Lap shear testing is the typically applied method for assessment of the bond strength between two adhered, flat, and controlled contact area material samples. The test is conducted and the results are calculated in a highly repeatable manner, using specialist tensile test equipment and a rigorous setup.
Lap shear testing is used to ensure the quality and reliability of adhesive bonds in industries such as: aerospace, automotive, and construction. As a sample test method, it serves to validate consistency in performance and therefore highlight process or material variations that may have occurred.
This article will discuss what lap shear is, how it is conducted and calculated, and its applications.
What Does Lap Shear Mean?
The term lap shear refers to a specific class of mechanical tests used to quantify the shear strength performance of the adhesion or bonding between two material or substrate samples. In a lap shear test, two such samples of materials are bonded together by the application of an adhesive or bonding agent as per the manufacturer’s instructions to an overlapping region.
The test requires the application of a highly controlled tensile force parallel to the bonded interface, attempting to pull the two materials apart in a mode that is essentially pure shear. The lap shear strength is measured as the maximum force or stress the bond can withstand before the onset of failure is observed. Failure modes are variable in that they can be brittle, elastic followed by fracture, or progressive, depending on the adhesive/joint method, the nature of the substrates, and their relationship to the bonding agent.
This test is widely used in manufacturing, construction, and aerospace to evaluate the quality and reliability of adhesive bonds, as both a design validation exercise and as an in-production quality control/evaluation tool.
Why Is Lap Shear Testing Important?
Lap shear testing ensures the reliability and quality of adhesive bonds, helping to identify defects, process variations, or inconsistencies in the bonding procedure that could lead to failure in real-world applications. Lap shear testing assists engineers and manufacturers in the selection of the most apt adhesive and bonding process/methods for specific surfaces and applications, giving repeatable and clear assurance of optimized performance and therefore product safety.
Engineers use lap shear tests to validate the suitability of adhesive joint geometry as part of the design process, ensuring that bonded joints can reliably meet safety and performance requirements, especially in critical applications like aerospace and automotive. In general, an application-related factor of safety (FoS) will be applied, but for this to be valid, a reliable minimum performance must be established in real-world parts or a close analog. The tests aid in optimizing the adhesive application process, leading to better efficiency, cost-effectiveness, and consistency in manufacturing. Where process steps can be shown to add no benefit in ultimate bond strength, by repeated and thorough testing, they become redundant costs that can be eliminated. Lap shear testing provides key comparative knowledge in research and development, facilitating the study of bonding properties of new materials, preparation steps, and adhesive formulations. This allows secure and validated advancements in manufacturing processes, materials science, and product reliability outcomes.
How Is a Lap Shear Test Conducted?
A lap shear test evaluates the bonding strength between two materials or substrates. Here's a step-by-step guide on how to conduct a lap shear test:
- Prepare the surfaces following the manufacturer’s instructions for the adhesive being applied. This may include: cleaning, roughening, application of accelerators, or other specialist preparation stages for the bond surfaces of the samples.
- Adhere the two samples with an adhesive or bonding agent, with a specified overlap whose area is accurately known. The application and joint assembly processes depend heavily on the nature of the substrates and the manufacturer’s recommendations for application.
- Complete the curing process for the applied adhesive according to the manufacturer’s instructions. This may include a period, an elevated-temperature bake period, and/or a minimum compression force applied to the bond area.
- Secure one end of each sample into fixtures or grips attached to a testing machine. There are various forms of chuck or clamping used in different equipment like: screw clamps, 1D collet chucks, predefined bolt patterns, etc.
- Apply tensile force parallel to the bonded interface, pulling the two samples apart. In some cases, a predefined strain rate will be required and a smooth, jerk-free application of load is implicitly needed to avoid shock loading and consequently worsened performance in the coupling.
- Record data for consistency and interpretation between tests. Accurate and consistent methodologies are imperative in this.
To learn more, see our full guide on Shear Modulus.
What Materials Are Commonly Tested in Lap Shear?
Lap shear testing is widely performed on a broad spectrum of materials to assess the bonding strength of adhesive joints, including:
- Metals such as: steel, stainless steel, aluminum, and titanium.
- Plastics.
- Wood, leather, and natural fibers.
- Ceramics.
- Composites such as: carbon fiber, glass-reinforced polyester, and Kevlar® materials.
- Concrete and stonework.
What Does Lap Shear Measure?
Lap shear testing measures the critical performance characteristics of an adhesive bond between material substrates. It assesses the maximum force or stress that the adhesive bond can withstand before failure occurs. It provides a quantitative measure of the bonding strength and bond durability that allows comparison between alternative substrates and adhesive arrangements.
To learn more, see our full guide on Shear Stress.
What Are the Key Parameters in Lap Shear Testing?
In lap shear testing, a range of key parameters are essential for accurate and usefully interpretable results. These are:
- Bonded Area: Most critical parameter. It directly affects the stress distribution within the adhesive bond. A larger bonded area can distribute the load over a broader region, leading to higher lap shear strength.
