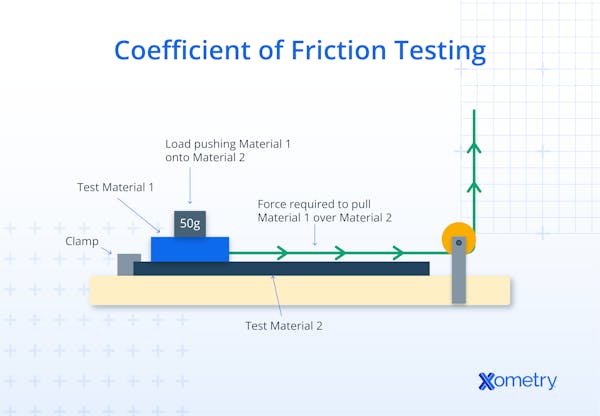
5. Puncture Strength
Puncture testing is used to determine the puncture or rupture behavior of a material. This is performed by clamping the material around its perimeter and then applying force with a probe until the material ruptures. This testing is mostly used for ductile materials such as plastic, rubber, or textile films or membranes. Puncture testing may also be used to determine the sharpness of a blade or syringe using the same method. The most used puncture test standards include ASTM D4833 for puncture resistance of geomembranes, ASTM D5748 for puncture resistance of stretch wrap, and ASTM F1306 for penetration resistance of films and laminates.
6. Tear Resistance
Tear resistance is the resistance of a material to a tensile load after a tear has been initiated. Tear testing is used to understand a material’s failure mode and can be used in the structural analysis of parts. The tear resistance of a material is also important to know for clothing, packaging, tents, and bulletproof vests.
A tear resistance test is performed by creating a tear in the material and then loading the material in tension with increasing force until the material deforms. The force required to deform the material is divided by its thickness to determine the tear resistance. Standards used for tear resistance testing include ASTM D1004 for tear resistance at low loads, ASTM D624 to determine the tear resistance of thermoset rubbers, thermoplastic elastomers, and silicons, and ASTM D2261 for the tear resistance of textiles.
7. Peel Strength
Peel strength is used to determine the bond strength of adhesives. The purpose of the test is to determine the failure modes and the force required to seperate the material. Peel testing is important to understand the failure of an adhesive such as cohesive and adhesive failure modes. Cohesive failure is where the adhesive fractures and therefore remains on both of the substrates, adhesive failure is where the adhesive fails to stick to one of the surfaces. Cohesive failure is desirable as it means the adhesive is effective at adhering to the substrate.
Peel strength tests adhesives that bond both flexible and rigid materials together. In a peel strength test, two substrates are bonded together and then pulled apart using a tensile tester. Peel strength testing standards include ASTM D5458 for stretch wrap film, ASTM D6862 for peel resistance at 90 degree angle, ASTM D903 for stripping strength of adhesives, and ISO 11339 for T-peel tests of two flexible materials that are bonded together.
8. Shear Strength
A shear strength test is used to determine a material's behavior in the shear condition. The shear condition is one in which two tensile or compressive loads act on a material in a non-concentric fashion. An example is a pair of scissors, where two opposing loads act on a material. Shear strength testing can, and is, used to determine a material's resistance to shear. But it is more commonly used to test adhesives by pulling a single lap joint apart using a tensile testing machine. Shear testing of adhesives can be used for applications in aerospace, construction, electronics, and packaging. Shear strength is important to understand a material’s failure mode and deformation characteristics. Standards used for shear strength testing include: ASTM D3164 for strength properties of adhesives in static shear by tension loading of single-lap-joint specimens, ASTM D732 for shear strength of plastics by punch tool, and ASTM D1002 for shear strength of metal adhesives.
9. Delamination Strength
Delamination strength is the resistance to the tensile forces of two laminates that are bonded together. Delaminations are a common concern for materials that are built up in layers such as composites, especially sandwiched composites in which delamination between the core and skin of the composite is common. Delamination strength testing is used to determine the peel resistance of composite skins bonded to core materials such as honeycomb or foams.
In a delamination strength test, two substrates that have been cured together with an adhesive are placed under a tensile load to determine the bond strength of a material. The test standards for delamination strength testing are ASTM D1781 for a skin-to-core bonding test and ASTM D5824 for adhesive bonds to a wood core.
