Shear stress is a concept in engineering and physics that measures how different materials react when force is applied to them in different ways. It’s also sometimes referred to as “tangential stress.” It’s an important one to know if you’re in manufacturing because it lets you know how exactly materials and even fluids will behave when you put them through different processes, and when they’re likely to reach their breaking or deformation point. We’ll explain it all below.
What is Shear Stress?
Shear stress measures exactly how much force a material can take before, quite simply, it’s had enough. The point at which a material’s innards start to slide or deform when force is applied parallel to its surface is its shear stress. You could also view it as the material’s level of resistance to stress. To break it down further, think of a material as having layers (on a microscopic level, many do). When “shear force” is applied, these layers are squished together and will eventually start to slide past each other in different directions, kind of like how a deck of cards would. The point where this sliding begins is the material’s shear stress.
So it goes without saying that knowing all about shear stress (and how to figure it out) is important when it comes to making things like buildings and bridges. It will give engineers all the information about exactly how strong and stable a material is, as well as how much load it can bear, so that structural components, like beams or columns, can hold their own against wind, earthquakes, and other potential forces. To make vehicles, aircraft, and spacecraft, parts need to be designed to withstand various forces, like wind, acceleration, and braking. In manufacturing, knowing the shear stress of a material will let you know if it can go through different processes, like drilling, cutting, or bending (all of which we can help you out with here at Xometry).
Most materials under too much shear stress will deform or warp, which will impact their functioning, stability, and reliability. Others, like ceramic, glass, and other brittle materials, are more prone to this type of failure, and are likely to crack and quickly break.
Shear stress is not just used for solid materials. When it comes to pipelines and hydraulic systems, knowing the shear stress of all sorts of liquids (like water or oils) and gases with different viscosities and flow patterns can help manufacturers design systems that won’t leak and won’t wear easily. Water from a river, for instance, will cause shear stress to the river bed, making it erode and change its landscape over time.
Those aren’t the only things impacted by shear stress. Most everyday actions we take will cause some level of shear stress. When using scissors to cut paper or fabric or a knife to cut various foods, the blades exert shear stress on the materials being sliced. When walking, our feet push against the ground, and driving a car will do the same to the road.
Shear Stress Formula
To give you the shear stress formula (it’s a pretty long one, and there are different formulas for different scenarios), we’ll first have to break down what all the symbols mean so you can start to make sense of it. The table below will explain exactly what all the symbols mean (we’ll put shear stress there again for easy reference).
Symbol | Meaning | Measured in |
---|---|---|
Symbol τ | Meaning Shear stress | Measured in Pa (pascals) or N/m² (newtons) |
Symbol F | Meaning Force (or “shear force”) applied parallel to the material’s surface | Measured in N (newtons) |
Symbol N | Meaning Number of forces (sometimes used for the “normal force”) | Measured in N (newtons) |
Symbol A | Meaning Cross-section of the material that the force is applied to | Measured in m² |
Symbol V | Meaning Internal force within the beam | Measured in N (newtons) |
Symbol Q | Meaning First (static) moment of an area | Measured in m³ or mm³ (can vary) |
Symbol t | Meaning Thickness of the particular area | Measured in m or mm |
Symbol I | Meaning The moment of inertia (the material’s resistance to deformation) | Measured in m⁴ or mm⁴ |
Symbol μ | Meaning dynamic viscosity of the fluid | Measured in Pa·s (pascal-seconds) or poise (P) |
Symbol du/dy (or ∂u/∂y) | Meaning Velocity gradient (u = parallel to the direction of flow, y = perpendicular distance) | Measured in 1/s (per second) |
Shear Stress Formula Breakdown
Now, let’s look at the different equations to use to find the shear stress of a material:
General shear stress: τ = F / A
Beam shear: τ = VQ/It
Fluids (liquids/gases): τ = μ (du/dy)
Shear Stress of Steel
The shear stress of steel can be different in each type of steel, as this will depend on its grade, composition, and what type of treatment it’s had. Here’s a helpful guide to the shear stress of some of the most common steel types.
