Whether you’re fresh out of college or it’s been some time since you’ve taken math classes, it’s always helpful to review equations that frequently show face in the work that you do. One example of this that we’d like to cover in our engineering fundamental series is Young’s modulus, which we’ll define below and then break down how to calculate it.
Young’s Modulus — A Quick Refresher
Young’s modulus points to the slope of a stress strain curve and can help show when a material is simply stretching and holding up okay under stress versus when it’s bound to deform or break. It’s an essential insight into the behavior of a material, and can help determine which materials are best to use based on this number and other factors.
While it’s a common equation found in engineering, you’ll also find it in medical, scientific, and aerospace settings, as knowing this can be the difference between broken parts, implants, and surfaces and ones that stay together. Sometimes you’ll hear team members or fellow coworkers call Young’s modulus the modulus of elasticity.
As you can see in this image, this style of graph can help show Young’s modulus, the ultimate strength point of a material, and at what point you can expect deformation or breakage to occur.
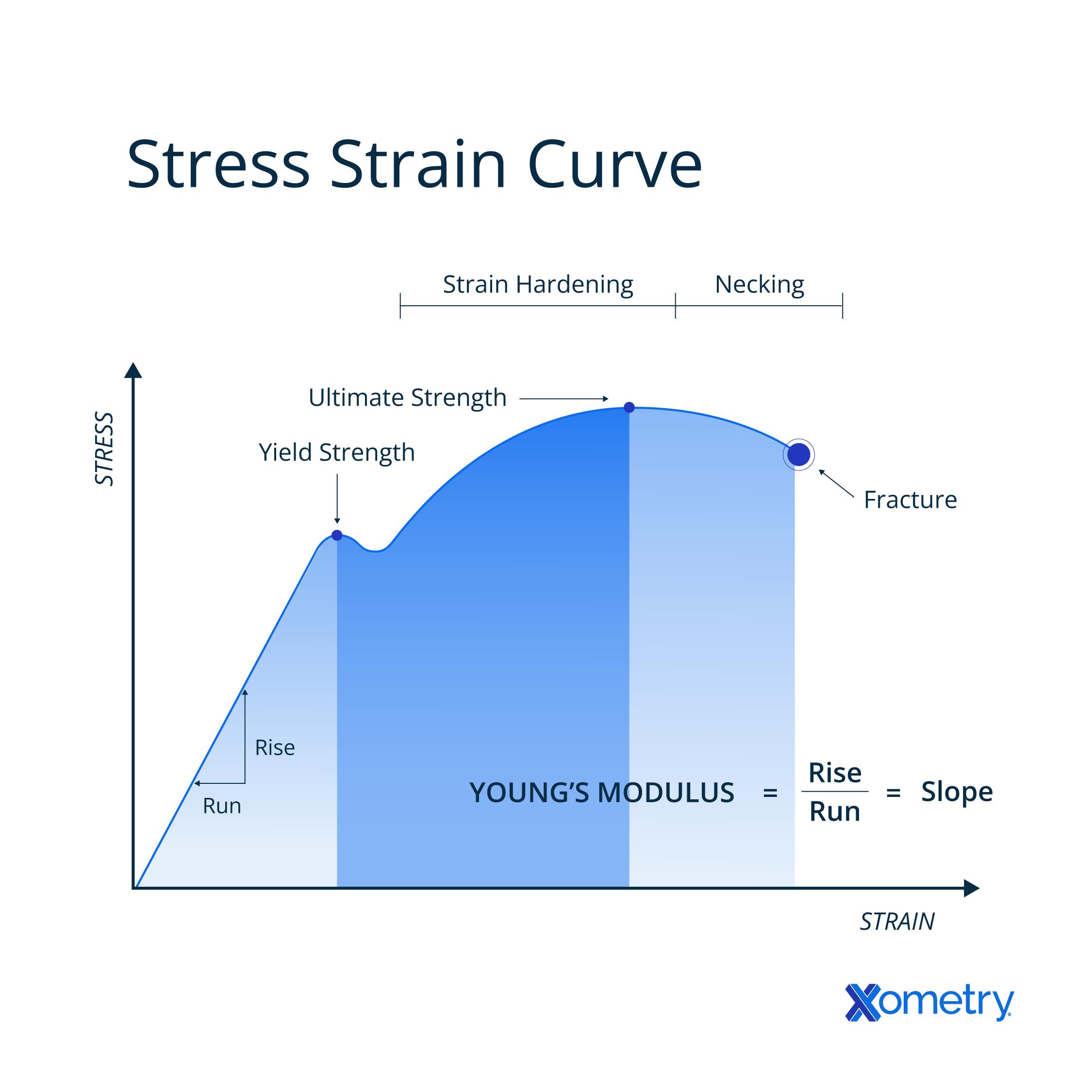
Steps to Calculate Young’s Modulus
To calculate Young’s modulus of elasticity, follow these steps:
1. Measure the Original Length of Your Material with a Micrometer
Use a micrometer to measure the original length (L0) of the material you’re working with, but do this before any force is applied or stretching occurs so that you can get the most accurate answer.
