Polybutylene terephthalate (PBT) is an engineering thermoplastic material exhibiting excellent mechanical and electrical properties. It's made by combined three materials and allowing them to polymerize. PBT is used in various industries such as the electronics, general industry, and consumer goods sectors for material like strips, gears, and covers. This material is heat resistant and tough, though it is weak in extreme environments. It will only affect humans if swallowed or heated to extreme temperatures. Compared to polypropylene, PBT is heavier and less soft.
What is Polybutylene Terephthalate?
Polybutylene Terephthalate (PBT) is an engineering-grade synthetic thermoplastic belonging to the polyester family of polymers. It is a high-performance material known for its balanced properties: high strength, stiffness, excellent stain resistance, good creep resistance, and low moisture absorption characteristics.
How is Polybutylene Terephthalate Made?
Polybutylene Terephthalate is made by combining three materials through esterification, lowering temperatures, and then letting the material polymerize. Manufacturing PBT requires three raw materials: butanediol (BDO), dimethyl terephthalate (DMT), and purified terephthalic acid (PTA), paired together with various catalysts. The general manufacturing process can be summed up in the following steps:
- Mixing of the raw materials
- Esterification – which is the process of combining an acid (i.e. dicarboxylic acid, terephthalic acid) with alcohols (ethylene for example) to produce esters, with water as a byproduct
- Pre-polymerization – or the separation of the catalyst activation stage from the polymerization stage. This process is characterized by lower temperatures and is used to reduce the polymerization rates later on in the manufacturing stages, as well as to reduce toxicity (including the total exhaust and toxic gases released during manufacturing). It also improves handling properties (such as molecular rates and NCO content – nitrogen, carbon, and oxygen).
- Polymerization – the stage where molecules combine to produce chain-like structures called polymers. The specifics of how those structures are made (what type of bonds, chain structures, etc.) affect the end material's primary properties.
What are the Characteristics of Polybutylene Terephthalate?
Polybutylene terephthalate's characteristics are good mechanical and electrical properties. This material crystallizes quickly, which translates to shorter mold cycles compared to other plastics, as well as lower molding temperatures. These characteristics make PBT a good choice for high-volume orders of parts that require good mechanical and electrical properties.
Generally, PBT exhibit a higher tensile and dielectric strength than many plastics. This improved performance means that PBT can replace popular choices like polypropylene and nylon in some scenarios while competing with materials like polycarbonate for more demanding applications.
In addition to this, the tensile and compressive strengths of PBT can be increased up to threefold through glass-reinforcing. This also confers more resistance to oxidation in hot air, on par with nylon 6. While PBT is attacked by strong bases, it can resist a broad range of chemicals at room temperatures, such as gasoline, oils, alcohols, esters, ethers, diluted acids, fats, and more.
What are the Uses of Polybutylene Terephthalate?
Polybutylene terephthalate is used for strips, gears, covers, and other components. PBT can be used in electronics, aviation, automotive, medical, and consumer goods, as well as in general industrial applications. Some of them are:
- Connector strips
- Insulating electrical components
- Valve parts
- Pump housing
- Bearings
- Wear strips
- Scraper blades
- Conveyor components
- Gears
- Bumpers
- Irrigation equipment
- Motor covers
- TV accessories
- Tractor hoods
- Tailgate outer panels
What are the Advantages of Polybutylene Terephthalate in the Plastic Injection Molding Process?
The advantages of polybutylene terephthalate lie in the excellent properties of the material. Thus, the main benefits of using PBT in your injection molding applications are:
- Excellent heat resistance (up to 150 degrees C or 284 degrees F)
- Very tough, including at lower temperatures of down to -40°C (-40 degrees F)
- Retains its color very well
- Good resistance to cracking
- Good insulating capabilities
- Excellent weatherability
- High impact strength (especially if reinforced)
What are the Disadvantages of the Polybutylene Terephthalate Plastic Injection Molding Process?
