Both laser cutting and waterjet cutting provide an extremely accurate and versatile way of cutting through materials, making them a couple of the most popular techniques in modern manufacturing. But they do have some significant differences, mainly in how they remove material to perform the cuts and the types of materials they are best for. In this article, we’ll go through these differences to help you better understand when to use either one.
What is Laser Cutting?
Laser cutting uses a very high-powered laser to cut or engrave materials, which it does by moving the flatbed they’re placed on. It can be performed on many materials but some of the easiest ones to laser cut are wood, cardboard, and acrylic. This technique works by burning through substances, so it releases odors as it does so. The machine generates an extremely strong, adjustable beam of light, which is focused on a tiny, seriously hot point. The path it follows has been set beforehand using CAD (computer-aided design) software in conjunction with the cutter’s own internal program. Once the cutting is done, the part can be removed. When it comes to the laser these machines use, there are two primary types: CO2 and fiber lasers. The following image shows an aluminum part that’s been laser-cut:
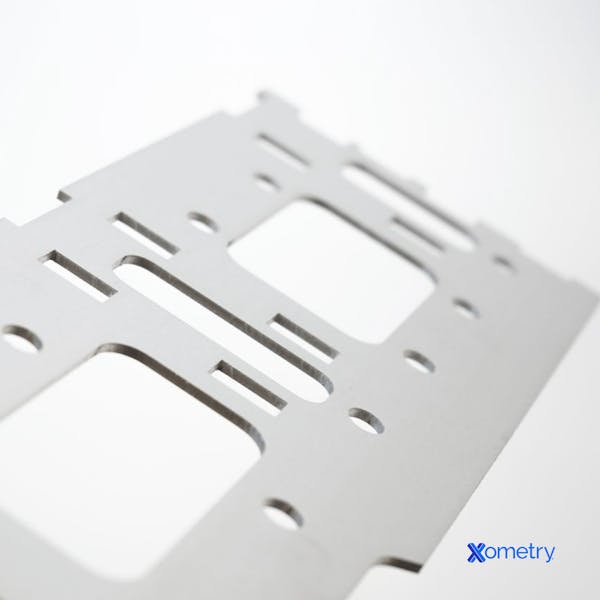
Laser cutters are pretty quick, with most of them generally capable of cutting at speeds of 20–70 inches per minute. That’s a lot faster than other methods, like waterjet cutting—which we’ll consider later—which can only usually handle 1–20 inches per minute. Using a laser cutter also allows you to be extremely precise, as it usually has a minimum cutting slit size of 0.15 mm. Other benefits include that it’s relatively quiet (around 75dB) and doesn’t produce much waste, whether that’s solid or liquid. A couple of downsides, though, are that lasers can only typically cut materials up to around 30-40 mm thick if you’re using an extremely powerful one—and it can produce potentially dangerous vapors, so good ventilation is a must.
What is Waterjet Cutting?
Sometimes called waterjet machining, this technique uses a high-velocity water stream to either remove material from a piece’s surface or split it entirely. Most of the time, it’s used on materials like wood, rubber, and plastic. If you want to cut through something thicker like metal or stone, then you can mix an abrasive material in with the water.
The general way it works is that water from the reservoir is pumped into the intensifier, which boosts the pressure anywhere from 5 bars to around 4,000 bars. The pressurized water sits in an accumulator, ready to be blasted. It then gets directed to the nozzle, where it’s released at speeds of around 1,000 meters per second. If an abrasive like garnet or aluminum oxide is mixed with the water, it’s housed inside a chamber within the nozzle. The water is blasted at such speeds that it actually erodes the surface it hits. If abrasives are used, the procedure is classified as abrasive waterjet cutting, but if it’s only water, then it’s called pure waterjet. This is an image of waterjet cutting in action by making a Xometry logo:
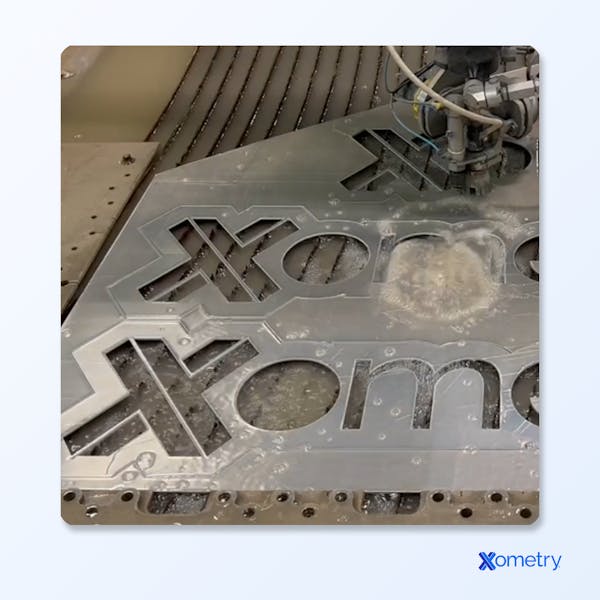
This method is amazing for thick materials and can tackle thicknesses even up to around 300 mm. Also, it doesn’t generate heat onto the workpiece, nor does it produce hazardous byproducts. Another great thing about waterjet cutting is that it can create beautifully clean and smooth cuts, which, in most cases, don’t even require any post-processing. Some potential drawbacks you might want to consider are that it can’t really maintain the same precise dimensional tolerances as laser cutting can, and when it comes to materials less than one inch thick, it can be significantly slower. Overall, waterjet cutting is considered an environmentally friendly technology, but in order to separate the used abrasive and reuse the water, you might potentially need hazardous waste disposal.
