Two commonly picked FDM materials among Xometry's 3D printing customers, PLA (Polylactic Acid) and ABS (Acrylonitrile Butadiene Styrene) are both used for a wide variety of industrial and consumer applications. PLA is more brittle than ABS and tends to degrade when exposed to UV light, but it's easier to print and does not warp as easily as ABS. PLA is ideal for quick and easy prototypes, whereas ABS is better suited for functional applications.
We will dive deeper into these two materials and compare their relative advantages, disadvantages, and properties. Hopefully, by the end, you'll have a better understanding of which is more suitable for your specific application!
PLA Comparison to ABS
PLA (Polylactic Acid) is a semicrystalline thermoplastic polyester. It is derived from renewable sources and is therefore classified as a bioplastic. PLA is typically manufactured from plant starch. This origin ultimately yields the two key monomers used in PLA synthesis—lactic acid and lactide. Each monomer can be used to produce PLA using a number of different processes.
Low-molecular-weight PLA was first produced in 1932. In 1952, DuPont further developed the process and created high-molecular-weight PLA. PLA is easy to print. It is biodegradable and, therefore, more environmentally friendly than ABS. Far less energy is also required to produce PLA. To learn more, see our guide on What is PLA.
The image below shows a few parts that Xometry 3D printed using PLA:
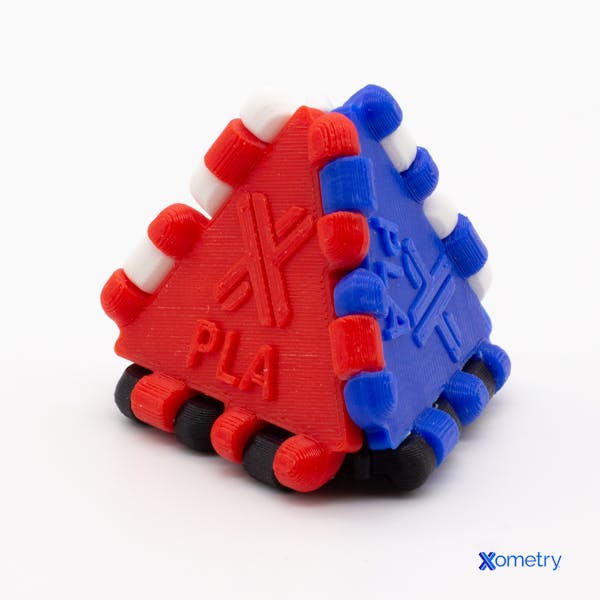
Advantages of PLA Compared to ABS
When compared with ABS, PLA has a few advantages, mainly:
- PLA is much easier to print than ABS. PLA can be printed at lower temperatures and does not warp as readily. PLA also does not typically require a heated bed or enclosed build chamber.
- Under the right conditions, such as those present in an industrial composting facility, PLA will break down into non-toxic by-products.
- Compared to ABS and other thermoplastics, PLA is a very affordable option.
Disadvantages of PLA Compared to ABS
There are some disadvantages of PLA to be aware of:
- PLA cannot withstand impacts very well and will crack more easily than ABS due to its brittleness.
- PLA cannot withstand prolonged exposure to UV light. PLA parts left out in direct sunlight, for example, will begin to break down and degrade more quickly than ABS parts.
- PLA has a relatively low melting point, meaning it won't be suitable for high-temperature environments.
ABS Definition and Comparison to PLA
Acrylonitrile Butadiene Styrene (ABS) was first patented in 1948 and commercialized in 1954 by the Borg-Warner Corporation. It is an amorphous thermoplastic polymer where the molecular structure is disordered. ABS is commonly manufactured via the polymerization of styrene and acrylonitrile. ABS is generally a tougher plastic than PLA. It can be used for applications that require significant strength and impact resistance. For more information, see our guide on what is ABS.
The parts in the image below were printed with Xometrys ABS-M30 material:
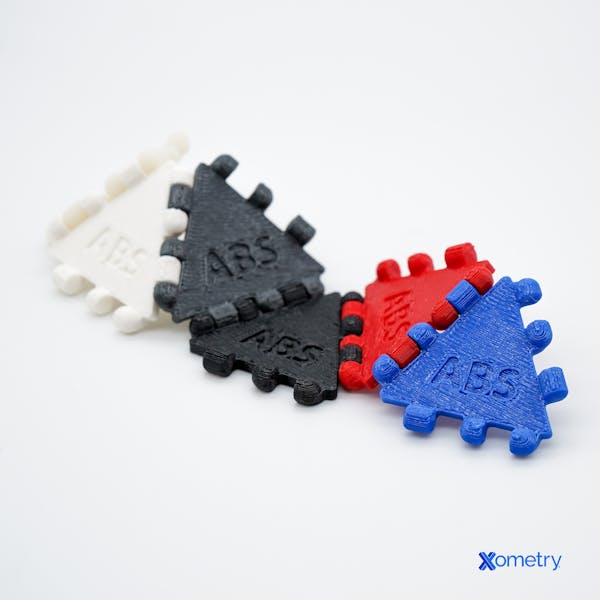
Advantages of ABS Compared to PLA
ABS has some distinct advantages of PLA, such as:
- ABS has a higher glass transition temperature than PLA. This means it can handle higher temperature use cases before the parts will soften or melt.
