Materials that are used to make tools should understandably be particularly hardy, and tool steel fits the bill. “Tool steel” as a term refers to carbon and alloy steels that are strong enough to be made into tools that can work on wood, plastic, and other metals in various processes, like stamping and forming, to name just a couple. Hand tools, drills, cutters, and bits are more often than not made from tool steel, as are larger items like machine dies and plastic extruding machinery. There are several different types of tool steels that are categorized into grades (and there are a few sub-grades, too), so to figure out what each grade is good for, keep reading. We’ll also cover what exactly is in tool steel and how it’s made.
What is Tool Steel?
Tool steels are hard, tough, and wear-resistant metals that won’t soften at high temperatures. They’ll typically have 0.7–1.5 wt% carbon in them, but some can have anywhere from 0.2–2.1 wt%. Although a higher carbon level will make the steel stronger and more hardenable, it will also make it brittle and less easy to weld. When cold-worked, tool steels are around 60/62 HRC on the Rockwell C hardness scale, but could range between around 58/64 HRC (some have been known to reach 66). Tool steel can withstand heat treatment, with the specific temperature being dependent on its exact composition. Here’s what it looks like before it’s made into tools:
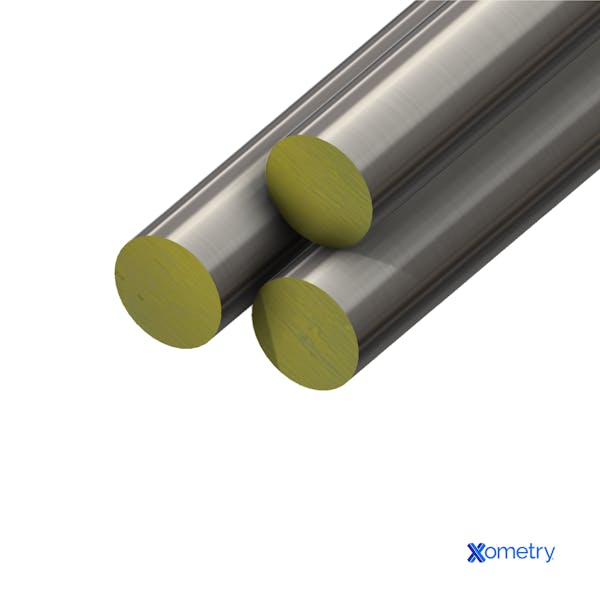
In addition to carbon, tool steels will have other elements to improve their strength and change their properties according to what exactly the tool is needed for. For instance, nickel or cobalt can be added to give the metal extra strength and high-temperature resistance, while adding carbide former made from different combinations of iron-based alloys, like tungsten, vanadium, chromium, and/or molybdenum, can make it more wear-resistant.
How It’s Made
Although the main method for making tool steel is via electric arc furnaces (EAF), this is not the only way. Below we’ll cover the processes used to make it.
EAF: Recycled steel scrap is melted and purified in a furnace, with the alloying elements mixed in until the composition is just right. Chemicals are added to keep oxidation at bay and remove impurities, and it’s then poured into a ladle (an oversized bucket with a spout). It’s then put into giant ingot molds and carefully cooled.
Electroslag refining (ESR): This process melts the metal extremely slowly for a smooth and non-porous surface.
Powder metallurgy: The metal powders are pressed and sintered until they’re solid and dense.
Annealing: To make the steel easier to work with and less brittle, its molecular structure can be changed with annealing, which is heating it at a steady and high temperature for a certain amount of time before cooling it right down again.
Hot or cold drawing: This process is used to make smaller or uniquely shaped tools with high tolerances. As these steels aren’t very ductile, several passes at temperatures of up to 1000°C are needed, but you’ll only be able to go over it once (and lightly) with cold drawing to prevent breakage.
Tool Steel Types
As promised in the intro, here’s a look at the different types of tool steel grades which, as you’ll see, differ in both composition and characteristics.
1. Water-hardening (W)
Common grades | Carbon % | Chromium % | Other elements | Working temp. | Melting temp. |
---|---|---|---|---|---|
Common grades W1, W2, W5 | Carbon % 0.6–1.4% | Chromium % Trace | Other elements Vanadium, molybdenum, silicone, manganese | Working temp. 400–500°F | Melting temp. 2500–2600°F |
Water-hardening (W)
This is a high-carbon tool steel that has lower hardenability than other types due to its low alloy content and needs water quenching. These steels harden well but could become brittle, and the quenching tends to make it prone to cracking or warping. It’s one of the more affordable options but hasn’t got the highest heat resistance. It’s mainly used for basic stuff like reamers and embossing and cutting tools.
2. Shock-resisting (S)
Common grades | Carbon % | Silicon % | Other elements | Working temp. | Melting temp. |
---|---|---|---|---|---|
Common grades S1, S2, S5, S7 | Carbon % 0.5–0.6% | Silicon % 1.5–2.5% | Other elements Molybdenum, tungsten, chromium | Working temp. 600–700°F | Melting temp. 2700°F |
Shock-resisting (S)
Common grades | Carbon % | Chromium % | Other elements | Working temp. | Melting temp. |
---|---|---|---|---|---|
Common grades P20, P21 | Carbon % 0.3–0.4% | Chromium % 1–2% | Other elements Molybdenum | Working temp. 700–800°F | Melting temp. 2500–2600°F |
Plastic mold (P)
This type has one main job, and that’s to make the molds that are used for manufacturing plastic products and parts.
4. Cold-work
This group has three main sub-types (covered below), each with average hardness, as well as high wear resistance and hardenability, used for making larger parts or ones that need to be hardened with minimal distortion.
