A heat sink is a device used to transfer heat from a heat source to the surrounding environment. Heat transfer is achieved through a combination of conduction, convection, and, to a lesser extent, radiation. A heat sink typically has a base with multiple fins on top, designed to increase the surface area for heat transfer to the surrounding fluid. They can be cooled either passively (using natural convection) or actively (with forced convection from a fan or pump).
This article will describe what a heat sink is, how it works, the various components that make up a heat sink, and some common applications of heat sinks.
What Is a Heat Sink?
A heat sink is a type of heat exchanger used to transfer heat from a heat-producing device or heat source into a surrounding fluid. This fluid is commonly air, but can also be water in sealed loops or specialized non-conductive thermal transfer fluids, such as glycol mixtures or dielectric oils. Cooling can occur passively through natural convection or actively through forced airflow, typically from a fan. Heat sinks are commonly made from copper or aluminum.
What Does a Heat Sink Look Like?
A common type of heat sink is shown in Figure 1 below:
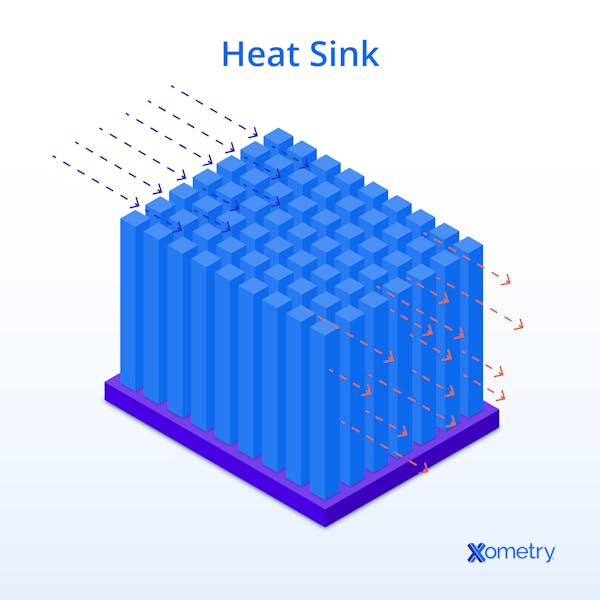
How Does a Heat Sink Work?
A heat sink makes use of the principles of conductive, convective, and radiative heat transfer to move heat from a hotter source to a lower-temperature fluid. Heat is conducted from this source into the sink. Heat sinks are made from materials with high thermal conductivity, such as copper or aluminum, allowing them to quickly conduct heat away from the source. This heat then transfers from the sink into the surrounding fluid via convection and radiation. The heat transfer rate is increased by having a large surface area in contact with the heat exchange fluid. Surface area can be dramatically increased by cutting fins into the heat sink base material.
Depending on cooling demands, heat sinks function either through natural convection (passive cooling) or forced convection provided by a fan or liquid pump (active cooling).
What Is the Purpose of a Heat Sink?
A heat sink is designed to dissipate waste heat caused by the operation of electrical or mechanical devices. This waste heat can accumulate and cause failures or degrade performance if not removed.
What Are the Key Components of a Heat Sink?
A heat sink is a relatively simple device. Listed below are the five components that make up a typical heat sink:
1. Base
A heat sink base is typically a flat block or sheet of material with excellent thermal conductivity. The base typically has a consistent cross-sectional thickness, but it can also be designed to have a cross-sectional profile that optimizes heat transfer for the specific geometry of the heat source. The base is typically mounted to the heat source with mounting hardware and thermal paste.
2. Fins
Fins protruding from the heat sink base are responsible for the transfer of heat to the surrounding fluid. These fins increase the heat sink's surface area in contact with air or coolant, which enhances the rate of heat dissipation.
The fins can either form an integral part of the base or can be attached separately using various techniques, for example, via a compression process. The shape and arrangement of the fins can dramatically improve the heat transfer rate.
3. Heat Pipes
A heat pipe is designed to transfer heat along its axis. Heat pipes can be incorporated inside standard heat sinks and heat spreaders through press fitting, soldering, and thermally conductive epoxy to improve their heat transfer efficiency. They work by transferring heat via a phase change mechanism that causes fluid to vaporize at the heat source, then travel along the axis of the heat pipe to the point where it cools down and changes back into a liquid via condensation.
4. Thermal Interface Material
Thermal interface materials, or thermal pastes, are used to significantly improve heat transfer between the heat source and the base of the heat sink by filling any air voids between the heat source and the heat sink. Air is a poor conductor of heat, so filling air gaps with a more thermally conductive material enhances the cooling efficiency of a heat sink. Thermal pastes can be ceramic, metal-oxide, or silicone-based. Metal-based thermal pastes offer high thermal conductivity but are electrically conductive and should be used with caution near sensitive components.
