Achieving texture in plastic is a way of enhancing both the visual appeal and functionality of plastic products. The ultimate texture and appearance of a plastic part are decided by factors such as: mold tooling, the properties of the injected plastic, and any subsequent post-processing. Texture specifically pertains to the inherent pattern that forms the surface of the plastic, while finish relates to the overall visual aspect of the plastic surface. Plastic surfaces are generally categorized into four main finishes: dull, matte, semi-gloss, and gloss, each offering a distinct aesthetic quality to the final product. Texture not only adds aesthetic value but also influences the tactile experience and performance of plastic components.
Here are four ways to achieve texture in plastic:
1. Mold Texturing
Mold texturing is the most common way to add texture to plastics and is especially used in injection molding processes. This technique involves the use of textured molds or inserts that create surface patterns on the plastic as it solidifies. These molds can feature a variety of patterns, such as: grains, stippling, geometric shapes, and more.
There are different types of mold texturing techniques available. The most common ones are as follows:
- Laser Etching: Laser etching combines 3D computer modeling and a five-axis robotic arm. It enables mapping any texture onto curved surfaces. The most common use of this technique is for intricate patterns on items like dashboards in the automotive industry.
- Sanding and Polishing: After rough machining, tool marks are often left behind and can transfer to resin parts during molding if not addressed. Specialists use files, diamond burrs, rotary tools, sandpapers, and abrasives to sand and polish the inside of the mold to eliminate tool marks and other surface flaws. Textures can range from mirrored to coarse. Care is needed to avoid mold damage or changes in proportions/dimensions.
- Photochemical Etching: Plastic parts with intricate patterns like: leather, stone, or wood grain are made using photo etching on molding tools. A light-sensitive chemical, or photoresist, is applied to the tool, and the desired pattern is projected onto it using UV radiation. The exposed areas are protected, and the remaining photoresist is washed away, creating a film mask. The tool is then immersed in an acid that etches away the unprotected portions, forming the desired texture. Careful management is needed for metal type, design complexity, and surface depth. Photo etching is a quick and cost-effective method for diverse textures but has limits—it won't work on obstructed areas or may deform designs on broad, curved surfaces.
- Blasting: High-pressure air is used to spray various dry or wet abrasive media, such as: silica (sand), glass or plastic beads, aluminum oxide, and walnut shells, against the tool wall. This method efficiently cleans the tool and imparts a uniform satin or matte finish. The final appearance depends on: the medium, air pressure, volume, and spray pattern. Sandblasting is a quick, cost-effective process that minimizes raw material use.
- Spark Erosion In EDM: Spark erosion, or electrical discharge machining (EDM), utilizes an electrode made of copper or graphite in an electrolytic solution (oil or water) to produce sparks that impact the tool wall. The affected region reaches the melting point but is rapidly cooled by the liquid bath, causing thermal shock that breaks the metal into tiny particles that are flushed away almost instantly. This process is ideal for achieving tight tolerances on hard or soft metals or creating features like sharp concave corners, deep thin slots, and debossed lettering that may be challenging to machine otherwise. EDM provides a fine, smooth finish, eliminating the need for hand polishing. Although slag or excessive melt may be present in the eroded area, this method is known for its efficiency. While EDM electrodes were initially used for textured surfaces, chemical etching has largely replaced this technology.
- In-mold Decoration: IMD, or in-mold decoration, is a process that involves inserting a pre-printed or decorated film into the mold cavity before injection molding. During the molding process, the plastic material adheres to the film, effectively transferring the design or texture onto the surface of the final part. This method is widely employed for decorative and branding purposes in various industries.
- Textured Inserts: Texture inserts are elements or inserts featuring specific surface patterns that can be placed within the mold cavity before the injection molding process. These inserts are then used to transfer their unique texture to the molded plastic.
2. Post-Processing Texturing
Besides adding the desired texture of the final plastic part directly into the mold, post-processing is another way to add texture to plastic parts. This can be done through: etching, sanding, bead blasting, coatings, etc. The most common post-processing texturing techniques for plastics are discussed below:
- Coatings and Paint: Following the molding process, various coatings, including paint, clear coats, or specialized protective finishes, can be applied to enhance the aesthetic and functional aspects of the product. These coatings serve multiple purposes, ranging from improving gloss and adding texture to providing additional functionalities like UV resistance. Plastic injection-molded parts are frequently painted either for decorative purposes or to conceal surface defects. Before painting, cleaning or sanding may be necessary to optimize paint adherence. For plastics with low surface energy, such as polyethylene and polypropylene, plasma treatment is a cost-efficient alternative to deep cleaning. This treatment increases surface energy, fostering a stronger molecular bond between the paint and the plastic. Three primary painting methods are commonly employed for plastic parts: spray painting, powder coating, and silk screening.
