PLA (polylactic acid) filament is one of the most commonly used in fused deposition modeling (FDM) 3D printing because it’s easy to work with and looks great. In the history of plastics, PLA is the OG (well, one of them). It was invented in 1938 by DuPont chemist Wallace Carothers (who also, coincidentally, invented nylon), but took quite a long time to become mainstream. In the ‘50s, large manufacturing product materials companies started doing more in-depth research on it, and by the ‘90s, PLA was on the market commercially. It was first adopted as a biodegradable PET alternative and has since been used for everything from packaging and disposable cutlery to appliances and devices. When 3D printers emerged in the late '00s, PLA was one of the first filament materials used and, today, it accounts for more than 40% of the plastics used in additive manufacturing.
What is PLA 3D Printing Filament?
PLA is a thermoplastic polymer made by fermenting plant products like sugarcane or cornstarch to produce lactic acid, which is then polymerized into PLA, often using lactide. It can then be mixed with nucleating agents or plasticizers (i.e., polyethylene glycol) to change its properties. For extra benefits, it can also be mixed with other materials like wood fibers, carbon, metal flakes, graphene, etc. It’s then extruded into filament or fiber. The PLAs with simpler ingredient lists are known as PLA, while the ones chock full of enhancers are referred to as PLA+.
- PLA: Close to the pure polymer but may contain limited amounts of additives to modify various properties, including intramolecular flexibility, melt viscosity, and color or visual properties.
- PLA+: Likely to contain significant quantities of a wide range of additives. These include carbon fiber for model stability, stiffness, and increased UTS (ultimate tensile strength); wood fiber for cosmetic effect; graphene for stiffness and increased UTS; and metal particles for cosmetic effect.
For more information on their similarities, differences, and uses, have a look at our guide: PLA vs. PLA+ 3D Printing.
Among PLA’s desirable properties is its intra-layer bonding, which allows newly extruded plastic to bond very well with plastic that has been recently cooled. The strands and layers blend effortlessly together for a smooth (and pretty) surface, and this doesn’t change much even if you switch up the machine’s settings. It also has a good tolerance to a range of extruding temperatures so that you can use it on many different machines. This makes it super easy to print with and a great starter 3D printing filament for those without much experience.
You can use PLA for items that need to be attractive, but not necessarily long-lasting. The material can’t take a lot of stress, so you wouldn’t want to make machine parts, engineering test pieces, or bearing-type components from it. It can’t survive being left outdoors and doesn’t hold up well when faced with water, chemicals, or abrasion. Also, just because it’s made from “green” materials, that doesn’t automatically make it eco-friendly. PLA needs to be separately recycled, and it’s only biodegradable if commercially composted.
What is the Composition of PLA Filament?
PLA filament is a polymer resulting from the fermentation of plant sources such as sugar cane, taro, and cornstarch. It falls into two broad categories:
- PLA: Close to the pure polymer but may contain limited amounts of additives to modify various properties, including: intramolecular flexibility, melt viscosity, and color or visual properties.
- PLA+: Likely to contain significant quantities of a wide range of additives. These include: carbon fiber for model stability, stiffness, and increased UTS (ultimate tensile strength); wood fiber for cosmetic effect; graphene for stiffness and increased UTS; as well as metal particles for cosmetic effect.
What are the Properties of PLA Filament?
All the important properties of PLA filament are listed in the table below.
