Creep is the plastic deformation of a material due to being constantly loaded under stress over an extended period of time. There are some similarities to elongation testing; however, elongation is tested by increasing the tensile stress on a sample until it breaks, whereas creep is tested by applying a constant force over an extended time. The creep of materials is governed by various mechanisms, such as diffusion creep and dislocation creep. The limiting mechanism depends heavily on the molecular structure of the material. Solute drag creep is one such mechanism. It typically occurs in metal alloys in which the atomic size of the alloying material is significantly different from that of the base metal.
Creep is a complex phenomenon that proceeds via a range of different mechanisms, depending on the crystal structure of the solid solution. The temperature plays a large role in controlling such creep mechanisms. Creep can be modeled and predicted via an equation to estimate the time before a component that is susceptible to creep will fail. It is therefore important to understand the controlling mechanism of creep in each application. This article will discuss solute drag creep, how it occurs, the factors that contribute to it, as well as how it can be reduced.
What Is Solute Drag Creep?
Solute drag creep is a mechanism of creep that under particular conditions can be the limiting factor in the overall creep strain rate. Solute drag creep may be present at elevated temperatures and constant load. When stress is applied, dislocations occur within a solid solution (such as a metallic alloy) and can move through the crystal lattice, allowing the deformation of the material. However, with solute drag creep, the solute concentrates at the dislocations, creating a solute atmosphere around them. In order for the vacancies in the lattice to move, they need to diffuse through the solute atmosphere, which can be a slow process. Thus, the solute induces a hindrance to the movement of dislocations within a solid solution. For more information, see our guide on What Causes Creep.
How Does Solute Drag Creep Occur?
Solute drag creep occurs in some alloy metals, according to the following mechanism:
- Strain on the material introduces some dislocations within the structure, and the solute (alloying element) atoms concentrate around these dislocations.
- This local concentration of solute atoms forms a solute atmosphere at the dislocations.
- This induces a “drag” on the movement of the dislocations, slowing their progress through the material, as the movement of the dislocation through the solute atmosphere is limited by the diffusivity of the solute.
Solute drag creep, therefore, exhibits a form of solid solution strengthening, whereby the deformation of the material is resisted by the dynamics of the solution.
What Are the Factors That Contribute Solute Drag Creep?
There are various factors that contribute to solute drag creep and, in particular, the creep strain rate. These factors are listed below:
- Temperature: Temperature is one of the biggest influences on the creep strain rate. A higher temperature provides more energy for the diffusion of the vacancies within the crystal lattice, even through the solute atmosphere associated with solute drag creep.
- Stress: The stress applied will directly affect the creep strain rate. Higher stress will contribute to a higher creep strain rate, which is true even if solute drag creep is the limiting mechanism.
- Relative Atomic Sizes Between Solute and Solvent: Solute drag creep is more likely to be a controlling factor in the creep of an alloy if the relative atomic sizes between the solute and the solvent are very different. A large difference in size makes the solute atoms concentrate more easily at dislocations and limits diffusion through the solute atmosphere.
- Diffusivity of Solute: The diffusivity of the solute in the solvent will contribute to the magnitude of the drag caused by the solvent atmosphere at a dislocation. If the diffusivity is low, a greater drag force will exist, and the creep strain rate will be limited as a result.
What Is the Importance of Solute Drag Creep in Manufacturing Processes?
It is important to accurately understand solute drag creep, particularly in manufacturing processes that experience high temperatures with consistent low loading. In these applications, creep that is induced in components will lead to dimensional changes and distortion, which will likely proceed to creep failure. Understanding solute drag creep is important to accurately predict the service life of components susceptible to creep. This feeds into the optimization of plant uptime and maintenance costs.
Further, an understanding of solute drag creep allows manufacturers to select the best alloy for the conditions. An alloy’s behavior can be tailored by carefully selecting the solutes and their concentrations. In this way, the phenomenon of solute drag creep can be leveraged to extend the service life of a component.
How Can Solute Drag Creep Be Reduced?
Solute drag creep can be reduced by manipulating the parameters that influence it. Of course, a lower temperature or lower stress would reduce the creep strain rate present due to solute drag creep. However, temperature and stress are usually not adjustable variables but are set by the operating environment that the material is to perform in. Therefore, to reduce the rate of creep strain allowed by solute drag creep, a different alloy could be used with a secondary solute introduced to reduce the diffusivity of the solute. This will therefore hinder the movement of dislocations further.
How Does Solute Drag Creep Compare to Coble Creep?
