Urethane casting provides end-use, rigid or flexible plastic parts with production-level quality. Built without expensive and time-consuming hard tooling, our urethane casting process uses a 3D printed master pattern and silicone molds to deliver high-quality, short-run parts.
To help you design and build parts that meet your needs, here are 5 actionable tips for designing custom urethane parts.
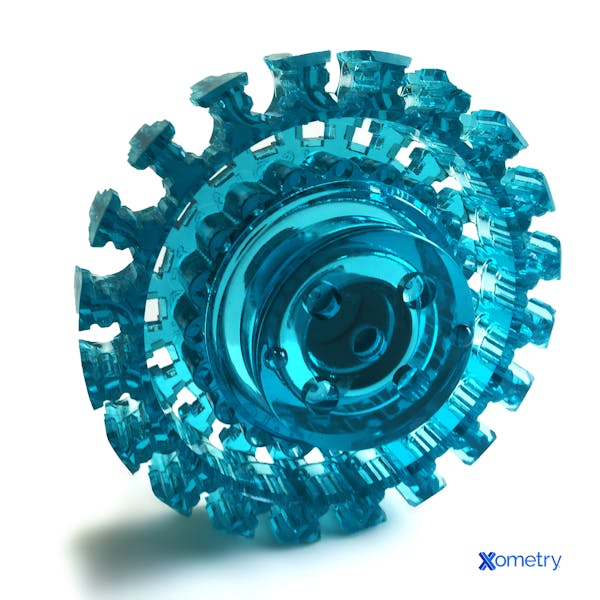
4. Give even wall thickness
The wall thickness of your part should be even throughout so that the urethane can flow into the silicone mold and cure at the same rate. Uniform wall thickness is important in order mitigate potential design issues. Xometry recommends at least 0.020’’ (0.5mm) wall thickness for small parts, and at least 0.040’’(1mm) wall thickness for larger parts. The larger the part, the larger the wall should be to ensure proper support. Also remember that knife edges, or very acute angles, should be blunted by a fillet or chamfer for a repeatable design.
5. Understand drafts and undercuts
During the urethane casting process drafts and undercuts are not a concern because liquefied urethane has the ability to take the shape of any mold. Yet, be sure to take into consideration any other production methods that the prototype will be going through to determine if the part should be designed as intended for end use production. Long zero draft features, while possible, pose a slight risk of part breakage/ warpage when extracting from the mold so a slight angle can help on larger quantity jobs.
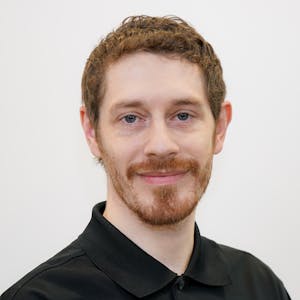