Vapor smoothing of PETG (polyethylene terephthalate glycol) is a low-labor method for producing moderate to high gloss and a greater degree of smoothness on the surface of some 3D-printed parts. It is achieved by exposing the parts to a solvent-laden atmosphere, such that the surface layer is partially dissolved and blends into a film, before solvent evaporation then hardens the material.
The end result can produce aesthetically pleasing prototypes, though some sacrifice of surface and feature accuracy may result. It is useful for cosmetic parts, and also as a way of rendering porous prototypes such as those from FDM (fusion deposition modeling) and FFF (fused filament fabrication) to a watertight and even airtight end state.
What Is Vapor Smoothing PETG?
Vapor smoothing PETG refers to the post-processing technique used to improve the surface irregularity of 3D-printed parts made from polyethylene terephthalate glycol (PETG) filament or powder. These parts are usually made using FDM, FFF, and the various methods of PBF (powder bed fusion, sometimes SLM (selective laser melting)). These processes have a tendency for the build resolution to result in visible Z-axis steps that mar the surface.
Vapor smoothing is a method most commonly used with ABS (acrylonitrile butadiene styrene) prints, but it is increasingly applied to PETG. However, it's important to note that vapor smoothing PETG may not yield the same results as ABS. It might not also be as effective in achieving a glossy finish due to the differences in material properties. PETG is more resistant to commonly used solvents, so the effect is reduced in comparison with its application to ABS.
What Is Vapor Smoothing PETG Also Known As?
In most material applications, vapor smoothing is also known as, chemical smoothing, acetone smoothing, and chemical vapor smoothing.
What Is the Purpose of Vapor Smoothing PETG in Manufacturing?
The purpose of vapor smoothing is to surface-liquify the build material by solvent exposure, to cause the layers to blur and blend together. This achieves a better layer adhesion at the surface, as the “skin” of the printed part softens and merges into a surface that has less layer-related discontinuity. It also produces a better cosmetic finish, as the roughness diminishes, and often a glossy surface results. And finally, there is no weakening of the (as-printed) inter-Z layer welding, as the solvent exposure should not be sufficiently intense to penetrate the model deeply.
What Are the Industries That Use Vapor Smoothing PETG?
There are various industry sectors that employ vapor smoothing techniques for 3D-printed parts, including PETG such as: the automotive industries, consumer goods companies, and medical sectors. Vapor smoothing can be beneficial for improving the surface finish of certain automotive components, improving non-precision parts such as soft or bone tissue models used for surgical planning, and consumer product cosmetic parts, such as electronics casings, fashion accessories, as well as
Vapor smoothing with PETG is not as widespread as with other materials like ABS. PETG is chosen for its specific properties, such as toughness and transparency. Sometimes, its natural surface finish is preferred for certain applications. It is important to note that the vapor smoothing process requires very aggressive and harmful solvents, reducing the applicability of the technique.
How Does Vapor Smoothing PETG Work?
Vapor smoothing PETG works by suspending the prototype part in a vapor-laden atmosphere. Some condensation will take place on the surface of the prototype. This condensed solvent will weaken the bonds that hold the polymer chains to each other without inducing any significant degree of depolymerization. The dissolution of the polymer into the solvent allows surface material from multiple Z layers to blend together into a more closely unified but softened mass. The end result is a smoothed and integrated surface that can be used to improve cosmetics, achieve waterproofness, and to a degree improve the anisotropic properties of a part printed in a PETG (or other materials).
What Is the Step-by-Step Process of Vapor Smoothing PETG?
Listed below is the general process of vapor smoothing PETG:
1. Gather the Necessary Materials
The primary material needed for vapor smoothing is a chemical solvent that can dissolve the outer layer of the 3D-printed part, effectively smoothing the surface. For PETG, solvents like ethyl acetate, MEK, or dichloromethane are required. Prepare a gas-tight and solvent-resistant container (the vapor chamber) large enough to hold the 3D-printed part and the vaporizing solvent. A support or rack to suspend the 3D-printed part inside the container will also be needed. Additionally, prepare all safety equipment such as PPE and fire extinguishers.
2. Prepare the Part
Most of the preparatory steps before vapor smoothing are simply those of post-print model completion. This includes removing any supports or soluble support material residues. Clean up any support blemishes that are part of the printed part. Fit hanging support to the part, preferably attached in such a way that any scarring that results from support contact during vapor smoothing doesn’t reduce the utility of the model. Finally, suspend the model in the vapor chamber.
3. Safety Precautions
Various safety precautions should be followed, such as: ensuring the space is well-ventilated, having a carbon filter VOC respirator available, and using it when handling the solvent or vapor smoothing parts. If possible, on completion, use a forced vent to clear the chamber and pass this through an activated charcoal filter and outside. Use solvent-resilient gloves (latex for example) when handling the solvent. Have a fire extinguisher on hand and leave post-smoothing parts suspended in a well-ventilated space to finish the solvent evaporation process.
