3D printing infill is something you should definitely know about if you’re interested in 3D printing and how it works. In this article, we’ll take a look at infill—something Xometry offers many different options for—as well as its purpose and how to choose the best pattern for your 3D print.
What is 3D Printing Infill?
Infill is the inside of an FDM (fused deposition modeling) 3D-printed part—the bit that fills the volume. It’s useful in many ways but some of the key reasons why it’s important are that it balances things like the part’s weight, strength, and the printing time. Of course, the pattern can be changed to whatever you like, but many basic designs come as standard in slicing software.
A lot of the time, you’ll find that you won’t need to completely fill the inside of a part to keep its strength or integrity, and that’s why using infill is great. It saves on material and time (because it’s printed faster and is usually thinner than the outside) and can still be strong and durable. We have a guide on everything you need to know about 3D printing, which we highly recommend you check out. At Xometry, we offer three main types of infill: solid, light, and ultralight. The image below shows these in that same order:
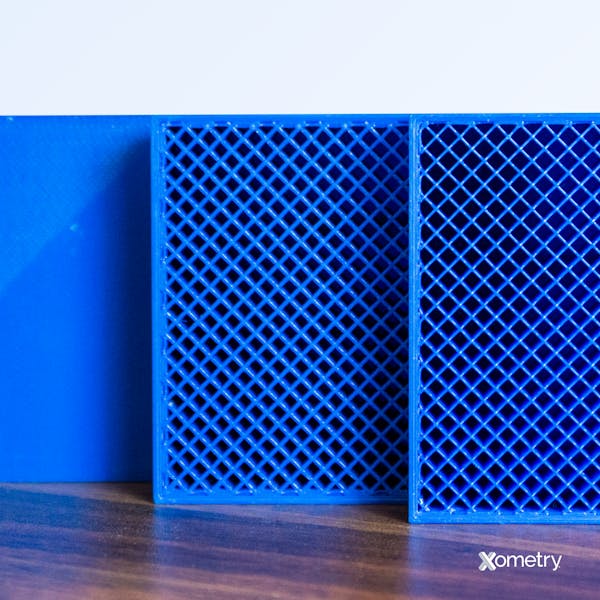
Generally, the more infill is used, the higher the density of the part. A typical FDM 3D-printed part will consist of an outer shell with a thickness that’s been predetermined, and inside, it will have the evenly distributed infill, which won’t be visible at all when the part is complete.
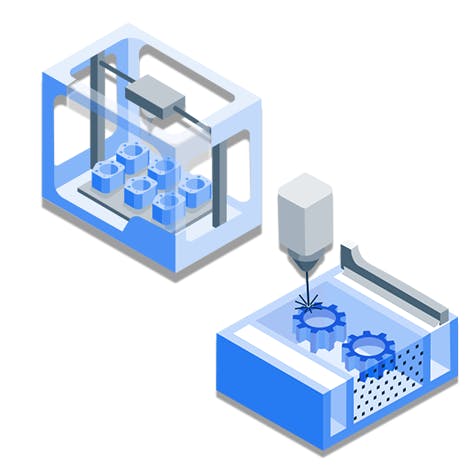
Infill Patterns
When it comes to patterns for your infill, there are several to choose from, and settling on one doesn’t just come down to how pretty it looks. The patterns might have the same or similar end result of reducing time spent and material used, but your decision will ultimately be dependent on the shape of the part you want to print—some patterns are better suited to certain shapes, while others aren’t.
Line
The line pattern is made up of multiple parallel lines per layer. Once each layer is done, the printer will start the next layer by printing the new lines at a 90-degree angle from the previous ones, which means the lines don’t actually cross over each other on the same layer. This pattern will strengthen the part in two dimensions and is slightly quicker to print than grid and triangular patterns. Here’s an example of line infill:
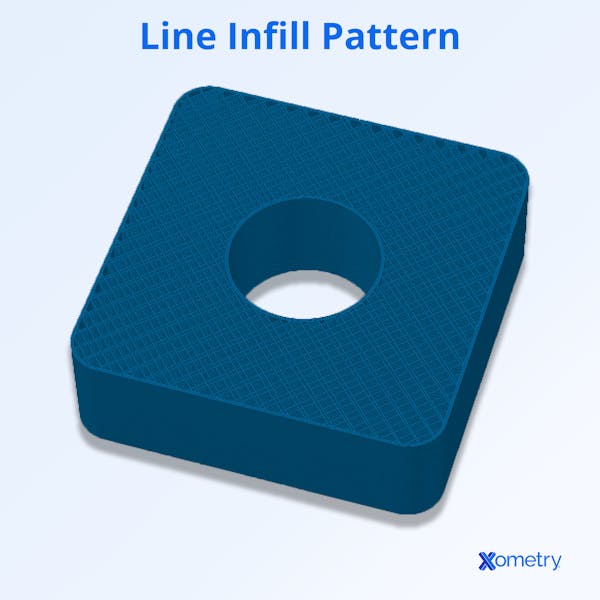
Gyroid
This consists of alternating wavy lines, and naturally, it takes a while to print. But it’s all worth it, because this pattern allows for almost isotropic mechanical properties, strengthening the X- and Y-axis shear strength, although the Z-axis can still remain somewhat weak. That’s why the gyroid pattern works great with flexible materials.