The disadvantages of polybutylene terephthalate plastic injection molding include weakness in extreme environments and against stronger acids and bases. Even though PBT is a high-grade engineering plastic, it is not suitable for more extreme environments. It is also surpassed in some areas by other engineering-grade materials, such as PET and nylon. Some of the disadvantages of PBT are:
- Tendency to warp when reinforced with glass
- Not resistant to stronger acids and bases
- Lower glass transition temperature compared to other high-grade plastics
- Poor resistance to hydrolysis
How does Polybutylene Terephthalate Affect Human Health?
Polybutylene terephthalate affects human health if swallowed or heated to extreme temperatures. PBT is known to exhibit an operating temperature of over 110 degrees C (230 degrees F), meaning that unless it is subjected to harsh environments, toxic vapor should not be a concern.
However, even though PBT itself is not harmful at average operating temperatures, the additives used in the manufacturing process (like bromine), can be harmful if they get inside the body. Those effects include different types of cancer, apoptosis, and genotoxicity (mutations in the cells that could lead to cancer).
Is Polybutylene Terephthalate Toxic?
Polybutylene terephthalate is toxic if inhaled, absorbed through the skin, dropped on the eyes, or swallowed. It can cause irritations if it interacts with the human body in any way mentioned above. Otherwise, PBT is FDA-approved to be used in contact with food (in the form of containers). This plastic is also very resistant to wear and moisture.
Property | PP | PBT |
---|---|---|
Property Density | PP 0.89-0.91 g/cm3 | PBT 1.3-1.4 g/ cm3 |
Property Excellent mechanical properties | PP x | PBT x |
Property High heat resistance | PP Up to 120 degrees C (248 degrees F) | PBT Up to 150 degrees C (302 degrees F) |
Property Water-resistant | PP x | PBT x |
Property Usually not toxic | PP x | PBT x |
Property Good electric insulation | PP x | PBT x |
Property Susceptible to aging due to heat, UV, and oxygen | PP Yes | PBT Less so |
Property Very tough | PP | PBT x |
Property Highly rigid | PP Less so | PBT x |
PP is softer and lighter than PBT. PP is also very resistant to adhesives, so glue and paint will have a hard time sticking to its surface. Some typical applications where PP has seen use are laboratory equipment, pipes, pallets, and hinges. Due to the higher impact strength, PBT is suitable for more demanding environments.
Polypropylene is in the top three most-produced commodities plastics, due to its good mechanical properties and chemical resistance, making it suitable for applications in the consumer goods industry (labeling and packaging).
With the help of glass-fiber reinforcements, PBT can withstand even higher temperatures than the one mentioned above, close to 200 degrees C (392 degrees F). Additionally, it can be treated with flame retardant additives, making it non-combustible.
It is also good to know that in terms of classification, while PBT is considered engineering-grade, PP is categorized as a commodity-grade plastic, which means that the latter is usually cheaper.
Conclusion
PBT is an engineering-grade plastic with excellent mechanical, chemical, and electrical properties, making it suitable for the most demanding of environments and operating conditions. Its toughness, high strength, and high operating temperatures make PBT a good candidate for applications in the aerospace, automotive, and general industries.
While generally being non-toxic, special care must be taken in cases where additives are used (especially the ones that confer flame retardancy properties). Even though PBT is resistant to many chemicals, it can still be damaged by the stronger acids and bases, which means it is not fit for applications such as laboratory containers.
PBT is one of the most versatile options when choosing the right plastic for your injection molding applications. Xometry's instant quoting engine can give you an initial estimate of the budget and lead time for your PBT project. We support the most popular 3D CAD files include .step, .stp, .stl, .3dxml and .ipt formats.
Disclaimer
The content appearing on this webpage is for informational purposes only. Xometry makes no representation or warranty of any kind, be it expressed or implied, as to the accuracy, completeness, or validity of the information. Any performance parameters, geometric tolerances, specific design features, quality and types of materials, or processes should not be inferred to represent what will be delivered by third-party suppliers or manufacturers through Xometry's network. Buyers seeking quotes for parts are responsible for defining the specific requirements for those parts. Please refer to our terms and conditions for more information.
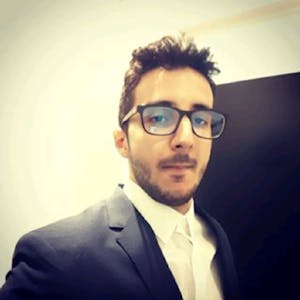