2. Use the Micrometer to Measure the Cross-Sectional Area and Other Diameters
Measure the width and height of your material, then measure out any other diameters it has and note those down. Doing so will help you clock any irregularities and get the most accurate number for the cross-sectional area, which you’ll need to calculate Young’s modulus.
3. Get Slotted Masses Into Place and Apply Force to the Material
Set up several slotted masses and attach them to your material. These will help you better control the tension and deformation process.
4. Use a Vernier Scale to Measure the Different Lengths
Once you start applying force and tension with the slotted masses, you can measure the various lengths of your material as it extends with a vernier scale.
5. Graph Your Measurements
Using a graphing calculator or a computer, create a graph using your measurements so you have a visual representation of your experimental data and can accurately show the important points on the graph.
6. Calculate Young’s Modulus
Now that you have all the necessary information, you can complete the calculation to find your material’s stiffness and elasticity. You’ll get it by dividing the tensile stress by the tensile strain and then adding in other important information, which you’ll see examples of below.
Use this equation to do find Young’s modulus: E = Tensile Stress / Tensile Strain = (FL) / (A * Change in L)
7. Analyze Your Graph and Note the Most Important Points
Once you have the graph and equation calculated, double-check your graph and ensure that you can see the clear linear region where elastic behavior for your specific material is shown. If a material has already been stretched and deformed, it’s not likely that you’ll be able to correctly and accurately complete this equation.
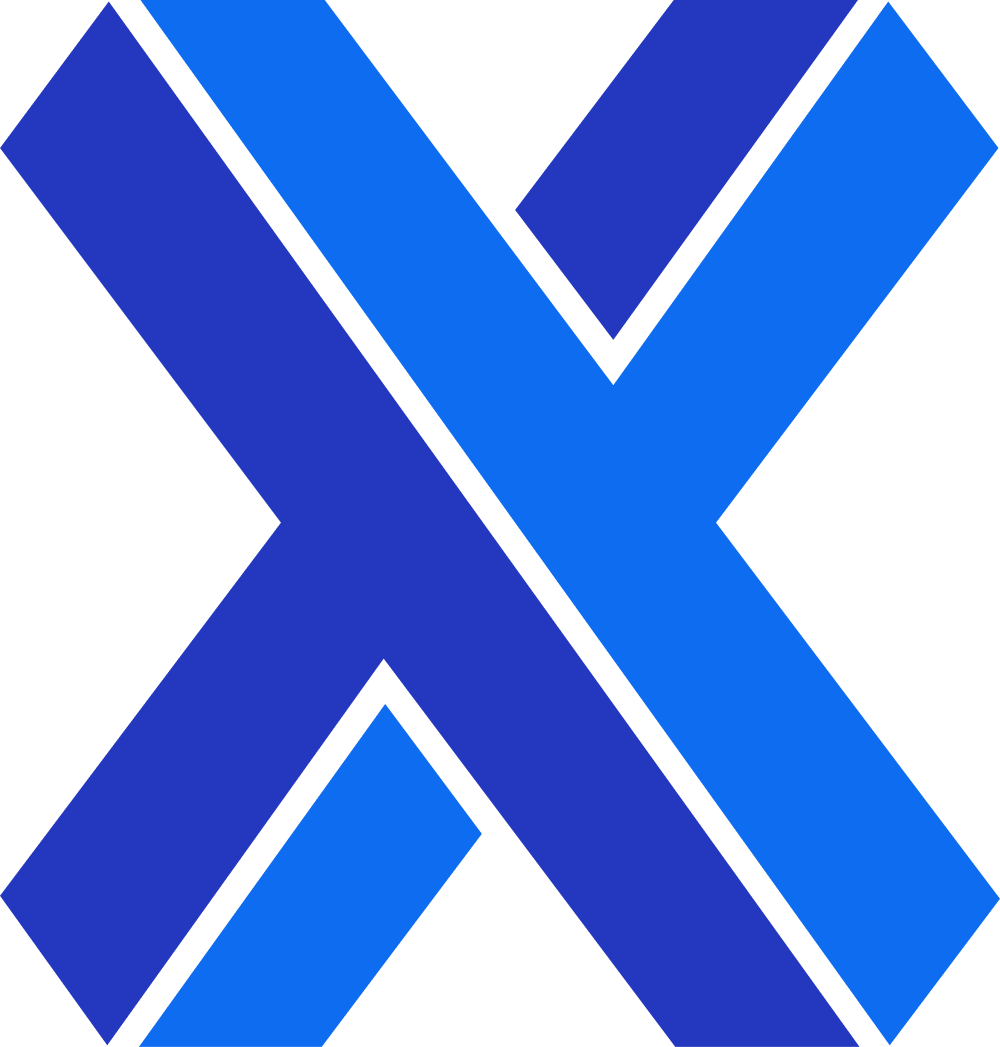
Example Calculations with Different Materials
To really help this concept stick, take a look at the following calculations that find the elasticity modulus of different materials:
1. Steel
In this example, we’ll look at a steel rod and find Young’s modulus for it. Consider the equation if the following factors are true:
- The rod has an original length (L0) of 2 meters
- It has a final length (Ln) of 2.04 meters
- The cross-sectional area (A) is 1 square centimeter (0.0001 square meters)
- To get the elongation you’ll subtract L0 from Ln (which will be 4 cm in this case)
- The force (F) applied is 1,000 Newtons (N)
Here’s how you would calculate this:
Equation: Young’s modulus = (F x L0) / (A x (Ln - L0))
With numbers inputted: Young’s modulus = (1,000 N x 2 m) / (0.0001 m2 x 0.04 m)
Answer: Young’s modulus ≈ 5 x 108 Pascal (Pa)
2. Aluminum
If you’d like to calculate the same equation but with an aluminum rod, here’s how to do so using sample numbers and with less force:
- The rod has an original length (L0) of 2 meters
- It has a final length (Ln) of 2.04 meters
- The cross sectional area (A) is 1 square centimeter (0.0001 square meters)
- To get the elongation you’ll subtract L0 from Ln (which will be 4 cm)
- The force (F) applied is 800 Newtons (N)