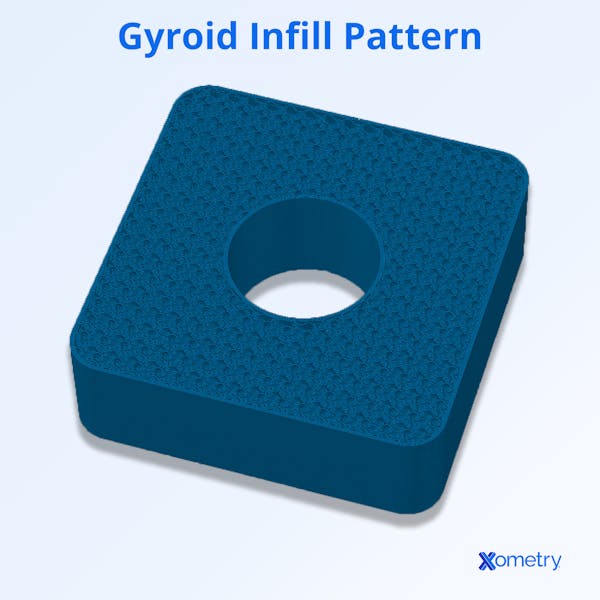
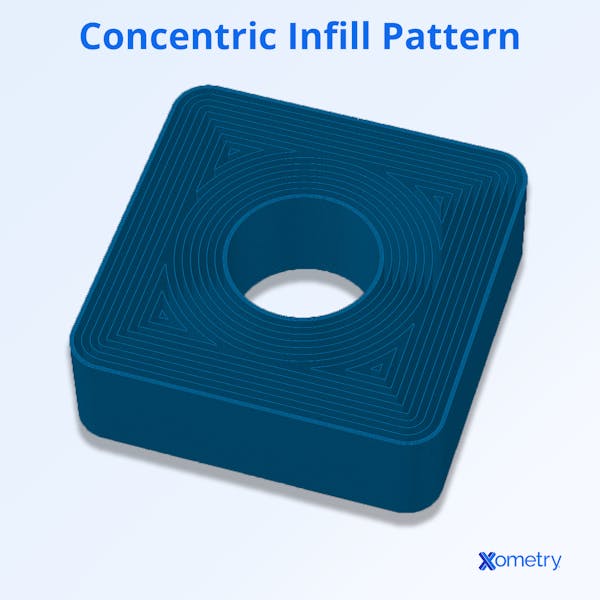
Lightning
It might sound cool, and it’s actually the quickest to print, but the lightning pattern isn’t very strong. As it prints, lightning bolt-shaped supports are added only where needed instead of evenly and all over the part. Parts with this pattern can be described as shells with a few supports in areas that need some extra help, like horizontal features or internal overhangs.