- Laser Markings and Engraving: Laser marking is a fast and tool-less process capable of delivering high-resolution effects to plastic injection-molded parts without the need for surface preparation. This method serves as an alternative to in-mold painting and mold-in graphics, offering decorative effects post-molding. Laser engraving, a broader technique applicable to various materials, involves visible surface changes in injection-molded plastics induced by a solid-state pulsed laser. Laser marking is frequently employed to create logos or unique identifiers for products that require traceability. Traditionally, laser marking produces surface discoloration in black or gray, forming numbers, letters, or logos—an alternative to conventional printing but not suitable for plastics resistant to color changes.
- Overmolding: Overmolding is a manufacturing process in which plastic or rubber material is applied over an existing plastic part. The primary purpose of overmolding is to enhance the external aesthetic appeal of the product, making it more attractive to customers. Rubber-like materials may be used in overmolding to improve grip.
- Bead Blasting: In this method, various types of dry or wet abrasive media, such as aluminum oxide, silica (sand), glass or plastic beads, and even walnut shells, are propelled against the plastic surface using high-pressure air. The choice of media influences the final appearance, providing options for different textures. Bead blasting not only cleans the surface but also imparts a uniform satin or matte finish, adding a desired texture.
- Sanding: After the initial machining or molding process, plastic parts may have some tool marks or imperfections. Various tools such as: rotary tools, sandpapers, diamond burrs, and abrasives can be used to manually sand and polish the surfaces. The textures achieved through sanding range from mirrored surfaces to coarsely textured finishes. However, manual sanding has limitations, especially in accessing deep holes or intricate features. Alternative procedures are required for such areas.
3. Adding Fillers or Additives
Additives and fillers, whether organic or inorganic compounds are incorporated into plastics to modify their properties. While plastics typically possess inherent qualities such as impact resistance and durability, they may also exhibit characteristics like: brittleness, hardness, combustibility, or excessive weight, which may not be suitable for their intended application. The introduction of additives or fillers allows for the alteration of the plastic's properties, ensuring it aligns with the intended purpose without compromising the attractive features that initially distinguished it. Fillers and additives can also contribute to the texture of plastic parts. Various types of fillers, such as: mineral fillers like talc and calcium carbonate, fibrous fillers like aramid and carbon fibers, and microspheres, can enhance or change the surface characteristics of plastic materials. These additions not only improve texture but also impart desirable properties such as: stiffness, dimensional stability, and heat resistance. Additives and fillers are primarily used to modify the plastic’s properties. Plasticizers, like those in PVC, make plastics flexible—crucial for applications such as wires. Fillers, including minerals and carbon fibers, reduce cost and weight, and enhance characteristics like moldability and strength. Stabilizers, such as antioxidants and UV absorbers, protect plastics from degradation, extending their life span. Flame retardants minimize fire risk by delaying ignition and reducing smoke.
4. Stamping or Printing
Stamping and printing processes are another way to add texture to plastic parts. Some of the common stamping and printing processes used include:
- Hot Stamping or Heat Transfer Printing: This process involves transferring a design or metallic finish on film or foil to the plastic’s surface by applying heat or pressure.
- Pad Printing: Pad printing is a method for transferring a two-dimensional image onto a three-dimensional object. It can be used for printing images, text, or colors onto products. Pad printing is particularly useful for irregular shapes and surfaces, including: concave, round, recessed, or raised features. In this process, a 2D image is transferred to a 3D object from a laser-engraved printing plate using a silicone pad. This is achieved by pressing an ink plate into the image on the printing plate before it's stamped onto the object by the silicone pad. The quick-drying inks used in this method prevent issues like: dripping, running, or smearing. It can be used to add single or multi-color graphics and lettering.
- Silk Screening: Silk screening is a widely used printing technique for adding images, text, logos, and intricate details to components. The process involves printing the design onto a sheet, placing it in a frame, and then positioning the frame onto the part. Colored ink or dye is moved across the screen using a scraper, leaving a thin, detailed design on the part. It is particularly cost-effective for large production runs, while the durable, reusable nature of the screens contributes to its efficiency.
What Is Texturing in Plastics?
Texturing in plastic parts refers to a surface-finishing process that imparts specific visual, tactile, or grain characteristics. It is a very cost-effective way to create patterns, of varying complexity, on the surface of plastic parts. Texturing provides a wide range of options, allowing for adjustments in the roughness, patterns, and sheen of the final product. The primary objective may be to enhance appearance, performance, or a combination of both. A glossy, smooth finish, for example, might be desired for aesthetic appeal, while a coarser texture could be more suitable for particular mechanical applications.
However, the significance of surface texture extends beyond aesthetic and tactile considerations. It significantly influences various functional properties, including: mechanical performance, friction, chemical interactions, electrical resistance or conductivity, and corrosion resistance.
What Is the Importance of Texturing in Plastics?
Texturing in plastics is important both for functionality and aesthetics. For aesthetics, the addition of a textured finish can improve the visual appeal of plastic. Texturing can help designers achieve a specific look for their plastic products, but it can also be used to help obscure imperfections and blemishes in the plastic.
