You are most likely familiar with the term “ceramics” but this class of material goes beyond pottery. In fact, ceramics are widely used to make components in the aerospace industry thanks to their many benefits. These include durability, strength, hardness, wear resistance, and electrical and thermal insulation. They also offer chemical stability.
Read on to find out more about exactly what ceramics are, the different types available, their properties, and how they’re being used in aerospace and 3D printing.
What Are Ceramics?
The term, “ceramic materials,” is a wide-ranging category largely defined by a lack of organic substances (those based around carbon-hydrogen bonds) and metallic elements. Absent those components, ceramics may be composed of: clay, minerals, oxides, and other compounds. Ceramics are basically what is left over after organic and metallic materials have been removed. Common ceramics are tiles, bricks, plates, glass, and toilets.
Ceramics are a refractory material, which means they are durable and able to withstand high temperatures. They also resist high pressures and most chemical compounds and are generally poor electrical conductors. Most ceramics are non-magnetic. Some ceramics shatter easily, while others are very tough.
There are two ceramic categories—traditional and modern. Traditional ceramics are things like pottery, and modern ceramics are a more advanced material category that are specially engineered to have specific properties. Many, for example, are meant to be hard and durable. Ceramics are typically shaped at moderate temperatures and then heated or “fired” at high temperatures to create hard, durable materials that resist heat, wear, and corrosion. The material is considered to be ceramic once it is no longer soluble in water even if heated.
It is important here to differentiate between water solubility and porosity. Some ceramics are still porous, meaning that they will still absorb water, but they are not water-soluble. Ceramics can be found in a wide variety of products and applications including tiles, bricks, engineering ceramics used in electronic devices, and aerospace components. We’ll talk a bit more about the two different ceramic types a little further down.
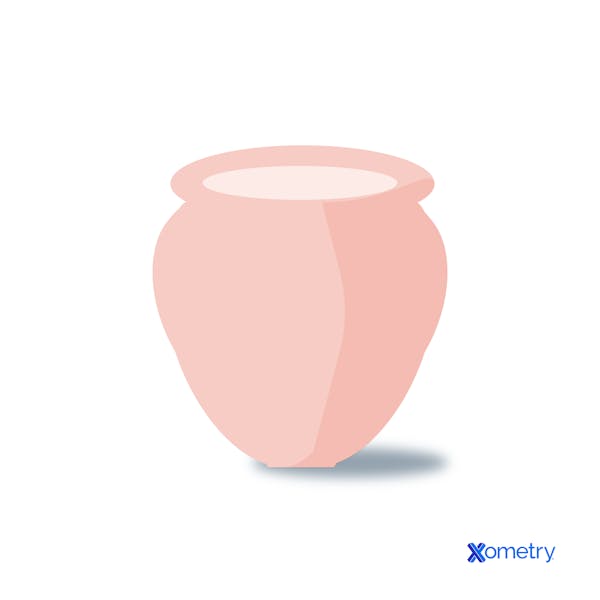
Ceramics are NOT the Same as Pottery
It’s easy to get the two confused, but the answer is no; ceramics are not the same as pottery. Although the terms are often used interchangeably, pottery is simply a subdivision of “ceramics”. The term “ceramics” is the rather broad umbrella term for many different materials and products made from non-metallic and inorganic substances, like bricks and cement.
Common ceramic pottery items include mugs, cups, vases, and bowls, or any type of functional container made of clay. You can also find ceramic sculptures and other artistic designs in pottery. Pottery is actually thought to be the oldest form of ceramics, which is likely why it is referred to as “traditional ceramics”.
Composition of Ceramics
Ceramics are made from many different substances and are usually a mix of clay, water, powders, and earthen elements. The materials and ratios vary depending on the ceramic product being made and what characteristics it’s supposed to have. For example, some are made from pure clay, while others could also include feldspar, silica, or other additives to enhance their properties.
In general, to make ceramics, the materials are combined, and then molded into the desired shape. They are then fired in a kiln or other special piece of equipment for completion. Advanced ceramics intended for specialized applications may be made from more exotic materials such as tungsten carbide, or zirconia.
