Laser cutting is widely used in the automotive, aerospace, electronics, and manufacturing industries due to its precision, speed, relatively low cost per part, and versatility. It can be used on a range of materials, including metals, woods, plastics, paper, and some composites. This article lists general design guidelines, laser cutting rules, and safety tips for operating a laser cutter. A general overview of laser cutting, including how laser cutters work, common applications, their pros and cons, and tips on the best laser cutting machines and software, will be provided.
1. Never Leave the System Running Unattended
Laser cutters use high-power, focused beams of light, typically from CO₂, fiber, or diode lasers, to cut and engrave various materials. The energy densities involved are sufficient to ignite combustible materials such as wood, paper, and many plastics. While most metals will not ignite, the high-temperature sparks and molten slag generated during cutting can ignite nearby flammable materials. To minimize fire risk, never operate a laser cutter unattended, even for short jobs.
2. Always Keep a Fire Extinguisher Nearby
Even when all recommended fire safety precautions are followed, there is still some risk of unintended ignition of the material being laser cut. Always keep a fire extinguisher near the laser machine, in accordance with local health and safety regulations, and ensure it is regularly serviced. A CO₂ fire extinguisher is the most suitable type for this application.
3. Always Keep the Area Around the Laser Cutter Clear of Debris, Clutter, and Flammable Materials
Some industrial metal laser cutters do not have enclosures. Hot metal sparks and slag can scatter beneath and around the laser cutter. Debris and clutter also pose a tripping hazard to the laser machine operator. Always keep the laser cutter and its surrounding area clean.
4. Keep the Laser Cutter's Interior Clean and Clear of Debris
Regardless of whether the machine has an enclosure, debris inside the laser cutter can obstruct the laser head and potentially damage the equipment. Dust and other materials inside the laser cutter can also present a fire hazard. A vacuum cleaner can be used to effectively clean the interior of a laser cutter.
5. Inspect the Cutter Tray's Interior After Each Use and Clean It if There Is Debris or Residue
Debris on the cutter tray can obstruct the cutting head and prevent the raw material from sitting flush on the tray. This may lead to inaccurate or misaligned cuts.
6. Never Modify or Disable Any of the Laser System's Safety Features
Laser cutting machines are equipped with automatic safety features designed to protect the operator during use. These include door interlocks, which disable the laser if the enclosure door is opened. This reduces the risk of the operator suffering permanent eye damage from reflected laser light. Disabling this feature may void the laser cutter's warranty and compromise user safety.
7. Never Use the Laser Cutter Until All Covers Are in Place and the Interlocks Work Properly
A laser cutter should be regularly inspected to ensure that all mechanical, optical, and safety systems are functioning correctly. In addition to inspecting the optics and mechanical components, it is essential to verify that all safety systems are operational. This includes verifying that machine interlocks function correctly and that all covers and doors close securely to prevent any laser light from escaping.
8. Never Stare Directly Into the Laser Beam or Optics
Even low-power lasers used for engraving or etching can cause permanent eye damage. Although it is unlikely to stare directly into the beam under normal conditions, reflected laser light from the workpiece can still enter the eye and cause injury.
9. Avoid Direct Viewing of Optical Instruments
Do not look directly through any optical components, such as lenses or beam expanders, while the laser is operating. These elements can focus or redirect laser light in unexpected ways, increasing the risk of eye injury.
10. Use Only Approved Materials
Laser cutters can process a wide variety of materials, but some, such as PVC, PTFE, or fiber-reinforced composites, should never be used due to toxic fumes or the risk of equipment damage. If unsure whether a material is safe, consult the laser cutter’s operating manual or the machine supplier. Avoid cutting any material that produces toxic or corrosive fumes, especially in the absence of a confirmed list of approved materials. Refer to the Material’s Safety Data Sheet (MSDS) or Safety Data Sheet (SDS) to confirm whether a material is safe for laser cutting.
11. Keep in Mind That There Are Materials That Can Emit Toxic and Corrosive Fumes
Some materials are unsuitable for laser cutting because they release hazardous fumes or particulates when exposed to laser energy. Examples include PVC, fiber-reinforced composites, and synthetic leathers, all of which can emit toxic gases or corrosive byproducts during cutting. PVC, for instance, emits chlorine gas, which is highly toxic to humans and corrosive to the optics and electronics of laser cutters.
12. Never Use a Laser Cutter if the Viewport Is Damaged
Some laser cutters have a viewport that allows the operator to monitor the cutting process and ensure proper operation. These viewports are typically coated with optical filters that block harmful wavelengths of laser light to protect the operator’s eyes. If the viewport is damaged, unfiltered laser radiation may escape, posing a serious risk of permanent eye injury or blindness.
