Gas welding, also known as oxy-acetylene welding (although nobody really calls it that), is a common fabrication process that can be done pretty much anywhere since you don’t need to be near an electrical outlet, and don’t need copious training, either. In this article, we’ll learn more about it, including when it’s used, its different types, and its pros and cons.
What is Gas Welding?
Gas welding uses oxygen and fuel gas to create a hot flame that can melt parts of metals and join them together. When cooled, this creates a very strong bond. To a certain extent, gas welding has been replaced by electrical welding forms (they’re cheaper and don’t involve gas which could be considered a safety hazard by some), but gas welders are still very much in use by hobbyists and professionals (including some Xometry customers) alike as it’s effective, simple, and portable. The below diagram explains how the process works:
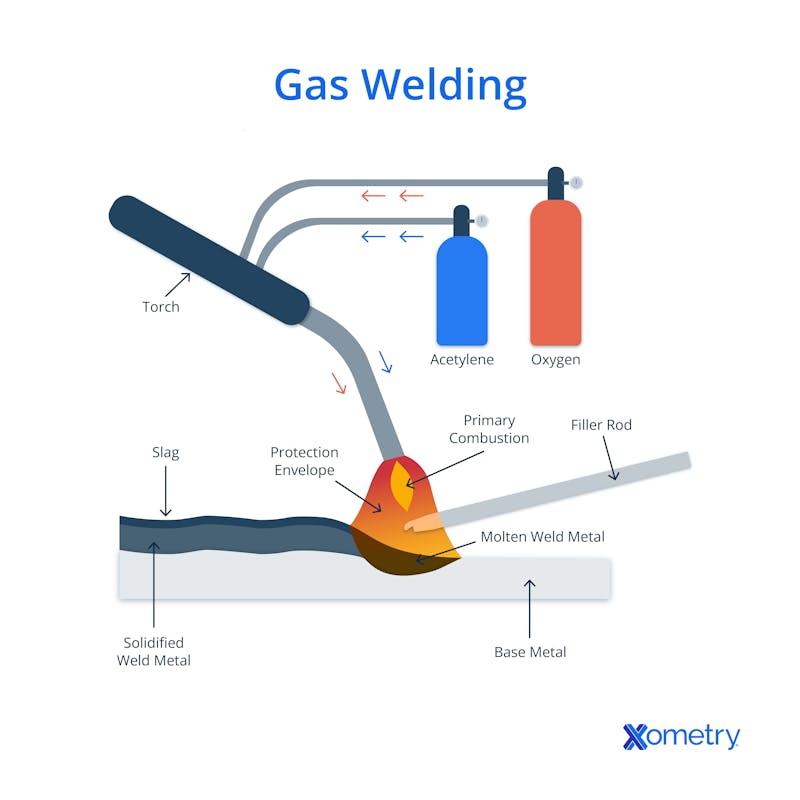
There are five types of gas welding which are categorized according to what gas is used (not all gas welding methods use the same type of gas). These are butane or propane, hydrogen, MAPP (methylacetylene-propadiene propane), oxy-acetylene, and oxy-gasoline. You’d usually opt for different fuel gases depending on your circumstances and what you need to weld. Although it's often used for repair work, gas welding can be turned to for fabricating sheet metal, joining aircraft parts, making automotive chassis and frames, and even joining high-carbon steel. If parts need to look good, too, they’ll more than likely have to go through some form of post-processing.
Your temperature, pressure, speed, and torch position can easily change depending on how you’re welding (i.e. the type of fuel you’re using, your oxygen ratio, or your ambient conditions). Let’s see how:
Temperature
To control the temperature of a gas welding flame, all you have to do is adjust the ratio between oxygen and fuel. The more fuel you add, the lower the temperature will be. That way, you can adjust the temperature to match each material’s melting point. But, for high-strength steel, the heat could mess with its mechanical properties.
Pressure
By adjusting the pressure ratio between the delivery of oxygen and the fuel gas, you can get three types of flames: neutral, oxidizing, and carburizing. The most common of these is the neutral flame, which is easy to spot because it has a small bright white inner flame and a larger blue flame around it. You can get it by mixing almost equal amounts of oxygen and fuel gas. For an oxidizing flame—perfect for welding cast iron and zinc alloys—mix more oxygen than fuel gas. You’ll notice that the inner flame is much shorter and more pointed and burns slightly hotter than a neutral flame. If you mix more fuel gas than oxygen, you’ll get a carburizing flame, which has a visible secondary flame between the short inner one and the larger outer one. This type of flame is popular among Xometry customers for welding aluminum and its alloys.
