Among the concepts out there that are important to successful engineering, bending stress is right up there. Without understanding bending stress, we wouldn’t be able to design safe buildings in industrial settings or pick the best materials for other structures, like bridges and airplanes. We’ll take a look at exactly what bending stress is, why it happens, and how to calculate it.
What is Bending Stress?
Bending stress is another word for flexural stress and it happens when you subject a material to a bending load or force — leading it to bow, bend, or flex. It’s different from strain, which is the actual deformation or change that comes from the force being applied.
The stress component comes from the internal resistance going on when a beam, arch, or other structural part’s cross-section begins to deform under the stress and tries to counteract it. While the whole structure might have some bending stress, that doesn’t mean each part of it experiences it equally. Depending on how it’s designed, where its neutral access is, and where the force is coming from, the stress will be distributed in different ways.
Knowing where bending stress happens and how it impacts specific metals, alloys, or composites can be the difference between making a well-built bridge or building and one that can’t hold intended loads. It’s also something engineers should think about when determining the lifespan of these structures and understanding the behavior of how a material will move and bend before reaching a point that jeopardizes the safety and integrity of a part.
When a force or load is placed on an object (like a beam, for instance), the bending force will begin to take place, causing the material to flex or bend. This leads to a combo of stresses that are called bending stress. This usually consists of tensile stress and compressive stress, which will impact specific parts of the object, and the neutral axis will also move as the force applied moves. A visualization of bending stress compared to other types of stresses is shown below:
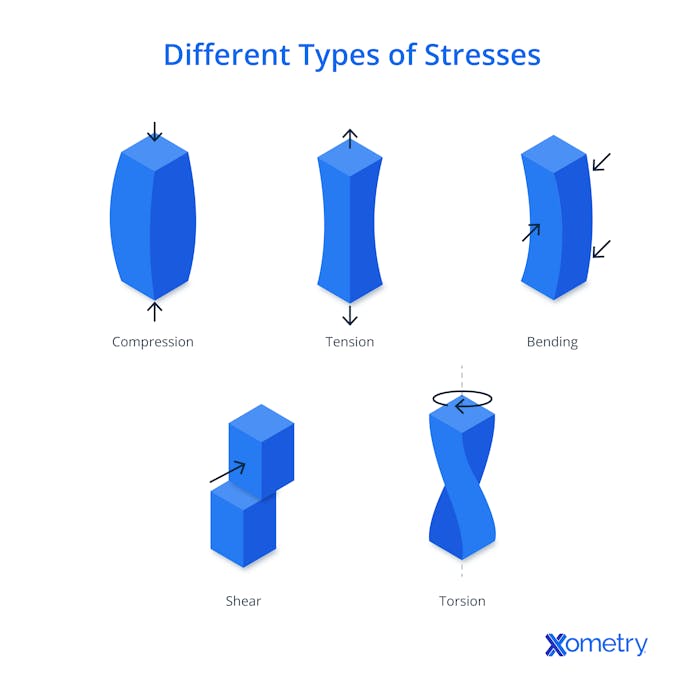
Types of Bending Stress
Bending stress is actually a catch-all term for a few different types that are worth familiarizing yourself with so you can better understand what a beam is undergoing:
1. Pure Bending
In this form of bending stress, an object will only experience a bending moment from the force that’s being applied, as opposed to having other stresses and forces working on it, too — such as shear stress, axial stress, or torsional force. The right conditions will need to be in place for pure bending and shear stress should be equal to zero, so while it might not be the most realistic scenario, it gives engineers a good idea of how a material will respond to this stress alone.
2. Symmetric Bending
This happens when the cross-section of the beam and the neutral access are symmetrical. Therefore, the force or stress is applied evenly and results in symmetric bending, which is another idealized situation like pure bending, which may not always match up with the environment this beam or structure would actually exist in.
3. Unsymmetric Bending
Logically, with how symmetric bending works, you’ll find that unsymmetric bending happens when the cross-section and beam aren’t symmetrical. Stress is then distributed more unevenly leading to this style of bending stress.
4. Non-Uniform Bending
When you’re thinking of day-to-day scenarios that feature slightly less perfect conditions, non-uniform bending will come up. This type of bending stress happens when forces or loads are unevenly applied and shear stress is present, too. This tends to be the most realistic because bridges and structures existing in everyday life will have far more forces, stresses, and tensions working on them.
