Nylon is the collective name for the family of polyamide polymers, first synthesized by Wallace H. Carothers. This research served to redefine and energize the study of petroleum-based synthetic polymers. Nylon fibers can be pulled from the molten material, or extruded to form filaments of various sizes using spinnerets. These range from fine fibers to large monofilaments. Nylon's strength and shock resilience equip it as a good material for the manufacture of low-cost, high-value products or parts. Its low coefficient of friction makes it suitable for rollers, seals, and wheels that must endure large forces. Several of its properties can also be improved by glass fiber or carbon fiber fillers, in the raw material. Acetal, also known as polyacetal, polyoxymethylene (POM), polyformaldehyde, and polyethylene glycol is a broad family of polymers that are generally manufactured by the polymerization of formaldehyde (CH2O).
These polymers offer high strength, durability, abrasion resistance, dimensional stability, and varying levels of impact resilience. They are often used as gears, bearings, and sliding components and can be considered as a substitute for light metals, with some property advantages.
This is combined with good temperature performance, however, the homopolymers are susceptible to acids, which degrade the properties and eventually break down the material. Antioxidants and acid-scavenging chemistries (nitrogen complexes and base salts) are often added, which also significantly improves this issue. Some forms are not temperature stable, but DuPont homopolymers undergo a condensation reaction with acetic acid, terminating the polymer chains with acetate groups, which improves this unwanted trait. This article will compare nylon vs. acetal in terms of applications, properties, and cost.
Nylon is the family name for a group of synthetic thermoplastics belonging to the polyamide class. It is usually manufactured by the reaction of diamines and a dicarboxylic acid. The process results in making molecules with carboxylic groups with an amine group at both ends. Nylon can also be manufactured from the lactam of an amino acid that undergoes self-condensation. These possess a ring of ―CONH― groups, an example being ε-caprolactam.
The earliest use of the material was as a replacement for silk. Nylon makes very elastic fibers that will extend significantly before fracture. The material is capable of withstanding large abrasion loads and is highly resistant to most chemicals and organism attacks. Nylon is also an excellent vibration damper, as it flexes at the microscopic scale rather than simply transmitting cyclic loading.
Figure 1 is an example of a nylon part made by Xometry:
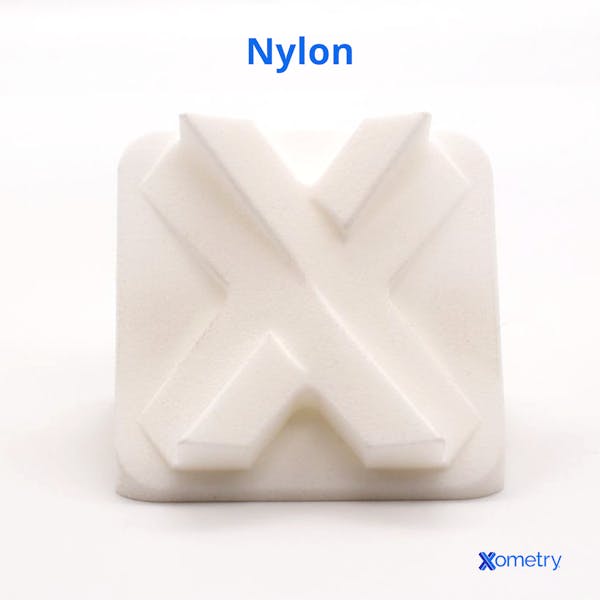
Nylon comes in various types: nylon 11, 12, 46, and 66, whose naming reflects the details of their chemical construction. The first number is the diamine carbon atoms count, whereas the second refers to the acid component’s carbon count. The family is usually referred to as PA (polyamide) followed by the carbon number count 6, 11, 12, etc. Generally, the material is supplied in black, white, and off-white (natural) variants. Nylon 66 is very widely used in engineering applications and has the (C12H22N2O2)n structure, where n represents the polymer chain nature of the bracketed monomer.
Understanding Acetal
The acetal polymers group can include both polyethers (-C-O-) and polyacetals (-O-C-O-). These are then divided into: homopolymers, manufactured using either formaldehyde or trioxane monomers; and copolymers, which combine two or more monomers.
Homopolymers are highly crystalline thermoplastic materials, generally having a helical atomic structure. The copolymers generally include small quantities of other cyclic ethers with additional methylene groups in the polymerization stage. The methylene components tend to result in better thermal and hydrolytic stability, which improves resistance to depolymerization.
As a result of its very good mechanical properties, acetal has become the preferred option for machine parts, manufacturing jigs, and metal component replacement. A wide spectrum of material options, chemical and UV resilience additives, and mechanical/electrical performance additives are available, making this a very broad family of specialist materials. The use of such additives applies to a wide range of niche applications.
Acetal poses severe health hazards during processing and in overheating conditions, as many forms break down to release formaldehyde gas. Good ventilation should be maintained in machining as, under even the moderate heat of rotating tools, trace formaldehyde can be released.