5. Mounting Hardware
Heat sinks can be securely fixed to their target heat sources using a number of different mounting methods. For smaller heat sinks, an adhesive with high thermal conductivity is used to directly stick the heat sink onto a heat source. This method is typically used on smaller PCB components. For larger heat sinks, normal screws can be used, or alternatively, spring-loaded push pins are used to optimize the contact pressure between the heat source and the heat sink.
What Materials Are Heat Sinks Made Of?
Heat sinks are made from materials with high thermal conductivity. The most common of these are listed below.
- Aluminum: Aluminum is a lightweight, low-cost material with good thermal conductivity. It is commonly used in heat sinks for electronic devices, such as computers and LED lights.
- Copper: Copper has excellent thermal conductivity and can be used on more sensitive components like computer CPUs.
- Aluminum Alloys: Pure aluminum is soft and difficult to machine, so aluminum alloys are often used. High-purity alloys like 1050 retain excellent thermal conductivity, while stronger alloys like 6061 offer improved mechanical strength at the cost of reduced thermal conductivity.
- Graphite: Certain forms of engineered graphite, like pyrolytic graphite, have very high in-plane thermal conductivity, rivaling or exceeding copper, and are significantly lighter. However, bulk or isotropic graphite has lower thermal performance.
- Diamond: Diamond has much higher thermal conductivity than copper and is used in specialized semiconductor applications. However, its high cost limits it to niche uses such as high-performance heat spreaders or laser diode cooling.
What Are the Types of Heat Sinks?
There are three basic types of heat sinks. They are described in more detail below:
1. Passive Heat Sinks
A passive heat sink is the simplest type of heat sink. It is simply a base with fins. Heat is transferred primarily through natural convection. As the air around the fins heats up through conduction, the hot air rises, causing cooler air to replace it. This is a continuous process. These types of heat sinks are not the most effective.
2. Hybrid Heat Sinks
A hybrid heat sink makes use of a control system to decide when to employ passive or active behavior. When the heat source produces low levels of heat, the fan or pump is not turned on, because natural convection is sufficient to transfer the required amount of heat away from the heat source. When natural convection is not adequate, the fan is activated, and forced convection helps to increase the amount of heat transferred away from the source.
3. Active Heat Sinks
An active heat sink makes use of forced convection to transfer heat. When a fan or pump causes fluid flow over the heat sink, this constant flow keeps replacing the hot fluid around the heat sink with cooler fluid. The higher the flow rate, the higher the heat transfer rate. Active heat sinks are more effective than passive heat sinks.
What Are the Applications of Heat Sinks?
Heat sinks are used wherever waste heat has the potential to damage equipment. Some examples are listed below:
1. Computer Processors
Computer processors (CPUs) produce a large amount of waste heat during operation. CPUs often use active cooling systems with copper heat sinks to manage high thermal loads during operation. Cool CPUs can operate more effectively.
2. LED Lighting
LED lights don’t emit much radiant heat like incandescent bulbs, but the LED junction itself generates significant thermal energy during operation. This heat must be dissipated, typically through passive heat sinks in smaller LEDs.
3. Power Electronics
Power electronics like AC–DC converters generate waste heat from components such as MOSFETs and voltage regulators. Aluminum heat sinks are commonly used in these applications, sometimes combined with active fans for more demanding thermal loads.
4. Automotive Industry
Apart from the heat sinks used on the control circuitry of vehicles, heat sinks are also used to keep electric motors cool during operation as well as to cool onboard chargers for electric vehicles.
5. Aerospace Industry
Aerospace systems use heat sinks in control circuitry and onboard electronics. In spacecraft, where there is no atmosphere for convection, specialized heat sinks radiate heat into space using high-emissivity surfaces and often include heat pipes to transport heat to radiators.
6. Consumer Electronics
Consumer electronics make extensive use of heat sinks to keep devices cool and operating efficiently. Typical examples include the heat sinks in computers and cell phones.
What Devices in a Computer Use Heat Sinks?
Many components within a computer make use of heat sinks. For example, the CPU (central processing unit) and GPU (graphical processing unit) commonly use heat sinks to improve efficiency and operating life. High-performance RAM modules and internal components of the PSU may also incorporate heat sinks, depending on thermal requirements. Individual SMDs (surface-mounted devices) on the motherboard may also use small heat sinks to stay cool.