In terms of functionality, texturing in plastics can help improve grip for a user, as well as provide better adhesion for paint or stickers. Aesthetics and functionality can be combined by texturing only a specific area of a plastic product, for example, a section of a lid. This provides a better grip for opening the lid, while also acting as a hint for the consumer of where and how to open it.
To learn more, see our guide on Plastic Fabrication.
What Equipment Is Capable of Texturing Plastics?
Various items of equipment are capable of texturing plastic, depending on the method. They are as follows:
- Lasers can be used to etch or engrave a textured finish onto plastic.
- Air compressors can be used to blast plastic with abrasive media, resulting in a textured finish.
- Sanders or rotary tools can be used to sand, polish, or grind plastic to achieve specific textures.
- Printing equipment can be used to apply silk screening or pad printing to plastic.
What Are the Advantages of Texture in Plastics?
There are a lot of benefits that come from textured plastic parts, including visual and physical benefits. Some of the benefits that textured plastics bring to the table include:
- Texture surfaces can obscure some visual imperfections in the part like: knit lines, flow lines, sinks, blush marks, and shadow marks. Moreover, texture can create a surface resistant to incidental contact damage during shipping and prevent fingerprint smudges from handling.
- Designers select textures for various aesthetic reasons. In certain instances, it may align with a specific style or elevate the perceived value of a part. Texture can impart a sense of depth, creating a more refined look that resonates with and impresses customers.
- Textured parts can provide better grip.
- Textured parts offer better paint.
- Texturing allows manufacturers to customize a product and add some unique features to the design.
- Textured plastic surfaces are cost-effective and can appear to be non-plastic.
What Are the Challenges of Texturing Plastics?
Texturing plastics poses several challenges, including:
- The texturing process can lead to wear and tear on the mold tooling over time. As the tooling degrades, it may impact the quality and uniformity of the textured finish.
- Not all plastics respond the same way to texturing processes. Material characteristics, such as melt flow, can affect how well the texture adheres to the surface and the overall quality of the finish.
- Some texturing methods, especially those involving intricate designs or high precision, can be time-consuming and expensive.
- Post-processing steps, like sanding or polishing, may be needed to achieve the desired level of texture. These steps can add complexity to the overall manufacturing process.
What Is the Most Efficient Way to Do Texturing in Plastic?
The most efficient way to do texturing in plastic is through mold texturing. This is because the texture is incorporated into the mold and imparted to the final product. Meaning it is a one-step solution. It eliminates the need for adding texturing using post-processing methods, which adds to the cost.
Is Texturing Plastics a Form of Aesthetics?
Yes. There are two forms of surface aesthetic in plastic: surface finish and texture. The difference between the two is that finish refers to the final look of the plastic, meaning the overall visual look; whereas texture refers to the pattern in the plastic, in other words, the tactile quality of the part or how it feels when touched. However, although the texture is mainly focused on the tactile properties of an object, the pattern that you see on the object can still add to the aesthetic appeal of the product.
Can Texturing Be Done by Mold?
Yes. Mold texturing is one of the most common ways to add texture to the final piece. This involves adding texture to the injection mold’s surface, which is then used to impart the texture to the final part during the injection molding process. Mold texturing can be done in various ways, from etching the mold in a chemical bath to engraving the texture manually or through a laser for added precision. The chosen technique depends on factors such as the desired texture and intricacy of the design.
Can Texturing Be Done by Laser?
Yes, laser texturing can be done by either applying the technique to the inside of the mold or by doing it directly onto the surface of the part. With laser texturing of injection molds, interesting textures such as that of leather, wood, or geometric patterns can be added to the inner surface of the mold, which is then recreated in the final part when the molten plastic is injected into the mold.
To learn more, see our guide on Laser Engraving.
Summary
This article presented ways to achieve texture in plastic, explained each of them, and discussed the advantages of texturing plastic. To learn more about plastic, contact a Xometry representative.
Xometry provides a wide range of manufacturing capabilities and other value-added services for all of your prototyping and production needs. Visit our website to learn more or to request a free, no-obligation quote.
Disclaimer
The content appearing on this webpage is for informational purposes only. Xometry makes no representation or warranty of any kind, be it expressed or implied, as to the accuracy, completeness, or validity of the information. Any performance parameters, geometric tolerances, specific design features, quality and types of materials, or processes should not be inferred to represent what will be delivered by third-party suppliers or manufacturers through Xometry’s network. Buyers seeking quotes for parts are responsible for defining the specific requirements for those parts. Please refer to our terms and conditions for more information.
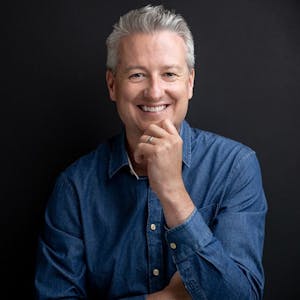