When you look past injection molding and extrusion, you’ll find 3D printing has shaken up the game for plastic part production. What was once a unique alternative is now a popular option that cuts down on processing times and makes it possible to print intricate and complex structures. However, there is a long list of technologies to choose from, including PolyJet and selective laser sintering (SLS) 3D printing, which often get compared to one another.
While they have a few similarities around the type of parts they produce, building principles, and the quality, they’re fairly different and offer their own set of advantages (and downsides) depending on the task you have in mind.
What Is PolyJet Printing?
This type of 3D printing first came to be in 2009, and since then has only improved. Trademarked Polyjet, it’s managed to protect its technology, but this has unsurprisingly led to parts, machines, and materials that are more expensive — 10 times the cost of SLS, if you’re comparing the two.
That said, PolyJet still has its perks. When you put it up against SLS, you’ll find that with PolyJet, you get a smoother surface and eight times higher resolution. This makes for impressively realistic prints and great accuracy. Just look at the photo below of PolyJet printed avocados—no, they’re not real!
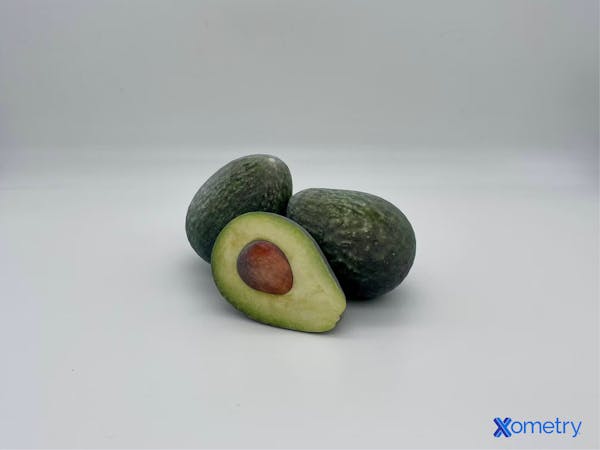
PolyJet printers work by feeding resin through a printhead onto the build platform. Then a UV light will cure the design, making it all ready to go.
Advantages vs. Disadvantages
It’s good to weigh up the pros and cons of different 3D printing technologies. Here are some of the advantages you can expect if you use PolyJet printing:
- You can use many more materials with PolyJet, compared to SLS printers, which only stick to nylons.
- You can choose resolution and speed on a PolyJet printer (you can’t with an SLS printer).
- PolyJet has the highest resolution, which ensures that any intricate details or fine features you’ve designed show up.
- PolyJet has Z resolution, which makes surfaces much smoother too.
- PolyJet equipment tends to be a lot safer because SLS uses a powerful laser.
There are also some downsides to choosing PolyJet for your printing needs:
- PolyJet materials are super expensive (10 times the price of those used in SLS printing).
- You need resin to build support structures for PolyJet printers, whereas with SLS you can just use powder—and reuse it again.
- PolyJet models are weaker than SLS ones.
- PolyJet printers have to go through head cleaning, which leads to some wastage.
- You need to have experience and skill to operate, clean, and calibrate a PolyJet printer.
What Is SLS Printing?
SLS 3D printing is a little older—created in the 1980s—and it’s also a trademarked name through DTM Inc., which brought the tech to market. It uses a nylon powder to create its builds, a material that can be bought from a wide range of suppliers, unlike PolyJet.
In turn, SLS printing is much more affordable than PolyJet printing, roughly 10 times cheaper. You’ll find it’s about $50 per kilogram. It can create strong products with little to zero waste, and the machine is much easier to run and maintain. You can see what a SLS 3D printer looks like here at Xometry in the picture below.
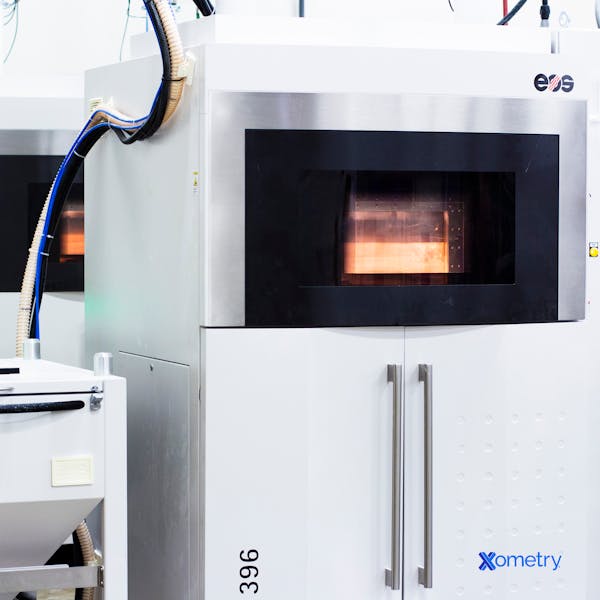
SLS works by building 2D slices that form a 3D model when put together. First a layer of powder gets applied to the build table, then the powder particles get fused together with the help of a very strong CO2 laser that’s getting its instructions from G-code. Then, you have a solid structure—one that’s only as high resolution as the machine’s light beam diameter can create.