Steel Type | Shear Strength (N/mm^2) |
---|---|
Steel Type Low-carbon HR steel | Shear Strength (N/mm^2) 345 |
Steel Type Low carbon C.R. sheet | Shear Strength (N/mm^2) 276 |
Steel Type ASTM A-36 | Shear Strength (N/mm^2) Depends on grade |
Steel Type 45-50 carbon HR sheet | Shear Strength (N/mm^2) 552 |
Steel Type Spring steel 1074, 1095 hardened to spring temper | Shear Strength (N/mm^2) 1,380 |
Steel Type COR-TEN Steel | Shear Strength (N/mm^2) 379 |
Shear Stress of Different Steel. Table Credit: https://unipunch.com/support/charts/material-specifications/
Shear Stress vs. Other Stresses
Shear stress is just one of the stress types that could make a material change, deform, or somehow react. For example, bending stress makes a material bend, while tension stress will cause the material to stretch. The diagram below shows how the different stress types could impact a material:
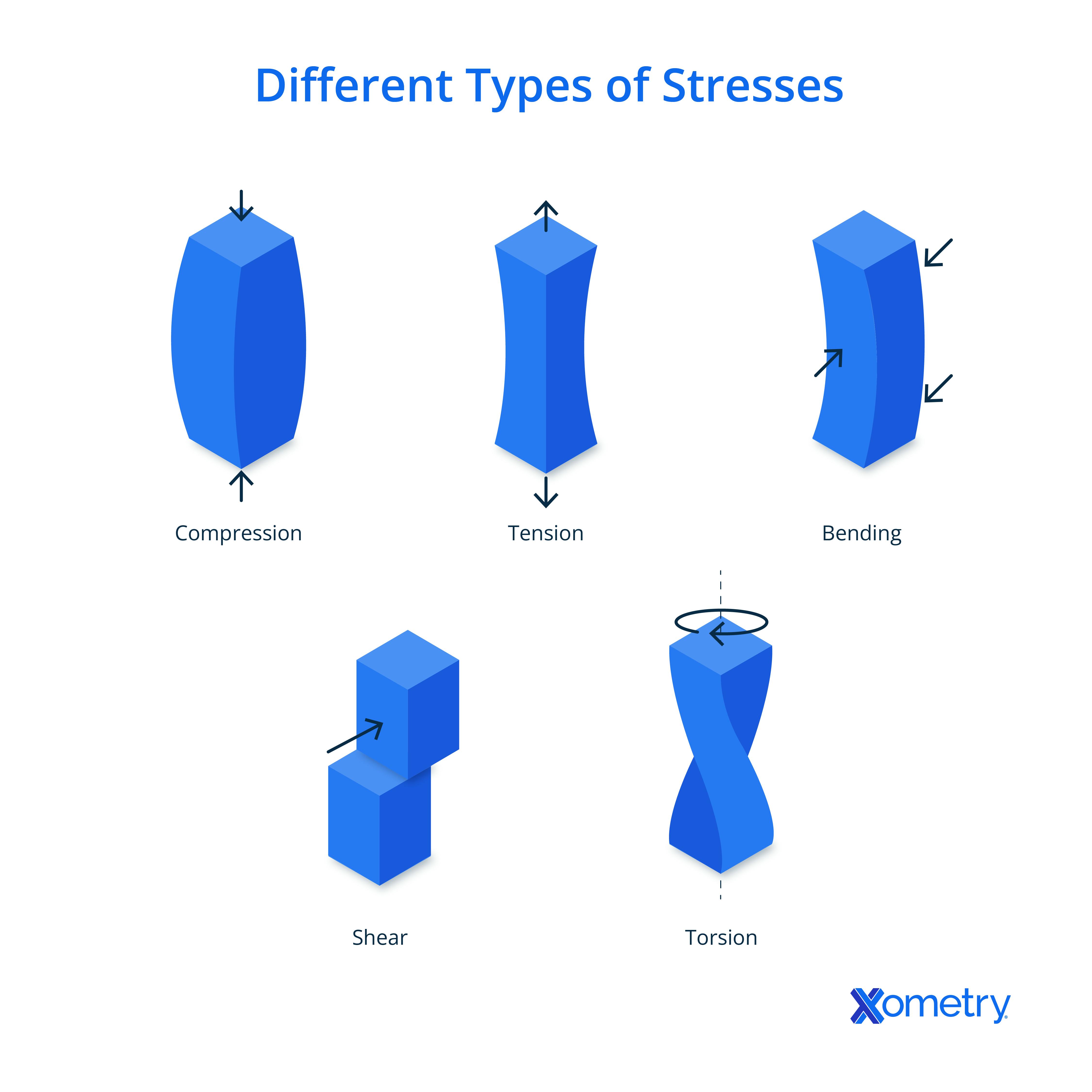
How Xometry Can Help
Whatever material you want to work with, Xometry provides a wide range of manufacturing capabilities and services for all your prototyping and production needs. We’ll even help you figure out the shear stress levels. Get your instant quote today on everything from 3D printing and CNC machining to sheet metal fabrication and metal stamping.
Disclaimer
The content appearing on this webpage is for informational purposes only. Xometry makes no representation or warranty of any kind, be it expressed or implied, as to the accuracy, completeness, or validity of the information. Any performance parameters, geometric tolerances, specific design features, quality and types of materials, or processes should not be inferred to represent what will be delivered by third-party suppliers or manufacturers through Xometry’s network. Buyers seeking quotes for parts are responsible for defining the specific requirements for those parts. Please refer to our terms and conditions for more information.
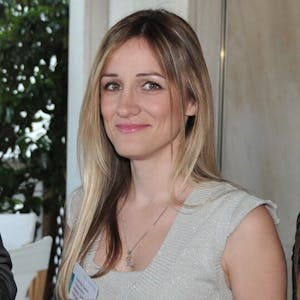