10. Bond Strength
A bond strength test is used to test the strength of an adhesive to stay attached to a material. The test is conducted by bonding two surfaces together, allowing it to cure, and then stressing the materials until the bond fails to determine the bond strength. Bond tests can be carried out at varying temperatures which affect bond strength, and stressed with different loads, which affect the bond differently.
For example, a joint in tension will often have different failure modes than a joint in shear. Bond testing is intended to be used on bonding within motors, and also on adhesives, including polymers, composites, and glues. The testing of these materials can be carried out when the material is applied to plastics, metals, and ceramics. Testing standards for bond strength include ASTM D1002 for single lap joint bonds, ASTM D3163 for rigid plastic testing, and ASTM D3164 for plastic and metal substrates.
11. Adhesion Strength
Adhesion strength testing is different from most adhesion testing as it measures the force required to remove the adhesion from the substrate rather than the force required to make the adhesive fail cohesively. The adhesive materials usually tested for adhesion strength are coatings and finishes, including: paint, ceramic coatings, resins, laminates, elastomerics, and glass. These materials are tested for their adhesion to metals, wood, ceramics, and plastics.
The most common way to test adhesion strength is to use a pull-off test. In a pull-off test, a dolly is fixed to a coating using an adhesive. The user then pulls off the attached dolly until the adhesion fails. Then, the testing machine records the force required per unit area. Adhesion strength testing standards include ASTM D4541 for testing the pull-off strength of coatings, ASTM D2197 for scrape adhesion of organic coatings (ceramic and glass), and ISO 4624 for the pull-off tests for paints and varnishes.
12. Break Load
A break load test is a material test designed to identify the force required to fracture a material and can be a form of compressive or tensile loading. In a break test, criteria for a break must be identified, and two types of break criteria must be used. The first is a sharp break, which is, defined as when a material load strength is reduced by a significant amount (often 5% or more, depending on the standard).
The second is a percentage break, which is defined by the relationship between the material load and degradation after peak loading. Break tests can involve compressive, tensile, or bending loads to determine the point of material failure. Testing standards for break load testing are ASTM C203-22 for break-loading of thermal insulation and ASTM D4632 for break-loading of geotextiles.
13. Creep
Creep tests are used to determine a material's deformation when subjected to a constant load for a sustained time at a constant temperature. All materials perform differently at raised temperatures and most lose strength among other mechanical properties. Therefore, creep tests are used to understand a material's properties under varying temperature conditions. Creep testing is a tensile test that is performed at constant temperature for hours or longer. The temperature must be constant as any change can cause expansion or contraction of the material.
During the test, the elongation is measured and plotted at regular intervals. The results of the test will show three distinct phases when plotted. The primary stage is where the creep rate is highest, in the secondary phase, the creep plateaus, and in the tertiary phase, the creep rate increases again before total failure. Creep testing is mainly used for metals, composites, and plastics operating at high temperatures. Common standards for creep testing are ISO 899-1 for creep testing on plastics, ASTM E139 for creep of metallic materials, ASTM D2294 for creep of adhesives, and ASTM E2714 for creep-fatigue testing.
14. Crush Resistance
Crush resistance testing is a form of compressive testing that applies a load until the specimen fractures, deforms, collapses, or shatters. A universal testing machine is used to measure a material's ability to resist deformation under a compressive load. This testing is used for applications that experience compressive loading in structures and packaging.
Materials that commonly undergo crush resistance testing are cardboard, glass, bearings, foam, and bricks. Standards for crush resistance testing include ASTM D642 for shipping containers, ASTM D695 for rigid plastics, ISO 3035 for corrugated fiberboard, and ISO 844 for rigid cellular plastics.
15. Deformation Strength
Deformation strength testing is designed to measure a material's ability to withstand deformation and the degree to which it deforms under load. The deformation of a material is measured as a percentage of the material's change in length. Deformation strength testing is commonly associated with compressible materials like plastics. In a deformation test, a material is compressed under two distinct loads. At each load, the length of deformation is measured. From this, the rate of deformation per unit of loading can be found. The testing standard for deformation strength testing is ASTM D621.