What Are Some Tips for Creating a Laser Cutting Design?
Laser cutting can be relatively easy to perform. Here are some tips for ensuring optimal results:
1. Use Software That Enables You To Create Vector Files
For laser cutting, it is important to use vector-based file formats with well-defined, mathematically precise edges. The design edges in a vector image are defined by mathematical expressions. This is in contrast to bitmap files, whose images are made up of multiple pixels. Zooming into a bitmap image will reveal the individual pixels, whereas a vector image does not resolve into pixels but maintains its shape regardless of zoom level or scaling. A bitmap file must be converted into vector format before the laser cutting software can generate machine instructions. Inkscape®, a free open-source vector graphics editor, can be used to trace bitmap images and convert them into vector files. Once in vector format, the file can be loaded into the laser cutting software.
2. Details Can't Be Smaller Than the Thickness of the Material
A common guideline in laser cutting is to avoid design features smaller than the thickness of the material being cut. For example, when cutting a 10 mm thick sheet of steel, designing an 8 mm hole may lead to poor edge quality or dimensional inaccuracy. It is, of course, still possible to do, but the quality of the hole and its accuracy will be poor.
3. Set a Minimum Distance Between the Cutting Lines
For thick materials with low melting points, closely spaced cutting paths may cause localized melting, warping, or vaporization between the cuts. Material testing is recommended if closely spaced cutting lines are necessary for the design.
4. Never Forget About the Kerf for Cutting
The width of material removed during laser cutting is referred to as the “kerf.” Kerf width typically ranges from 0.1 mm to 1.0 mm, depending on the material, laser type, and cutting parameters. The width depends on the material type, laser power, cutting speed, and material thickness. The laser cut path should be offset so the kerf’s inner edge aligns with the outer edge of the intended part dimensions. Laser cutting software can compensate for kerf width by offsetting the laser cut path so that it is fully outside the intended part shape. Alternatively, the original CAD design can be modified to account for the kerf position.
5. Choose the Right Material
Choosing the correct material is critical to the success of a laser-cutting project. It is important to understand what materials the laser cutter is capable of processing. Most desktop laser cutters are not powerful enough to cut metal and are primarily designed for non-metallic materials like wood, acrylic, paper, and thin plastics. Some materials, such as PVC plastic, should be avoided entirely because they emit toxic and corrosive gases that are harmful to both users and equipment.
What Is a Laser Cutter?
A laser cutter is a machine that focuses a high-powered laser beam to cut or engrave materials with precision. Laser beams are typically generated using CO₂ lasers, fiber lasers, or diode lasers, depending on the application and material type. For more information, see our guide on Laser Cutting.
Figure 1 is an example of a laser cutter:
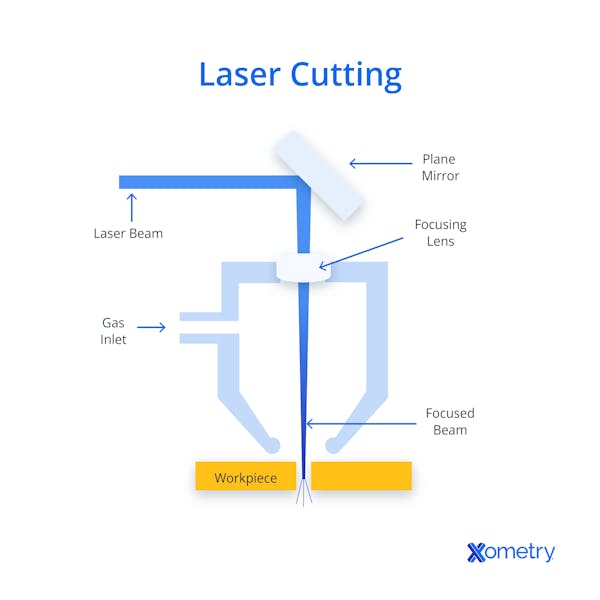
What Are the Uses of Laser Cutters?
Laser cutters are used in a wide range of industries, including automotive, aerospace, electronics, signage, and general manufacturing. They can cut sheet, plate, or tubing materials into complex shapes that may undergo further processing. Laser-cut components can then be bent, welded, fastened, or otherwise assembled into a final product. Learn more in our guide on the Uses of Laser Cutting.
What Is the Advantage of Using a Laser Cutter?
Laser cutters can automatically process complex designs with high precision in a variety of materials. They offer precision that often exceeds what can be achieved with manual cutting or alternative methods like oxy-fuel or plasma cutting. Laser cutting typically produces cleaner edges than flame or plasma cutting, reducing the need for secondary finishing.
