A 3D printing slicer is a software package that converts a 3D model into a set of machine-readable instructions to print the part. The success of the 3D printed part depends heavily on selecting the correct 3D printing slicer settings. These settings can mean the difference between a high-quality part and a difficult-to-clean tangled mess of plastic. The most important settings for an optimal 3D print are temperature, location, number of supports, and anything that can affect the bed adhesion. Getting these settings wrong will most likely result in a failed print. This article will explore the ten most important settings of FDM (Fused Deposition Modeling) printers to keep track of to ensure a successful 3D printed part.
1. Temperature
The temperature settings in 3D printer slicer software refer to the temperatures of the build platform and the extruder hardware (also known as the “hot end”). The optimal build platform temperature helps keep the first printed layer attached to the build platform while also limiting the potential for warping.
The extruder temperature, on the other hand, is the temperature that the plastic is heated to as it is extruded from the print nozzle. Typically the extruder apparatus contains a heating element, which is regulated by a heat sensor, such as a thermocouple.
Both of these temperatures are selected based on the material being extruded. For example, PLA (Polylactic acid) requires a bed temperature of 50–60°C and an extruder temperature of 190–220°C, whereas ABS (Acrylonitrile butadiene styrene) requires a bed temperature of 90–110°C and an extruder temperature of 220–250°C. Many slicers will have predefined temperature settings for specific material classes. These values generally work well without too much tweaking.
2. Speed
Printing speed can be set to a global value in a slicer program. However, it is possible to set specific speeds for specific parts of the print. For example, speeding up the printing of the infill can save significant time, as these areas will not be seen, while printing the walls at a slower speed will result in improved print quality. In general, increasing the speed will result in faster prints, but this will be at the expense of print quality. The more rigid a 3D printer is, the higher the speed it can print at while maintaining good quality.
3. Flow
The flow rate of the 3D printer refers to the rate at which material exits the nozzle. Normally, the flow rate is set at a default value depending on the printer. An incorrect flow rate will result in wall thicknesses that are either too thin or too thick. A high flow rate will result in excessive filament usage, whereas a low flow rate may result in structurally weak prints. The flow rate rarely needs to be changed. The flow rate is usually not changed directly but is modified by entering a factor that is multiplied by the default flow rate.
4. Retraction
Whenever the printer is not actively printing, i.e., when it is moving from one location to the next, it will slowly ooze plastic from the nozzle. This phenomenon can result in thin strings of plastic draped all over the print. Retraction addresses this issue by reversing the extruder to pull the material back into the nozzle when it is not actively being dispensed, thus preventing oozing. Retraction settings can be further customized by setting the amount of material that is retracted as well as the speed of retraction.
5. Cooling
3D printer settings for cooling are primarily linked to the speed of the fan located on the extruder assembly. This fan speed is set on a scale of 0 to 100%. The cooling fan speed is especially important if large unsupported overhangs or bridges are to be printed. This is because the plastic will sag between unsupported areas if not cooled quickly enough. The fan is typically turned off during the printing of the first layer, as this helps produce a better bottom surface and improves the bed adhesion.
6. Infill
Many slicers will have a large number of different infill settings. The most important of these are the infill density and the infill pattern. The higher the infill density, the denser the part, with 0% referring to a part with no infill and 100% referring to a completely solid part. A typical infill density is 20%. The term “infill pattern” refers to the geometric shape of the infill. There are many different infill patterns. The most common is the grid infill. Some patterns optimize print time at the expense of part strength. Others prioritize parts strength but compromise by having a longer print time.
