A Bowden extruder is a 3D printer material feed mechanism that pushes filament into the hot end through a long tube. The long tube connects the extruder motor to the extruder’s hot end. The feed mechanism that supplies material to the extruder can thus be mounted to the 3D printer’s frame, separately from the motion-controlled hot end. This setup reduces the moving mass of the print head, which allows for either higher accelerations or lower-motor powers. Various filament materials are compatible with Bowden extruders, including PLA, ABS, PETG, and nylon.
This article will discuss what a Bowden extruder is, including its uses, how it works, and the materials used.
What Is a Bowden Extruder?
A Bowden extruder is a filament feeding mechanism used in many fused filament fabrication 3D printers. The filament gets fed into the hot end via a flexible PTFE tube. Although the term "Bowden" originates from mechanical control cables, a Bowden extruder in 3D printing specifically refers to a system where the filament is pushed through a PTFE tube. This design allows the force component (the extruder motor) to be mounted separately from the hot end. The filament feed motor is attached to the machine chassis rather than the print head, so it doesn’t add weight to the print head itself. As such, the head can make faster and more precise movements.
How Does a Bowden Extruder Work?
The drive mechanisms vary, using either a gear or pinch wheel to convert the rotation of the feed or drive motor into a linear progression of the filament. As the filament is pushed through the feed mechanism, it is delivered under compression into the Bowden tube. That pressure is countered by the resistance at the hot end, where it is melted and dispensed.
The Bowden tube guides the filament while minimizing buckling. The filament feeds through since the tube is longitudinally rigid. Although the tube provides lateral support, flexible filaments may still experience buckling due to insufficient constraint. The filament feeds through since the tube is longitudinally rigid. It is normal for the filament to want to curve because of the compressive force applied to it. This causes the filament to press against the inside of the tube, causing extra friction.
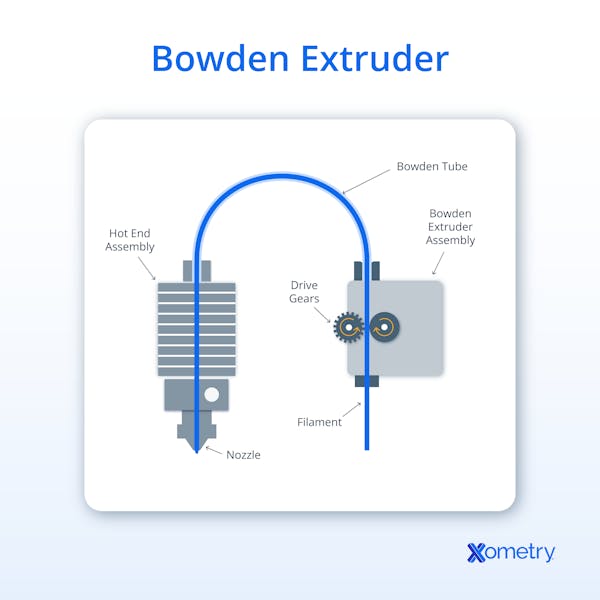
Why Are Bowden Extruders Used?
Bowden extruders separate the relatively heavy feed motor and gear mechanism from the moving nozzle and hot end assembly. It reduces the weight of the moving components and improves the inertial response of the print head. This also keeps the heat of the hot end away from the extruder motor.
What Are the Different Materials That Are Compatible With a Bowden Extruder?
Listed below are filament materials that are compatible with Bowden extruders:
1. ABS
ABS filaments are known for their tendency to warp and shrink if they cool too quickly. The long filament path exacerbates issues with filament retraction and pressure fluctuations, resulting in oozing, stringing, and poor flow consistency. ABS filaments benefit greatly from precise temperatures. However, the Bowden setup may introduce slight delays in extrusion response, which can require fine-tuning of retraction settings and print speeds to achieve consistent results.
