Since its inception, the aerospace industry has been trying to reduce the weight of aircraft by all means necessary. 3D printing is a relatively new method for achieving such a goal. 3D-printed parts are nearly always produced quicker, lighter, and cheaper than their conventionally made counterparts. This has led to a massive uptake of 3D-printed parts in aircraft interiors as well as every other aspect of the aircraft. It's not just aircraft, but also rockets that have found a use for 3D printing, with both SpaceX and NASA 3D printing rocket engines and nozzles.
This article will discuss 3D printing aerospace interior components, its purpose, how it works, the advantages, disadvantages, and examples of 3D-printed aerospace interior components.
What Is the Purpose of 3D Printing of Aerospace Interior Components?
There are many reasons why 3D printing is seeing a large uptake in the aerospace industry. The purpose of 3D printing the interior components of an aircraft is to reduce weight (which saves fuel consumption), reduce material waste, and allow for rapid production of small to medium batches of components. Additionally, 3D printing reduces the need for stockpiling as CAD files can be saved on a database and printed as required. It also allows for components to be manufactured into one part removing the need for assembly.
How Does 3D Printing of Aerospace Interior Components Work?
3D printing of aerospace interior components follows the same process as any 3D-printed part. Essentially, all that is needed is a CAD file and a 3D printer. Assuming that a part has already been drawn in a CAD system, the file can then be sliced and ready for input into the 3D printer. The slicing software turns the CAD file into a G-code which is a series of vectors that the 3D printhead can follow to print the part. The file is then uploaded to the printer and is printed. Depending on the print, there may be some post-processing required. Usually, the post-processing involves an abrasive technique to remove the support structure of the 3D print. This process is most effective for small batch productions and productions with complex geometry which would otherwise have a long lead time and high price.
What Are the Advantages of 3D Printing in the Aerospace Industry?
The advantages of 3D printing in the aerospace industry are:
- Weight reduction.
- Reduced fuel consumption (due to weight reduction).
- Reduced lead times.
- Easy-to-use generative design.
- Minimized waste.
- Quick prototyping.
What Are the Disadvantages of 3D Printing in the Aerospace Industry?
3D printing also has its disadvantages which are:
- Not cost or time effective for large-scale production.
- Limited by the size of the print bed.
- Limited by material (although a range of materials is growing).
- Parts are anisotropic, with a reduction in strength in the XY directions due to print layers.
- Large quality variations.
Examples of 3D Printed Aerospace Interior Components Applications?
The range of 3D-printed parts for aerospace interiors is mostly non-structural. It is, however, rapidly growing. Some prime examples of 3D-printed interior components are:
- Vents
- Ducting
- Baffles
- Cable management
- Electrical housings
- Covers
- Trim
- Door latches
- Armrests
- Mounting brackets
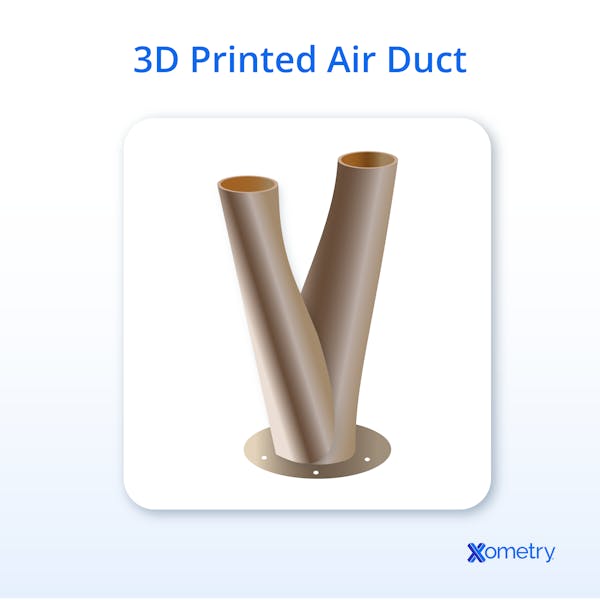
What Are the Materials Used in the 3D Printing of Aerospace Interior Components?
There are various materials that can be printed for use in an aerospace interior. Below are some of the common material groups:
1. Polymers
Polymers commonly used to print 3D components include: PLA (polylactic acid), ASA (acrylonitrile styrene acrylate), ABS (acrylonitrile butadiene styrene), PET (polyethylene terephthalate), and PC (polycarbonate). Polymer 3D-printed parts are lighter than the parts they replace as 3D-printed parts are essentially hollow using a small infill to create support within the part. Plastic 3D-printed parts are printed from a CAD file using a 3D printer and then used for various applications such as: covers, ducting, spacers, curtain headers, and cup holders. 3D-printed parts are as durable as the parts they replace, however, they do lack strength in the load-bearing Z-direction.