16. Ductility
Ductility testing is used to determine a material's ability to plastically deform without failure. It is important as it determines a material's ability to resist the formation of cracks. Ductility testing is achieved using a tensile test or bend test on a universal testing machine. Several types of bend tests may be used, including guided bend, semi-guided bend, free bend, and bend-and-flatten tests. These methods often employ specialized fixtures to control the bending angle or radius, rather than using simple three-point bending. The center is then deformed until a predetermined angle is reached. The material can then be inspected for damage and cracks, and the failure can be determined depending on the amount and type of damage. Alternatively, a specimen can be tensile tested to a predetermined length and then inspected for cracks. Standards for ductility testing are ASTM D638-14 for plastics, ASTM E8/E8M-21 for metallic materials, and ASTM E290 for bend testing.
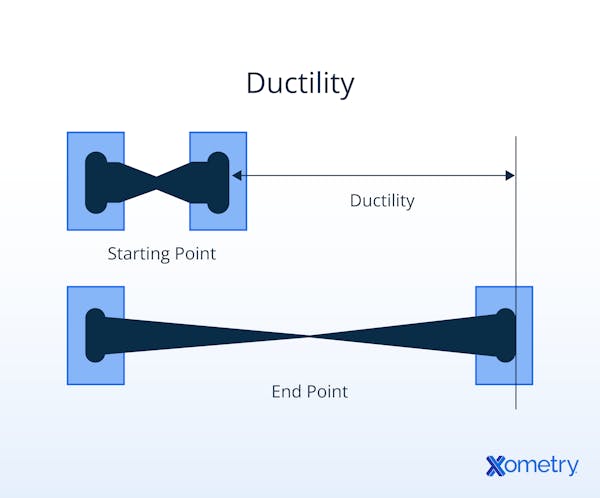
17. Elastic Limit
Elastic limit testing is used to determine a material’s limit of elastic deformation before deformation becomes plastic (permanent). Elastic limit testing can be used to identify the maximum load a material can receive regularly in service without permanent deformation. Elastic limit testing can be achieved with a universal testing machine in a tensile, compressive, or bend test. The elastic limit is often close to its proportional limit, which is the point at which the stress-strain relationship becomes non-linear. Standards for testing elastic limit include ASTM D3039 for composites, ASTM E8/E8M for metals, and ASTM E2769-18 for bend testing elastic limit.
18. Elongation
Elongation testing is used to determine a material's ductility before it breaks. The elongation of a material can be identified using a tensile testing machine. The distance between the grips of the machine is measured before the test, and when the material breaks. The change in length can then be divided by the original gauge length to determine the material elongation as a percentage. Elongation testing can be used for metals, composites, and plastics, but not ceramics, as ceramics are often too brittle to record any elongation. Standards for elongation include ASTM A370 for carbon steel, ASTM D638 for plastics, and ASTM E8 for metallic materials.
19. Rupture Strength
Rupture testing is used to determine a material's ability to resist a fracture or failure under stress. Puncture testing is related but not identical to rupture testing; puncture testing measures localized penetration resistance, while rupture testing often measures failure under broader stress conditions. In puncture testing, a material specimen is supported at each end, and a probe applies a force to the center of the material until it ruptures. This information can be used to understand the deformation failure modes and strengths of materials used in packaging applications. Rupture testing is also used to determine the ripeness of foods. Standards for rupture testing include ASTM B406 for cemented carbides and ASTM B528 for sintered metal powder.
20. Young’s Modulus
Young's modulus is the ratio of strain (change in length divided by original length) to the stress (force per unit area). Young's modulus represents the deformation of a material in a region in which the change in strain is proportional to the stress. This relationship can be tested using a tensile testing machine in which a material is exposed to a tensile load. Young's modulus is calculated by dividing the stress of a material by its strain. Young's modulus of any material can be tested, including metals, plastics, composites, and organics. Standards for Young's modulus testing include ASTM D638 for plastics, ISO 6892-1 for metallic materials, and ASTM D3039 for composites.
21. Toughness
Toughness testing determines a material’s ability to resist break or fracture and usually refers to a material's ability to resist an impact. Since toughness is a material's ability to withstand fracture formation and propagation, it can be tested by working out how much energy can be absorbed before complete failure. In a toughness test, a notch is created in a specimen and then the notch is loaded until crack propagation occurs.