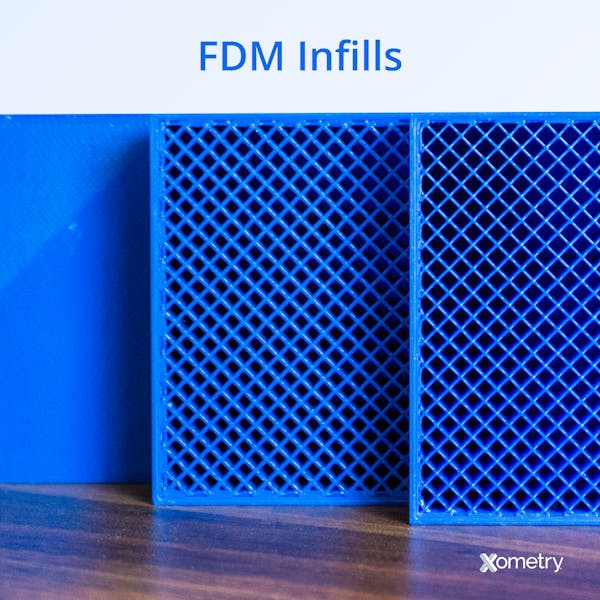
7. Supports
Determining the optimal 3D printing slicer settings for supports is critical to effectively printing parts with overhangs or bridges. Optimizing the cooling rate can assist with printing overhangs without supports, although this is generally not recommended. A 3D printer cannot simply dispense material into thin air. Every layer needs some kind of support beneath it - either the previous layer's print or a designed-in support member that is not a part of the finished product.
In the case of overhanging features, the support material must be built up from the build plate to where the overhang begins. As with infill, the support density and pattern can also be adjusted. The minimum overhang angle can be set to control where supports are placed. This value is typically between 45 and 60% (0% means no supports are placed anywhere, and 90% means that even the slightest overhang is supported).
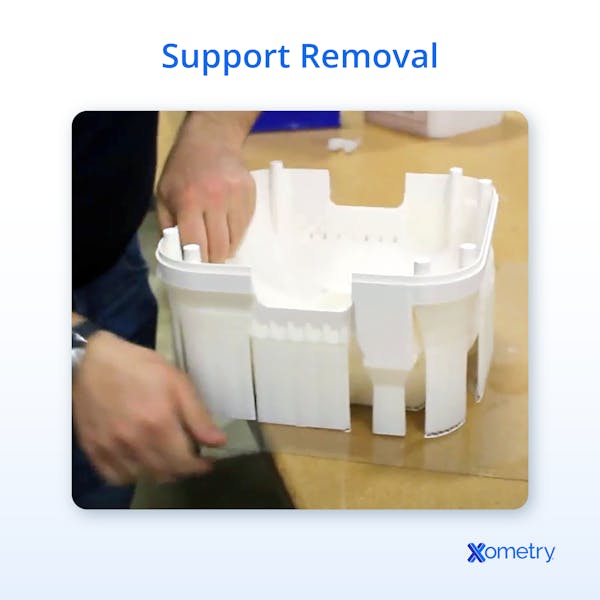
8. Layer Height
The slicer software will divide a part into multiple slices along its z-axis (vertical direction). The height of these slices is known as the layer height. A large layer height will result in faster prints since the machine does not have to print as many layers. However, this will be at the expense of dimensional resolution, which can manifest in a stepping effect. Small layer heights will take longer, but the part will have higher resolution and a reduced visible stepping effect.
9. Shell Thickness
The shell thickness of 3D printing slicer settings refers to the characteristics of the outer plastic shell that forms the wall of the 3D printed part. The shell thickness must be a multiple of the nozzle print width, i.e., a shell thickness of 0.8 mm with a 0.4 mm nozzle will mean the nozzle will extrude two lines (perimeters). The number of perimeters in the wall can be set to increase the part's strength with only a slight increase in print time. Shell thickness can have a significant effect on the strength of a part, even more so than infill percentage in some cases. In general, the more perimeters you print with, the stronger your part.
10. Bed Adhesion
A common challenge with 3D printing is bed adhesion. Parts will sometimes come loose from the print bed. This can cause the printer to extrude the material into empty air, since the part it was supposed to build on is no longer in the correct location, creating a tangled mess of plastic. Alternatively, if the part adheres to the nozzle, plastic will slowly accumulate around the nozzle and ultimately encase the entire extruder. Poor bed adhesion can also cause the first layer to warp, resulting in print failure. Bed adhesion can be improved in the slicer 3D printer settings by printing a “brim” or a “raft.”
A brim is a single layer that effectively expands the surface area of the first printed layer, creating a larger bonding area beyond the part’s footprint on the bed plate. A raft is similar to a brim, but actually prints directly under the part as well as beyond the footprint.