Properties of Ceramics
The properties of ceramics, like those of any material, depend on the types of atoms involved, the bonds between them, and their arrangement. This is referred to as the atomic structure of a material and is what will determine its characteristics. Ceramic materials tend to be:
- Harder and more brittle than metals
- Wear-resistant
- Refractory
- Good thermal and electrical insulators
- Nonmagnetic
- Oxidation-resistant
- Chemically stable
Let’s consider the mechanical and chemical properties of ceramics in more detail below:
Mechanical Properties of Ceramics
The mechanical properties of ceramics include:
- Poor impact strength
- High compressive strength
- Extremely stiff and rigid structure with little or no yielding
- The presence of microcracks can cause local stress concentrations and brittle fracture
- Hardness and strength in compression, with a high softening temperature
- Poor thermal shock resistance
- Brittle nature
Shane Felton, a Manager, Solutions Engineering here at Xometry said, "There are many types of advanced ceramic materials available depending on the mechanical properties required for the part in question. First, pick the best manufacturing process and material grade for your application - typically, this will be either 3D Printing or CNC Machining. If you choose a material that needs to be machined, ensure that the material is readily available in the size required to make the part. If you choose a carbide material or another advanced ceramic, keep in mind that these materials are more difficult to machine than most materials, and EDM is commonly used. So, designing the part to be Wire EDM friendly can be key."
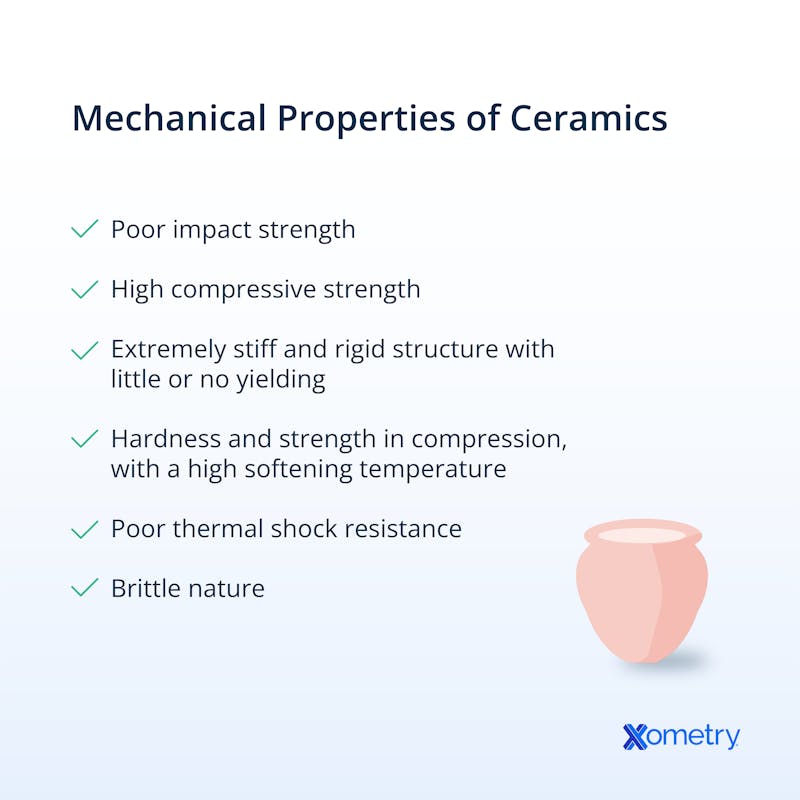
Figure 2: A list of ceramics' mechanical properties
Chemical Properties of Ceramics
Compared to most engineering materials, most ceramics are very chemically stable. They inherently resist chemical reactions and corrosion. Ceramics are also generally inert and do not react with acids or bases. Having said that, the chemical properties of ceramics can vary depending on their type and composition.
For instance, some may be prone to corrosion or degradation under certain conditions, while others can survive a chemical attack. There are also ceramics with unusual chemical properties such as the ability to conduct electricity or act as catalysts. The chemical behavior of ceramics can be summarized as follows:
- Mostly resistant to chemical attacks (i.e., by gasses, liquids, and even high-temperature melts)
- Generally inert and non-reactive with acids or bases.