The force required before crack growth begins is related to the material’s fracture toughness, but toughness more broadly refers to total energy absorption, not just maximum force. There are three modes of toughness testing. Mode I applies a tensile stress to the notch, mode II applies an in-plane (shear) stress, and mode III applies both mode I and II stresses at the same time. Toughness testing can be used on any material and is performed to understand a material's resistance to cracks. Standards for toughness testing include ISO 12135:2021 for metallics, ASTM D6671 for composites, and ISO 17281:2018 for plastics.
What Is Material Testing?
Material testing is a measurement process in which a material is exposed to a physical load to understand its properties and behaviors. Material testing can be performed on rigid or flexible metals, plastics, polymers, composites, or organic materials. The properties determined by material testing can help identify the suitability of a material for a certain application. Material testing can also be used to predict a material’s life span and predict when a material is likely to fail in service.
What Is the Purpose of Material Testing?
The purpose of material testing is to understand a material's properties and behaviors. From this, designers can determine a material’s suitability for a certain application. Material testing can also be used to predict the material’s service life in different environments and how a material interacts with other materials, such as adhesives.
How Does the Manufacturer Determine the Testing for the Specific Materials?
The testing for a particular material will be determined based on several factors, including the material type, the forces it will experience in service, and the environment it is exposed to. For example, ceramics will not be used in elongation testing as they are brittle materials that do not experience significant elongation. The manufacturer will determine if the test will be a tensile, compressive, or bend test depending on the forces the material will experience in service. If the material is used for a structural foundation, it is unlikely to experience much tension, but it will experience compression. Finally, a manufacturer may use a creep test if the material is exposed to extreme temperatures, such as in an engine.
What Are the Advantages of Material Testing?
There are many advantages of material testing to benefit from, several of which are listed below:
- Improved understanding of material performance and behavior
- Reduced risk of in-service failure
- Understanding of material failure modes
- Increased consumer confidence
- Quality control
- Advances in material development
What Are the Challenges of Material Testing for Manufacturing?
Naturally, there are many challenges to performing an accurate material test, these challenges include:
- Human error
- Parallax error
- Equipment limitations
- High costs
- Sample contamination
- Compliance with testing standards
What Does Mechanical Testing for Materials Involve?
Mechanical material testing can involve many aspects, but all testing should involve:
- Test program
- Procurement of material
- Measuring of parameters
- Recording of data
- Data analysis
- Compliance with a standard
What Is the Role of Chemical Analysis in Material Testing?
Chemical analysis is a tool used to identify and verify the composition of a material when it is tested. Without identification of the material, there is no way of associating the properties found with the material tested. For example, if aluminum is tested then the material properties could be associated with aluminum. The problem is there are many grades and compositions of aluminum all with different properties. Therefore, it is key to know the chemical composition, so the properties found can be associated with that certain material.
How Physical Testing Impacts Product Quality?
The manufacturer can ensure that production meets quality standards by physically testing the product. Physical testing is often the only way to guarantee that the materials being used and their processes result in a product with the desired mechanical properties. This will ensure that products meet the needs of their intended application.
Does Material Testing During Manufacturing Ensure High-Quality Product Output?
Yes, material testing can identify that production quality is of a high standard, and if it is not then the problem can be identified and rectified. Material testing is often the only way to ensure that the production quality is right. By testing materials and ensuring production quality, consumers can be confident in the product they buy and customer satisfaction and brand reputation can be increased and maintained.
Summary
This article presented the different types of material testing, explained each of them, and discussed when each of them is used. To learn more about material testing, contact a Xometry representative.
Xometry provides a wide range of manufacturing capabilities and other value-added services for all of your prototyping and production needs. Visit our website to learn more or to request a free, no-obligation quote.
Disclaimer
The content appearing on this webpage is for informational purposes only. Xometry makes no representation or warranty of any kind, be it expressed or implied, as to the accuracy, completeness, or validity of the information. Any performance parameters, geometric tolerances, specific design features, quality and types of materials, or processes should not be inferred to represent what will be delivered by third-party suppliers or manufacturers through Xometry’s network. Buyers seeking quotes for parts are responsible for defining the specific requirements for those parts. Please refer to our terms and conditions for more information.
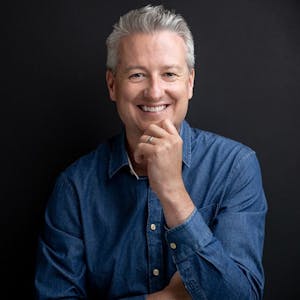