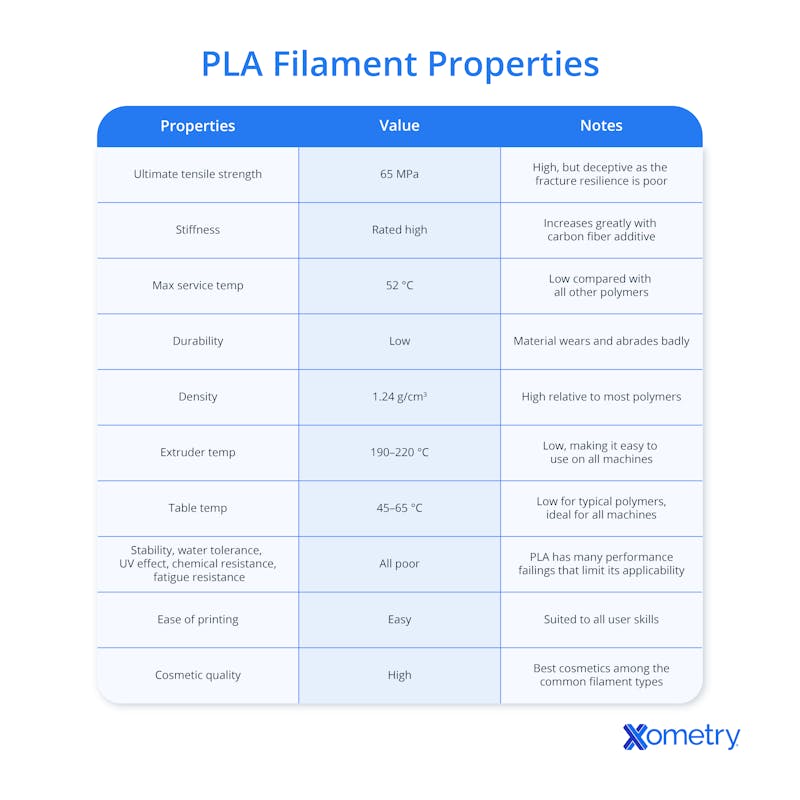
What are the Limitations of 3D Printing with PLA?
PLA is the ideal material for cosmetic models that are of short-lived applicability. These are parts that will not experience high stress, and whose dimensional precision can be accepted as moderate. PLA is very ill-suited to engineering test pieces, part assembly, or components that must act as bearings or tolerate abrasion during motion. PLA is also unsuited to outdoor use, wet applications, any chemical exposures, and conditions that expose its poor durability. While PLA is often presented as the “green” alternative, it is not well suited to environmental disposal. It needs to be sorted separately and is biodegradable under commercial composting conditions.
Why is PLA Used in 3D Printing?
PLA is used in 3D printing because it offers some significant advantages over other common FDM filaments. It is these properties that drive its selection for a significant proportion of all small FDM prints. This includes PLA’s intra-layer bonding and wide temperature tolerance. Intra-layer bonding is the ability of newly extruded plastic to couple well with recently cooled plastic. Good intra-layer bonding significantly enhances the blending of strands and layers to each other, resulting in smoother surfaces. This bonding is hard to disrupt by altering machine settings, making the material very forgiving to print. Good tolerance to a broad range of extruder temperatures allows PLA to be used on the widest variety of machines. Tolerance of a relatively cold table and build environment makes the material very usable, even in unskilled hands.
How is PLA Used in 3D Printing?
PLA is used as a material in 3D printing, specifically in fused deposition modeling (FDM). The molten filament is extruded to form fused layers, which build up to form 3D objects. PLA makes good cosmetic results possible, even with limited tuning/skill in the operation of the machine.
What is the Best PLA Print Speed?
The best PLA print speed is typically 40–60 mm/s. But, the material can give good results at speeds of up to 100 mm/s when machine parameters are suitable. Print speed is heavily dependent on the machine characteristics and the desired cosmetic quality of the outcome.
What is the PLA Filament Melting Temperature?
The PLA filament melting temperature is between 170 to 200°C. For best results in melting PLA filament, table 2 below summarizes the recommended printer settings:
Printer Settings | Value |
---|---|
Printer Settings Extruder temperature | Value 200°C |
Printer Settings Bed temperature | Value Between 50-70°C |
Printer Settings Nozzle Temperature | Value Between 195-220°C |
Printer Settings Print speed | Value 30-90 mm/s |
Printer Settings Extruder fan speed | Value 100% |
Printer Settings Retraction speed | Value Between 30-80 mm/s |
Printer Settings Retraction distance | Value Between 2-5 mm for Bowden setup
1-2 mm for direct drive printer |
Printer Settings Flow of filament | Value Reduce in 5% increments |
Printer Settings Layer height | Value 0.2 mm for standard speed and quality |
Printer Settings Prin bed | Value Level |
Printer Settings Bed material | Value Best with glass, aluminum, and BuildTak |
When melting PLA filament, adjust your machine from a low temperature in small increments – while taking care not to mistake other issues such as over- or underfeeding of filament for nozzle temperature issues. Once the setup is right, it will need at most only small adjustments for general use thereafter.
