Types of Bronze Alloys
Bronze alloys come in a variety of compositions, each designed for a particular use. With its great mechanical prowess and 9–14% aluminum enrichment, aluminum bronze is a reliable option for naval equipment such as propellers and valves.
Silicon bronze, which is composed of around 0.13% iron and 6% silicon, is mostly used for coating red brass and bronze, which are recognized for their durability and resistance to corrosion. Copper, tin, and phosphorus combined create phosphor bronze which exhibits exceptional spring properties and great fatigue resistance, making it a valuable material for electrical applications. As we delve deeper into the realm of adaptable alloys, this examination of various bronze kinds reveals their distinctive qualities.
Listed below are 9 different types of bronze:
1. Aluminum Bronze
With aluminum serving as the main alloying ingredient, aluminum bronze is a copper-based alloy family that offers superior corrosion resistance and strength comparable to medium-carbon steel. Its varied qualities find uses in a variety of industries. Its composition is around 9–14% aluminum, 4% iron, and about 82.7% copper. Some notable alloys include: C95200 for bushings and gears, C95400 for chemical and marine applications, C95500 with increased strength, C95800 for marine applications, and C95900 for wear plates.
2. Phosphor Bronze
Phosphor bronze is a copper alloy containing around 95% copper, 0.5–11% tin, and 0.01–0.35% phosphorus, often with additional elements like lead for specific properties. Tin enhances corrosion resistance, while phosphorus boosts wear resistance and stiffness. Recognized for toughness, strength, and low friction, phosphor bronze’s fluidity in the molten state aids casting. It is widely used for: springs, bolts, bushings, electrical switches, dental bridges, and marine applications like ship propellers. Standard alloys cater to various industrial needs, making phosphor bronze a cost-effective choice for springs, electrical contacts, and cryogenic applications.
3. Silicon Bronze
Silicon bronze is a low-lead brass alloy having trace amounts of manganese, aluminum, and zinc mixed in with 94–96% copper, 2.5–6% silicon, and 0.3–1.4% iron. Its corrosion resistance and smooth finish are well-known attributes. Its density of 8.53 g/cm³ makes it appropriate for casting and welding. Two noteworthy mechanical properties of this alloy are its tensile yield strength which ranges from 105 to 415 MPa and its hardness rating which indicates strength greater than copper. Silicon bronze is commonly used in marine hardware, U-bolts, architectural embellishments, hydraulic applications, tubing, and welding rods.
