Manufacturing with Garolite Machining
Garolite is a composite material with superior engineering properties. Learn more about its material makeup, mechanical characteristics, design and machining challenges, and finish options.
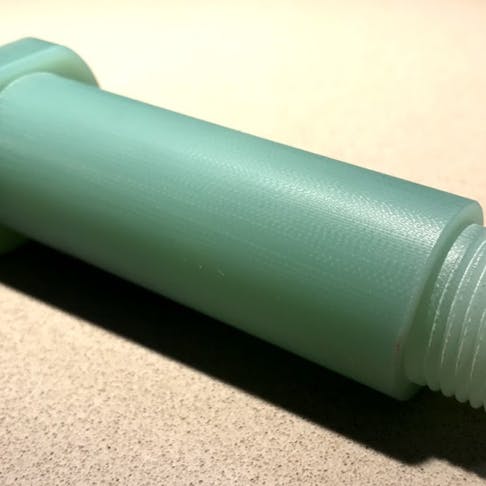
A Composite Solution
Garolite is a high-performance material that offers an install-once-and-last-forever level of reliability. As a composite, it boasts stiffness with superior engineering properties. Read on to understand the considerations of where and how to use this material for maximum value.
Garolite (G-10 or G10) is a composite material created by curing fiberglass and epoxy under high pressures. The resulting glass-epoxy laminate is extremely stable over temperature with low-moisture absorption and a high strength-to-weight ratio. Garolite has electrical insulating properties which are useful for electronic integrations. G-10 also has flame retardant variants, such as FR-4, which are typically used as the substrate for printed circuit boards (PCBs). G-10 is often used synonymously with phenolic as they are both fiberglass composites.
Garolite parts are used in the medical, aerospace, and marine industries due to the material’s dimensional stability, longevity, and resistance to humidity. Corrosion resistance is inherent in G-10 because it is not a metal. G-10 specifies to MIL-I-24768/2 (GEE), MIL-P-18177 GEE and LP-509.
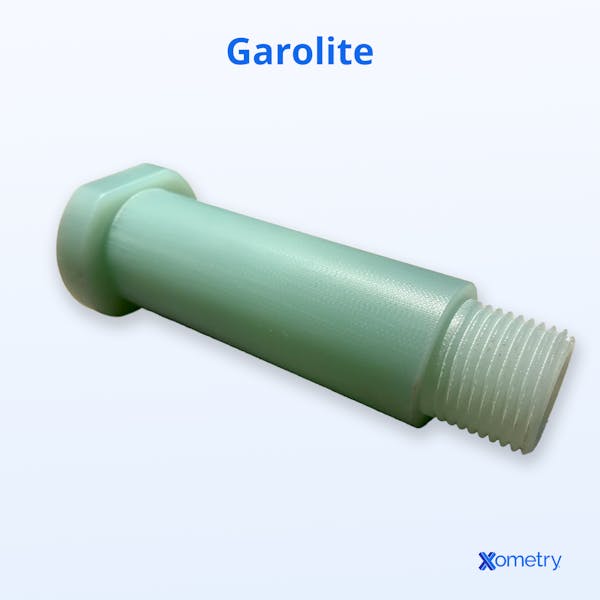
Mechanical Properties | Result |
---|---|
Mechanical Properties Color | Result Light green (sometimes yellow) |
Mechanical Properties Density | Result 1.82 g/cc |
Mechanical Properties Hardness and Rockwell | Result M110 |
Mechanical Properties Water Absorption | Result 0.10% |
Mechanical Properties Tensile Strength | Result 262-310 MPa (grain dependent) |
Mechanical Properties Flexural Strength | Result 448-517 MPa (grain dependent) |
Mechanical Properties Flexural Modulus | Result 16.5-18.6 GPa (grain dependent) |
Mechanical Properties Compressive Strength | Result 448 MPa |
Mechanical Properties IZOD Impact, Notched | Result 6.41-7.47 J/cm (grain dependent) |
Mechanical Properties CTE | Result 9.90 µm/m-℃ |
Mechanical Properties Maximum Service Temp | Result 140℃ |
Mechanical Properties Maximum Service Temp | Result 140℃ |
Mechanical Properties Flammability | Result UL94 HB |
Some mechanical characteristics of G-10 are dependent on the orientation of the feature due to the directional layers in the G-10 laminate.
