What is TPR?
TPR or thermoplastic rubber is typically a copolymer that merges the properties of polystyrene (PS) and butadiene (synthetic) rubber (23% and 77%, respectively). This material was developed to provide much of the property benefit of synthetic rubber while allowing processing (and reprocessing) in the more precise and controllable injection molding process. TPR delivers outstanding fatigue resilience, chemical stability, impact strength, and moderate recyclability.
TPR does not match the performance of vulcanized rubbers, so it is not suitable for tire manufacture, having too low a tear modulus. However, the significantly better ozone-, weathering-, and UV-resistant properties of TPR mean that it finds wide application across many product sectors.
What is TPU?
TPU, or thermoplastic polyurethane, is a broad classification of polyurethane polymers that share properties such as elasticity, wear resistance, and very high chemical compatibility with oils. The materials are thermoplastic, making them suitable for injection molding. TPU can be sourced in a variety of shore values, from rubbery to rigid. Their high strength and resilience are derived from a polymer chain structure consisting of alternating hard and soft segments. TPUs can be recycled by melting and reforming, although the degradation in chain length/integrity is significant on remelting.
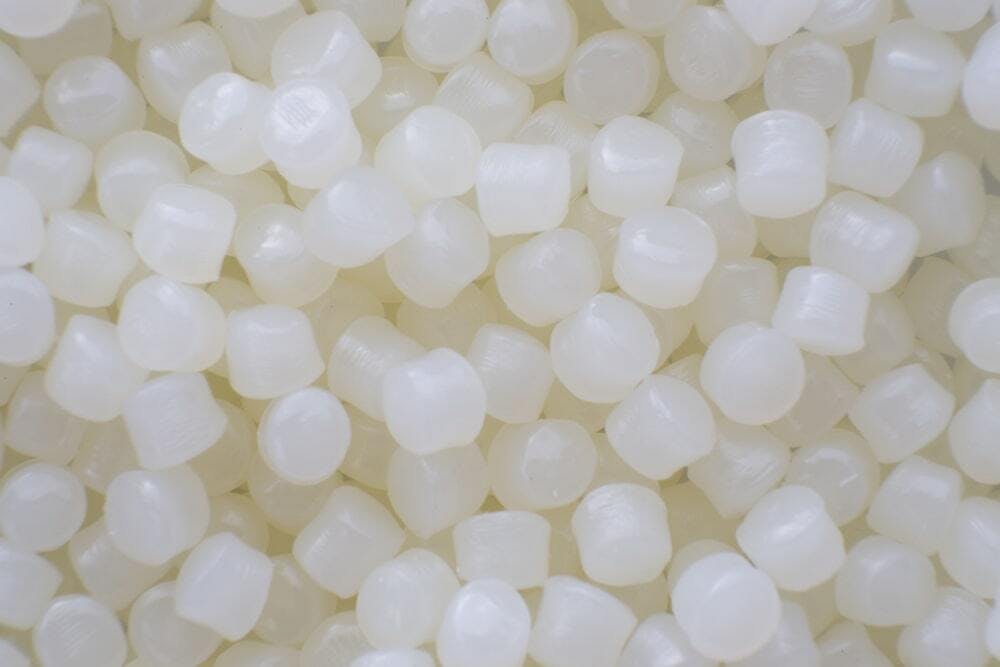
Close up of white TPR.
Image Credit: Shutterstock.com/Meaw_stocker
Applications and Uses
TPR Applications
- Auto Manufacture: Door and window seals, transmission/suspension parts, fender inserts, exterior and interior trim, instrument panels, AC and engine air ducts, grommets, drive belts, fluid pipes, floor mats, O-rings.
- Construction: Door and window seals, hydraulic seals, plumbing seals.
- Industrial: Vibration dampers, pipes, manifolds, seals, suspension bushes, shock absorbers, roof membranes.
- Consumer: Refrigerator seals, handgrip overmolds, mobile phone covers, switch panels, vibration dampers.
- Medical: Air tubes, syringe seals, breathing masks and plenums, seals, valves, and catheters.
- Electronics: Encapsulation, power leads, high-quality cables, mobile phone shock protection, and seals.
- Footwear & Sports Equipment: Diving flippers, snorkels, masks, ski-pole grips, ski-boot components, and shoe soles.
TPU Applications
- Automotive: Automotive interior parts (good surface finish, durability, wear resistance; and low cost).
- Agriculture: ID tags for animals (great flexibility, tear and weather resistance, and temperature tolerance. Great for encapsulating RFID).
- Piping and Plumbing: Seal profiles and O-rings, tubes, belts, and hoses. Specialist polymers with optimal melt-flow properties, extrusion-adapted high resistance to hydrolysis by hydraulic and other oils and organics, resistance to compression at high temperatures, high toughness, flexibility, and resistance to tearing.