Solute drag creep is different from Coble creep in two key ways. Coble creep is primarily a mechanism of diffusion creep, in which vacancies in the lattice structure diffuse along grain boundaries. Coble creep also shows a linear relationship between stress and strain rate. On the other hand, solute drag creep is primarily a mechanism of dislocation creep and is identified as a power-law creep. Both creep mechanisms are influenced by diffusion, but how that diffusion works out in the creep mechanism is quite different. Coble creep is also less sensitive to temperature.
How Is the Solute Drag Creep Rate Derived?
The solute drag creep rate is derived through the comparison of experimental data with mathematical predictions. Generally, solute drag creep can be described using a power-law creep model. This power law can also be referred to as Norton’s law. The premise is that the creep strain rate (the rate at which deformation of the material occurs) is proportional to the stress raised to a particular power, n.
έc = Aσ^n
A is a constant which can be made up of a number of parameters, such as the Boltzmann constant, the diffusivity of the solute, the activation energy for diffusion, and other constants related to the particular material. Other terms can also be added to model temperature and time sensitivity. Generally, for solute drag creep, a three-power law is seen, where n ≅ 3.
Does Solute Drag Creep Occur on Alloy Metals?
Yes, solute drag creep does occur in alloy metals. The very mechanism of solute drag creep is that the atoms of the solute (alloying element) concentrate around dislocations within the crystal lattice. This solute atmosphere slows down the diffusion of lattice vacancies, thus slowing the movement of the dislocation. By its nature, solute drag creep occurs within alloy metals, as a solvent (base metal) and solute (alloying element) need to be present within the crystalline solid in order for the phenomenon to occur. For more information, see our guide on Alloy Material.
Is Solute Drag Creep Caused by High Temperature?
Yes, solute drag creep is more apparent at high temperatures. Solute drag creep can also occur at low temperatures. However, for dislocations to migrate within the material’s crystal structure (i.e., for creep to occur), some energy is required for the vacancies to diffuse through the solute atmosphere formed at the dislocations. It is this requirement for diffusion through the solute atmosphere that characterizes solute drag creep. At higher temperatures, more energy is available, and thus this diffusion happens much more quickly. Therefore, at higher temperatures, the creep is more apparent.
Is Solute Drag Creep Dependent on Grain Size?
No, solute drag creep is not greatly dependent on grain size. Other creep mechanisms, such as diffusion creep and grain boundary sliding, are heavily influenced by grain size. However, since solute drag creep is about the movement of dislocations, and how they are hindered by concentrations of solute atoms, it is not directly dependent on grain size.
Can Solute Drag Creep Influence Dislocation Creep?
Yes, solute drag creep can influence dislocation creep. Dislocations generally move in two ways: by gliding or by climbing. Gliding is a movement within the same plane of the crystal lattice, whereas climbing occurs when the dislocation transfers into an adjacent plane of the lattice structure, “climbing” up through the layers. Typically, dislocations move more easily by gliding rather than by climbing. However, when solute drag creep occurs, the solute atmosphere around a dislocation hinders the movement of the dislocation. This hindrance may then influence the creep to be limited by gliding rather than climbing.
What Is the Difference Between Solute Drag Creep and Harper–Dorn Creep?
The difference between solute drag creep and Harper–Dorn creep is that the former is a dislocation creep that follows a power law, whereas the latter is a diffusion creep that has a linear response to the applied stress. Harper–Dorn creep is apparent at large grain sizes (at smaller grain sizes, the limiting linear diffusion creep is Nabarro–Herring creep), and is understood to result in climb-controlled dislocation movement.
Summary
This article presented solute drag creep, explained what it is, and discussed its various applications. To learn more about solute drag creep, contact a Xometry representative.
Xometry provides a wide range of manufacturing capabilities and other value-added services for all of your prototyping and production needs. Visit our website to learn more or to request a free, no-obligation quote.
Disclaimer
The content appearing on this webpage is for informational purposes only. Xometry makes no representation or warranty of any kind, be it expressed or implied, as to the accuracy, completeness, or validity of the information. Any performance parameters, geometric tolerances, specific design features, quality and types of materials, or processes should not be inferred to represent what will be delivered by third-party suppliers or manufacturers through Xometry’s network. Buyers seeking quotes for parts are responsible for defining the specific requirements for those parts. Please refer to our terms and conditions for more information.
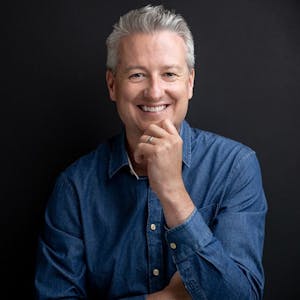