Attribute | Laser Cutting | Waterjet Cutting |
---|---|---|
Attribute Speed | Laser Cutting Roughly 70 inches per minute for materials under an inch thick | Waterjet Cutting Generally around 20 inches per minute for materials under an inch thick |
Attribute Accuracy | Laser Cutting 0.15 mm | Waterjet Cutting 0.5 mm |
Attribute Incompatible materials | Laser Cutting Reflective and thermolabile substances (they respond negatively to heat) | Waterjet Cutting Tempered glass and diamonds (because it doesn’t generate heat) |
Attribute Cost | Laser Cutting The machine can cost anywhere between $8,000 and $250,000 | Waterjet Cutting From $60,000 to $450,000 (but more cost-effective when cutting thicker parts) |
Laser Cutting vs. Waterjet Cutting Attributes
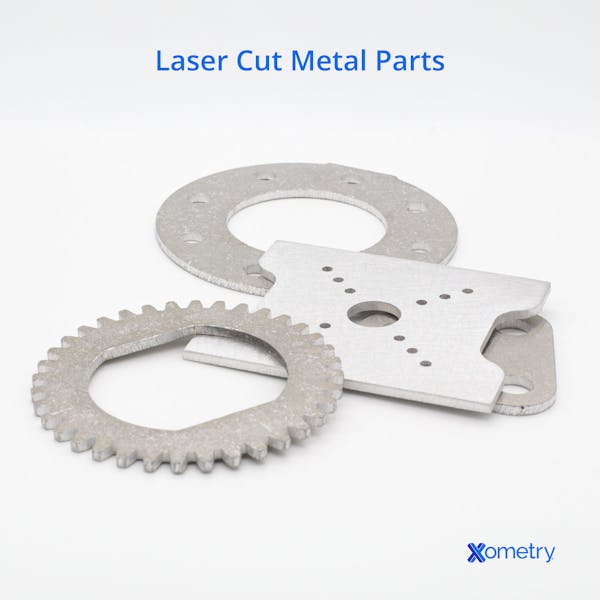
Frequently Asked Questions on Laser and Waterjet Cutting
What’s the maintenance like on these machines?
For laser cutters, you need to clean the lenses and mirrors regularly. On top of this, it’s a good idea to carry out checks periodically on the ventilation system to make sure no fumes have built up. But waterjet cutters actually need even more frequent maintenance because of the wear that the water and abrasives can cause. It’s good practice to inspect the nozzles, seals, and abrasive hoppers, and of course, treat the water to remove waste.
What safety precautions should I take for each machine?
As mentioned briefly, laser cutting requires proper ventilation. In addition, it’s a good idea to wear protective eyewear that can shield you against the intensity of the laser. With waterjet cutting, you’re dealing with high-pressure abrasives, so definitely wear protective clothing and eye protection. We also highly recommend you get some training on how to use these machines safely because they can be quite intense.
Are there any mutual alternatives to laser cutting and waterjet cutting?
There sure are! Two of the most comparable alternatives are plasma cutting and oxy-fuel cutting. The former uses a stream of ionized gas at temperatures higher than 20,000°C to melt material away, and it’s mainly used on metals. The latter heats metal to the ignition temperature, which is basically the point at which combustion starts, using a mixture of oxygen and fuel gas, like acetylene. It then blasts some concentrated pure oxygen directly into the heated area, which generates an exothermic chemical reaction between the oxygen and the metal. This creates a substance called iron oxide, or slag, along the warmed area, and the oxygen jet finally removes this, which allows it to cut through the metal. It can be used on some non-ferrous metals, too, but it won’t work as well.
How Xometry Can Help
Manufacturing and fabricating parts are more than possible at Xometry, and we have a long list of services you can get instant quotes for depending on your needs, including laser cutting and customized plastic fabrication services. Take a look at our plastic 3D printing, plastic extrusion, and plastic laser cutting pages for more information.
Disclaimer
The content appearing on this webpage is for informational purposes only. Xometry makes no representation or warranty of any kind, be it expressed or implied, as to the accuracy, completeness, or validity of the information. Any performance parameters, geometric tolerances, specific design features, quality and types of materials, or processes should not be inferred to represent what will be delivered by third-party suppliers or manufacturers through Xometry’s network. Buyers seeking quotes for parts are responsible for defining the specific requirements for those parts. Please refer to our terms and conditions for more information.
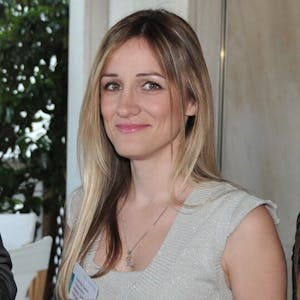