Best Settings for PLA 3D Printing Filament
To get the best results when 3D printing with PLA filament, you’ll want to make sure your printer has the right settings (although, to be fair, this material is pretty forgiving of settings). When melting it, the machine should be increased from a low setting in small increments, while being careful not to over- or under-feed the filament. You don’t particularly need a heated bed with this filament; the only thing that it would help with is easier removal of the final print. To make your piece stronger, you’ll want a wall thickness of 1.2–2.2mm, but for items with a solely cosmetic purpose, this can be 0.8mm. Getting the wall thickness just right is probably the only thing that will need a little skill. The settings we recommend for working with PLA filament are listed in the table below.
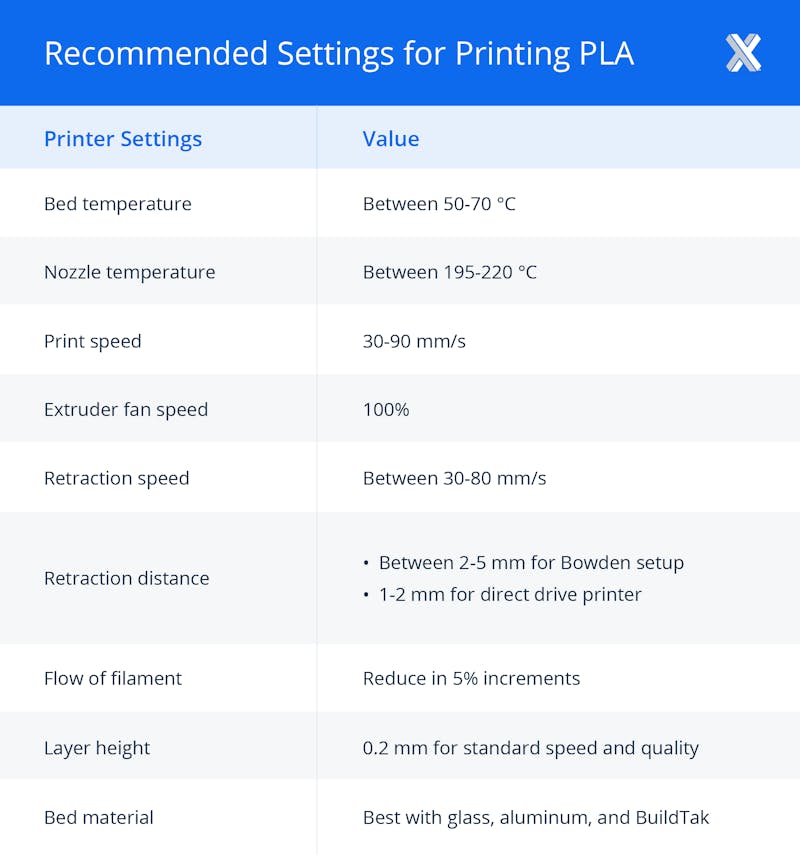
PLA vs. ABS vs. PETG
These three filament types have quite a few differences meaning that they can’t really be used interchangeably. The below table breaks down their pros and cons, but for more information, you can head on over to our in-depth guides on 3D printing with PLA vs. ABS and PETG vs. PLA.