2. PLA
PLA filaments generally work well with Bowden extruders because they are relatively rigid and have low shrinkage and warping compared to materials like ABS or Nylon. The longer filament path may still demand tweaks such as increased retraction distances to compensate for compression and prevent stringing and oozing. On balance, PLA's lower printing temperature and relatively low sensitivity to temperature fluctuations make it better suited for this configuration than other, less forgiving filament materials. PLA filaments are less prone to warping if the temperature is consistently controlled.
To learn more, see our full guide on PLA Filaments.
3. Nylon
Nylon filaments can produce good results with Bowden extruders. However, the material can create some problems. Nylon filaments in the Bowden setup experience increased friction when the tube path is long. Friction forces may deform the filament and make retractions more difficult. Nylon filaments also demand precision in temperature control so they don’t warp. This can be hard to achieve because of the delayed extrusion response and retraction in Bowden systems. Users must experiment with retraction distance, print speed, and extruder temperature to achieve satisfactory results. Nylon filaments perform best with steady and reliable temperature control that minimizes warping and enhances interlayer adhesion.
4. PETG
Polyethylene terephthalate glycol (PETG) filaments can be used in Bowden extruder setups. However, there are property and parameter considerations that can improve performance. PETG is moderately flexible compared to PLA but remains rigid enough to work well in Bowden systems. This results in a lower tendency to curl and warp in the tube when pushed by the extruder motor. Still, the longer the Bowden tube, the more friction and elastic compression the filament will experience. These factors can make retraction tuning more challenging, increasing the risk of stringing and oozing. PETG filaments benefit somewhat from consistent temperature control, though the print quality doesn’t vary as much as in some other materials.
To learn more, see our full guide on PETG Filaments.
5. Flexible Materials
In general, flexible filaments are harder to use in Bowden extruders. They tend to curl, leading to friction and compression in the tube. The elasticity makes delivery uneven and retraction less precise. The uneven flow also affects temperature uniformity, which can hamper adhesion within and between layers.
7. Composite Filaments
Composite filaments (those that contain additives like carbon fiber, wood, or metal particles) typically present considerable challenges when used with Bowden setups. They have increased friction due to frequent contact with the Bowden tube, which can hinder smooth extrusion. Additive-laden filaments tend to have higher friction coefficients than pure ones. This results in filament deformation or jamming, particularly when abrasive additives are involved. This can lead to inconsistent extrusion, including under-extrusion or intermittent flow. Additives such as wood or metal particles present a higher risk of clogging than others. Additionally, carbon fiber and metal-filled filaments are highly abrasive and can wear down standard PTFE Bowden tubes over time, necessitating the use of reinforced tubing or alternative extrusion systems (such as direct drive).
Composite filaments typically need consistent temperature control to ensure proper adhesion, as the additives can reduce the material's flow consistency and bonding strength. Smoother filament flow and more precise control will generally improve temperature stability, making for better-bonded prints.
What Is the Primary Function of a Bowden Extruder in the Context of 3D Printing?
All 3D printing filament extruders serve the same general purpose: they feed filament to the object being printed in a controlled manner and at the proper temperature for adhesion. Bowden extruders do so by pushing the filament through a tube that runs from the fixed extruder to the moving print head. This keeps the heavy extruder mechanism off the mobile head but can introduce more friction and elastic deformation to the feed process.
How Does the Bowden Extruder Contribute to the Overall 3D Printing Process?
The Bowden extruder improves printing performance in some ways but also has a few drawbacks. They are commonly used with rigid filaments such as PLA, ABS, and PETG, while flexible filaments like TPU or TPE can be more challenging due to increased friction and compression inside the Bowden tube. The system can improve the guidance and control of the movement of filament from the spool to the hot end when optimized and maintained in good functioning condition. In a remote Bowden setup, the extruder motor is stationary and mounted away from the hot end, reducing the weight of the print head. This can enable faster movements with greater precision, resulting in improved print quality.
Does the Choice of Filament Impact the Effectiveness of a Bowden Extruder?
Yes, the nature of the filament can influence Bowden extruder functionality. Each of the many 3D print material options on the market exhibits different compatibility with a Bowden setup.