- Compared to PLA, ABS is pretty tough. It can withstand impacts better and has a higher resistance to abrasions.
Disadvantages of ABS Compared to PLA
ABS has its own share of disadvantages:
- ABS is more difficult to 3D print. The increased temperature differential between the ambient temperature and the print makes the parts more susceptible to warping. This is why it's best to print ABS using temperature-controlled build chambers and heated beds, like the industrial machines Xometry utilizes.
- ABS releases VOCs (Volatile Organic Compounds) and UPFs (Ultrafine Particles) during printing. Excessive exposure can cause eye and respiratory tract irritation, nausea, and headaches. Care should be taken to ensure the environment is well-ventilated and proper PPE is worn when working with ABS.
Attribute | PLA | ABS |
---|---|---|
Attribute Used for high-temperature applications | PLA No | ABS Yes |
Attribute UV Resistance | PLA Poor | ABS Moderate |
Attribute Brittle | PLA Yes | ABS No |
Attribute Biodegradable | PLA Yes | ABS No |
Attribute Produces dangerous fumes during 3D printing | PLA No | ABS Yes |
Attribute Made using renewable raw materials | PLA Yes | ABS No |
Attribute Heat Deflection Temperature @ 66 psi (°C) | PLA 55°C | ABS 96°C |
Attribute Cost | PLA Very Low | ABS Low |
Attribute Tensile Strength, Yield (XZ MPa-ZX MPa) | PLA 50 MPa-37 MPa | ABS 32 MPa-28 MPa |
Attribute Impact Strength (Notched Izod, J/m) | PLA 96.1 | ABS 200 - 215 |
Attribute Abrasion Resistant | PLA No | ABS Yes |
At Xometry, we often receive common comparison questions about PLA and ABS. Below we will go over some of the most common comparisons we get asked about and outline how each material performs for each.
Applications
PLA is not widely used for typical consumer and industrial applications. It is mostly used for 3D printing in hobbyist applications or prototyping but has found some applications in the biomedical industry. ABS, on the other hand, is used as an engineering plastic across almost every industry. It is preferred for applications requiring toughness and impact resistance.
Part Accuracy
PLA is a very easy material to 3D print and it produces parts that are dimensionally stable. ABS, on the other hand, tends to warp easily during printing which makes it a bit harder to control precise dimensions. Rest assured that Xometry uses high-end industrial printers that reliably print with ABS-M30 and can maintain accuracy across builds.
Speed
Both PLA and ABS can print at comparable speeds; however, you may need to dial down the speed a bit with ABS to avoid defects.
Surface
3D-printed PLA and ABS have the common FDM (Fused Deposition Modeling) surface finish with visible layer lines. However, ABS can be vapor smoothed with solvents like acetone while PLA must be hand sanded for optimal surface finish. The vapor smoothing process melts the surface, giving it a smooth and homogeneous finish.
Heat Resistance
PLA has poor heat resistance when compared to ABS. PLA will begin to soften at 55-60 °C whereas ABS does not begin to soften until 96-105 °C.
Biodegradability
PLA is a bioplastic and biodegradable under the correct conditions. Unfortunately, these conditions are usually only present in industrial composting facilities, so you likely won't be able to just toss a discarded print into your compost bin at home and expect it to degrade naturally. The required conditions include high temperatures and exposure to specific microbial environments. PLA can take up to 80 years to fully decompose in nature. That said, ABS is not biodegradable and can take hundreds of years to fully decompose.
Cost
PLA and ABS are among the lowest-cost materials used in 3D printing. Both can be purchased for around $20 per 1 kg spool for hobbyist machines. ABS can be slightly more expensive than PLA, but the difference is usually insignificant. If you use Xometry to order your parts, you can easily compare the costs using our Instant Quoting Engine®.
Alternatives to PLA and ABS
Despite the benefits of using PLA and ABS, an alternative material can achieve similar results:
- PETG: PETG (Polyethylene Terephthalate Glycol) provides a good middle ground between ABS and PLA. It prints as easily as PLA, but has mechanical properties as good as those of ABS, without its challenges of excessive warping and toxic fumes.
How Xometry Can Help
Xometry offers nine unique 3D printing processes and offers dozens of materials, including PLA printing and ABS printing. We can even print in rubbery materials like TPU or solid metal materials like stainless steel, depending on the printing process. Best of all, you can get pricing and lead times automatically by using the Xometry Instant Quoting Engine®. Get started today by uploading your STL files or other supported 3D CAD files, select the process and material you'd like, and get an instant quote!
Disclaimer
The content appearing on this webpage is for informational purposes only. Xometry makes no representation or warranty of any kind, be it expressed or implied, as to the accuracy, completeness, or validity of the information. Any performance parameters, geometric tolerances, specific design features, quality and types of materials, or processes should not be inferred to represent what will be delivered by third-party suppliers or manufacturers through Xometry’s network. Buyers seeking quotes for parts are responsible for defining the specific requirements for those parts. Please refer to our terms and conditions for more information.
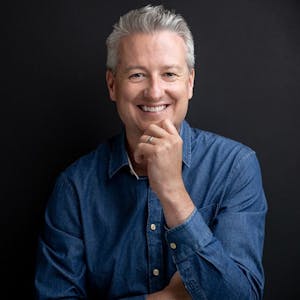