How Do I Choose the Right Heat Sink for My Application?
In order to select the correct heat sink for your application, it is important to understand how much heat your device will be producing, as well as the environment in which it will operate. Once these are known, the heat sink can be designed by calculating the heat transfer rate required to keep your device at the optimal temperature and then designing a heat sink configuration to achieve this temperature.
What Are the Benefits of Heat Sinks?
Listed below are some common benefits of using heat sinks:
- Improved Reliability: Heat sinks help maintain a consistent operating temperature, which helps improve the reliability of a device.
- Extended Lifespan: Heat sinks remove waste heat from a device that would otherwise reduce its lifespan.
- Improved Performance: Devices like CPUs, for example, operate most effectively when cool. An effective heat sink can improve the performance of a device.
- Reduced Noise: If a passive heat sink can be used, then a cooling fan may not be necessary. This will ultimately reduce the noise of the device.
- Cost Savings: Heat sinks improve thermal management, which can extend component lifespan and reduce the need for additional cooling systems, contributing to potential savings in system design and maintenance costs.
What Are the Limitations of Heat Sinks?
Listed below are some common limitations of using heat sinks:
- Limited Cooling Capacity: Because of space and material limitations, a heat sink can only remove heat at a certain rate. Trying to make heat sinks that will remove even more heat even faster becomes impractical and uneconomical.
- Space Constraints: In some cases, the space needed for a suitable heat sink can be larger than the space available.
- Maintenance Requirements: Heat sinks, especially inside a PC, often accumulate dust. They must be regularly cleaned to prevent a drop in the heat transfer rate.
- Noise: Active heat sinks may require a noisy fan to operate effectively. Even silent fans will add a degree of noise.
- Cost: Copper heat sinks are effective but expensive and may not be economically feasible for the device. Cheaper materials like aluminum are available but might not have the same performance as copper.
What Are the Factors That Affect a Heat Sink’s Performance?
A heat sink's performance can depend on a number of factors, as explained below:
- Thermal Conductivity: The thermal conductivity of the heat sink material is one of the most important factors affecting performance. Materials with higher thermal conductivity, such as copper or diamond, can transfer heat away from the electronic component more efficiently.
- Fin Design: Increased fin count generally improves heat transfer by increasing surface area, but overly dense fins may hinder airflow and reduce performance.
- Airflow: Heat is removed from the heat sink by the action of natural or forced convection. The higher the rate of airflow around the fins of the heat sink, the higher the rate of heat transfer.
- Thermal Resistance: Resistance to heat transfer at the interface between a heat source and its heat sink can be caused by the existence of air gaps between components. Using thermal paste at the interface helps reduce thermal resistance by eliminating insulating air pockets.
- Ambient Temperature: A higher ambient temperature will result in a smaller temperature gradient between the heat source and the surrounding fluid. This will reduce the performance of the heat sink.
Common FAQs About Heat Sinks
Do Heat Sinks Cause Heat Creep in 3D Printing?
No, a heat sink is designed to eliminate heat creep in 3D printing. It transfers heat from the hot end to the surrounding air and prevents it from creeping up the extruder assembly.
What Is the Difference Between a Heat Sink and a Heat Spreader?
A heat sink typically includes a base and fins and dissipates heat into the surrounding fluid, often aided by convection. A heat spreader, on the other hand, does not significantly dissipate heat but instead redistributes it over a larger surface area to reduce local hot spots and facilitate transfer to another cooling component, such as a heat sink, cold plate, or system chassis.
Summary
This article presented heat sinks, explained what they are, and discussed how they work. To learn more about heat sinks, contact a Xometry representative.
Xometry provides a wide range of manufacturing capabilities, including 3D printing and other value-added services for all of your prototyping and production needs. Visit our website to learn more or to request a free, no-obligation quote.
Disclaimer
The content appearing on this webpage is for informational purposes only. Xometry makes no representation or warranty of any kind, be it expressed or implied, as to the accuracy, completeness, or validity of the information. Any performance parameters, geometric tolerances, specific design features, quality and types of materials, or processes should not be inferred to represent what will be delivered by third-party suppliers or manufacturers through Xometry’s network. Buyers seeking quotes for parts are responsible for defining the specific requirements for those parts. Please refer to our terms and conditions for more information.
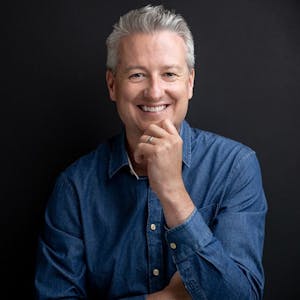