SLS and MJF are powder-bed fusion technologies that create 3D parts from a thermoplastic powder. Selective laser sintering (SLS) uses a laser to melt and fuse powder grains, whereas multi-jet fusion (MJF) employs a fusing agent, heat, and infrared light to fuse the powder. SLS can employ a more comprehensive selection of materials – many of which can be dyed – whereas MJF creates better isotropic properties at a slightly higher print resolution. MJF is ideal for smaller functional parts, while SLS is the better choice for visual prototypes and medium-sized functional parts. Both styles are similar in terms of printing cost and speed, though MJF is cheaper for larger production volumes.
This article will compare SLS vs. MJF and outline their differences, materials, and printing technology.
Intro to SLS and A Quick Comparison to MJF
SLS (selective laser sintering) is a powder-bed 3D printing technology for thermoplastic materials. It was first invented by Dr. Carl Deckard and Dr. Joe Beaman in the mid-1980s. This process works by selectively sintering a plastic powder with a laser beam (typically a CO2 laser). The laser beam traces out successive cross-sections of a part and sinters the plastic particles as it moves. After each layer, the print bed moves down, and another layer of powder is applied. Sintering refers to the process of heating the plastic particles to the point where their outer surfaces begin melting. This causes the individual particles to stick together. SLS technology is a much more mature technology than MJF and functions on a wider range of materials. Below is an image of a typical SLS machine.
To learn more, see our guide on SLS Printing.
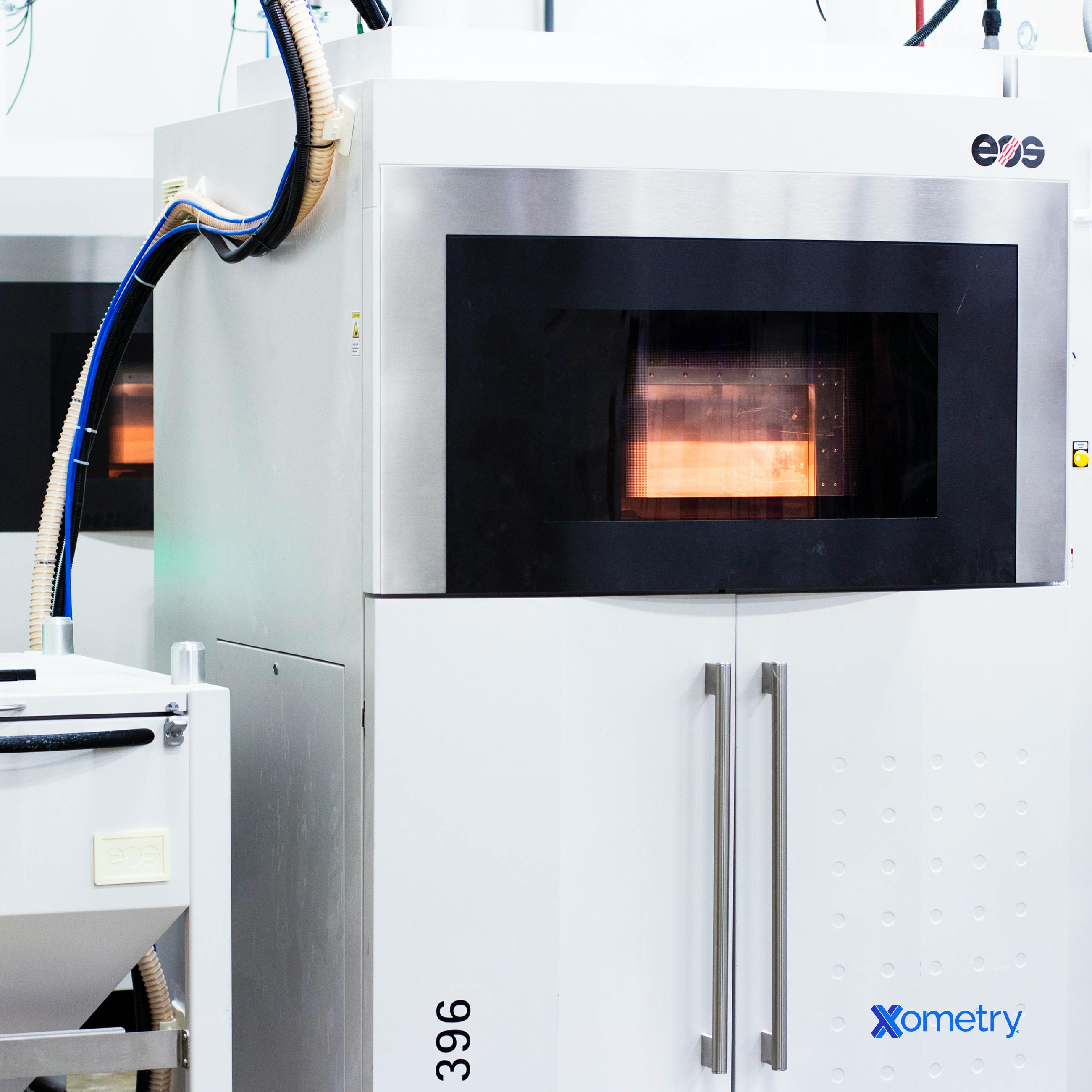
Advantages and Disadvantages of SLS Compared to MJF for Making Parts
