Tolerance is the acceptable range for a dimension which is determined by the designer based on the form, fit and function of a part. Unless specifically called out by the designer, the standard tolerance used by Xometry for CNC machining is +/- .005” for metal parts and +/- .010” for plastic parts.
If tighter tolerances (less than the standard, e.g. +/- .002”) are required, the information must be communicated as to which dimensions require a more narrow range. This can be specified at the part modification level in our instant quoting platform. As a point of reference, a piece of paper is about 0.003” thick.
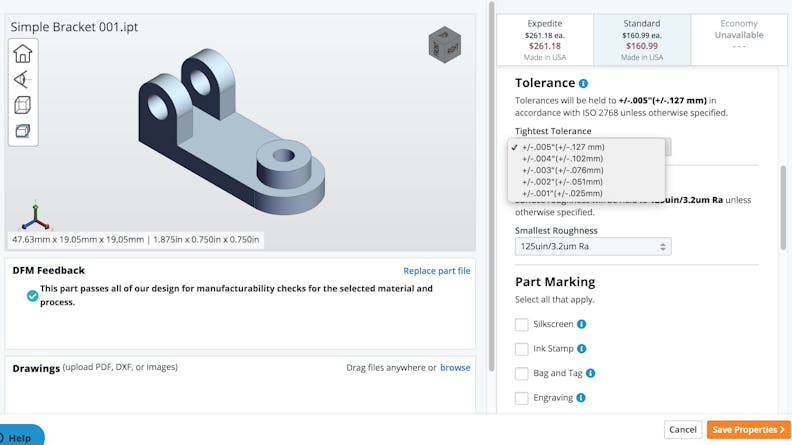
You can toggle between different tolerances in the Xometry Instant Quoting Engine
Tighter Tolerances = Increased Costs
It is important to keep in mind that a tighter tolerance can result in additional cost because of increased scrap, additional fixturing, special measurement tools and/or longer cycle times because the machine may need to slow down in order to hold the tighter tolerance. Depending on the tolerance call out and the geometry associated with it, costs can be more than double of what it would be to hold the standard tolerance.
Overall geometric tolerances can also be applied to the drawing for the part. Based on the geometric tolerance and type of tolerance applied, additional cost may be the result because of increased inspection times.
The best way to apply tolerances is to only apply tight and/or geometric tolerances to critical areas when it is necessary to meet the design criteria to minimize costs.
Tigher Tolerances Can Mean a Change in Manufacturing Process
Specifying tighter than standard tolerances can actually change the optimal manufacturing process for your parts. For example, a hole that can be machined on a vertical mill at one tolerance range may need to be bored on a lathe in a tighter tolerance range, adding set-up costs and lead time. Even tighter tolerance requirements may require grinding or lapping.
Tighter Tolerances Can Change Inspection Requirements
Keep in mind how features will be inspected when adding tolerances to your parts. If a feature is difficult to machine, it is likely also difficult to measure. Certain features require specialized inspection equipment, and this may increase part costs.
Tolerances are Material Dependent
The difficulty of manufacturing a part to a specific tolerance can be very material dependent. Generally, the softer a material is, the harder it is to hold a specified tolerance due to the material flexing while cutting. Plastics such as Nylon, HDPE, and PEEK may not hold as tight tolerances as steel or aluminum without special tooling considerations.
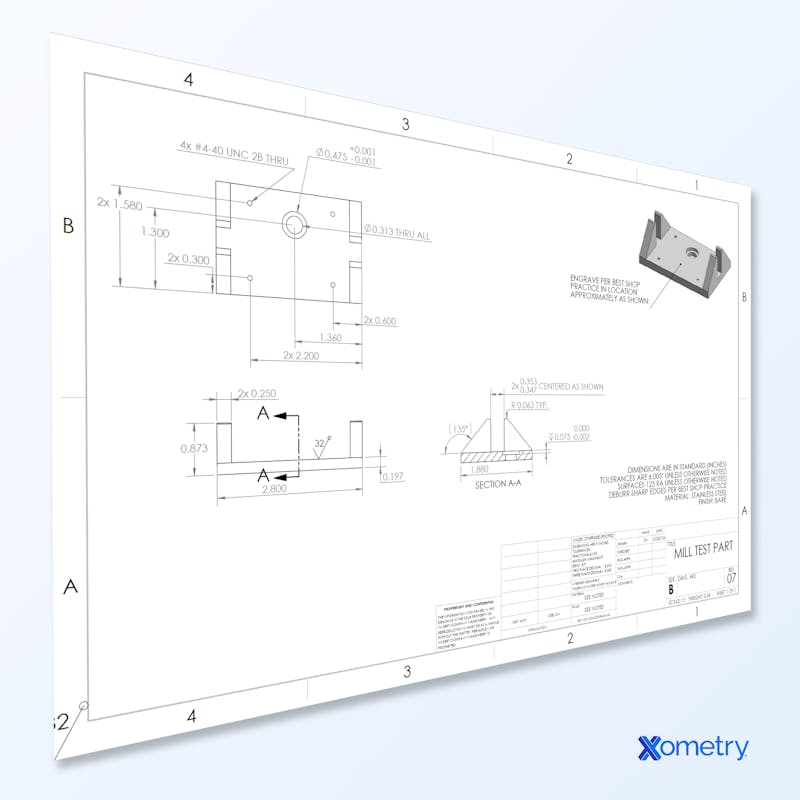
You can find additional resources on CNC tolerances by downloading our ebook, Mastering Tolerances for CNC Machined Parts.
Disclaimer
The content appearing on this webpage is for informational purposes only. Xometry makes no representation or warranty of any kind, be it expressed or implied, as to the accuracy, completeness, or validity of the information. Any performance parameters, geometric tolerances, specific design features, quality and types of materials, or processes should not be inferred to represent what will be delivered by third-party suppliers or manufacturers through Xometry’s network. Buyers seeking quotes for parts are responsible for defining the specific requirements for those parts. Please refer to our terms and conditions for more information.