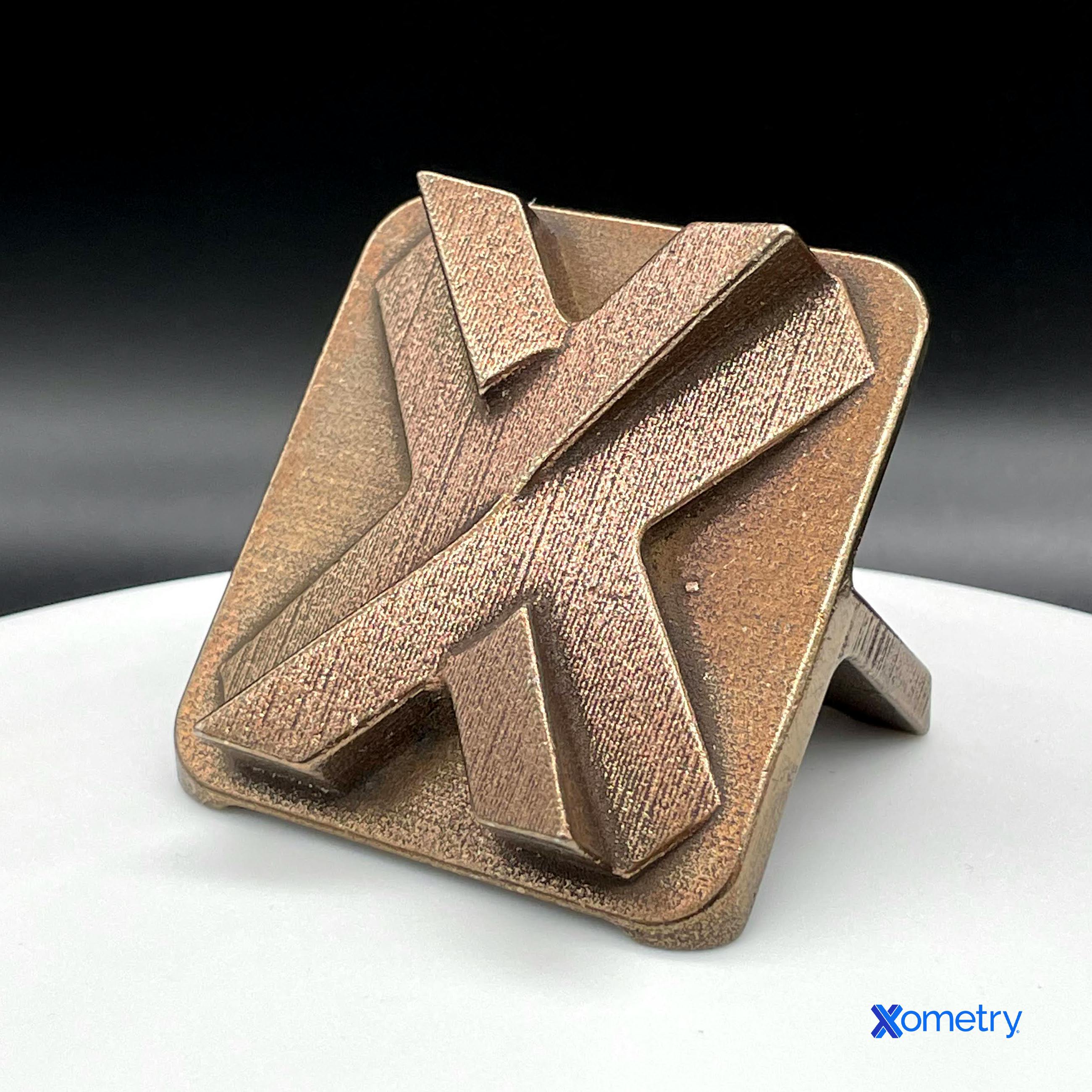
4. Nickel Aluminum Bronze
Nickel aluminum bronze alloys, comprising aluminum, exhibit increased strength through added iron and nickel. The composition, including 79% copper, 8.50–9.50% aluminum, 3.50–4.50% nickel, and other elements, enhances strength without compromising ductility. Widely employed in marine applications like ship valves and propellers, these alloys serve roles in bushings, bearings, wear plates, and hydraulic valve components. The corrosion resistance and versatile properties make nickel aluminum bronze a valuable choice in diverse industries, from aerospace for landing gear to oil & gas for seawater lift pumps.
5. Bismuth Bronze
Bismuth bronze, sometimes referred to as lead-free bronze or lead-free brass, addresses issues with recycling and the harm that comes with lead-based bronzes. It usually contains 87–91% copper, 1–6% bismuth, 1% nickel, 2–4% tin, and zinc. It is still as machinable and workable as leaded bronze. This high-temperature, corrosion-resistant material is used in plumbing, fasteners, bearings, and other applications in which safety for drinking water is required. For ecologically concerned applications, its non-toxic nature makes it a useful replacement for traditional leaded alloys, although it is more expensive and more difficult to recycle.
6. Bearing Bronze
Bearing bronze is a versatile copper alloy, typically composed of 81–85% copper, 6–8% lead, 6.3–7.5% tin, and 2–4% zinc, among other elements. With a consistent density of 8.93 g/cm³ and a copper-gold color, it is often used for light-duty applications due to its ease of shaping. Resistant to seawater corrosion, it self-lubricates, making it suitable for marine applications. Its mechanical properties, including low tensile yield strength and moderate machinability, contribute to its common use in bearings, bushings, impellers, plates, washers, and machine-tool bearings.
7. Tin Bronze
Tin bronze alloys, in which tin is the primary alloying element, have good mechanical qualities that make them appropriate for some uses even though the cost of the metal is higher. C90700 is among the high-tin bronzes utilized in: pump bodies, gears, bearings, bushings, and structural elements. It has an 89% copper and 11% tin composition. Additional variants – with C90500, C92300, C92501, and C92700 serving comparable applications in low-speed, heavy-load service scenarios – include valve guides, piston pins, and different types of bearings. Resistant to corrosion, they operate as bearings at temperatures up to 500 °F and loads of 4,000 lbs per square inch, demanding precise alignment and lubrication.