Here’s how you would calculate this:
Equation: Young’s modulus = (F x L0) / (A x (Ln - L0))
With numbers inputted: Young’s modulus = (800 N x 2 m) / (0.0001 m2 x 0.04 m)
Answer: Young’s modulus ≈ 4 x 108 Pascal (Pa)
3. Rubber
Here is how this calculation could be determined if we use a rubber band and possible measurements for this type of material:
- The rubber band has an L0 of 10 centimeters
- It has an Ln of 15 centimeters
- The cross-sectional area (A) is 1 square centimeter (0.0001 square meters)
- The elongation is 5 centimeters (Ln-L0)
- The force applied is 20 Newtons
Here’s how you would calculate this:
Equation: Young’s modulus = (F x L0) / (A x (Ln - L0))
With numbers inputted: Young’s modulus = (20 N x 0.1 m) / (0.0001 m2 x 0.05 m)
Answer: Young’s modulus ≈ 4 x 105 Pascal (Pa)
When you compare all of these different materials, you’ll notice that the Young’s moduli for rubber is a much lower magnitude than steel and aluminum, meaning that the former material is more flexible and elastic, whereas the latter materials are stiffer.
Why It’s Useful to Calculate Young’s Modulus
Engineers use this equation in real-world scenarios for several reasons:
- Understanding materials: Knowing the Young’s modulus for a certain material will help you get to know it better and help predict what environments and situations it can be put through with success.
- Design considerations: When a structure is relying on a specific material or a human needs a particular implant, calculating Young’s modulus will help determine which materials to use, as you’ll have a better understanding of which ones can withstand the stresses.
- Stress calculation: You’ll need to know Young’s modulus in order to calculate the stress in a material — another vital factor in engineering and design.
- Predicting material failure: With the modulus of elasticity, you can have a much better and more accurate prediction of the point at which a material will break or deform for good under pressure.
How Xometry Can Help
Xometry provides dozens of different materials across a wide range of manufacturing capabilities that are important to the engineering, medical, and scientific fields, including compression molding, medical CNC, 3D printing, rapid prototyping, and laser cutting. Get started by uploading your 3D CAD to get an instant quote for various manufacturing options today!
Disclaimer
The content appearing on this webpage is for informational purposes only. Xometry makes no representation or warranty of any kind, be it expressed or implied, as to the accuracy, completeness, or validity of the information. Any performance parameters, geometric tolerances, specific design features, quality and types of materials, or processes should not be inferred to represent what will be delivered by third-party suppliers or manufacturers through Xometry’s network. Buyers seeking quotes for parts are responsible for defining the specific requirements for those parts. Please refer to our terms and conditions for more information.
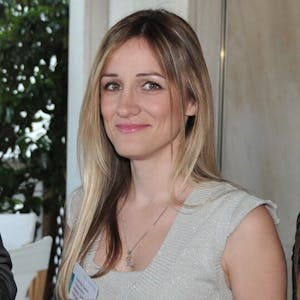