- Sample Preparation: The quality of the bond surfaces, adhesive amount and application, curing conditions, and alignment of the samples all dramatically influence bond performance and test results.
- Loading or Strain Rate: A standard loading rate should be defined and maintained for consistency in testing and to allow comparability between alternative test samples.
- Temperature and Humidity: Environmental conditions can significantly impact adhesive bond strength, for some substrate materials and adhesives. This is essential when usage conditions must be simulated, such as when evaluating adhesives for outdoor or high-temperature applications.
- Sample Retainer Design: Proper grip alignment and secure attachment ensure accurate load application and prevent premature failure at the grip interface.
- Data Acquisition: Accurate data-collection systems and sensors are critical to measure the applied load and displacement accurately. Real-time and high-time-resolution data monitoring is essential for reliable results.
- Data Analysis: Without repeatable and effective analysis of the collected data, results will be impossible to interpret. Lap shear strength is the maximum load applied divided by the bonded area.
- Specimen Geometry: The dimensions and geometry of the test samples, including thickness, width, and length, should be defined and consistent to ensure repeatability. Wider bonding samples of the same area can have significantly different performances, and samples wider than the clamping fixtures must be avoided to prevent twist and distortion from invalidating the results.
How Is Lap Shear Strength Calculated?
Lap shear strength is calculated as the result of dividing the maximum load (stress) applied during the lap shear test by the bonded area.
Lap Shear Strength (MPa or psi) = Maximum Load (N or lbf)/Bonded Area (mm^2 or in^2)
The result is usually expressed in megapascals (MPa) or pounds per square inch (psi) and represents the maximum stress that the adhesive bond can withstand before failure. The actual value is liable to vary depending on factors like: adhesive type, substrate material, and test conditions.
This provides a quantitative measure of the adhesive bond's strength and is a crucial parameter for assessing the performance and reliability of adhesive joints in various applications.
What Factors Affect Lap Shear Strength?
A range of factors can affect lap shear strength in adhesive bonds, such as:
- Divergent adhesives have varying bonding strengths and characteristics, and their compatibility with the substrate will have a potentially high level of influence on lap shear strength.
- The condition of the substrate surfaces, including cleanliness, roughness, and any pretreatments applied, whether following the manufacturer's recommendations or not, can impact bonding strength.
- Proper adhesive application techniques and even distribution affect the bond's integrity. Excess application, insufficient adhesive, and non-uniform coating can all affect bond quality.
- The adhesive curing time, temperature, and humidity levels can influence bond strength. Some adhesives are very forgiving of poor control, while others are highly sensitive to cure regimes.
- The type of materials being bonded, their surface energy, and mechanical properties play a significant role. Low-energy surfaces such as polyethylene and polypropylene can, for example, be bond-enhanced by flame and plasma methods which greatly alter performance from being generically poor with all adhesives to potentially high strength.
- Parameters like: loading rate, atmospheric humidity, and test temperature can influence test results by altering adhesion properties and/or adhesive material properties.
- Exposure to environmental conditions, such as temperature, humidity, and UV radiation can affect bond strength over time. For effective lifetime performance evaluation, it's common to apply aging techniques in the form of HALT (highly accelerated life testing) methodology.
- Compatibility between the adhesive and substrate materials is crucial for achieving optimal lap shear strength. This can alter joint performance substantially.
When Is Lap Shear Used?
Lap shear testing is used in many industries and applications, whenever the assessment of adhesive bonds plays a role that demands validation. Some examples are:
- Assesses the bonding strength of adhesives used in aircraft components, such as: wings, fuselages, and interior structures. Bonding with advanced adhesives is increasingly a mainstay process for resilient, lightweight, and strong structures.
- Evaluates the reliability of adhesive bonds in automotive applications such as: car body panels and buffer pads, windshields, and even structural components in low-volume and race-vehicle manufacture.
- Tests the effectiveness of adhesives in applications like: curtain walls, cladding, and structural bonding in building construction.
- In manufacturing processes involving the bonding of materials, lap shear testing helps ensure product quality and reliability. Adhesives play an increasing role in manufacturing durable consumer, industrial, and medical products for automated assembly, low assembly height, and high strength.
- In the evaluation of adhesive bonds used in boat construction and repair, lap shear testing plays a central evaluation role. Adhesive jointing methods are widespread in the marine sector, offering low localization of stress in coupling composites which are susceptible to stress concentration and fracture.
- In material science and engineering, lap shear testing is used to study and compare adhesive properties for new applications, methodologies, and formulations.
What Are the Benefits of Lap Shear Testing?
The benefits of lap shear testing include:
- Ensures the reliability and quality of adhesive bonds, helping identify production and design defects or inconsistencies that could lead to failure in real-world scenarios.
