Pad printing and screen printing are two different methods of printing that are used for a variety of products and on a variety of different materials. Screen printing is used on textiles, ceramics, wood, glass, metal, paper, and plastic. It can be used for balloons, decals, clothing, medical devices, product labels, signs and displays, printed electronics, and fabrics. Pad printing is used on plastic, glass, metal, rubber, and wood. It can be used for medical devices, candy, pharmaceutics, cosmetic packaging, caps and closures, hockey pucks, TV and computer monitors, apparel such as t-shirts, and letters on computer keyboards. This guide explains how the two processes work and provides a contrast to enable insight as to which may be the best alternative for use.
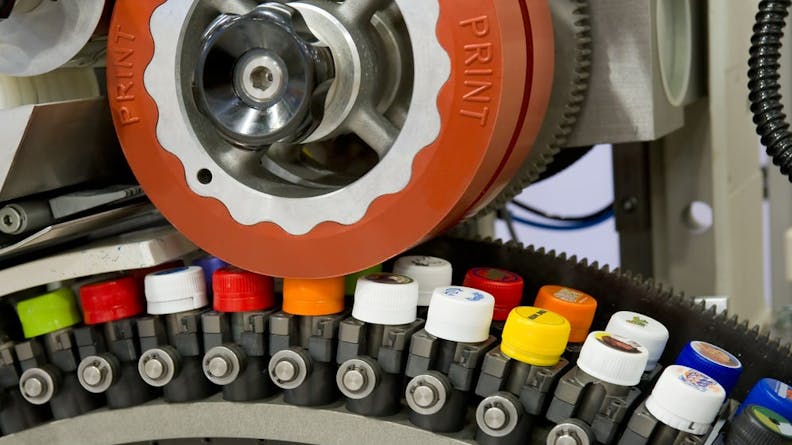
A pad printing machine.
Image Credit: alterfalter/Shutterstock.com
What is Pad Printing?
Pad printing transfers a 2-D image onto a 3-D object using an indirect offset, gravure, printing process using an image transmitted from the cliché via a silicone pad onto a substrate. It is used to print on otherwise difficult to print on products in many industries, including medical, automotive, promotional, apparel, electronic objects, sports equipment, appliances, and toys. It can also deposit functional substances such as conductive inks, lubricants, and adhesives.
Physical changes within the ink film both on the cliché and on the pad let it leave the etched image area and adhere to the pad, then release and adhere to the substrate. The distinctive properties of the silicone pad allow it to pick images up from a flat plane and transfer them to a variety of surfaces, such as textured, concave, or convex surfaces.
The pad printing process has developed quickly in the past 40 years and is now one of the most essential printing processes. The use of silicone rubber was crucial to its success as a print medium because it allows easy deforming, is ink repellent, and ensures an excellent ink transfer.
Pad printing begins with the artwork for design being etched onto a base plate. Then, the etched area of the base plate or cliché is filled with ink. A closed ink cup removes any residue/excess ink on the surface.
Next, a flexible silicone pad is pressed onto the base plate, and the inked artwork transfers onto the pad. Finally, the pad is pressed onto the material being printed.
The silicone printing pad works as a transfer vehicle, picking up ink from the ink plate and transferring it to the part. Pads vary in shape and diameter depending on their application.
There are two main shapes for pad printing pads. There are round pads, and long narrow pads called bar pads. There are three size categories within both the pad groups: small, medium, and large pads. Custom-shaped pads can also be created to meet particular application requirements.
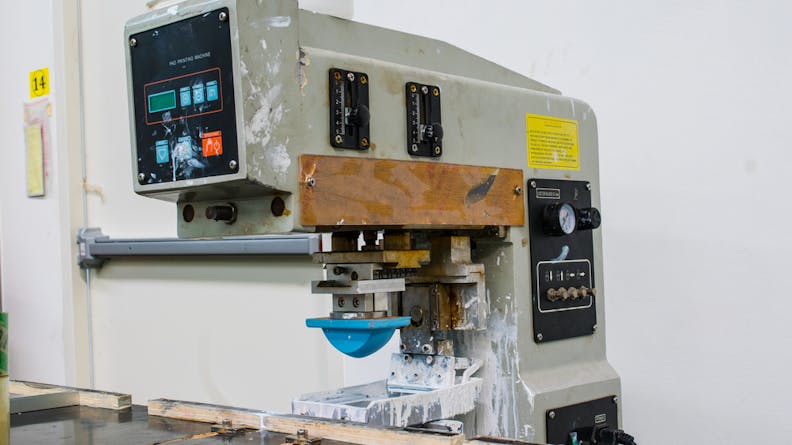
An automated pad printing machine.
Image Credit: Chaowalit/Shutterstock.com
Types of Pad Printing
Pad printing can be categorized by the pad printing machine or method used.
Open Inkwell System
Open ink well systems, the older pad printing method, uses an ink-trough for the ink supply that is located behind the printing plate. A flood bar presses a pool of printing ink over the plate, and a doctor-blade removes the ink from the plate surface and leaves ink on the etched artwork area ready for the pad to pick up.