Types of Ceramics
As briefly touched upon, ceramics tend to fall into two categories—traditional and advanced. Traditional ceramics are made from natural materials like feldspar, quartz, and clay, in a wet molding process. Each of these ceramics is known for its ability to serve specific purposes, such as permeability, magnetism, insulation, and conductivity. Their structure depends on the clay’s composition. This means that they’re not as perfectly structured as advanced ceramics which have a uniform microstructure. Traditional ceramics are mainly used in daily household items, such as jugs, vases, pots, planters, kitchen and tableware, as well as building materials.
Now advanced ceramics are a whole different ballgame as they are specially designed and engineered for high-performance use so they’re made to be hard-wearing, strong, extremely tough, and able to resist heat and chemicals. They’re usually made from a mix of high-purity synthetic powders like aluminum oxide, silicon carbide, and silicon nitride. To create the final product, the materials are processed using specialized techniques to give them their durable properties.
There are many different materials and ceramic types that fall under the traditional and advanced categories. We’ll discuss some of them below, referring to traditional ceramics as “pottery” while we compare them to advanced ceramics.
Advanced Ceramics
Some common types of advanced ceramics are listed below:
Silica
Silica, or SiO2, is renowned for its impressive thermal shock resistance and leachability. It is a popular choice for aerospace and energy applications for the production of investment casting shells and cores.
Tungsten Carbide
Tungsten carbide is known for its ability to maintain its properties at high temperatures. The material Tungsten carbide often gets mixed with high percentages of a metal binder, such as cobalt or nickel, which is used as a second metallic phase to form materials known as "cermets." Pure tungsten carbide can also be produced as an advanced technical ceramic using a high-temperature hot isostatic pressing process. Thanks to its hardness and wear resistance, this material is used to make products that need to be extra strong, like cutting tools, and abrasive water jet nozzles. However, its weight can limit its use in certain applications.
Fire Bricks
Fire bricks fall under the category of “refractory materials” meaning that they are resistant to both extremely high temperatures and chemical attacks, and won’t crack or break down when exposed to either. Their low thermal conductivity makes them naturally energy-efficient, which is why they are the preferred go-to for lining furnaces, fireboxes, fireplaces, and kilns, as well as other applications where resistance and durability is important. Fire bricks are most often made from a mixture of clay and other materials, and are used in lots of industrial applications, like steelmaking, glassmaking, and ceramics.
Bone China
Also known as fine china (the type you’ll find in a fancy restaurant), bone china is a porcelain variety famed for its strength, chip resistance, and translucency. It was first made in the 1800s by an English ceramicist, Josiah Spode. This type of ceramic is made from bone ash, kaolin, and feldspathic material. As it’s highly durable, bone china can be molded into thinner shapes than porcelain can. It goes through several changes during production, but the differences in the material properties give it its final transparent look. The final product is elegant which, combined with its durability, makes it a common material for fine dinnerware, ornaments, and other decorative objects.
Silicon Carbide (SiC)
Silicon carbide, made from silicon and carbon atoms, is another advanced ceramic material with high chemical- and wear resistance, as well as great thermal conductivity. These properties make it ideal for use in thermal processing applications and advanced ceramics, like cutting tools, abrasives, and semiconductor devices. The process of making silicon carbide (or SiC) involves heating a mixture of sand (silicon dioxide) and petroleum coke (carbon) at a very high temperature.
Titanium Carbide
Used for cutting tools, wear-resistant coatings, and other applications that require extreme strength and hardness, titanium carbide is a type of advanced ceramic composed of titanium and carbon atoms. It’s usually made by heating a mixture of titanium dioxide and carbon at high temperatures. Titanium carbide is known for having stable properties even at high temperatures and in harsh environments.
Glass Ceramics
Glass ceramics are composite materials made by mixing tiny crystals into glass. They’re made slightly differently than the other advanced ceramics on our list; glass is heated to a high temperature and then quickly cooled down, giving it a crystalline aesthetic. This unique combination of amorphous and crystalline states makes for customizable properties. Many varieties are especially known for their high strength, toughness, and resistance to thermal shock.
They were initially developed for the mirrors and mounts of astronomical telescopes. Glass ceramics have gained wider popularity, though, and are now found in everyday products such as cooktops, cookware, bakeware, and high-performance reflectors for digital projectors.