Flexible filaments like TPU or TPE (thermoplastic elastomer) typically require very careful adjustments and monitoring to prevent buckling or deformation in the filament path. Filaments that contain abrasive or high-friction additives like carbon fiber or metal particles can wear down the Bowden tube over time, leading to steadily increasing friction and irregular feed rates. PTFE-lined tubes can help reduce wear but may degrade with prolonged use at high temperatures.
Inconsistent filament diameter can cause extrusion issues, leading to under-extrusion or clogging. ABS, PETG, and others require more precise and narrow temperature control to create smooth, well-bonded parts. The Bowden extruder does not directly control filament temperature, but proper temperature regulation in the hot end is crucial for successful printing. This can be challenging since the feed path varies, and elastic effects influence extrusion speed.
Bowden extruders work well with a wide range of filament materials. However, you may need to experiment with settings or even modify the mechanism to optimize its performance.
What Are the Advantages of a Bowden Extruder?
The advantages of Bowden extruders are:
- Removing the weight of the extruder from the printer head can allow higher accelerations in the transport mechanism.
- Hot print materials are more thermally isolated from the print head, reducing heat creep.
- Lower print head height allows some printers to build taller parts.
What Are the Disadvantages of Bowden Extruder?
While the Bowden extruder does offer advantages, it has its downsides and scenarios for which it is ill-adapted. These drawbacks include:
- Bowden extruders can struggle with flexible filaments because the long path introduces extra friction. Careful setup and good maintenance can partially mitigate this.
- Since the feed is initiated far from the hot end, there can be a delay in filament response time due to elasticity in the feed, leading to less precise extrusion control.
- Retraction can be challenging to control reliably due to friction and elasticity in the filament.
- Loading and unloading filament can be more cumbersome compared to direct drive setups.
- Bowden extruders typically experience more wear and friction than other types, especially with abrasive filaments.
How Fast and Precise Is a Bowden Extruder Compared to Other Extruders?
When correctly operating, a Bowden extruder setup’s main advantage is the reduction of moving mass at the print head. This allows for higher accelerations because the moving head’s inertia is minimized.
Are Bowden Extruders Commonly Used in Applications Where High Printing Speeds Are Essential?
No. Bowden extruders are not commonly used in advanced high-speed printers. While they do reduce moving mass, they limit the precision of the printing process. Bowden-enabled print speed can hit an upper limit because of the irregular feed issues discussed above.
What Is the Difference Between Direct Drive vs. Bowden?
The two systems differ in some key regards that define their functionality and maintenance issues, including:
- Direct drive uses a pinch wheel or gear filament feed situated at the print head and feeds directly into the hot end with no intermediary stage or mechanisms.
- Remote Bowden systems place the feed mechanism of the extruder in a fixed position far from the hot end. They employ a tube under tension to feed the filament under compression.
- Direct drive extruders can be more effective for flexible and abrasive filaments.
Summary
This article presented Bowen extruders, explained them, and discussed how they work and their various uses. To learn more about Bowen extruders, contact a Xometry representative.
Xometry provides a wide range of manufacturing capabilities, including 3D printing and other value-added services for all of your prototyping and production needs. Visit our website to learn more or to request a free, no-obligation quote.
Copyright and Trademark Notices
- FDM® is a registered trademark of Stratasys Inc.
Disclaimer
The content appearing on this webpage is for informational purposes only. Xometry makes no representation or warranty of any kind, be it expressed or implied, as to the accuracy, completeness, or validity of the information. Any performance parameters, geometric tolerances, specific design features, quality and types of materials, or processes should not be inferred to represent what will be delivered by third-party suppliers or manufacturers through Xometry’s network. Buyers seeking quotes for parts are responsible for defining the specific requirements for those parts. Please refer to our terms and conditions for more information.
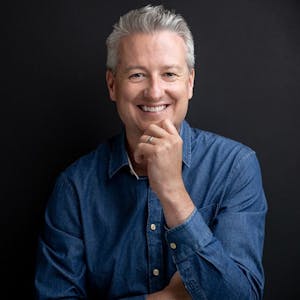