Speed
The speed at which you need to weld depends on how long it takes to form a proper weld pool. Be careful not to move so fast that the weld doesn’t complete, and don’t move slow enough to burn a hole through the material. In general, this type of welding isn’t as hot as other types, so it might take a little longer.
Torch Position (aka Gun Position)
The torch position can directly affect the weld pool size. If you notice your weld pool getting too big, it means everything’s getting too hot, so try moving the torch parallel to the weld to reduce some of the heat. On the other hand, if the weld isn’t receiving enough heat and the weld pool is too small, move the torch almost perpendicular to the weld. Also, adding filler material needs heat, so it becomes easier and faster to do so when your weld pool is very hot. Another thing to be aware of is that this type of welding lacks flux shielding, so keep an eye out for any defects in the weld.
Using a Gas Welder
Here’s your cut-out-and-keep, step-by-step guide on how to use a gas welder:
- Make sure you have all the equipment you need, that it’s all securely attached, and that the nozzle is clear.
- Put the metal on some heat-resistant material like fire bricks, and make sure it’s secure and won’t move around.
- Adjust the fuel gas with the nozzle’s regulator closed. Open the cylinder shut-off valve, and slowly open the regulator to the pressure you want. When that’s set, close the fuel gas shut-off valve at the torch.
- Do the same as step 2, but now with the oxygen supply.
- Only turn on the fuel gas at the torch and ignite the flame. At first, the flame will let off some black smoke from the unburnt carbon, so make sure you don’t breathe any of it in. Then, open the fuel valve at the torch until the smoke stops.
- Open the oxygen valve at the torch and adjust it until you get the type of flame you need
- Make a tack weld at each end of the joint to stop the pieces from moving during welding. You can do this by holding the torch at a 45-degree angle close to the metal and moving in a zigzag pattern between the metals. When they heat up and a weld pool forms, remove the heat.
- Welding the joint is very similar to making the tack welds. Move in the same zigzag way at the same angle across the two pieces of metal until the pool starts to form. Then, push the pool along by moving the torch slowly from one end to the other.
- When you’ve finished, let it air-cool. Don’t involve water because that’ll make the weld brittle.
- When shutting everything off, always turn off the fuel gas first and then the oxygen, and then close the shut-off valves at the cylinders.
Materials
Most metals can be gas welded to metals of the same type. For example, steel can be welded to steel, but not to aluminum. Another benefit of this process is that it’s compatible with both ferrous and non-ferrous metals. In the table below, we’ve listed some of the most common gas-weldable metals:
Metal | Description |
---|---|
Metal Aluminum | Description With a relatively low melting point of 1,220 degrees Fahrenheit, aluminum is welded using a carburizing flame. When gas welding aluminum, it’s important to remove the oxide layer with a brush because it has a much higher melting point than the aluminum itself. |
Metal Copper | Description One of the most popular metals among our customers for making water and gas pipes, copper pipes can be connected either by gas welding or forming using compression joints. Copper is slightly different from other metals when welding, in that you need to place a fitting over the pipe first, and heat it along with the pipe instead of heating the joint directly. You’d then add filler metal to the joint and capillary actions will suck the melt into the joint. |
Metal Stainless Steel | Description Stainless steel requires a lot of heat to melt because it has a very high melting point. It’s also protected against corrosion because of its chromium content (at least 11%). |
Metal Brass | Description Brass is welded using an oxidizing flame and is made up of copper and zinc. It’s also highly thermally conductive and has a melting point of 1,710 degrees Fahrenheit so only a large nozzle can apply enough heat to melt it. |
Gas Welding Materials
How Xometry Can Help
We provide a wide range of manufacturing capabilities and services here at Xometry, including CNC machining, 3D printing, laser cutting, and of course, gas welding as a post-processing operation. If you’d like to find out more about gas welding or get a free no-obligation quote, reach out to a Xometry representative today.
Disclaimer
The content appearing on this webpage is for informational purposes only. Xometry makes no representation or warranty of any kind, be it expressed or implied, as to the accuracy, completeness, or validity of the information. Any performance parameters, geometric tolerances, specific design features, quality and types of materials, or processes should not be inferred to represent what will be delivered by third-party suppliers or manufacturers through Xometry’s network. Buyers seeking quotes for parts are responsible for defining the specific requirements for those parts. Please refer to our terms and conditions for more information.
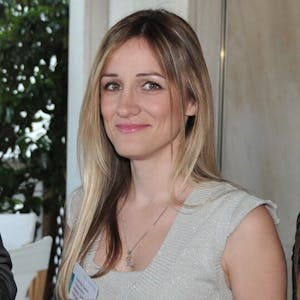