Sealed Ink Cup System
Sealed ink cup systems use a sealed container for the ink supply, flood bar, and doctor blade all at the same time. A ceramic ring with a highly polished working edge creates the seal against the printing plate. The ink lying on the plate is drawn back into the ink reservoir by a blade. In a sealed ink cup system, the ink cup glides from its position over the printing image. The ring blade takes off the excess ink in the process. As a result, the printing ink only remains in the depressions of the plate.
Pros and Cons of Pad Printing
One of the main advantages of pad printing is that it prints on three-dimensional surfaces and products of all shapes and sizes. Many companies run their pad printing operations in-house, as set-up costs are relatively low. Other advantages are that a pad printing machine doesn't take up much room, and the process is relatively simple and easy to learn.
While pad printing is ideal for achieving accurate results, one disadvantage is that it is limited in terms of speed. Multiple colors must be applied separately, so registration is a slight risk. The size of the motive is also limited by the pad, plate, and efficiency of the pad printer.
What is Screen Printing?
Screen printing involves creating an image by pressing ink through a stenciled mesh screen to create a printed design. It's a widespread technique used in a wide range of different industries. The process is sometimes called serigraphy, silk screening, or silk screen printing, but these names refer to essentially the same method. Screen printing can be used with nearly any material, even with substrates that have uneven or round surfaces.
The screen utilized in screen printing is made of a piece of mesh stretched over a frame. Traditionally, silk was used in the process. In modern times, synthetic threads such as nylon or polyester are usually employed in the screen printing process. A finer and smaller aperture for the mesh is used for a design that needs a higher and more delicate degree of detail.
Different types of mesh size determine the outcome and look of the finished design on the material. For the mesh to be effective, it is mounted on a frame and is placed under tension. The mesh frame can be made of different materials, such as wood or aluminum. The tension of the mesh is checked using a tensiometer.
Screen printing stencils are created by blocking off parts of the woven mesh screen in the negative image of the design to be printed, so the open spaces are where the ink will appear on the substrate.
Before printing, the frame and screen must go through a pre-press process. An emulsion is 'scooped' across the mesh. Once it dries, it is selectively exposed to ultra-violet light through a film printed with the required design, hardening the emulsion in the exposed areas but leaving the unexposed parts soft. A water spray washes them away, leaving a clean space in the mesh with the same shape as the desired image, allowing the passage of ink.
The screen printing process is relatively simple and involves a blade or squeegee moving across the screen and filling the open mesh apertures with ink. A reverse stroke then forces the screen to touch the substrate briefly along a contact line. The ink wets the substrate and pulls out of the mesh apertures as the screen springs back after the blade passes. One color is printed at a time, meaning several screens are needed to create a multicolored image or design.
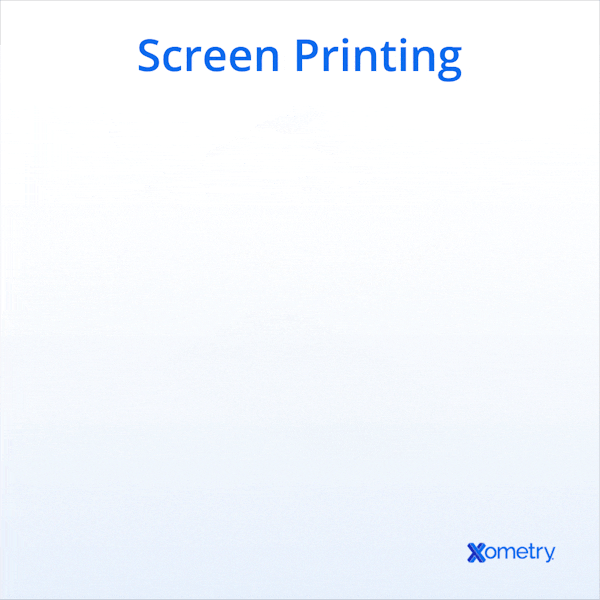
Types of Screen Printing
Screen printing is done by hand or machine, but the basic process is always the same. The differences are in the printing ink used, its rendered effect, and the printed surface.
Spot Color Screen Printing
The most commonly used screen printing technique is spot color screen printing. It uses the ink’s stock color by printing it through the stencil of the mesh. This technique creates a vibrant solid spot of color and is much simpler than other screen printing methods.
Grayscale Printing
Grayscale printing is used for printing full-color images as one-color grayscales or half-tones. The print looks more detailed if the half-tone has more dots. It is not a black and white printing method but instead, pulls out the CMY or RGB or color scales only but in shades of gray. It is one of the more cost-effective screen printing techniques, often used for printing black and white designs onto fabrics.
Half-Tone Printing
In half-tone printing, single colors in gradients are printed. The entire process uses a single color of ink, and this color gets half-toned, creating a different shade when seen from a distance. It is best used to create a multi-color printing look without actually doing it. Half-tone printing is also a cost-effective method since only one color of ink is used.