Machining Challenges
G-10 CNC machining or turning typically requires high RPMs and secure workholding. Because of the fiberglass components, proper ventilation and safety equipment is a must. This includes respirators, protective garb, and eye protection for machinists. Medical G-10 parts are typically machined dry (i.e., no coolant) to avoid any material contamination but can also be cut with coolant to mitigate dust. The glass abrades standard cutting tools, so diamond-coated or super-alloy endmills are recommended to extend tool life with this material.
After cutting, Garolite typically produces a significant amount of dust which resembles powder instead of standard machining chips. Machinists should use special care to remove the dust for disposal without blowing it airborne. Machine shops that typically cut Garolite, glass-filled nylon, glass-filled ULTEM (PEI), carbon fiber, and graphite will have dedicated dust evacuation collection systems in the machines to facilitate clean up and avoid dust contamination.
Garolite parts can have features such as threaded holes that are typically milled, not tapped. External threads are turned on a lathe or thread milled instead of using a die. This is because the laminate material has a risk of delamination if enough heat and pressure is generated parallel to the grain.
Part Finishing
Garolite parts typically finish smooth to the touch, with a matte surface. The grain of the material can be apparent depending on the cut path. In particular, a countersink against the grain of the part will appear lighter than the rest of the part due to the gradual transition between layer cross-sections. G-10 parts will not hold a polish without a secondary coating.
FREE CNC Machining Design Guide
G-10 Design Limitations
The only way to produce parts in G-10 is through machining. G-10 laminate typically comes in sheet, rod, and bar shapes. Part size in this material may be limited if there is no stock size available. It is recommended for designers to use common stock thicknesses whenever possible on their project to avoid machining mid-layer in the laminate. Generous radii are recommended for internal corners due to the high RPMs needed when machining G-10. Smaller radii require smaller tools, which can wear out quickly against the glass composite.
Threaded inserts, such as helical coils, are recommended to increase the hold strength on a part. This is particularly useful if there is high torque or high repetition required on the thread.
G-10 is best used in internal components because it can break down under long-term UV exposure and lose its properties.
Because of the dust mitigation that is necessary for handling Garolite, there are fewer machine shops which readily manufacture this material. This, combined with a high material cost, makes this material more premium-priced, with a longer lead time when compared to other standard plastic or metals.
Xometry’s Garolite Supply Chain
Xometry, a leading manufacturer of custom Garolite machined components, utilizes a large Partner Manufacturing Network to produce parts to-spec and on-time. Xometry’s Instant Quoting Engine ™ allows creators to instantly quote Garolite projects with a 3D CAD model and further specify tight tolerances, inspection criteria, material certifications, and needed quantities. Xometry offers domestic Garolite machining services for expedited and standard lead times on G-10 projects as well as an international economy option. Xometry is ISO 9001, AS 9100, and ITAR certified.
To start your Garolite (G-10) project, simply go to get.Xometry.com/quote and upload your 3D CAD model. Xometry accepts STEP (.step, .stp), SOLIDWORKS (.sldprt), Parasolid (.x_t, .x_b), Autodesk Inventor (.ipt), Dassault Systems (.3dxml, .catpart), PTC, Siemens (.prt), ACIS (.sat)
Ready to start making parts with Garolite but don't know how to get started? Watch this video with Xometry Greg on "How to Get an Instant Garolite (G-10) CNC Machining Quote With Xometry." You'll learn how to add part specifications, certifications, inspection reports, drawings, and more.