How to Calculate Bending Stress
Here is the formula you should know in order to calculate bending stress:
M/I = σ/y = E/R
Or you can write it like this:
σ = My/I = Ey/R
Here is what the following letters and symbols mean within this formula:
- σ is bending stress (Pa or N/m²)
- M = Bending moment applied to the object (Nᐧm)
- y = the perpendicular distance between the neutral axis and a specific point on the object’s cross-section
- I = the area moment of inertia of the object (m⁴)
- E = modulus of elasticity or Young’s modulus (Pa or N/m²)
- R = radius of curvature (m)
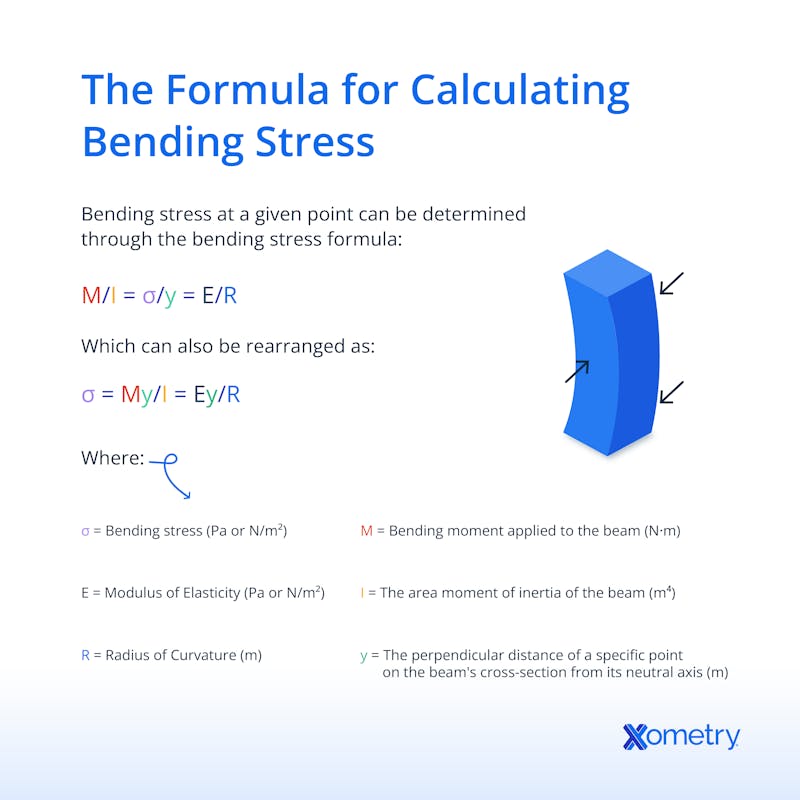
Bending Stress Examples
Bending stress is present in all kinds of everyday objects and structures, a few of which we list out below.
- Bridges: With a large mix of pedestrians, pets, cyclists, cars, trucks, and passengers going across bridges, it’s fair to say this is one of the most obvious and clear examples of bending stress and what beams and structures undergo when they’re put to work.
- Airplane wings: Planes are another great example of bending stress in action, particularly when applied to their wings. With gravity and aerodynamic forces working against the wings, bending stress is an important factor to consider when designing them so they can move successfully, especially while these forces are at play.
- Buildings and architectural structures: The beams and columns that makeup skyscrapers, office buildings, and homes have to account for bending stress, too, so engineers can understand how much force and how heavy of a load they can manage.
How Xometry Can Help
Xometry provides dozens of different materials across a wide range of manufacturing capabilities that are important to the engineering, medical, and scientific fields, including compression molding, medical CNC, 3D printing, rapid prototyping, and laser cutting. Get started by uploading your 3D CAD to get an instant quote for various manufacturing options today!
Disclaimer
The content appearing on this webpage is for informational purposes only. Xometry makes no representation or warranty of any kind, be it expressed or implied, as to the accuracy, completeness, or validity of the information. Any performance parameters, geometric tolerances, specific design features, quality and types of materials, or processes should not be inferred to represent what will be delivered by third-party suppliers or manufacturers through Xometry’s network. Buyers seeking quotes for parts are responsible for defining the specific requirements for those parts. Please refer to our terms and conditions for more information.
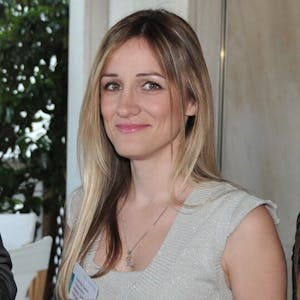