Advantages vs. Disadvantages
SLS also has its fair share of perks and downsides. Here are some of the good qualities that come with this type of printing:
- SLS materials are way cheaper than PolyJet, about 1/10th of the price.
- The powder on the build table serves as the support structure and can be reused, which cuts down on costs and waste.
- SLS prints are the strongest out of any other plastic 3D printer.
- This type of process leads to zero or little waste, and cleanup is extremely simple.
- It’s much easier to maintain, service, and operate an SLS printer over a PolyJet one.
There are also some disadvantages of SLS printing to consider:
- SLS has relatively slim pickings when it comes to materials.
- It has lower resolutions on all dimensions and axes compared to PolyJet.
- SLS builds have a rougher finish and surface because of the powder grain size.
- Said rough surfaces are impossible to polish, so you’re left with a sand-like texture on builds.
- The high-power laser can be hazardous and dangerous to work with.
You can see an example of an SLS printed part with a Xometry logo in the photo below.
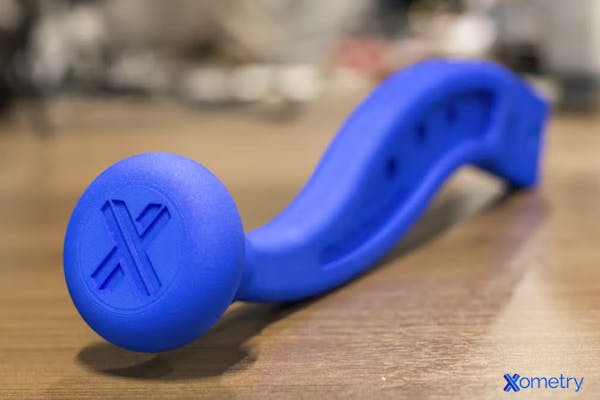
Attribute | PolyJet | SLS |
---|---|---|
Attribute Resolution | PolyJet 16 microns | SLS 45 microns |
Attribute Part wall thickness | PolyJet 0.2 mm walls are doable | SLS 1.2 mm is a practical limit |
Attribute Wide range of materials | PolyJet Yes | SLS No |
Attribute Low support waste | PolyJet No | SLS Yes |
Attribute Low process waste | PolyJet No | SLS Yes |
Attribute High material strength | PolyJet No | SLS Yes |
Attribute Smooth surface finish | PolyJet Yes | SLS No |
Attribute Largest build volume | PolyJet 1,000 x 800 x 500 | SLS 600 x 300 x 300 |
Attribute Cost per kg of material | PolyJet $200 to $500 | SLS Around $50 |
Attribute Applications | PolyJet Cosmetic and sanded/painted parts, engineering assessment models, lenses/light pipes, rubber parts for seals, overmolds | SLS Highly stressed parts for evaluation needs, other components that don’t need to be cosmetically or aesthetically pleasing |
PolyJet vs. SLS Comparison
Alternative Options for Printing
There are so many types of 3D printing technologies out there, and you might be searching for alternatives outside of PolyJet and SLS or simply looking to see what options exist for future projects—here are two.
- SLA: For a similar method that uses fusion like SLS, stereolithography (SLA) is a worthy alternative and also uses a laser but provides high-resolution prints.
- FDM: For rapid production like SLS and a wider range of materials like PolyJet, look to fused deposition modeling (FDM). It draws layers of the model and fuses them together for a final product that’s made quickly and cost-effectively.
How do PolyJet and SLS materials compare?
These two differ mainly in format and price—PolyJet materials are complex resins, and SLS material is a nylon powder. The former can cost up to $500 per kilogram, whereas SLS powders are around $50 per kilogram. With a PolyJet print, you get an end product that’s smooth (or can be smoothed), but with SLS you’ll have a rougher, sandy finish.
How are PolyJet and SLS similar?
You’ll find that PolyJet and SLS are pretty different, but they do have a few similarities. Both use Z layering and build their products with polymer materials. You can also lean on them for isotropic parts that are equally strong in all their axes, and they’re both capable of printing high-quality components that are ready to go off the plate.
What are the differences between PolyJet and Multijet?
Another printing type that gets compared to PolyJet is Multijet. Multijet tends to be cheaper and they’re patented and owned by different companies. They both work in similar ways—by dispersing droplets that are UV cured.
How Xometry Can Help
We offer both PolyJet and SLS printing services here at Xometry, as well as various other types. Get a free quote on our website for these and others, such as direct metal laser sintering, fused deposition modeling, and plastic 3D printing.
Disclaimer
The content appearing on this webpage is for informational purposes only. Xometry makes no representation or warranty of any kind, be it expressed or implied, as to the accuracy, completeness, or validity of the information. Any performance parameters, geometric tolerances, specific design features, quality and types of materials, or processes should not be inferred to represent what will be delivered by third-party suppliers or manufacturers through Xometry’s network. Buyers seeking quotes for parts are responsible for defining the specific requirements for those parts. Please refer to our terms and conditions for more information.
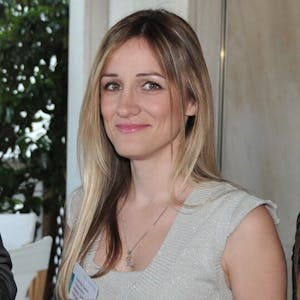