Pottery Ceramics
Pottery ceramics, otherwise referred to as traditional ceramics, can be divided into three categories—porcelain, stoneware, and earthenware.
Porcelain
Porcelain is made from a fine white clay called kaolin, which is known for its fine particle size and high plasticity. Typically white or translucent, porcelain is hard, strong, and durable. To make porcelain, the clay mixture has to be fired at high temperatures of around 1200 to 1450 °C, making the clay non-porous. Porcelain is often used for decorative or fine art objects and practical items such as dinnerware, electrical insulators, and dental implants.
Advanced Applications of Ceramics
Advanced ceramics are used in various industries for many different applications. Just some of them are:
- Aerospace: Many high-temperature aerospace components, including turbine blades, heat shields, and nose cones, are made using advanced ceramics. Until recently, conventional manufacturing has been used to shape these parts, but a much easier method is getting increasingly popular—3D printing.
- Biomedical: Ceramics show up in medical implants due to their biocompatibility, strength, and wear resistance.
- Electronics: Electronic devices receive ceramic components because of the material’s electrical insulation properties and ability to dissipate heat.
- Energy: Thanks to their thermal stability and heat resistance, ceramic materials are being used in various energy applications, such as fuel cells, solar panels, and thermal insulation.
Need Ceramic 3D Printing?
Other related technologies that use ceramic pastes or slurries include direct light printing (DLP) and lithography-based ceramic manufacturing (LCM) technology. A ceramic powder can also be used in material jetting printers, while solid ceramic filament can be used for LOM and FDM. Of these processes, stereolithography or related photopolymerization techniques are the most common because they can achieve smooth surface finishes. For more information, see our How Does 3D Printing Work guide.
Benefits of 3D Printed Ceramics vs. Metals
3D-printed ceramics are preferable to metals in several ways, including:
- High-Temperature Resistance: Unlike metals, ceramics can withstand high temperatures without melting, or losing their strength and shape.
- Lightweight: Making them perfect for use in aviation, ceramics are generally lighter than metals (per unit volume).
- Corrosion Resistance: Many metals have the tendency to oxidize quickly, but ceramics are highly resistant to corrosion.
For more information on the properties and uses of semimetals, you might want to read our What Are Metalloids guide.
Advantages of 3D Printed Ceramics vs. Plastics
3D printed ceramic parts are better than plastics in many ways. Here are just a few:
- Higher Temperature Resistance: Ceramics can withstand much higher temperatures than plastics. Even polyimides, which are considered to have the strongest resistance to heat among plastics, will start to melt around the 400°C mark. This pales in comparison to ceramics’ 1200°C to 2800°C.
- Greater Strength and Durability: Ceramics are, in general, much stronger and more durable than plastics.
- Better Chemical Resistance: Ceramics are less likely to react with chemicals than plastics are.
- Longer Lifespan: All the above factors combined make ceramic a more durable material, with a longer life than plastic.
Summary
We hope you enjoyed our article on the different types, properties, and benefits of both traditional and advanced ceramics, and how they’re used in industry—particularly in aerospace. To learn more about ceramics, please feel free to contact a Xometry representative.
Xometry provides a wide range of manufacturing capabilities and other value-added services for all of your prototyping and production needs. Visit our website to learn more or to request a free, no-obligation quote.
Disclaimer
The content appearing on this webpage is for informational purposes only. Xometry makes no representation or warranty of any kind, be it expressed or implied, as to the accuracy, completeness, or validity of the information. Any performance parameters, geometric tolerances, specific design features, quality and types of materials, or processes should not be inferred to represent what will be delivered by third-party suppliers or manufacturers through Xometry’s network. Buyers seeking quotes for parts are responsible for defining the specific requirements for those parts. Please refer to our terms and conditions for more information.
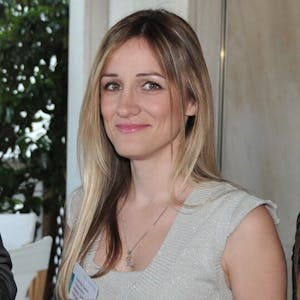