- Helps engineers and manufacturers select the most appropriate adhesives, substrates, and bonding methodologies for specific applications, giving repeatable data to assure optimal performance and safety.
- Aids in optimizing the adhesive application process and assessing the efficacy of process alterations, leading to better manufacturing efficiency, cost-effectiveness, and consistency in manufacturing.
- Essential in research and development to study the bonding characteristics of new materials, assembly methods, joint geometry, and adhesive formulations, contributing to advancements in materials science and technology.
What Are the Challenges and Limitations of Lap Shear Testing?
Challenges and limitations of lap shear testing include:
- Adhesive manufacturer-compliant surface preparation and bonding techniques are crucial, and minor variations can significantly impact results. That does not preclude local modification to procedures that may improve results.
- Temperature and humidity conditions (both during production and during testing) can affect bond strength, requiring careful control of testing and production assessment protocols/sampling.
- Achieving uniform stress distribution across the bonded area can be challenging, impacting the accuracy of results. Any out-of-alignment or differential elasticity in the substrates as load is applied can twist/wrinkle the test, invalidating the results.
- Testing small or irregularly shaped samples is challenging, limiting applicability in certain scenarios.
- Assesses mode I fracture (I being the interfacial shear failure mode, normal to the bonded interface), whereas real-world adhesive joints may experience other failure modes.
- Results rarely correlate directly with field performance, necessitating additional testing and analysis for a comprehensive assessment. The guide they offer is comparative performance in a narrow operational mode, from which differential contexts must be surmised or extrapolated.
What Standard Does Lap Shear Testing Use?
Lap shear testing is conducted according to various international and industry-specific standards and test methods, depending on the materials, application, and industry involved.
- ASTM D1002: Standard test method for apparent shear strength of single-lap-joint adhesively bonded metal specimens by tension loading (ASTM International).
- ISO 4587: Adhesives—Determination of tensile lap-shear strength of rigid-to-rigid bonded assemblies (International Organization for Standardization).
- ASTM C1583: Standard test method for tensile strength of concrete surfaces and the bond strength or tensile strength of concrete repair and overlay materials by direct tension (ASTM International).
- ASTM D5868: Standard lap shear adhesion test for fiber-reinforced plastics (FRP) co-bonded to similar materials or metals.
- MIL-STD-401B: Test method standard for adhesive bond shear strength (United States Department of Defense).
To learn more, see our full guide on ASTM Standards.
What Device Is Used for Lap Shear Testing?
Lap shear testing is typically performed using a universal tensile testing machine. This device is equipped with specialized grips or fixtures designed for lap shear tests, which can often be exchanged for alternate grips to suit a range of test media.
The main structure that applies tensile or compressive forces to the test specimen is a highly rigid and vertically or horizontally mounted slide assembly that moves the grips on a single axis, with a force capacity suited to the application range of test specimens. Grips/clamps/fixtures hold and secure the samples, ensuring proper alignment and uniform loading along the bonded area. These are typically tension-engaged but must be designed to not create “notching” that might render the test sample weakened to the point that substrate failure easily occurs before bond failure.
A load cell sensor that measures the applied force accurately is usually integrated into the test apparatus. The crosshead is the moving part of the machine that draws one end of the sample to apply the force to the specimen. A data acquisition system/PC collects and records load and displacement data during the test for subsequent analysis.
Is the Lap Shear Test Used To Measure Adhesive Strength?
Yes, the lap shear test is commonly used to measure the adhesive strength of bonded joints. It uses a simplified and regularized test specimen to assess the ability of an adhesive to bond two substrates together and withstand tensile forces applied parallel to the bonded interface in a single mode of strain. This provides a simplified quantitative measure of the adhesive's bonding strength, to allow inter-sample comparisons to be made with a high degree of dependability.
Summary
This article presented lap shear tests, explained them, and discussed how they're conducted and their various applications. To learn more about lap shear tests, contact a Xometry representative.
Xometry provides a wide range of manufacturing capabilities and other value-added services for all of your prototyping and production needs. Visit our website to learn more or to request a free, no-obligation quote.
Copyright and Trademark Notice
- KEVLAR® is a trademark of E. I. DuPont de Nemours and Company
Disclaimer
The content appearing on this webpage is for informational purposes only. Xometry makes no representation or warranty of any kind, be it expressed or implied, as to the accuracy, completeness, or validity of the information. Any performance parameters, geometric tolerances, specific design features, quality and types of materials, or processes should not be inferred to represent what will be delivered by third-party suppliers or manufacturers through Xometry’s network. Buyers seeking quotes for parts are responsible for defining the specific requirements for those parts. Please refer to our terms and conditions for more information.
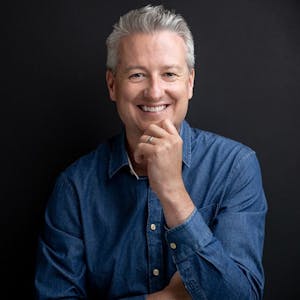