Sheet metal fabrication is a process by which metal parts are cut and bent from a roll of stock material that is typically less than 0.25” thick. Cutouts are typically laser cut or punched and then bent using a brake or press machine. Sheet metal fabrication has many commercial applications as a cost-effective way to make metal parts. If you’re looking for a how-to guide to get started with sheet metal fabrication, this mini-guide is a great place to start!
When manufacturing with sheet metal it’s important to be aware of the limitations associated with the process. Sheet metal cannot produce certain complex geometries or parts, and it can also be difficult to hold high tolerances—such as those that are available in CNC machining or 3D printing—on certain features like bends. However, large items that can be manufactured using sheet metal are often much less expensive when compared to similar parts designed for CNC machining or 3D printing.
There are a handful of considerations to keep in mind when designing for sheet metal to ensure cost-effectiveness and manufacturability.
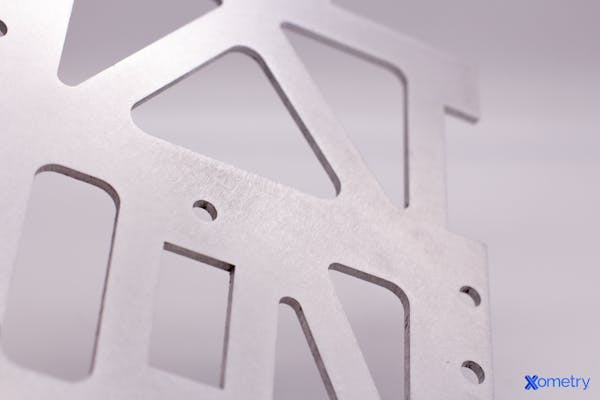
Uniform Thickness
Parts must maintain a uniform wall thickness throughout their entirety. Generally, Xometry is capable of manufacturing sheet metal parts up to 3/8" (9.525mm) in thickness, but this tolerance mainly depends on the geometry of the part.
When considering sheet metal thickness, a single sheet with punches (holes) is a good rule of thumb. Some features, such as countersinks are doable, but counterbores and other machined features are difficult to produce as they require post-machining.
Orient Bends in the Same Direction
One way to reduce costs is to make sure that all bends on the same plane go in the same direction. This allows the brake or press machines to perform the bend without having to reorient the part, which raises costs and can often be difficult depending on the geometry.
Fillets
Sheet metal parts can have very sharp edges so designing fillets of half the material’s thickness for corners will greatly reduce risk of injury.
Become an Expert in All things Sheet Metal Fab
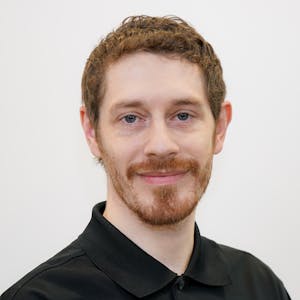