- Textile: Used for conveyor belts, inflatables, and military equipment. Wide range of processing options, and good mechanical, chemical, and thermal properties.
- Sports Equipment: Extreme flexibility, high-impact and temperature resistance, transparency, and environmental tolerance.
There are common market sectors and ostensibly common product areas that can use either TPR or TPU materials. In general, the commonalities do not imply interchangeability, as each application tends to exploit a narrow property of one or another material. For example, the automotive sector uses TPRs for extreme flexibility and weathering properties and TPUs for resilience, wear resistance, and ergonomic applications.
Physical Properties
Property | TPR value (metric) | TPU value (metric) |
---|---|---|
Property Hardness, Shore D | TPR value (metric) 10–69 | TPU value (metric) 59–83 |
Property Tensile Strength, Ultimate | TPR value (metric) 0.345–80.0 MPa | TPU value (metric) 28.0–96.0 MPa |
Property Tensile Strength, Yield | TPR value (metric) 0.586–4.83 MPa | TPU value (metric) 52.4–79.3 MPa |
Property Modulus of Elasticity | TPR value (metric) 0.0180–0.683 GPa | TPU value (metric) 0.621–5.50 GPa |
Property Flexural Yield Strength | TPR value (metric) 2.66–24.1 MPa | TPU value (metric) 19.0–95.1 MPa |
Property Flexural Modulus | TPR value (metric) 0.0917–0.814 GPa | TPU value (metric) 0.520–4.50 GPa |
Property Taber Abrasion, mg/1000 Cycles | TPR value (metric) 30–800 | TPU value (metric) 5–25 |
Property Melting point | TPR value (metric) 104–191°C | TPU value (metric) 185–243°C |
Property Coefficient of Thermal Expansion, linear | TPR value (metric) 110–170 µm/m°C | TPU value (metric) 13.5–55.8 µm/m°C |
Table Credit: https://matweb.com/
Recyclability and Sustainability
TPU is recyclable; its waste can be processed back into high-quality raw material. Although it tends to be second-grade due to thermal decomposition. Bio-sourced TPUs are also slowly becoming available.
TPR is highly recyclable, but the recycled material is second-grade. They are stable materials that degrade extremely slowly in the natural environment. Algal-derived monomer source materials for TPRs are also becoming available.
Cost
TPRs are generally very low-cost materials, ranging from $1.60 to $2.00 per kg. TPUs are a little more expensive, at $2.00 to $4.00 per kg.
Alternative Materials
For injection molding use, a wide variety of thermoplastic elastomeric materials are available, with an equally wide spectrum of properties and costs. While these are not interchangeable across the whole range, there are many commonalities of properties that result in options at the specification stage. Listed below are some alternative materials:
- Thermoplastic Vulcanisates (TPE-V or TPV).
- Thermoplastic Polyolefins (TPE-O or TPO).
- Thermoplastic Copolyesters (TPE-E, COPE, or TEEE).
- Thermoplastic Polyether Block Amides (TPE-A).
- Styrenic Block Copolymers (TPE-S).
- Melt-Processable Rubber (MPR).
- Fluoropolymer Elastomers (FPE).
When a switch to thermosetting polymers is an option, there are more material choices, as listed below:
- Vulcanized natural rubber (NR) (latex, vulcanized to form Buna rubber).
- Polyisoprene (IR).
- Polychloroprene (CR).
- Butadiene rubber (BR).
- Nitrile (butadiene) rubber (NBR).
Thermoset rubbers bring new properties and new restrictions to the options list. They can, however, achieve remarkable results whenever specific properties are sought and the processing issues do not prevent use.
TPR and TPU Parts Through Xometry
Xometry's plastic injection molding service provides a comprehensive offering of TPR and TPU materials available on-demand for custom parts. Uploading your 3D CAD file to the Xometry Instant Quoting Engine® is the best way to get started.
Disclaimer
The content appearing on this webpage is for informational purposes only. Xometry makes no representation or warranty of any kind, be it expressed or implied, as to the accuracy, completeness, or validity of the information. Any performance parameters, geometric tolerances, specific design features, quality and types of materials, or processes should not be inferred to represent what will be delivered by third-party suppliers or manufacturers through Xometry’s network. Buyers seeking quotes for parts are responsible for defining the specific requirements for those parts. Please refer to our terms and conditions for more information.
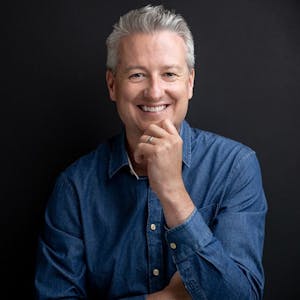