Listed below are some key advantages of SLS vs. MJF:
- Though both processes regularly use nylon 12, SLS can operate on a broader range of other materials.
- SLS parts are typically printed in white or gray but can be dyed almost any color.
Here are some key disadvantages of SLS vs. MJF:
- Only 30 to 50% of the powder can is recyclable after an SLS printing run. MJF has significantly better recyclability, which can reduce costs.
- Parts printed with SLS have anisotropic material properties. Anisotropy means their mechanical properties differ depending on the direction of the applied load. MJF prints do not have this problem.
MJF Intro and a Quick Comparison to SLS
MJF (multi-jet fusion) is a powder-bed 3D printing technology that was developed by Hewlett-Packard in 2016. It employs a multi-step process. A thin layer of powder is first laid down on the print bed. The powder is then heated to just below its sintering temperature. Next, a fusing agent is applied to the powder in the shape of the part’s cross-section. A detailing agent is then applied to the edges of the part to help create crisper and sharper edges. Finally, an infrared heat source passes over the plastic and sinters the treated plastic particles. MJF is a more advanced technology geared towards high production rates than SLS. The image below shows an MJF printing process:
To learn more, see our guide on What is MJF.
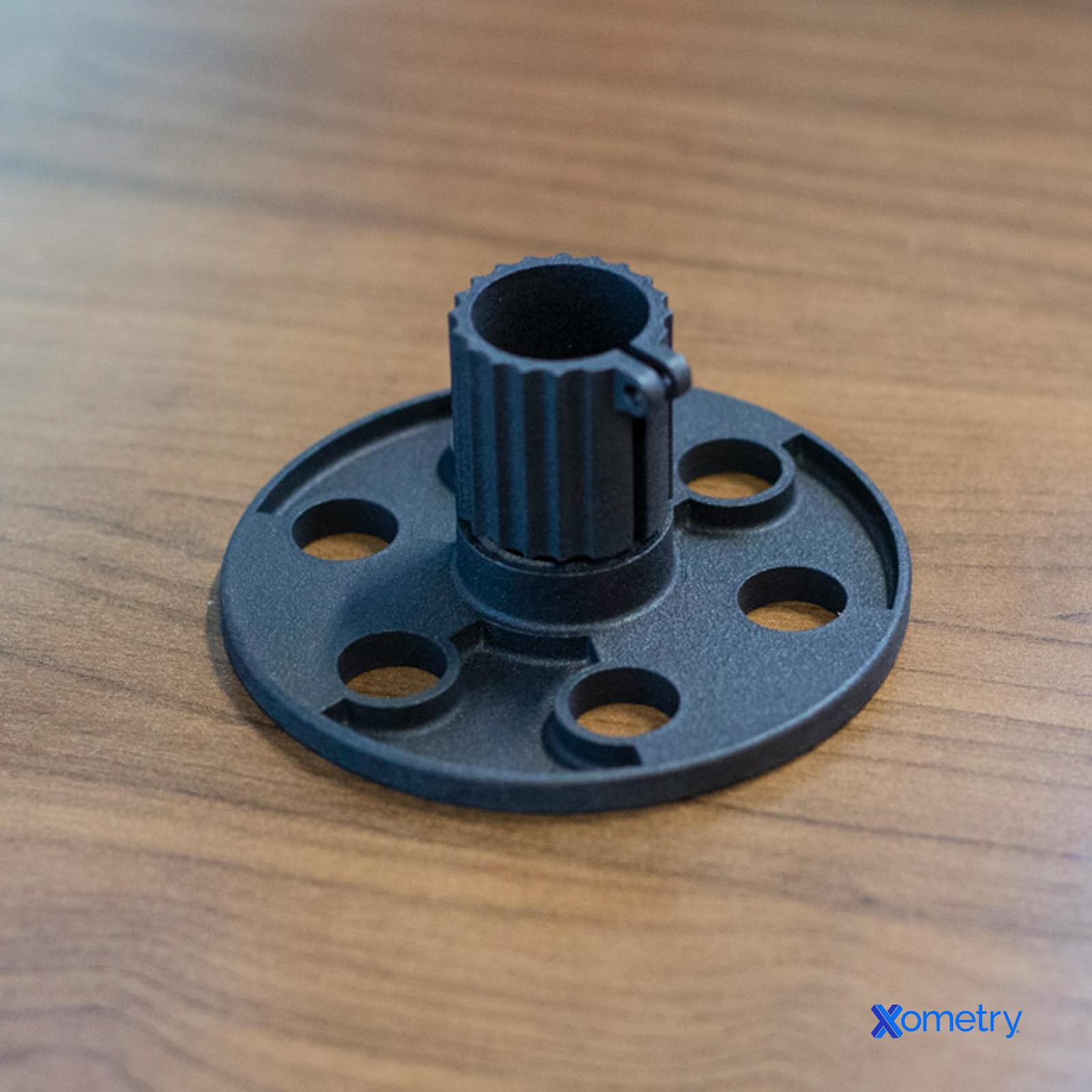
Advantages and Disadvantages of MJF Compared to SLS For Making Parts
Listed below are some key advantages of MJF over SLS:
- MJF machines are capable of producing parts with isotropic material properties – the resulting plastic is almost 98% isotropic.
- The powder used in an MJF printer is significantly more recyclable; up to 80% of the powder is often reusable.
