The 4 Benefits of Highly-Trained Manufacturing Employees
Keeping your employees trained up yields a strong return on investment, including boosts in productivity, safety, recruiting, and competitiveness. Successfully trained and compliant team members produce results that benefit the entire company. Here's a quick look at why small manufacturers should invest in employee training.
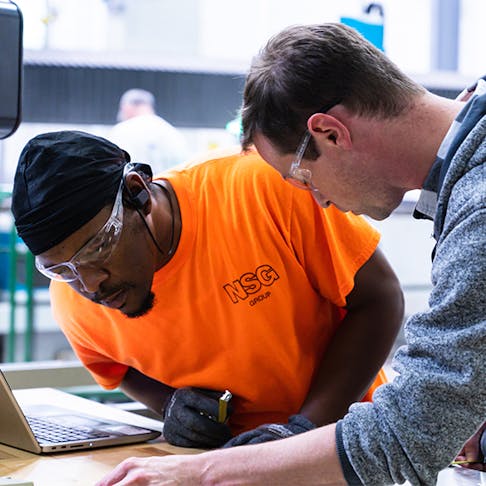
Should Your Manufacturing Employees Get More Training?
“Since most small manufacturing owners wear many hats, they have limited time to plot out comprehensive workforce learning and development strategies tied to business objectives,” says Jeannine Kunz, vice president of Tooling U-SME. “Although they realize people need access to continual learning opportunities, it is difficult to allocate the time, resources and funds needed to invest in training. Unfortunately, in the end most owners don’t act, as other more time sensitive projects take priority.”
Yet employee training and certification are worthy of a higher position on your punch list. Notes Kunz: “Organizations that have a strong learning foundation in place significantly outperform their peers in quality, productivity, customer satisfaction, and market share.”
When your manufacturing workforce is properly trained, your company is better positioned to take advantage of technological and productivity improvements, and reduce turnover and improve your recruitment prospects. Here, then, is a quick look at the four benefits of highly-trained manufacturing employees.
1. Leverage Technological Innovation and Advancement
“As operations become increasingly advanced, employee development programs are becoming critical to manufacturing success,” Kunz says. “Manufacturers can buy all the new equipment/tools and source all the materials they want, but it’s the people they put in place to program, maintain and operate that make the difference in the effective use of the technology. That is why continual learning and development is such an integral part of a company’s overall strategic plan.
2. Improve Productivity
Better-trained employees work more efficiently and make fewer mistakes. This reduces waste and do-overs, which has the additional value of stoking customer trust, satisfaction and loyalty. To quantify training’s impact in this area, multiply your labor cost by your estimated productivity improvement.
3. Reduce Turnover and Improve Recruitment
“Employee retention is a significant issue for companies and building a culture of learning is a big step towards improving turnover,” Kunz adds. It’s also a key factor in recruiting and retaining younger employees. Multiple surveys show that professional or career growth and development opportunities are especially important to younger members of the workforce. Mentioning continuing education and training opportunities in want-ads and recruitment marketing is a smart move.
4. Enhance Safety
It’s also vital to keep employees trained on general health and safety to avoid fines and lawsuits. OSHA offers free compliance assistance for small- and medium-sized businesses to help you identify where you need additional programming. You can also get no-fee insights from your state’s On-Site Consultation Program.
Training is Worth the Investment
Should you pay for training? Most experts say yes. Successfully trained team members produce results that benefit the entire company, and Kunz adds: “When you consider the process of recruiting and replacing an employee can actually cost more than the employee's annual salary, the return on investment can be quite substantial over time.”
“When successfully organized, workforce training can yield good returns for talent as well as the small manufacturer. Employees inspired by their training become loyal, they innovate and contribute to the strategic goals of the business,” Kunz concludes. “On the flip side, satisfied employers are more apt to invest in their career growth, because their upskilled staff are more productive and efficient.”
[1] Used with permission
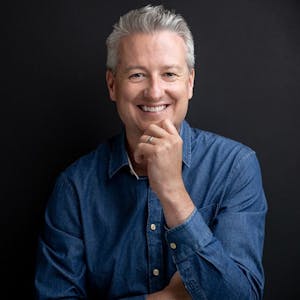