Thermoplastics melt and become liquid when heated, and then solidify once cooled. Thermoplastic elastomers (TPE) and thermoplastic rubbers (TPR) are materials that behave as thermoplastics while also having excellent flexibility. These elastomers typically have hardnesses in the range measured by the Shore A scale. TPEs are used for many applications, from oxygen masks to seals. TPRs, on the other hand, are most commonly used for shoe soles because they provide excellent grip. Thermoplastic elastomers are actually a group of materials with very different chemical makeups and properties. However, they all share the ability to be melted for processing, and they all have elastomeric behavior.
"TPR" does not refer to a group of materials, but rather to a specific one with a specific chemical makeup. Both TPR and TPE can be processed using injection molding, blow molding, compression molding, and 3D printing. Each of these thermoplastics is available in various formulations and brands that ultimately result in a significant range of properties. This article will describe the properties and applications of TPR vs TPE in more detail, as well as the differences between them.
What is TPR?
TPR stands for ”thermoplastic rubber.” The term refers to a broad range of synthetic rubbers that can be processed as thermoplastics. Natural rubber does not melt and will break down chemically and become useless if heated too much. Thermoplastic rubber is used in applications where a flexible and durable material is required, but where the part being fabricated has a sufficiently complex geometry to necessitate the use of thermoplastic processing equipment like injection molding. TPR is tough, has good chemical resistance, and also has good fatigue resistance.
TPR consists of SBS (styrene-butadiene-styrene), which is a type of block copolymer. TPR is synthesized using a process called “living anionic polymerization.” This is a chain polymerization process that joins two monomers, namely butadiene, and styrene, into SBS. This process creates a polymer structure with both hard crystalline regions and soft amorphous regions. The hard regions contain styrene and the soft regions contain butadiene. The hard regions provide the thermoplastic properties, whereas the amorphous regions supply the elastomeric properties.
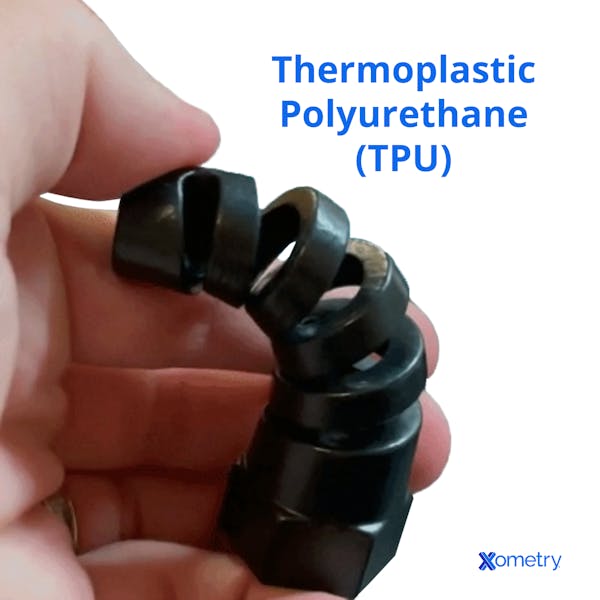
What Is TPE?
TPE (thermoplastic elastomer) refers to thermoplastics that exhibit elastomeric behavior, i.e., they can deform and then return to their original shape. However, it must be noted that while the phrase elastomer tends to cover rubbers as well, thermoplastic elastomer, in this case, can refer to a number of different materials with TPE-S being the most commonly used. TPE is durable and can be melt-processed using injection molding, blow molding, compression molding, and 3D printing. The different types of TPEs are listed below:
- TPE-S (Styrenic block copolymers): TPES is one of the most widely used TPEs.
- TPO (Thermoplastic polyolefins): Typically used as a polypropylene replacement with higher toughness.
- TPV (Thermoplastic vulcanisates): TPV is a specially prepared mixture of EPDM (ethylene propylene diene monomer) and PP (polypropylene) with a maximum operating temperature of 120C.
- TPU (Thermoplastic polyurethanes): TPU has excellent abrasion and tear resistance and good rebound resilience.
- TPE-E (Thermoplastic copolyesters): TPE-E has excellent temperature and chemical resistance. It has a maximum operating temperature of 140C.
- TPE-A (Thermoplastic polyether block amides): TPEAs have good high-temperature resistance and can be bonded to Nylon.
TPE is typically synthesized using graft polymerization which refers to the process of grafting polymer chains as branches to a polymer backbone.
