The Advantages of Additive Manufacturing
Because computer models and designs can be effortlessly transported electronically or even shared for download on the Internet, additive manufacturing allows businesses to quickly and cost effectively develop functional prototypes for product testing or even run a limited production line without having to worry about line limits and minimums while also allowing quick modifications when necessary.
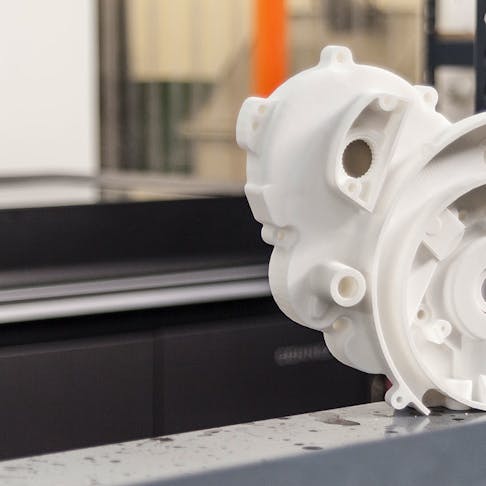
Additive manufacturing (AM), commonly known as 3D printing, is the process of creating objects by adding materials in layers. This method is opposite to subtractive manufacturing, which makes objects by cutting away at a solid block of material. AM can use various materials, including plastics, metals, biomaterials, and even edible materials. Its popularity has surged recently, driven by advancements in 3D printing techniques such as Fused Deposition Modeling (FDM), stereolithography (SLA), selective laser melting (SLM), material jetting, and others that expand its applications and capabilities.
AM has many advantages over traditional manufacturing methods. Because computer models and designs can be easily transferred electronically or shared via the Internet, AM enables businesses to rapidly and cost-effectively develop functional prototypes for product testing. Additionally, it supports limited production runs without concerns about traditional production line minimums or capacity limitations. This flexibility also allows for quick design adjustments, accommodating modifications as needed throughout the production process.
Top Benefits of Additive Manufacturing
The following article presents the top four benefits of additive manufacturing, focusing on recent technological advancements that are positioning it as a preferred manufacturing method for the future. These advantages illustrate the transformative potential of additive manufacturing today. As industries increasingly adopt this technology, the benefits—from complex design capabilities to accelerated production timelines—are reshaping the manufacturing landscape.
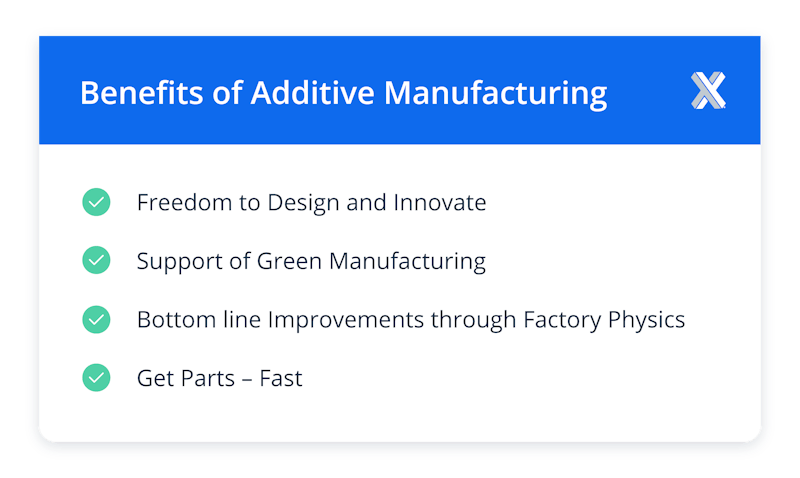
Freedom to Design and Innovate
One thing product engineers can rely on is the inevitability of modifications and redesigns, making adaptability a crucial aspect of engineering. AM supports this dynamic by enabling rapid iterations and bringing innovation and design to the forefront. More than simply creating physical parts, it empowers engineers with creative freedom in the production process, without incurring the time or cost penalties often associated with traditional manufacturing and machining. This flexibility is a major advantage of AM, providing opportunities for efficient and cost-effective design adjustments. This is especially true considering that over 60% of designs submitted for tooling and machining are modified while in production. That is a significant amount, and in traditional manufacturing, this quickly leads to substantial increases in cost and time delays. Additive manufacturing remedies this by moving away from conventional static designs while allowing engineers to try multiple iterations or versions simultaneously with minimal additional costs.