Oil hardening (O)
Common grades | Carbon % | Manganese % | Other elements | Working temp. | Melting temp. |
---|---|---|---|---|---|
Common grades O1, O2 | Carbon % 0.9–1.1% | Manganese % 1–1.5% | Other elements Tungsten, vanadium | Working temp. 400–500°F | Melting temp. 2500°F |
Oil hardening (O)
Common grades | Carbon % | Chromium % | Other elements | Working temp. | Melting temp. |
---|---|---|---|---|---|
Common grades A2, A6 | Carbon % 0.95–1.1% | Chromium % 4–5% | Other elements Molybdenum 1%, manganese 1% | Working temp. 700–800°F | Melting temp. 2400–2500°F |
Air hardening (A)
Common grades | Carbon % | Chromium % | Other elements | Working temp. | Melting temp. |
---|---|---|---|---|---|
Common grades D2, D3, D6 | Carbon % 1.5–2% | Chromium % 11–12% | Other elements Vanadium, molybdenum | Working temp. 800–900°F | Melting temp. 2200–2400°F |
High carbon and chromium (D)
These are also air-hardening steels and are preferred for long production runs.
5. Hot-work (H)
Used to make lots of tools other than cutters, H-grade boasts the ability to work well in high heats for long stretches at a time. It’s low carbon with a good amount of alloying metals in it. There are three types in this category:
Molybdenum-based (H40-H59)
Common grades | Carbon % | Chromium % | Other elements | Working temp. | Melting temp. |
---|---|---|---|---|---|
Common grades H42, H43 | Carbon % 0.3–0.5% | Chromium % 2–3% | Other elements Molybdenum 8–10% | Working temp. 1100–1200°F | Melting temp. 2300–2400°F |
Molybdenum-based (H40-H59)
Common grades | Carbon % | Chromium % | Other elements | Working temp. | Melting temp. |
---|---|---|---|---|---|
Common grades H21, H26 | Carbon % 0.3–0.5% | Chromium % 2–3% | Other elements Tungsten 9–12% | Working temp. 1200–1300°F | Melting temp. 2400–2500°F |
Tungsten-based (H20-H39)
Common grades | Carbon % | Chromium % | Other elements | Working temp. | Melting temp. |
---|---|---|---|---|---|
Common grades H11, H13 | Carbon % 0.35–0.45% | Chromium % 5% | Other elements Molybdenum 1–2% | Working temp. 1000–1100°F | Melting temp. 2500–2600°F |
It’s often used for cold heading die casings and magnesium/aluminum hot extrusion processes.
6. High-speed (HSS)
HSS can hold their own in super high temperatures without losing any hardness and are named after their speedy cutting and feed rates. You’ll find many cutting tools, saw blades, and tool and drill bits made from HSS. They’re also abrasion-resistant, thanks to the included tungsten and vanadium.
Molybdenum-based (M)
Common grades | Carbon % | Molybdenum% | Other elements | Working temp. | Melting temp. |
---|---|---|---|---|---|
Common grades M2, M4 | Carbon % 0.7–0.85% | Molybdenum% 5–10% | Other elements Tungsten, vanadium | Working temp. 1100–1200°F | Melting temp. 2200–2400°F |
Molybdenum-based (M)
Common grades | Carbon % | Tungsten % | Other elements | Working temp. | Melting temp. |
---|---|---|---|---|---|
Common grades T1, T15 | Carbon % 0.7–0.85% | Tungsten % 12–18% | Other elements Chromium, vanadium | Working temp. 1100–1300°F | Melting temp. 2400–2600°F |
Tungsten-based (T)
This keeps its hardness in high temperatures for the precise machining of even the hardest materials.
7. Special purpose
As the celebrity of the bunch, you wouldn’t want to use these costly steels if, for instance, a W-type would do the trick. Manufacturers tend to reserve these for applications that other steels can’t handle. They don’t have a lot of alloying metals (they like to work alone) and don’t need much treatment. There are two groups of special-purpose tool steels, described below.
Carbon-and tungsten-based (F)
Common grades | Carbon % | Tungsten % | Other elements | Working temp. | Melting temp. |
---|---|---|---|---|---|
Common grades F1, F2 | Carbon % 0.9–1.25% | Tungsten % 4–6% | Other elements None | Working temp. 900–1000°F | Melting temp. 2500–2600°F |
Carbon-and tungsten-based (F)
Common grades | Carbon % | Chromium % | Other elements | Working temp. | Melting temp. |
---|---|---|---|---|---|
Common grades L6, L7 | Carbon % 0.7–0.9% | Chromium % Low | Other elements Nickel, molybdenum | Working temp. 700–800°F | Melting temp. 2500°F |
Low alloy (L)
As another tough one, this type is used for bearings, clutch plates, rollers, wrenches, cams, and collets.
How Can Xometry Help
Xometry provides a wide range of manufacturing capabilities including CNC machining, 3D printing, injection molding, laser cutting, and sheet metal fabrication. Get your instant quote today.
Disclaimer
The content appearing on this webpage is for informational purposes only. Xometry makes no representation or warranty of any kind, be it expressed or implied, as to the accuracy, completeness, or validity of the information. Any performance parameters, geometric tolerances, specific design features, quality and types of materials, or processes should not be inferred to represent what will be delivered by third-party suppliers or manufacturers through Xometry’s network. Buyers seeking quotes for parts are responsible for defining the specific requirements for those parts. Please refer to our terms and conditions for more information.
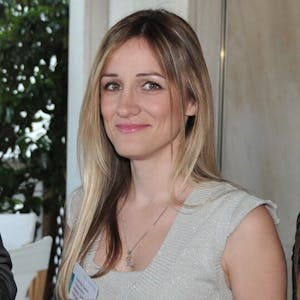