Vapor smoothing is a post-processing technique employed in the domain of additive manufacturing to improve the surface finish and aesthetics of objects that have been 3D printed in PLA plastic.
PLA (polylactic acid) is a popular thermoplastic filament used in 3D printing because it is biodegradable and easy to use. However, PLA prints often exhibit visible layer lines and rough surfaces. That’s where vapor smoothing comes in. The PLA object is exposed to solvent vapors, resulting in the partial dissolution of the outer layer. It creates a smoother and more polished appearance.
By vapor smoothing PLA, you can: improve part aesthetics, make surfaces stronger, and reduce porosity. The process is thus valuable for both visual and functional improvements. However, it also comes with some drawbacks, such as the potential loss of fine details and the need for proper safety precautions when handling solvents. This article will examine the process of vapor smoothing PLA in more detail, including: its definition, benefits, and drawbacks, especially in relation to laser cutting.
What Is Vapor Smoothing PLA?
Vapor smoothing is a post-processing method used to improve the surface finishes of 3D-printed PLA (polylactic acid) objects. In this procedure, the PLA component is exposed to vaporized solvent. This causes a chemical reaction, melts the surface, and leaves behind a smoother finish. It is important to remember that vapor smoothing of PLA requires attention because prolonged exposure to ethyl acetate vapor may distort the object or smooth out features you want to keep. You’re best off controlling exposure time and running tests on sample prints to determine the ideal smoothing effect.
How Does the Vapor Smoothing PLA Work?
The process of vapor smoothing is initiated by carefully suspending the parts within a sealed process chamber, ensuring that they receive maximum exposure to the vapor. The solvent fumes produce a controlled liquefied chemical melt that redistributes itself across the material’s surface, resulting in smoother surfaces, sealed cavities, and greater shine. The vapors are then forced out of the chamber by heating it. Vapor smoothing preserves precise dimensions and water tightness, and has no detrimental effects on mechanical properties. Uniform wall thicknesses and rounded internal corners can help you prevent voids from forming. Timing is essential to prevent problems with joint integrity or parts sticking together during the process.
How Does Vapor Smoothing PLA Impact the Laser-Cutting Process?
The laser-cutting process is impacted by vapor smoothing PLA in both good and bad ways. It reduces the charring and discoloration caused by cutting, so the cuts look nicer. However, there is a greater chance of melting or deformation, especially if the smoothing process is overdone, as the softened PLA may be more susceptible to the laser's heat. Proper laser parameter optimization and cutting process monitoring will improve your results and prevent potential material damage or deformation.
To learn more, see our guide on What is Laser Cutting Used For.
What Are the Advantages of Using Vapor Smoothing PLA in Laser Cutting?
Your laser cutting operations may improve after vapor smoothing PLA for several reasons:
1. Improved Cut Quality
The vapor smoothing technique creates a smoother surface, so the subsequent laser cuts will also come out cleaner and more precise. Fewer surface irregularities and layer lines mean better edge definition and fewer imperfections in the final parts. Consequently, the end product is more likely to meet your specifications and look pleasing to the eye.
2. Reduced Charring and Discoloration
This controlled post-processing technique minimizes the burning effect that can occur during cutting, thus preserving the visual appeal of the final product. Additional refinishing or surface treatments may not be necessary. This streamlines the production process and delivers pristine finished parts directly from the laser cutter.
3. Enhanced Detail Retention
By vapor smoothing PLA, you can typically preserve intricate 3D-printed details. The smoothed surface makes minor details more distinct, whether laser cutting is involved or not. The improved detailing will make laser-cut details look like they fit the same aesthetic.
4. Increased Precision
Because vapor-smoothed PLA allows for more precise cuts, it gives you the option of more intricate and complex designs. The smoother surface and improved material consistency enable the laser to precisely follow its programmed cutting path. As a result, it generates finely detailed and accurate cuts that can meet the demands of engineering, manufacturing, and prototyping.
5. Reduced Post-Processing Requirements
Many hours of post-processing can be saved if you vapor-smooth PLA. The improved surface finish reduces imperfections, eliminating the need for extensive sanding or surface treatments. Consequently, the production process becomes more efficient, enabling quicker turnaround times while maintaining the high quality of the final laser-cut parts.
6. Time and Cost Savings
Industrialists and home users alike benefit from time and cost savings by incorporating vapor smoothing into the laser cutting pipeline. This technique streamlines the production process, reducing the need for labor-intensive post-processing. The smoother surface achieved through vapor smoothing results in superior part finishes, minimizing material waste and maximizing efficiency in both small-scale projects and large-scale manufacturing operations.
What Are the Disadvantages of Using Vapor Smoothing PLA in Laser Cutting?