This freedom to design and innovate on the fly without penalties yields significant rewards: accelerated production timelines, enhanced product quality, a greater diversity of product designs, and ultimately, a higher volume of products. For businesses, this means the potential for increased revenue driven by streamlined production and faster time-to-market.
Support of Green Manufacturing
It is very clear that additive manufacturing streamlines traditional manufacturing and production methods significantly. This compressed process also means that there is a smaller environmental footprint. When considering the mining process of steel or the retooling process required in traditional manufacturing, it is easy to see why additive manufacturing is seen as a sustainable alternative.
While AM does require electricity, its energy consumption is typically lower than that of many traditional manufacturing methods for producing parts. Additionally, it minimizes waste by using only the necessary material for each part, and certain plastics used in AM processes are recyclable. Additive manufacturing is also highly effective for lightweight applications in vehicles and aircraft, which is critical for reducing fuel emissions. Components produced using additive manufacturing processes allow manufacturing engineers to build solid parts with a semi-hollow honeycomb interior. These parts maintain an excellent strength-to-weight ratio comparable to that of solid parts. The main difference, however, is that these components can be as much as 60% lighter than traditional, subtractive manufacturing methods, significantly lowering the fuel costs and environmental impact associated with the final product.
Bottom Line Improvements through Factory Physics
One of the most effective ways to improve a company’s bottom line is by reducing risk and increasing predictability. Through principles of factory physics, digital additive manufacturing technology transforms previously unpredictable production methods and makes them predictable by analyzing and balancing factory workloads. With online quoting engines such as Xometry.com and automated volume calculations from CAD software, engineers can receive real-time delivery dates.
Additionally, AM machines have defined volume capacities that can be tracked and monitored continuously, allowing for precise management and automation of factory loads. This makes pricing dynamic, responding instantly to factory physics metrics like load and capacity. It also provides engineers with a reliable method for controlling costs, reducing the risks of scheduling unpredictability and supply chain interruptions. 3D printers and other AM equipment can read CAD files to determine build times and material requirements, even before production begins. This allows the ability to plan capacity better, give customers accurate delivery dates, and schedule factory capacity by forecasting future needs without interruption.
Get Parts – Fast
At this point, on-demand parts availability is likely recognized as a critical advantage of AM—and rightly so, as immediate access to parts can facilitate a more agile product development and design process. This advantage reinforces the flexibility to iterate and redesign without traditional manufacturing constraints. Speed is critical at every stage in additive manufacturing—from quoting and production to shipping. This applies to end-use parts and components used as a bridge solution until traditional manufacturing can scale up.
Whatever the case, most end with additive manufacturing acting as the bridge between technologies. This is how we at Xometry are set up with our additive AND subtractive manufacturing services. For example, let’s assume that a supplier producing traditional parts for an automotive manufacturer falls through, a machine could be down for maintenance, or they have 100% machine utilization with no capacity to make the needed parts. Automotive manufacturers can turn to an additive manufacturing company such as Xometry to instantly produce the required thermoplastic pieces to keep the factory running. Without these parts-on-demand enabling continuous production, the factory would have been idle for weeks, costing the company thousands of dollars in revenue.
Another example of additive manufacturing's impact on government applications is its role in ensuring critical, life-saving equipment for armed forces is available on demand. When the production of military flashlights—essential for soldiers on patrol and during night missions—was temporarily halted for retooling, AM provided a crucial solution. By enabling rapid validation of the new flashlight design, AM allowed the assembly to proceed without waiting for traditional tooling processes to catch up. Without AM’s capacity for overnight design adjustments, the delay would have been at least 12 weeks—a significant wait time that could have affected mission readiness and safety.
Demand for rapid part production is projected to grow steadily, particularly as the industry gains familiarity with enabling technologies such as AM. Traditional manufacturing companies are already investing in expanding onsite additive manufacturing capabilities to meet demand more effectively. As adoption grows, additive manufacturing's potential to enhance efficiency and reduce lead times will continue to unfold, laying the groundwork for a shift toward digital-first, globally networked manufacturing facilities — companies like Xometry are at the forefront of this transformation, pioneering advancements in on-demand, digitally-driven production solutions.
