When you’re manufacturing with plastics, thermoplastics, rubbers, and elastomers, rarely will you ever have the problem of not having enough choice. The issue tends to be choosing which material of the thousands out there has all the properties you need—especially when some are so similar. That’s often the case when you’re weighing up thermoplastic elastomers (TPEs) and silicone, so let’s get into what makes each different and the applications where they’ll really shine.
What is Thermoplastic Elastomer?
Manufacturers tend to opt for TPEs when they’re after a material with a blend of plastic and rubber properties. This synthetic rubber has excellent elasticity and a high melting point. It can be heated up, stretched, and returned back to its original shape before going through the whole process again.
It’s these properties that have given TPE a name in manufacturing, and why it’s often compared to silicone, as they share a few properties—but equally have quite a few differences. When you’re choosing a TPE to work with, you’ll find it’ll be based on how you’re processing or manufacturing it. For instance, there are TPEs for blow molding, extrusion, and injection molding.
What is Silicone?
Silicone may look and act a bit like rubber, but it’s much more complex. This synthetic material is made up of a bunch of oxygen-silicon molecules (called siloxanes) and it’s a popular pick that manufacturers still like using today. Like TPE, it has elastomeric properties, too.
There are a few cases where silicone falters—it’s not particularly well suited when up against steam, hydrocarbon fuel, or specific types of hydrocarbons, like those that are alkali, acidic, or aromatic. Still, those reasons shouldn’t be enough to put you off, as it’s a very common material used across plenty of sectors.
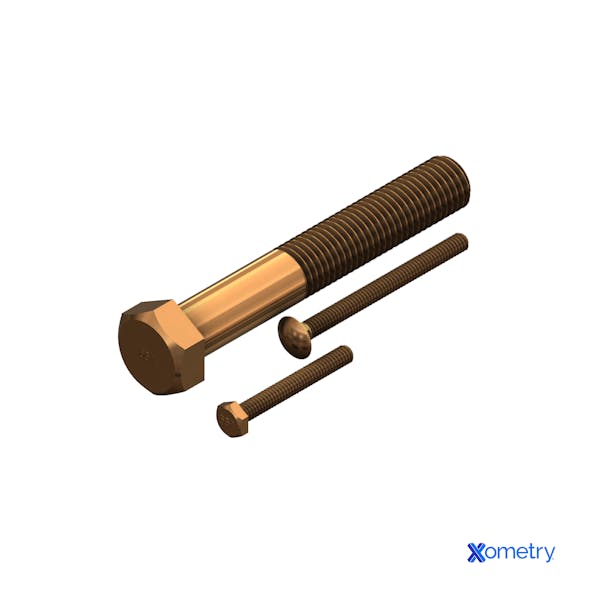
How Their Injection Molding Processes Vary
Both of these rubber-like materials are great when it comes to injection molding processes. For silicone injection molding, you’ll need a molding tool made with CNC machining that has an excellent heat-resistant finish in order to mold silicone—especially with its wild ability to handle high temperatures without degrading or melting. Once you have this tool made, it’ll be added to a press that can create precise shots of material. From there, tons of different items can be made with silicone injection molding, including cooking utensils, gaskets, and prosthetics.
TPE is a little less complex as it has a melting point so tools don’t have to be as specialized. It comes in the form of pellets, which will be fed into a hopper and then melted down into a hot resin. This will be shot into a closed mold under high pressure and then it’ll cool down and harden into the shape you need. It’s a pretty advanced material, so manufacturing with it can be pretty fast and result in quicker lead times.
Comparing These Materials
When you’re thinking of using either TPE or silicone, you’ll want to take stock of each of their characteristics and what they both excel at (and aren’t so great at). Silicone is great if you need products that will have good thermal conductivity and have good resistance to fire, heat, and cold. It also has a remarkable quality that’s hard to find in any other plastic or rubber—it doesn’t have a melting point. It’ll either combust or turn brittle after 450 ℃.
In this instance, thermoplastic elastomers are a good alternative as items made of this material are affordable but still have good chemical resistance, stability, and heat resistance. TPEs, of course, have a melting point, too, but a pretty high one. The biggest deciding factor in many scenarios is twofold. If you need a product that can be heated and reprocessed, you’ll want to go with TPE (silicone can’t do this), but if extreme heat resistance is the biggest priority, silicone is the winning material.
How Xometry Can Help
You might be working with silicone, TPEs, or a completely different set of plastics, but we have plenty of services that cater to all of these needs. You’ll find urethane and silicone casting, plastic extrusion, and insert molding on our site, all of which you can get free quotes for.
Disclaimer
The content appearing on this webpage is for informational purposes only. Xometry makes no representation or warranty of any kind, be it expressed or implied, as to the accuracy, completeness, or validity of the information. Any performance parameters, geometric tolerances, specific design features, quality and types of materials, or processes should not be inferred to represent what will be delivered by third-party suppliers or manufacturers through Xometry’s network. Buyers seeking quotes for parts are responsible for defining the specific requirements for those parts. Please refer to our terms and conditions for more information.
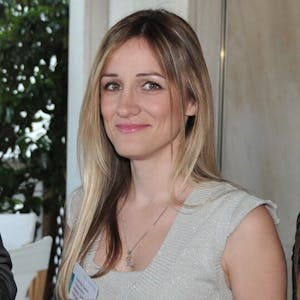