4. Preheat the Container
Preheat the vapor chamber to an appropriate temperature, based on experience and tests. Don’t exceed a safe level (below 70 °C), to avoid the risk of bubbles developing on the prototype. Ideally, the chamber should be maintained at your target temperature for the period of the process. And if possible this temperature and the timing of the process should be automated, for maximum consistency.
5. Vapor Exposure
The duration and intensity of the vapor exposure are highly dependent on print material, model geometry, solvent type, solvent heating, and your own experimental evaluations. The critical time/intensity required is enough to soften the surface without achieving deeper penetration into more vulnerable areas. The part should be left until a satisfactory degree of smoothing has been achieved. However, it should not be long enough to degrade model accuracy excessively or trigger distortion in vulnerable areas of the part.
6. Seal the Container
The vapor chamber should be gas-tight and able to pressure vent to clear air, through a filter. It is best to assume that your own space near the chamber will be quite heavily contaminated with solvent vapor and that this level may climb without you being fully aware of it, as your sense of smell may be degraded by exposure to the VOC.
7. Wait and Monitor
Observe the smoothing process for any new part that you have not smoothed before. Variations due to part geometry and even build profile settings can have a profound effect.
For example, if a part has thin and unsupported sections, there is a risk of distortion in the part geometry as the material softens. Infill density can also influence behavior, as lower-density sections can be more deeply influenced if the surface porosity is enough to allow vapor penetration. All of these variables risk model damage that cannot be reversed.
8. Ventilation and Safety
The solvents used to smooth polymers are often toxic and can have neurological effects when in the bloodstream. Many of the chloroform-related chemicals are carcinogenic, and MEK is also a high-risk chemical. Treat them all as harmful, irrespective of which VOC you are employing. Use well-ventilated spaces, if possible vent the chamber to open air (outside) using an activated charcoal filter and wear a respirator mask.
9. Post-Process Cleaning
Many parts will not require any cleaning after vapor smoothing if they went into the process contaminant-free and the process itself is clean. However, it's important to ensure all traces of solvent are evaporated using a post-vapor-smoothing stage. A simple wash with isopropyl alcohol and then a mild detergent solution followed by deionized water rinse and drying will leave the models clean and ready to use.
10. Final Inspection
There is potential for loss of detail, distortion, and other imperfections to result from vapor smoothing, so a detailed examination and check for any excessive dimensional changes, loss of symmetry, warping, etc. is worthwhile, before passing parts as complete and ready for use.
What Are Some Common Post-Processing Methods for Metal Parts?
Listed below are some common post-processing methods for metal parts:
1. Electrochemical Polishing
Electrochemical polishing (or anodic polishing, electrolytic polishing, or electropolishing) places the metal part as the anode in an electrolytic cell. It uses an ionization current to erode a thin and very controlled surface layer from the part. There is a strong tendency for peaks and high points on a surface to react more vigorously with the electrolytic process. High points are removed more aggressively than low points or flat surfaces. This results in significant improvement in the surface finish such that porosity-free prototypes can get close to a mirror finish if allowed long enough in the process.
2. Mechanical Polishing
The traditional method for improving surface finish on metals is to abrade the surface with increasingly fine-grain ablation materials. This ends with a polish process that uses abrasive so fine it leaves no eye-detectable irregularities. This process is as old as metallurgy and was used in the ancient world to give items an appealing appearance. For example, surfaces with silver or copper mirroring do give high-status weapons an impressive finish. In a modern context, much of the same can be achieved by progressively decreasing the grain size of abrasives used in a barrelling process or mechanical/hand polishing. This is a time-consuming and generally expensive process. It is rarely used in mass production but may be applicable to prototypes, for which cost is rarely a primary driver. However, irregular and complex parts do not lend themselves to this.
3. Chemical Polishing
Chemical polishing relates closely to electrochemical polishing, lacking only the ionization current. It is performed using proprietary blends of phosphoric, nitric, sulfuric, and hydrochloric acids, combined with stabilizers and surfactants to deliver smooth surfaces. Chemical polishing can be fast, but it is only suitable for modifying relatively smooth surfaces, as there is less tendency for “high point” removal than in electrolytic processes.
How Much Does Vapor Smoothing PETG Cost?
As a service, the price of vapor smoothing is very variable. Specialist providers who perform this process extensively provide the service for around 5–15% of the cost of the printed part. The pricing structures of providers who perform this process less often are much more variable—ranging from free to a similar cost to the original prototype.
It should be noted that setting up to perform vapor smoothing can be very low cost as a trial process. Good equipment and a high operational safety standard represent potential costs of$30–60k for a safe, repeatable, and rapid capability.
How Does Laser Beam Profiling Optimize PETG Part Vapor Smoothing?
Analyzing the laser beam profile ensures that the energy is evenly distributed across the PETG surface. Uniform energy distribution results in a more consistent surface finish. Resolution depends on spot size, so a better quality laser and better optics will allow higher resolution outcomes in print. Better energy distribution results in more uniform heat application in fusing the powder and a lower risk of localized heat damage that can mar the surface finish.
For more information, see our Laser Beam Profiler guide.
What Are Examples of Vapor Smoothing PETG Products?
