A Quick Guide to Countersinks, Curls, and Hems
Compared to other machining processes, designing Sheet Metal parts is relatively straight-forward. Sheet metal parts are made from a single metal sheet by punching, cutting, stamping, and/or bending and are known for their end-use durability. But there are still many important design-for-manufacturability issues to consider.
Check out our list of quick tips and tolerance specifications for designing Sheet Metal countersinks, curls, and hems! And for even more information, download our free Sheet Metal Design Guide!

The maximum depth of a countersink is .6 times the material thickness of the part. Countersinks must be at least 8 times the material thickness from each other, 4 times the material’s thickness from an edge, and 3 times the material’s thickness from a bend.
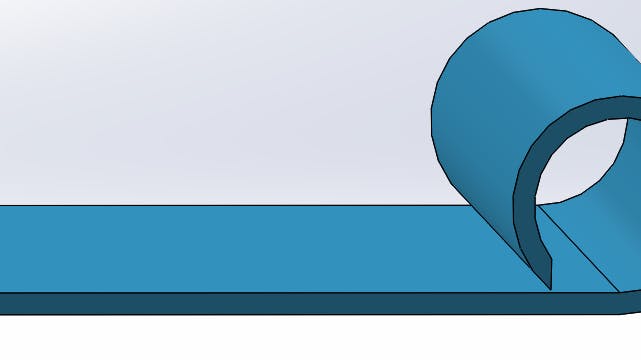
Outside radius of curls must be at least 2 times the material’s thickness. Holes should be placed away from the curl at least a distance of the radius of the curl plus the material’s thickness. Bends should be at least 6 times the material’s thickness plus the radius of the curl.
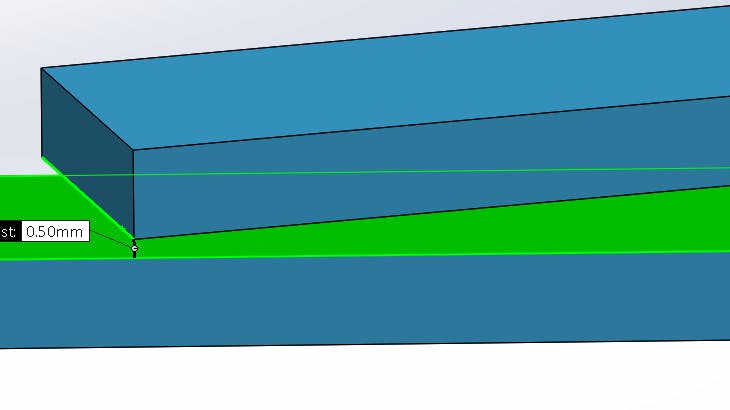
Hems are folds to the edge of a part to create a rounded, safe edge. Hems may be open, flat, or tear-dropped, and tolerances depend on the hem’s radius, material thickness, and features near the hem (Note: flat hems risk fracturing the material at the bend and should be avoided if possible).
For open hems, minimum inside diameter is equal to the material thickness (larger diameters tend to lose circular shape), and the return length is at least 4 times the material’s thickness. Tear-dropped hems must maintain an inside diameter of at least one material’s thickness, an opening of at least ¼ the material’s thickness, and return length is also 4 times the material’s thickness.