- MJF printers have removable build volumes. This means the completed parts can be allowed to cool outside the printer, and the workspace prepped for more production right away.
Here are some key disadvantages of MJF vs. SLS:
- MJF parts are gray and can only accept black dye.
- The material choice for MJF printers is more limited. Hewlett Packard, however, is continually developing new materials.
Comparisons Between SLS and MJF
When comparing SLS and MJF, there are some common properties that come to mind. Matt Schmidt, a Senior Solutions Engineer here at Xometry, states, "The SLS and MJF platforms are very similar and are capable of processing common materials such as Nylon 11 and 12. However, there are some differences in the way each platform processes the materials that create different results. The SLS system utilizes a laser thermal source to melt powder bed materials, which has greater and more localized heating effects. The higher heat gradiant often resluts in lower mechanical property values for tensile, yield and elongation. On the other hand, MJF utilizes an infrared heat lamp, which is a more broad spectrum and melts materials at a more consistent rate across the powder bed. This increases the mechanical properties slightly over SLS. However, the localized heat source from a SLS laser platform, will provide slightly more accurate dimensional results over the broad spectrum heat lamp of MJF. Material properties and accuracy become factors within the decision-making process. Lastly, the SLS systems traditionally have larger build areas, which provide for larger parts or larger volume throughput with better production costs. The overall low operational costs of MJF favor day-to-day prototype builds and lower-volume production parts."