What Is the Disadvantage of Using a Laser Cutter?
Laser cutting can be costly to implement due to high initial capital investment, ongoing energy consumption, and regular maintenance requirements. To justify the investment, a laser cutter typically requires a high utilization rate to remain cost-effective. For small operators with limited production or occasional laser cutting needs, outsourcing may be a more economical alternative to purchasing and maintaining a laser cutter. For more information, see our Advantages and Disadvantages of Laser Cutting.
How Does Laser Cutting Work?
Laser cutting works by generating a focused beam of coherent light composed of high-energy photons. The most common types of lasers used in cutting are CO₂, fiber, and diode lasers, each suited to different materials and power requirements. The laser beam is directed via mirrors (in CO₂ systems) or fiber optics (in fiber lasers) toward a lens that focuses it onto the material’s surface. The focused beam moves along the programmed path, cutting by melting, burning, or vaporizing the material depending on its properties.
Common FAQs About Laser Cutting and Designing
Is Laser Cutting Software Necessary for Laser Cutting?
Yes, laser cutting software is essential for converting design files into machine instructions. The software translates the design into machine-readable instructions that specify laser power, cutting speed, and beam path.
What Is the Best Laser Cutting Software?
The best laser cutting software depends on the user’s application and skill level. For simple artistic or hobbyist projects, software like LaserGRBL is adequate, especially for diode laser engravers. For more advanced or industrial applications, LightBurn® offers robust design, control, and optimization features compatible with many laser platforms.
What Is the Best Laser Cutting Machine?
The best laser cutting machine depends on the application type, material, required precision, and production volume. For hobbyist projects involving wood, paper, acrylic, or light plastics, the Glowforge® Basic is typically sufficient. For industrial applications such as cutting metal, a high-power fiber laser system from a manufacturer like TRUMPF or Bystronic is a suitable option. The specific model should be selected based on material type, cutting speed, precision needs, and budget, in consultation with the manufacturer.
Is Laser Cutting Suitable for Industrial Use?
Yes, laser cutting is highly suitable for high-precision, high-volume industrial manufacturing. It is used extensively to cut metals (e.g., steel, aluminum), as well as wood, plastics, and composites. Industrial systems use multi-kilowatt fiber lasers for metals, CO₂ lasers for non-metals, and direct diode lasers for certain specialized tasks. For more information, see our guide on How Is Laser Cutting Used In Industries.
Is There an Alternative to Laser Cutting?
Depending on material type and application, alternatives to laser cutting include plasma cutting, waterjet cutting, and mechanical CNC machining. Plasma cutting is more affordable but generally produces rougher edges, especially on thicker materials, often requiring post-processing. Waterjet cutting can handle thicker and multi-layered materials. It is a cold-cutting process that avoids thermal distortion and produces clean edges. However, waterjet systems typically have higher operating costs and slower cutting speeds, and the equipment is more expensive.
Are Laser Cutters Required to be Registered?
No, laser cutters do not need to be registered. However, their operation must comply with relevant occupational health, laser safety, and environmental regulations. If unsure, consult local regulatory authorities, as safety regulations and legal requirements can vary by country, state, or industry.
Summary
This article presented laser cutting and designing, explained what it is, and discussed the guidelines, rules, and safety tips to consider when using this manufacturing process. To learn more about laser cutting, contact a Xometry representative.
Xometry provides a wide range of manufacturing capabilities, including sheet cutting and other value-added services for all of your prototyping and production needs. Visit our website to learn more or to request a free, no-obligation quote.
Copyright and Trademark Notices
- Lightburn® is a trademark of LightBurn Software, LLC
- Glowforge® is a trademark of Glowforge Inc.
- Inkscape® is a registered trademark of Software Freedom Conservancy, Inc
Disclaimer
The content appearing on this webpage is for informational purposes only. Xometry makes no representation or warranty of any kind, be it expressed or implied, as to the accuracy, completeness, or validity of the information. Any performance parameters, geometric tolerances, specific design features, quality and types of materials, or processes should not be inferred to represent what will be delivered by third-party suppliers or manufacturers through Xometry’s network. Buyers seeking quotes for parts are responsible for defining the specific requirements for those parts. Please refer to our terms and conditions for more information.
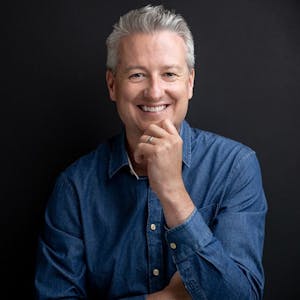