Comparison | PLA | ABS | PETG |
---|---|---|---|
Comparison Strength | PLA Poor | ABS Excellent | PETG Great |
Comparison Ultimate tensile strength | PLA Good | ABS Lower than PLA | PETG Lower than PLA (tougher and more flexible) |
Comparison Durability | PLA Poor (brittle, degrades over time) | ABS Good | PETG Good |
Comparison Resilience | PLA Poor | ABS Excellent | PETG Good |
Comparison Elasticity | PLA Poor | ABS Good | PETG Moderate |
Comparison Shock-, fracture-, and impact-resistance | PLA Poor | ABS Excellent | PETG Good |
Comparison Aesthetic appeal | PLA Excellent | ABS Poor (often has rough surface finish) | PETG Moderate (can be glossy but shows stringing) |
Comparison Transparency | PLA Moderate (can be semi-transparent) | ABS Poor (typically opaque) | PETG Excellent (can make semi-transparent or clear parts) |
Comparison Intra-layer fusion | PLA Excellent | ABS Poor (can warp) | PETG Excellent |
Comparison Water resistance | PLA Poor | ABS Good | PETG Excellent (practically hygroscopic) |
Comparison UV tolerance | PLA Poor | ABS Poor | PETG Good |
Comparison Ease of use | PLA Easy | ABS Hard | PETG Moderate |
Comparison Skill required | PLA Low | ABS High | PETG Moderate |
Comparison Requirements | PLA Not many (hardly any warping, can print at low temperatures) | ABS Higher/controlled nozzle temperatures, enclosed environment, i.e. a chamber | PETG Higher nozzle temperature (often not possible with budget printers) |
Comparison Applications | PLA Decorative items, prototypes | ABS Structural and moving parts, bearing/rubbing surfaces | PETG Mechanical and functional parts, outdoor use |
Comparison Cost | PLA Cheapest ($15–20 per kg) | ABS Moderate ($20–30 per kg) | PETG Moderate ($20–30 per kg) |
PLA vs. ABS vs. PETG
Common FAQs About PLA 3D Printing Filament
Is a Heated Printing Bed Required When Printing With PLA?
No, a heated printing bed is not required when printing with PLA. A heated bed offers only one real advantage. It is that the relative contraction cooling of the model material breaks the bond to the table, making removal of the finished part easier. However, since PLA couples only weakly to the table material (glass, anodized aluminum, etc), this is a modest advantage that does not preclude the use of PLA on the simplest, cold bed machines.
What is a Good Wall Thickness for 3D Printing PLA?
A good wall thickness for 3D printing of PLA is in the 1.2–2.2 mm range for high-strength results. For purely cosmetic shells, a thickness of 0.8 mm will often suffice. Because the ideal wall thickness is defined in terms of the wall's function within a model structure, some skill is required in selecting this property.
What is the Difference Between PLA and ABS in 3D Printing?
The difference between PLA and ABS in 3D printing is in the part’s cosmetics and strength. ABS offers poorer cosmetics, poorer intra-layer fusion, lower UTS, and requires higher and more controlled nozzle temperatures than PLA. ABS also makes it harder to optimize print settings and requires more skill to use. However, the strength issue is more than compensated by the greater elasticity of ABS. ABS is much more resilient and shock/fracture-resistant. It is a good choice for structural strength components. The higher durability also makes ABS a great choice for moving parts that require bearing/rubbing surfaces.
What is the Difference Between PLA and PLA+ in 3D Printing?
The difference between PLA and PLA+ is in the material properties. While both share most properties in common, the nature of the additional additives in PLA+ modifies a limited range of properties that may suit particular applications. For example, the addition of metal flakes or wood fibers can render a particular cosmetic result.
What is the Difference Between PETG and PLA in 3D printing?
The difference between PETG and PLA in 3D printing is in the properties. PETG offers some significant advantages over PLA in terms of strength, durability, water/chemical/UV tolerance, and transparency. This comes at a price, though. PETG is much more sensitive to print conditions. Its nozzle temperature requires more heat, which can be hard for the lowest-cost equipment to deliver. In addition, PETG will not deliver such a good surface finish and overall cosmetics.
How Xometry Can Help
Xometry provides a wide range of manufacturing services, including custom 3D printed parts for all of your prototyping and production needs. To learn more about PLA filament and if it is the right material for your application, contact a Xometry representative, or go straight to our PLA 3D Printing service to start a new instant quote.
Disclaimer
The content appearing on this webpage is for informational purposes only. Xometry makes no representation or warranty of any kind, be it expressed or implied, as to the accuracy, completeness, or validity of the information. Any performance parameters, geometric tolerances, specific design features, quality and types of materials, or processes should not be inferred to represent what will be delivered by third-party suppliers or manufacturers through Xometry’s network. Buyers seeking quotes for parts are responsible for defining the specific requirements for those parts. Please refer to our terms and conditions for more information.
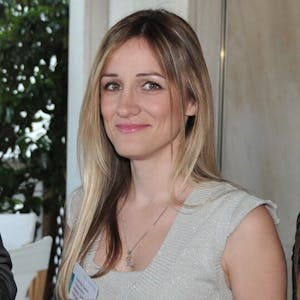