The table below lists some of the more common properties of SLS vs. MJF as well as how they compare with each other:
Attribute | SLS | MJF |
---|---|---|
Attribute Print resolution | SLS 120 microns | MJF 80 microns |
Attribute Can be dyed in multiple colors | SLS Yes | MJF No |
Attribute Minimum recommended feature size | SLS 0.75 mm | MJF 0.75 mm |
Attribute Can recycle more than 80% of unused powder | SLS No | MJF Yes |
Attribute Parts need to be cooled after printing | SLS Yes | MJF No |
Attribute Parts need support structures | SLS No | MJF No |
Attribute Largest print volume | SLS 660 x 380 x 580 mm | MJF 380 x 280 x 380 mm |
Table 1. SLS vs. MJF Comparison
Technology comparison: SLS and MJF are both powder-bed fusion technologies. Powder bed fusion (PBF) means that parts are cumulatively built up one layer at a time by fusing powdered thermoplastics. SLS uses a heated chamber and a CO2 laser to sinter the particles. Meanwhile, the MJF process depends on an infrared heat source, preheated powder, and a specialized fusing agent deposited by a printhead, all working together to fuse the particles.
Material comparison: SLS and MJF extensively use polyamides like nylon 12 and 11, TPU (thermoplastic polyurethane), TPA (thermoplastic polyamide), and polypropylene. SLS is also able to print with carbon- and aluminum-filled nylon. Overall SLS works with a broader range of nylons, while MJF offers other material options like polypropylene and flexible TPU.
Applications comparison: SLS and MJF are used to create functional parts such as casting patterns, medical devices, and elastomeric parts. SLS is often used for prototyping components that will eventually be injection molded, as the designs tend to react similarly to the manufacturing process, allowing engineers to hone designs before committing to mold tooling, which can be costly. Regarding aesthetics, MJF products have a dull, uneven gray color and can only accept black dye. However, SLS parts are naturally off-white and can be dyed with many colors, making them more ideal for visual prototypes.
Print volume comparison: SLS machines have larger build volumes than MJF machines, especially for certain material variants, such as glass-filled nylon. With its larger build area, SLS can print more nested parts in a single run. Large 3D-printed parts can often warp, but it’s more of a problem for MJF processes than SLS. With SLS printing, build planners utilize as much of the build volume as possible because unused powder is less recyclable in SLS than with MJF.
Surface finish comparison: SLS and MJF parts both have a characteristic rough/matte surface finish. However, in both cases, technicians can smooth the surfaces via shot blasting or media tumbling. Chemical vapor smoothing has recently allowed both SLS and MJF parts to achieve a sealed, semi-gloss surface at low costs.
Cost comparison: SLS and MJF have similar print costs at lower quantities. However, at higher quantities, MJF's economy of scale is better than that of SLS. MJF is more competitive because the printing process is slightly faster, and the unused material is more recyclable.
An Alternatives to SLS and MJF
Despite the benefits of SLS and MJF, there is an alternative technology that can achieve similar results to both, and that is stereolithography. Stereolithography can achieve similar or better print resolution and quality. SLA uses a liquid photopolymer and builds parts by curing successive layers of that liquid precisely using a UV laser. However, because SLA does not produce thermoplastic parts, the mechanical properties and heat deflection of SLA components will be lower than SLS or MJF manufactured parts.
Some Similarities Between SLS and MJF
- Both technologies make use of powder bed fusion processes to manufacture parts.
- Printing cost is comparable when scaled up.
- Parts have a rough/matte surface finish.
- Both printers most commonly use nylon 12 powder.
Summary
Xometry offers a full range of 3D printing services for your projects, including SLS and MJF 3D printing services. Visit our Instant Quote Engine for an instant quote in seconds.
Disclaimer
The content appearing on this webpage is for informational purposes only. Xometry makes no representation or warranty of any kind, expressed or implied, as to the information’s accuracy, completeness, or validity. Designers should not infer performance parameters, geometric tolerances, specific design features, quality and types of materials, or processes to represent what will be delivered by third-party suppliers or manufacturers through Xometry’s network. Buyers seeking quotes for parts are responsible for defining the specific requirements for those parts. Please refer to our terms and conditions for more information.
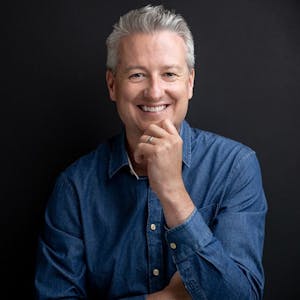