Disadvantages of vapor smoothing PLA before laser cutting include:
1. Material Compatibility
Not all types of PLA filaments react the same to the smoothing process. Certain variants might exhibit varying responses, leading to problems like surface defects or altered material properties. Consequently, careful selection of compatible PLA materials is essential to ensure optimal results and avoid any adverse effects on the laser-cut parts.
2. Increased Laser Power Requirements
The smoothing process adds a little heat resistance to the plastic, so vapor-smoothed PLA might need extra laser power during cutting. This increased power requirement may limit the efficiency and speed of the laser-cutting process. You must balance laser parameters to fit both your productivity needs and the material’s limitations.
3. Increased Risk of Melting or Deformation
There are inherent risks of melting or deformation associated with vapor smoothing PLA once it gets to the laser cutting stage. If not precisely controlled, the smoothing process can make the material more susceptible to these issues. Melted or deformed parts often don’t have the same structural integrity parameters as pristine parts. Monitor and control your laser parameters carefully to avoid adverse effects.
4. Limited Compatibility With Intricate Designs
Generally speaking, vapor-smoothed PLA can only achieve a certain level of intricacy in its structures and thin features. The smoothing process can soften or distort these intricate elements, potentially compromising the precision of the laser-cut parts. Designers and manufacturers must carefully consider the complexity of the intended design and assess the compatibility of vapor smoothing with follow-on processes like laser cutting.
5. Additional Post-Processing Considerations
Companies involved in vapor smoothing PLA must be mindful that, even though it reduces the need for post-processing, the parts still may need certain finishing steps. Some items should be cooled or annealed after laser cutting in order to counter the effects caused by the smoothing process. Proper cooling and annealing processes can help ensure that the final laser-cut parts maintain the structural integrity and properties that you expect.
6. Safety Precautions and Ventilation
Vapor smoothing PLA generates fumes that can pose health risks to operators, necessitating a few simple safety measures. A well-ventilated working environment, for example, helps prevent the accumulation of potentially harmful fumes. By prioritizing safety, companies can protect their employees and ensure a secure working environment during both the smoothing and laser-cutting processes.
How To Smooth 3D Prints Using Vapor Smoothing PLA
Vapor smoothing PLA starts by placing the printed object in a controlled chamber. When a solvent vapor is added, the PLA material reacts with it to produce a chemical melt that smoothes out surface flaws. The procedure gives the 3D-printed object a glossy and elegant appearance, improving its overall quality and visual appeal.
How Does Laser Cutting PLA Objects That Have Been Vapor Smoothed Compare to Those That Haven't?
Laser cuts on PLA objects that have been vapor smoothed generally come out with better edge definition and fewer imperfections than those made on unsmoothed items. The smoother surface allows the laser to cut with greater precision and produces cleaner and more refined edges.
Can Any PLA 3D Print Be Vapor Smoothed?
Yes, all PLA 3D prints can be vapor smoothed. Ethyl acetate vapor rapidly smooths PLA prints by dissolving the surface layer, creating a smoother finish. The process involves placing the print in a vapor chamber containing ethyl acetate. However, caution must be exercised as the temperature and exposure time can affect the resulting appearance and structural integrity.
To learn more, see our guide on 3D Printer Capabilities.
What Is the Difference Between Vapor Smoothing PLA and Acetone Vapor Smoothing?
The processes for vapor smoothing PLA with acetone and other vapor smoothing solvents, such as ethyl acetate, are distinct. For ABS (acrylonitrile butadiene styrene), acetone vapor smoothing works well, but it might not be the best solution for PLA. Instead of simply dissolving PLA, acetone may potentially degrade it, turning it rubbery and sticky. It can sabotage PLA prints' strength and surface quality. Acetone is safe when used with the proper PPE to smooth ABS.
Summary
This article presented vapor smoothing PLA, explained what it is, and discussed its various advantages. To learn more about vapor smoothing PLA, contact a Xometry representative.
Xometry provides a wide range of manufacturing capabilities and other value-added services for all of your prototyping and production needs. Visit our website to learn more or to request a free, no-obligation quote.
Disclaimer
The content appearing on this webpage is for informational purposes only. Xometry makes no representation or warranty of any kind, be it expressed or implied, as to the accuracy, completeness, or validity of the information. Any performance parameters, geometric tolerances, specific design features, quality and types of materials, or processes should not be inferred to represent what will be delivered by third-party suppliers or manufacturers through Xometry’s network. Buyers seeking quotes for parts are responsible for defining the specific requirements for those parts. Please refer to our terms and conditions for more information.
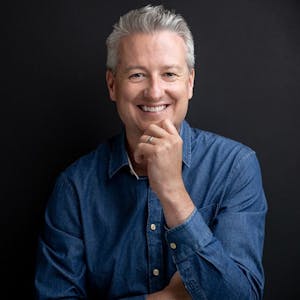