Printing with a brim has the advantage that you do not need to remove excess material from the bottom face of the part (merely from the bottom edges), whereas printing with a raft means that you need to do a little extra post processing to remove it from the entire bottom face of the part.
What is a 3D Printer Slicer?
A 3D printer slicer is a software package used to prepare a 3D model for 3D printing. It converts the model, typically in STL format, into a set of printer instructions in a machine-control language called G-code. G-code not only contains the toolpath information, but also contains other instructions such as temperatures, speeds, layer heights, fan cycles, and more.
Why Are 3D Printer Slicer Settings Important?
3D printer slicer settings are important because they ensure that a part is printed with the correct set of instructions for a specific material and part design. The settings also help ensure that every unique part is printed with the correct supports, infill, temperature, etc. Using the incorrect slicer settings can result in a failed print.
How Can I Change the Settings on my Slicer?
The exact method of changing a slicer’s settings depends on the software being used. However, most slicers will have a set of standard 3D printing settings for new users, as well as more advanced 3D printing slicer settings that can be modified by more experienced users.
How to Use a 3D Slicer
Slicer software can be used by downloading it from the supplier's website. Some slicers are free, while others need to be purchased. Once it is downloaded and installed, open the software and import the desired 3D model. The acceptable file formats will depend on the software you are using, but the most common format is STL (standard file format). Most CAD and design packages can export models as STLs.
How Does a 3D Printer Slicer Work?
A 3D printer slicer works by converting a 3D model into multiple 2D slices. The number of slices depends on the chosen layer height. These individual 2D slices are then converted into a set of instructions that can be understood by the 3D printer. These instructions are called G-code. They tell the machine where and how fast to move, and what temperatures are required, and give it information about other features to be printed, such as brims, supports, and outer shell thickness.
What Are the Best Slicers for 3D Printing?
There are many different slicer software packages available. The best of these are:
- Cura: This software was developed by Ultimaker, which has its own range of top-tier 3D printers. Cura is free and can be used with almost any FDM (Fused Deposition Modeling) 3D printer.
- Simplify3D: Simplify3D is a paid software that comes with a range of powerful printer settings and a simple user interface
- Prusa Slicer: This software was developed by Prusa, which supplies medium-cost, high-quality 3D printers. It is optimised for Prusa’s own machines but is compatible with most third-party FDM 3D printers.
- Netfabb: Netfabb is a professional software package developed by Autodesk. It is best suited for industrial 3D printing applications. Netfabb can be used for preparing files for almost any type of 3D printer technology.
- OrcaSlicer: OrcaSlicer is an open-sourced slicer forked from Bambu Studio, which itself is based on PrusaSlicer. It offers advanced features like pressure advance calibration, flow rate tuning, and multi-material support. OrcaSlicer is popular with both hobbyists and professional users.
Does the Slicer Affect Print Quality?
No, the brand of slicer software used will not directly affect the print quality. However, using the correct 3D printing slicer settings can be the difference between a failed print and a successful one, and some slicers have better options, which can provide superior results. However, most slicers will provide good baseline settings that can be tweaked for optimal results.
Summary
This article presented ten 3D printing slicer settings, explained what they are, and discussed how each one is important for 3D printing. To learn more about 3D printing slicer settings, contact a Xometry representative.
Xometry provides a wide range of manufacturing capabilities, including 3D printing and other value-added services for all of your prototyping and production needs. Visit our website to learn more or to request a free, no-obligation quote.
Disclaimer
The content appearing on this webpage is for informational purposes only. Xometry makes no representation or warranty of any kind, be it expressed or implied, as to the accuracy, completeness, or validity of the information. Any performance parameters, geometric tolerances, specific design features, quality and types of materials, or processes should not be inferred to represent what will be delivered by third-party suppliers or manufacturers through Xometry’s network. Buyers seeking quotes for parts are responsible for defining the specific requirements for those parts. Please refer to our terms and conditions for more information.
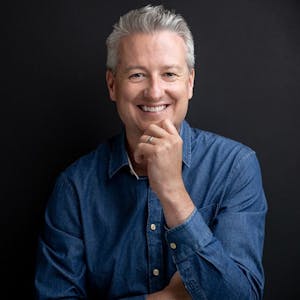