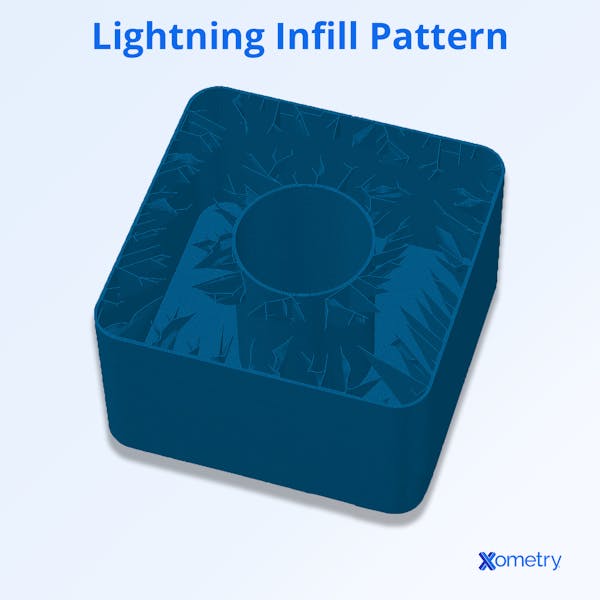

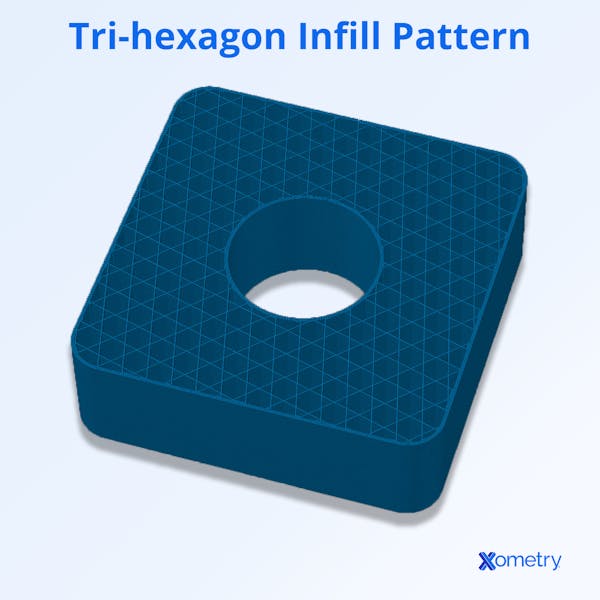
Cubic
This pattern creates strong, little 3D cube-shaped cells within the part, built layer-by-layer, with each layer slightly offset from the one below. This offsetting makes the cubes look like they’re stacked on a corner, and it’s great for creating a balanced part that’s strong in all directions.
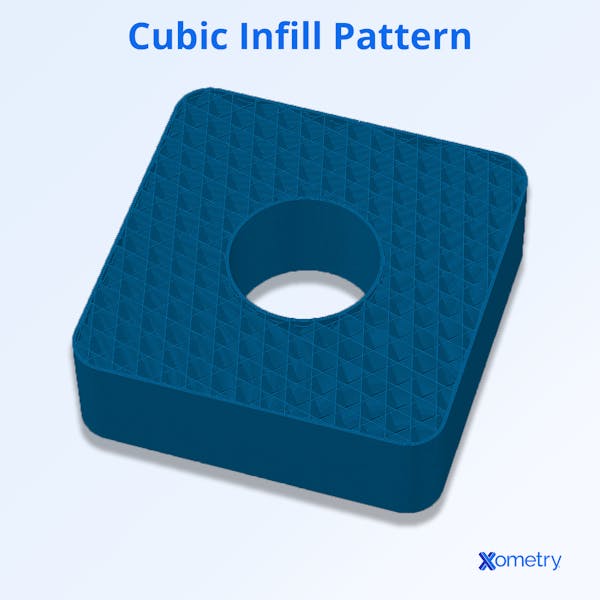
Grid
The grid is the closest infill pattern to what we use the most for our FDM prints here at Xometry and is one of the most common around. The pattern is a grid with lines that cross over themselves at 90 degrees. It’s good for large, flat surfaces but could get some nozzle clogging—especially if you’re printing with a desktop FDM printer.