TPR vs. TPE: Applications and Uses
TPR and TPE are both used for applications that require flexibility and toughness, and their applications often overlap. TPR has been widely used for shoe soles due to its slip resistance, low cost, and flexibility. Some typical TPR applications are listed below:
- Shoe soles
- Dog toys
- Tire treads
- Gaskets
TPE covers a wide range of materials and for that reason, it can be used for a large number of potential applications, some of which are listed below:
- O-rings, seals, bushings, vibration isolation mounts, soft tool grips
- Interior panels, car mats, vehicle suspension shock dust cover
- Oxygen masks, flexible tubing for medical applications
- Diving equipment like fins and snorkels
TPR vs. TPE: Physical Properties
Table 1 below lists some physical properties of TPR and TPE:
Physical Properties | Thermoplastic Rubber (TPR) | Thermoplastic Elastomer (TPE-S) |
---|---|---|
Physical Properties Brand | Thermoplastic Rubber (TPR) Elastron D100.A40.N | Thermoplastic Elastomer (TPE-S) Elastron G100.A30.N |
Physical Properties Tensile Strength (MPa) | Thermoplastic Rubber (TPR) 2.5 | Thermoplastic Elastomer (TPE-S) 2.5 |
Physical Properties Melting Temperature Range (°C) | Thermoplastic Rubber (TPR) 140-185 | Thermoplastic Elastomer (TPE-S) 100 |
Physical Properties Compression Set (%) (@23 °C 22 h) | Thermoplastic Rubber (TPR) 16 | Thermoplastic Elastomer (TPE-S) 10 |
Physical Properties Hardness (Shore A) | Thermoplastic Rubber (TPR) 40 | Thermoplastic Elastomer (TPE-S) 30 |
Physical Properties Tensile Modulus @ 300 % Elongation (MPa) | Thermoplastic Rubber (TPR) 1.5 | Thermoplastic Elastomer (TPE-S) 1.1 |
Physical Properties Elongation @ Break (%) | Thermoplastic Rubber (TPR) 550 | Thermoplastic Elastomer (TPE-S) 800 |
Physical Properties Tear Resistance (N/mm) | Thermoplastic Rubber (TPR) 15 | Thermoplastic Elastomer (TPE-S) 17 |
Physical Properties Electrical Insulation | Thermoplastic Rubber (TPR) — | Thermoplastic Elastomer (TPE-S) — |
Because there are so many variations on both TPE and TPR, the data in Table 1 above shows the properties for just one representative material in each category. Always consult a raw material supplier for more applicable datasheets.
TPR vs. TPE: Recyclability and Sustainability
Both TPR and TPE are thermoplastics. As such, they can theoretically be recycled. However, plastic recycling is already quite rare with far more popular commodity plastics like polypropylene and polyethylene. In light of this, recycling lower-volume materials like TPR and TPE is not typically economical or common practice. If recyclability is a requirement for a given application, TPR is a good potential replacement for natural rubber, which cannot be recycled at all.
In terms of sustainability, both TPR and TPE are made from crude oil products. Therefore, both are not environmentally sustainable in the sense that they are not often recycled and are produced from non-renewable resources.
TPR vs. TPE: Cost
Thermoplastic elastomers are, in general, significantly more expensive than standard commodity thermoplastics. For that reason, their use must be carefully considered in light of potentially cheaper alternatives like natural rubber, cast polyurethane, and normal rigid thermoplastics. TPEs can cost starting from $2.50 per kilogram, and TPRs cost starting from $2.79 per kilogram.
Alternative Materials to TPR and TPE
TPR and TPE are elastomers. As such, they can only be replaced by materials that are also elastomers with suitable properties. Thermosetting elastomers like polyurethane offer some of the same characteristics as TPR and TPE, such as flexibility, toughness, and abrasion resistance, TPU has similar properties to thermosetting polyurethane but can be melt-processed.
Summary
This article presented the TPR and TPE, explained what they are, and discussed when to use each material. To learn more about TPR and TPE, contact a Xometry representative.
Xometry provides a wide range of manufacturing capabilities and other value-added services for all of your prototyping and production needs. Visit our website to learn more or to request a free, no-obligation quote.
Disclaimer
The content appearing on this webpage is for informational purposes only. Xometry makes no representation or warranty of any kind, be it expressed or implied, as to the accuracy, completeness, or validity of the information. Any performance parameters, geometric tolerances, specific design features, quality and types of materials, or processes should not be inferred to represent what will be delivered by third-party suppliers or manufacturers through Xometry’s network. Buyers seeking quotes for parts are responsible for defining the specific requirements for those parts. Please refer to our terms and conditions for more information.
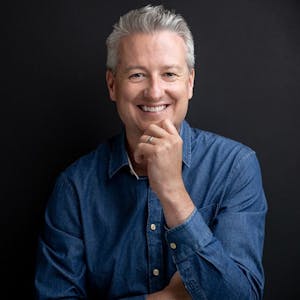