2. Carbon Fiber
Carbon fiber is always printed within another material such as nylon or another polymer and is printed in either continuous or chopped fiber form. The continuous fiber form is printed by a separate printhead into the internals of a polymer part. The chopped carbon fiber is less than 1 mm in length and is contained within the polymer filament being printed. Continuous carbon fiber is laid in the load paths to increase the strength of a part in a particular direction. Whereas, the chopped carbon fiber increases strength in the whole part. Some examples of items in which carbon-fiber-reinforced plastics are used are: light switch panels, cabin climate control components, and door latches. Carbon fiber printed parts are highly durable and replace many aluminum parts.
3. Metal
Metal 3D printing is achieved using a slightly different process to polymers. Metals come in a powdered form and are then melted and fused to the print bed and subsequent layers using a laser in a process referred to as selective laser sintering (SLS). Metal 3D-printed parts are less common as metal is used in more structural and flight-critical components and is therefore harder to qualify. However, 3D-printed metal is commonly used in aircraft engines within bearing housings, fuel nozzles, temperature sensors, and heat exchangers.
4. Nylon
Nylon is a 3D-printable polymer. However, it is different from materials such as PLA and ABS as nylon is more flexible and durable. Nylon is less stiff and strong than PLA and ABS but has an impact resistance of ten times that of ABS. Nylon is printed in the same way as other polymers, however, it usually includes carbon fiber reinforcement to compensate for its low strength. Onyx™, by Markforged, is a carbon-fiber-reinforced nylon that has been used for in-flight entertainment consoles, panel switches, and seat frames.
5. Glass Fiber
Similarly to carbon fiber, glass fiber is used in 3D-printed polymers as a reinforcement. Glass fiber comes in a continuous or chopped format. The chopped form is integrated into the filament and provides reinforcement for the general part. Whereas, continuous fiber provides strengthening for a particular load path. Fiberglass is cheaper and less strong than carbon fiber and is used for applications in which carbon fiber would be unnecessarily strong. Finally, glass fiber, as with carbon fiber, has a fatigue life higher than most of the metal components they replace.
What Is the Future of 3D Printing Interior Components in Aerospace?
The future for 3D-printed parts in aerospace interiors is great. While lots of applications are found for 3D printing, there are many more applications to come. This is because 3D printing has opened up options for specialized components without specialized tooling. 3D printing is also expanding the range of materials that can be used. There are already hundreds of 3D-printed parts in airline interiors, and this usage is expected to grow as the US aerospace and defense market value is set to reach $5.58 billion by the year 2026.
For more information, see our guide on How 3D Printers Work.
Does SpaceX Use 3D Printers?
Yes, SpaceX uses 3D printing for their rockets. They use these printers to manufacture rocket engines and nozzles. SpaceX has used 3D printers to print their SuperDraco engine chamber out of Inconel using direct metal laser sintering (DMLS). SpaceX has also 3D printed the Main Oxidizer Valve (MOV) body for the Merlin 1D engine. This part was printed in two days rather than taking seven months to fabricate and has a reduced maintenance schedule.
Does NASA Use 3D Printers in Space?
Yes, NASA has used 3D printers in space. In 2014, NASA used a printer made by Made In Space, Inc., in the international space station to print a printhead faceplate. The printed part was then returned to Earth for analysis. The results of these tests showed that there were no differences between specimens printed on Earth and in space. This has opened many opportunities for 3D printing in space, where materials can be recycled and reused as opposed to the weeks or even months lead time it takes to deliver critical components to the international space station.
Can You 3D Print Airplane Parts Besides Interior Components?
Yes, there are 3D parts being used in all areas of aircraft including: the interior, engines, structure, electrical and hydraulic systems, and for specialized tooling. Specialized tooling is one of the oldest applications due to the reduced need for qualification. Specialized tooling includes: jigs, injection mold tools, casting molds, and adapters. Aircraft also use 3D-printed mount brackets, valves, housings, and bearing cases.
Summary
This article presented 3D printing aerospace interior components, explained it, and discussed the types of materials used. To learn more about 3D printing in aerospace, contact a Xometry representative.
Xometry provides a wide range of manufacturing capabilities, including 3D printing and other value-added services for all of your prototyping and production needs. Visit our website to learn more or to request a free, no-obligation quote.
Copyright and Trademark Notices
- Onyx™ is a registered trademark of Markforged.
Disclaimer
The content appearing on this webpage is for informational purposes only. Xometry makes no representation or warranty of any kind, be it expressed or implied, as to the accuracy, completeness, or validity of the information. Any performance parameters, geometric tolerances, specific design features, quality and types of materials, or processes should not be inferred to represent what will be delivered by third-party suppliers or manufacturers through Xometry’s network. Buyers seeking quotes for parts are responsible for defining the specific requirements for those parts. Please refer to our terms and conditions for more information.
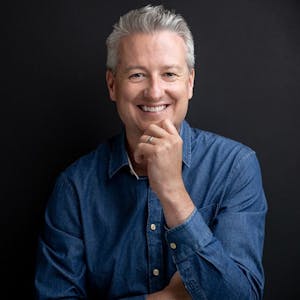