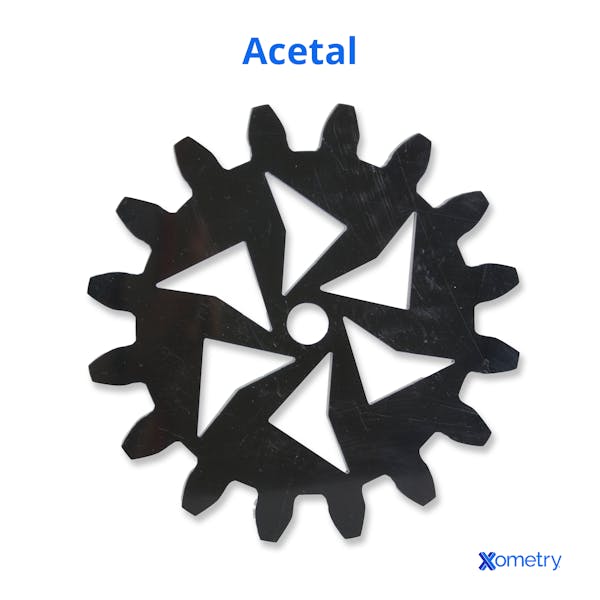
Nylon vs. Acetal: Applications and Uses
Nylon has various consumer and industrial applications, including:
- Automotive: Lower stress engine parts and housings; generally nylon 12 because of its temperature tolerance, often 20% or more glass filled, for improved rigidity and strength.
- Coatings: Powder coating materials.
- Electrical: Insulator components, in 110/240V and 3-phase electrical installations.
- Engineering: Fasteners (bolts, nuts, washers, self-lock in steel nuts), plane (or plain) bearings, toothed gears, housings and impact pads, rollers, wheels, and seals.
- Fabrics: Tough upholstery cloth and tarpaulins, webbing and automotive safety belts, umbrella fabric, waterproof clothing, parachutes, tents, yarn, and tights/stockings.
- Monofilaments: Rope, fishing nets, and brush bristles.
- Tracks: For light earthmoving vehicles.
Acetal is used in limited engineering applications for strength, wear resistance, and easy machinability. This includes:
- Bearings
- Gears
- Moving machine parts
- Manufacturing fixtures
- Jigs
Acetal offers relatively poor cosmetics and is never used in consumer goods manufacture. Some forms of acetal are widely used as load-bearing and wear-resistant components in medical prosthetics, where chemical stability is valued.
Nylon vs. Acetal: Physical Properties
Table 1 shows the properties comparison of nylon (nylon 6 PA), POM H (Delrin® 100CPE NC010), and POM C (BASF Ultraform® H 2320 006 Q600):
Property | Nylon 6 PA value (metric) | POM H (Delrin® 100CPE NC010) (metric) | POM C (BASF Ultraform® H 2320 006 Q600) (metric) |
---|---|---|---|
Property Optical transmission | Nylon 6 PA value (metric) Can be transparent, when based on cycloaliphatic monomers | POM H (Delrin® 100CPE NC010) (metric) Slightly translucent | POM C (BASF Ultraform® H 2320 006 Q600) (metric) Slightly translucent |
Property Density | Nylon 6 PA value (metric) 1.1–1.17 g/cm3 | POM H (Delrin® 100CPE NC010) (metric) 1.42 g/cm3 | POM C (BASF Ultraform® H 2320 006 Q600) (metric) 1.40 g/cm3 |
Property Hardness, Shore D | Nylon 6 PA value (metric) 70–85 | POM H (Delrin® 100CPE NC010) (metric) 86 | POM C (BASF Ultraform® H 2320 006 Q600) (metric) 85 |
Property Tensile strength, ultimate | Nylon 6 PA value (metric) 50–90 MPa | POM H (Delrin® 100CPE NC010) (metric) 31 MPa | POM C (BASF Ultraform® H 2320 006 Q600) (metric) 64 MPa |
Property Tensile strength, yield | Nylon 6 PA value (metric) 40–100 MPa | POM H (Delrin® 100CPE NC010) (metric) 67 MPa | POM C (BASF Ultraform® H 2320 006 Q600) (metric) 72 MPa |
Property Elongation at break | Nylon 6 PA value (metric) 5–120% | POM H (Delrin® 100CPE NC010) (metric) 45% | POM C (BASF Ultraform® H 2320 006 Q600) (metric) 30% |
Property Modulus of elasticity | Nylon 6 PA value (metric) 1.3–4.2 GPa | POM H (Delrin® 100CPE NC010) (metric) 3 GPa | POM C (BASF Ultraform® H 2320 006 Q600) (metric) 2.8 GPa |
Property Flexural yield strength | Nylon 6 PA value (metric) 20–150 MPa | POM H (Delrin® 100CPE NC010) (metric) 76 MPa | POM C (BASF Ultraform® H 2320 006 Q600) (metric) — |
Property Flexural modulus | Nylon 6 PA value (metric) 1.3–3.7 GPa | POM H (Delrin® 100CPE NC010) (metric) 2.8 GPa | POM C (BASF Ultraform® H 2320 006 Q600) (metric) 2.45 GPa |
Property Dielectric constant | Nylon 6 PA value (metric) 3.1–12 | POM H (Delrin® 100CPE NC010) (metric) 4 | POM C (BASF Ultraform® H 2320 006 Q600) (metric) 3.8 |
Property Melting point | Nylon 6 PA value (metric) 190–238 °C | POM H (Delrin® 100CPE NC010) (metric) 178 °C | POM C (BASF Ultraform® H 2320 006 Q600) (metric) 166 °C |
Property Max service temperature | Nylon 6 PA value (metric) 60–180 °C | POM H (Delrin® 100CPE NC010) (metric) 140 °C | POM C (BASF Ultraform® H 2320 006 Q600) (metric) 155 °C |
Nylon vs. Acetal: Recyclability and Sustainability