Duotone Printing
Duotone printing uses two half-tones to print the same image with two colors. First, a black half-tone is printed with black ink, and then a second half-tone is printed with color ink. It is similar to sepia-toned print in photography and gives an artsy effect.
Simulated Process Printing
The simulated printing process combines the four-color printing process with spot color printing. Since this technique is ideal for lighter and darker shades, it is versatile and popular with people looking to produce photorealistic print detail.
CMYK (4-Color Printing)
CMYK is the most complex screen printing technique. It uses the four primary colors: cyan, magenta, yellow, and black. Then, these four colors are combined. It can be done manually but ideally should be performed using automated controls to achieve the best results.
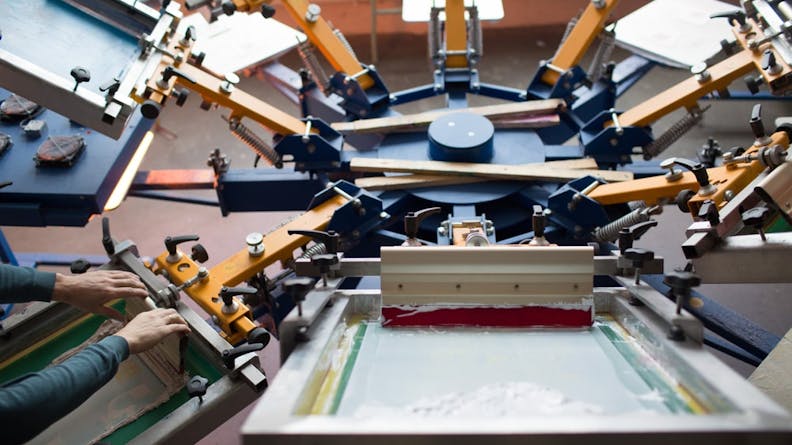
A silk screen printer in operation.
Max4e Photo/Shutterstock.com
Pros and Cons of Screen Printing
An advantage of screen printing is its flexibility with substrates. It is ideal for high print volumes, as the more products that need to be printed, the lower cost per item. Despite having a complex setup process, screen printing usually only needs to be set up once. Another advantage is that screen-printed designs are typically more durable than those produced using heat press or digital methods.
The disadvantages are that while screen printing is ideal for products in high volumes, it isn't as cost-effective to use for low volume production. In addition, the setup for screen printing is much more complicated than digital or heat press printing. It also takes much longer, so it usually has a slightly slower turnaround than other print methods. Finally, it also doesn't lend itself well for designing a wide range of colors or a photography-based design.
Pad Printing vs. Screen Printing
Pad printing, which uses a flexible silicone pad to transfer ink from an etched base plate onto the product, is ideal for moving a 2D image onto a 3D object. And it’s a particularly effective method for printing onto irregular, small objects such as keyrings and jewelry where screen printing may struggle.
But setting up and executing a pad printing job can be slower and more involved than screen printing, and pad printing is limited in its printing area as it can’t be used to print over a large area, which is where screen printing comes into its own.
One process isn’t better than the other. Instead, each is better suited to particular applications.
Screen Printing
Screen printing is best suited for large images on flat surfaces, large, two-sided images on cylindrical parts, and opaque images against light, dark or transparent substrates. It is more cost-effective because screen printing can be accomplished with one pass, and printing costs go up with each additional pass. It also is ideal for images that require only a single color.
Pad Printing
The pad printing process is best for images printed on complex materials like polypropylene, images that cover a raised or recessed area, images that cover any complex curves such as concave or convex, images that are near a vertical wall or obstruction, small image requirements, or for printing on smaller, metal parts, and multicolored images.
Summary
Are you in need of printing or part marking? Contact Xometry to get your quote for part marking, engraving, or other services. You can also learn more about the different types of part marking technologies by exploring our Ultimate Guide to Direct Part Marking. In that guide, you will find our guidelines around each process and further information on the types of markings we perform and what we'll do in case of missing information to ensure your order gets to you on time while remaining to your specifications.
Disclaimer
The content appearing on this webpage is for informational purposes only. Xometry makes no representation or warranty of any kind, be it expressed or implied, as to the accuracy, completeness, or validity of the information. Any performance parameters, geometric tolerances, specific design features, quality and types of materials, or processes should not be inferred to represent what will be delivered by third-party suppliers or manufacturers through Xometry’s network. Buyers seeking quotes for parts are responsible for defining the specific requirements for those parts. Please refer to our terms and conditions for more information.
Sources:
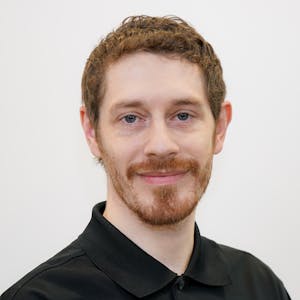