Some examples of vapor-smoothed PETG products are:
1. Prototypes and Functional Parts
The use of vapor smoothing for prototypes is common, especially if cosmetic quality is more important than precision. Functional prototypes can often have a second life as market test products, investor relations tools, and advertising media. To that end, vapor smoothing can be a very useful process in delivering multi-task, capable 3D-printed product outcomes.
2. Decorative Objects
When a 3D print is produced for a decorative purpose, the as-printed state generally fails to fit the bill. FDM/FFF parts are low resolution and really look like prototypes! Vapor smoothing can lift the appearance of parts from striated and prototype-like to presentable, with low effort and labor required. Alternatives such as filling/sanding are labor-intensive and skilled. The intrinsic porosity and low resolution of these parts in their unsmoothed state are cosmetically poor.
PBF parts have a rough, particulate finish that cannot be considered highly cosmetic. Their resolution is much better than typical FDM/FFF however, and their porosity is approximately zero. On that basis, vapor smoothing can lift these parts from “functional but ugly” to excellent, by minimizing the sandy nature of the surface and rendering it glossy.
3. Cosplay Props and Costumes
Stage, movie, and cosplay equipment are sometimes produced by 3D printing and often include painted and plated finishes to meet color expectations. This requires smoothing that doesn’t double or triple the cost of parts. Similarly, an increasing prevalence of home 3D printing is creating consequent growth in vapor smoothing as a do-it-yourself process.
4. Display Models and Miniatures
Display models and miniatures have a tendency to be small and intricately detailed. Vapor-smoothing PETG-printed materials help make these more visually pleasing.
What Is the Life Span of Vapor Smoothing PETG Products?
The useful functional life of a PETG prototype ends when it is broken by excessive force in use, abraded to the point of damage, or crushed. In general, PETG prototypes do not have an intrinsic life span, in that the material is extremely stable and hard to degrade by any non-aggressive means. For example, exposure to the types of solvents used in vapor smoothing does not happen in normal environments. The temperature required to damage a PETG printed part is very high, again not present in normal environments. And PETG is non-hygroscopic and essentially impervious to microbial or bacterial attack.
What Is the Quality of Vapor Smoothing PETG Products?
When carefully performed, vapor smoothing of PETG parts can produce a very significant quality improvement in 3D-printed parts.
Does Vapor Smoothing Affect PETG Part Surface Smoothness and Uniformity?
It depends. Vapor smoothing allows microscopic surface features, up to the resolution of the build, to dissolve into a single, continuous film and then harden as the solvent evaporates. The end result is generally a moderate- to high-gloss surface which no longer shows the build-related surface texture that results from the printing. For lower Z resolution processes such as FDM/FFF, the surface will be considerably smoothed. However, it may show signs of the Z steps where curvature emphasizes those steps by a disjointed flat surface that appears as aliasing on the curvature. These features will be smoothed but not removed. Where the build features and resolution are of a higher standard, such as in PBF models, vapor smoothing can reliably remove virtually all signs of the build steps and powder texture. The smoothness and uniformity of the surface will be improved, and porous prototypes can be relied on to be waterproof in most cases, after smoothing.
What Is the Difference Between Vapor Smoothing PETG and Acetone Vapor Smoothing?
PETG is not soluble in acetone, so considerably more aggressive solvents such as MEK are required. Acetone vapor smoothing is appropriate for ABS and polystyrene prototypes and some others. In all other regards, the processes are essentially identical. If the equipment is wisely selected, both processes can be implemented in the same system, though not at the same time.
What Is the Difference Between Vapor Smoothing PETG and Vapor Smoothing PLA?
Smoothing of PETG is usually performed with MEK, toluene, chloroform, cyclohexanone, or dichloromethane, whereas PLA (polylactic acid) reportedly responds best to dichloromethane only. Otherwise, the process equipment is interchangeable and the methods are identical.
For more information, see our guide on Vapor Smoothing PLA.
Summary
This article presented vapor smoothing PETG, explained it, and discussed it works and its advantages. To learn more about vapor smoothing PETG, contact a Xometry representative.
Xometry provides a wide range of manufacturing capabilities, including 3D printing and other value-added services for all of your prototyping and production needs. Visit our website to learn more or to request a free, no-obligation quote.
Disclaimer
The content appearing on this webpage is for informational purposes only. Xometry makes no representation or warranty of any kind, be it expressed or implied, as to the accuracy, completeness, or validity of the information. Any performance parameters, geometric tolerances, specific design features, quality and types of materials, or processes should not be inferred to represent what will be delivered by third-party suppliers or manufacturers through Xometry’s network. Buyers seeking quotes for parts are responsible for defining the specific requirements for those parts. Please refer to our terms and conditions for more information.
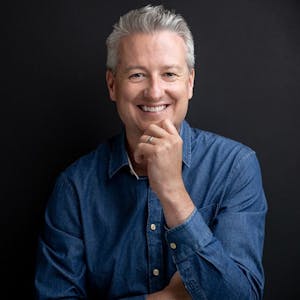