8. Manganese Bronze
Manganese bronze alloys, composed of 60–68% copper, 25% zinc, 3.0–7.5% aluminum, 2.5–5.0% manganese, and 2.0–4.0% iron, exhibit exceptional strength and wear resistance. Though challenging to machine, its impressive tensile yield strength of 460 MPa and fatigue strength of 170 MPa make it a preferred choice in aerospace, marine, and oil & gas industries. It is used for applications like welding rods, fasteners, gears, slow-speed heavy-load bearings, cams, and landing-gear parts. Despite its cost and difficulty in fabrication, manganese bronze's longevity and durability make it indispensable in critical applications.
9. Copper-Nickel Bronze
Copper-nickel bronze is a popular alloy for its longevity, corrosion resistance (particularly in saltwater), and excellent thermal stability. It contains 90% copper and 2–30% nickel. Notably, ship hulls, electrical components, pumps, valves, and marine equipment all commonly make use of the 90% copper and 10% nickel alloy (C70600, CW352H). Nickel improves strength and resistance to corrosion, making it more ductile. Alloys with 30% nickel content, such as C71500 and C71640, provide better resistance against wear, galling, sand abrasion, and seawater flow. When more mechanical qualities are required, those that are more heavily alloyed with aluminum, chromium, or tin perform well.
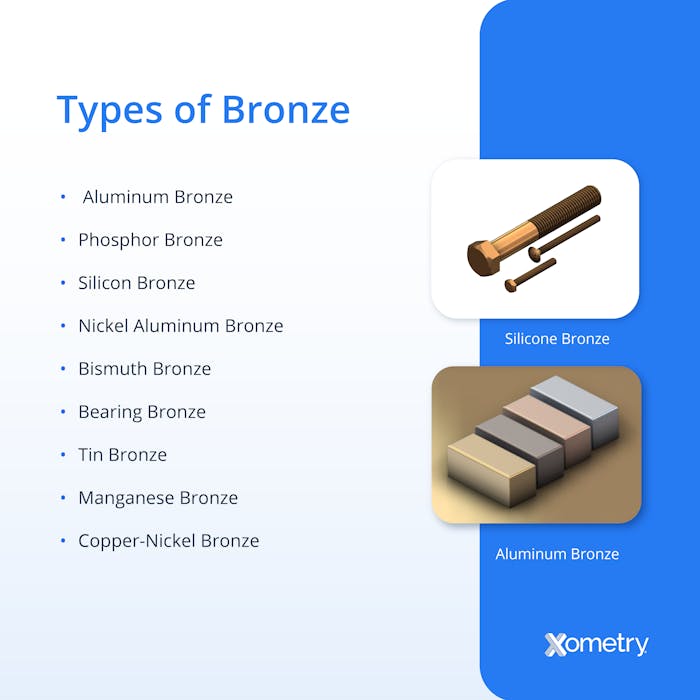
Types of Bronze Infographic
Xometry provides a wide range of manufacturing capabilities including CNC machining, 3D printing, injection molding, laser cutting, and sheet metal fabrication. Bronze is one of the dozens of materials we work with every day. Get your instant quote today to get your project started.
Disclaimer
The content appearing on this webpage is for informational purposes only. Xometry makes no representation or warranty of any kind, be it expressed or implied, as to the accuracy, completeness, or validity of the information. Any performance parameters, geometric tolerances, specific design features, quality and types of materials, or processes should not be inferred to represent what will be delivered by third-party suppliers or manufacturers through Xometry’s network. Buyers seeking quotes for parts are responsible for defining the specific requirements for those parts. Please refer to our terms and conditions for more information.
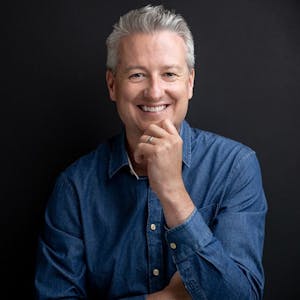