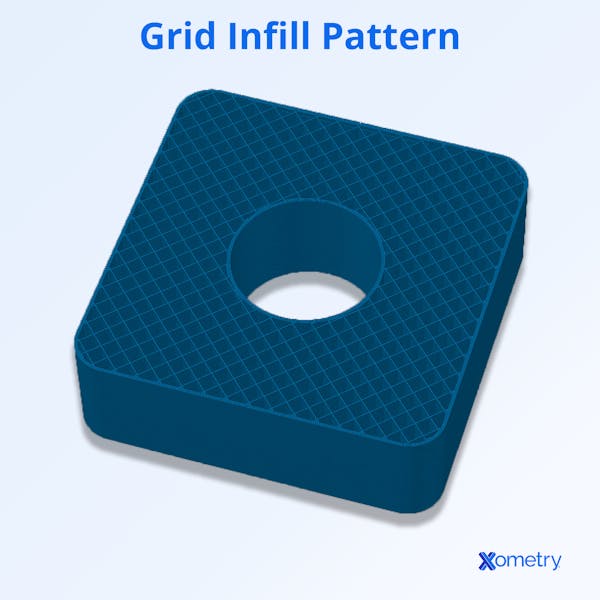
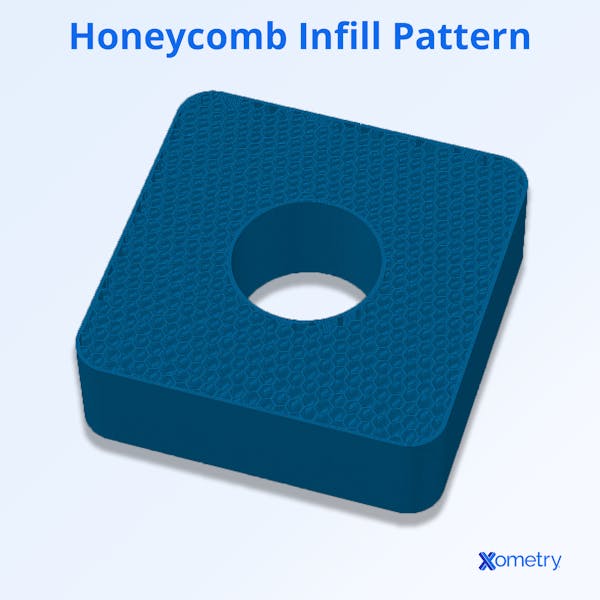
How do I Choose the Best Type of Infill?
There’s quite a bit of trial and error when it comes to choosing the best pattern for your infill. Don’t let that dissuade you—go ahead and do as many test runs as you need to find the perfect one. There are a few things you can keep in mind to reduce the amount of duds you produce. Firstly, if you need the part to be strong and durable, it’s better to go for a pattern made for the task, like the honeycomb. For display models, you could go for the lightning, which uses very little infill. You can also choose this one if you’re strapped for time and need the part pronto. If you’re still in doubt about which one to settle on, you can always use a simple pattern, like the grid or line, and take it from there.
What infill percentage should I use?
Deciding on how much infill to use ultimately depends on what you’ll be using your 3D-printed part for. If you’re making a prototype or a model as a hobby, you’ll rarely ever need more than 20% infill. But if you’re making a functional part that will undergo mechanical stress loads, you’ll be better off with an infill percentage of 50% or even more. The same goes for parts with flat, horizontal surfaces; more infill will be needed as support so the top layer doesn’t sag.
As a general rule of thumb, the higher the infill percentage, the stronger the part, but there are a few other factors that can affect the part’s strength, like the material and the print direction. Most FDM parts are anisotropic because they tend to be weaker along the Z-axis (the height) as the layers don’t stick together as strongly in that direction. If you need a part to bear weight, we recommend building the part so that the weight will fall on the XY plane where the bonding is stronger. For heavy-duty use, you may as well use a solid 100% infill—something we offer at Xometry. Keep in mind that even FDM parts with a solid infill can show signs of porosity because of tiny gaps between the layers.
Can I Use Multiple Infill Patterns or Percentages in One Print?
The short answer is yes. Many slicer programs give you the option for a variable infill or adaptive infill, which allows you to adjust the pattern and density in different areas of the print. It’s good for complex prints that need to be stronger in certain areas but not so much in others.
How Xometry Can Help
If you have any questions about infill or 3D printing in general, one of our representatives would be more than happy to help. Xometry also offers a huge range of industrial-grade services, including metal and full-color 3D printing. Best of all, it’s super quick and easy to get a quote, so feel free to upload your files to the Xometry Instant Quoting Engine® to get started!
Disclaimer
The content appearing on this webpage is for informational purposes only. Xometry makes no representation or warranty of any kind, be it expressed or implied, as to the accuracy, completeness, or validity of the information. Any performance parameters, geometric tolerances, specific design features, quality and types of materials, or processes should not be inferred to represent what will be delivered by third-party suppliers or manufacturers through Xometry’s network. Buyers seeking quotes for parts are responsible for defining the specific requirements for those parts. Please refer to our terms and conditions for more information.
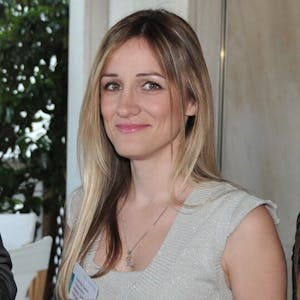