The whole polyamide (nylon) family is manufactured from materials sourced from petrochemicals. There is almost no pressure towards research into substitutes made from biological source materials, as nylon is a very low-cost material. Nylons are not biodegradable as reflected in their extremely long life in the environment. This characteristic makes them a serious pollution problem, particularly in the oceans due to the prevalence of lost fishing nets and ropes. The plastic becomes increasingly broken apart by wave/rock action; small pieces, microparticles, and nanoparticles particularly impact birds and marine fauna such as turtles. Nylon is highly recyclable, but because it is used in fabrics and ropes, these are almost impossible to sort.
The acetal family is made from chemistries that are derived from hydrocarbon sources. The market for the entire acetal family is small and highly specialist. There appears to be no activity in either bio-sourced raw materials or biodegradable versions of the materials.
Acetal (when pure and sorted) is highly recyclable, but its usage is quite limited, so few recycling service providers have any commercial interest in handling it. Also, it is generally used for very long-lived and highly customized components, so it rarely carries the recycling identification mark (as “other”) ♹. Materials presented for recycling without identifying marks, and in small quantities, are rarely processed but instead passed into the waste stream for landfill or incineration. Additionally, the variants in chemistry in the range of acetal materials make recycling impractical. The additives are unidentified (and impossible to remove) and the polymer chemistries are varied to the extent that the recycled material would have widely varying properties.
Nylon vs. Acetal: Cost
The price of bulk nylon 6 granules (example material) for molding ranges from $1.80–2.20 per kg. The price of nylon 6 fiber is $2.12–2.50 per kg. Acetal copolymer and homopolymer granules for molding are priced between $1.60 and $8.00 per kg for basic grades with generic and famous branding. Additive grades carrying metal powders, carbon fibers, PTFE and graphite fillers, and nanocomposite materials vary significantly in price.
Alternative Materials to Nylon and Acetal
There are many alternatives to nylon and acetal, the selection of which depends on the application. Options for nylon are:
- Fibers: Silk, wool, rayon, polyester, lycra, hemp, bamboo, and cotton.
- Molding: ABS (acrylonitrile butadiene styrene), HDPE (high-density polyethylene), PBT, PET, POM (acetal), and PP (polypropylene).
Acetal tends to be used at the extremes of polymer properties for strength and wear resistance and has extremely good machining properties. Alternative materials for machine parts are higher grades of nylons, reinforced fluoropolymers, and metals. In industrial fixtures, it's common to use Tufnol® (and similar) composites as acetal alternatives.
Summary
Xometry provides a wide range of manufacturing capabilities and other value-added services for all of your prototyping and production needs. Visit our website to learn more or to request a free, no-obligation quote.
Copyright and Trademark Notices
- Kevlar® and Dupont® are registered trademarks of the E.I. DuPont de Nemours Company.
- Tufnol® is a registered trademark of the Tufnol Company
- Ultraform® is a registered trademark of BASF SE, Germany
Disclaimer
The content appearing on this webpage is for informational purposes only. Xometry makes no representation or warranty of any kind, be it expressed or implied, as to the accuracy, completeness, or validity of the information. Any performance parameters, geometric tolerances, specific design features, quality and types of materials, or processes should not be inferred to represent what will be delivered by third-party suppliers or manufacturers through Xometry’s network. Buyers seeking quotes for parts are responsible for defining the specific requirements for those parts. Please refer to our terms and conditions for more information.
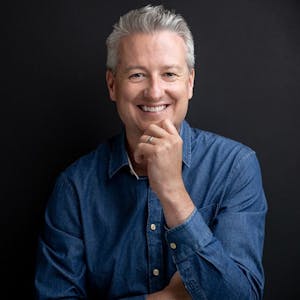