Plaster casting is a subset of investment casting. It uses plaster for the casting cavity, rather than a refractory (baked ceramic) material for the investment. This is a manufacturing process used to create intricate and detailed metal parts. It is reserved for relatively low-melting-point metals. Plaster casting is used in various industries and applications such as: aerospace, art, jewelry, and automotive.
Although plaster casting offers most of the advantages of investment casting, and a lower cost of mold production than refractory methods, it is poorly suited to high-volume production. Molds are relatively fragile which can create manufacturing difficulties and the time and cost associated with creating individual molds for each part is high. The process is not suited to all types of metals and applications, being restricted to lower-melting-point materials. So material selection and process compatibility are major factors in process selection.
This article will further discuss plaster casting, how it works, its advantages, disadvantages, and applications.
What Is a Plaster Casting?
A plaster casting (craft or industrial-made) produces a metal component. It is formed in a plaster cavity mold tool that has been cast around sacrificial master copies of a required part, made in plastic foam or wax. The pattern part is burned out of the plaster and the cavity is then charged with molten metal to make a close reproduction of the pattern.
What Is the Other Term for Plaster Casting?
Plaster casting is also commonly referred to as an investment, plaster mold, or lost wax casting. It differs from the more commonly employed process in that the investment is made from plaster rather than refractory clay.
What Is the History of Plaster Casting?
Plaster casting of metals has a long and storied history, covering thousands of years. The earliest evidence of this casting method is from Mesopotamia and Sumeria. It was progressively refined by ancient Egyptian craftsmen, then by Greeks and Romans. It fell into disuse as a technique in medieval Europe, being revived in the 15th and 16th centuries by various artists. In the late 19th century, advancements in technology, materials science, and manufacturing processes resulted in the later industrialization of investment casting. It suited various uses across numerous higher-value industries, including: aerospace, automotive, and medical sectors.
How Does Plaster Casting Work?
Plaster casting works by carving, casting, or 3D printing patterns. For larger volumes, it is common to make a steel cavity tool into which the wax can be cast. However, 3D printing directly in wax allows for more complex geometries that cannot be easily molded in a hard material cavity. In some cases, the master can be cut from or molded in polymer foam or expanded polystyrene. This is less common for short to medium production runs but offers a practical approach to the hand-making of one-off patterns. Whatever the method of manufacture of the master, elements such as fill sprues, feeders, and gas vents must be included in the master. This is done to make a finished cavity in a single-stage plaster mold.
Assembly may be required to join multiple patterns on a central wax tree or sprue, to allow multiple parts in a single pour. A hot iron can be used to fuse these parts together into a single whole to be invested. Alternatively, the multiple parts and all sprue/feeder/vent features can be 3D printed as a single body. The pattern and feeder structure are then coated with plaster or a plaster-silica mixture. This coating is cast in a flask to create a mold that is thick enough to withstand handling, which is then left to harden. During this phase, the partially hardened mold is heated to drive off the remaining moisture.
Burnout is the step in which the hardened investment mold is heated in a furnace to melt and remove the wax or plastic patterns. This leaves behind cavities that fully and precisely reflect the now-absent pattern. Charging is the step in which molten metal is poured into the empty cavity invested over the pattern. A good pattern layout allows the metal to flow into the finest sections of the cavity and fill the entire volume, plus all gas vent and feeder pathways. Cooling occurs fairly rapidly as the filled mold rests after charging. The metal will solidify and precisely reproduce the cavity into which it was poured. Breakout is the demold stage, in which the plaster is broken away, releasing the final metal part. The parts will require additional finishing, to remove the casting tool features at which fill and gas venting occurred, as these will be represented in metal in the raw cast. These connection points will need handwork to cut and grind the defect points. Additional post-work may be required in machining precision-fit points or surface finishing to polish.
How Does Plaster Casting Differ From the Other Types of Casting?
The differences between plaster casting and the range of other casting methods are either very minor or quite marked, depending on which is being considered. In comparison with traditional investment casting, the processes are essentially identical. The difference is that plaster casting lacks the refractory stage which makes a harder, tougher tool that can handle higher-temperature metals such as steel and titanium. Sand casting, on the other hand, is different in all regards in the forming of the mold. It uses packed or bonded sand. It can handle essentially all metals, from the lowest to the highest melting points. The end results with sand casting tend to be lower accuracy and lower repeatability than well-executed plaster casting. However, they can deliver one-off parts faster and with less effort/setup.
Finally, die-casting uses a steel, iron, or carbon cavity that can be pressure or gravity-fed. The tooling is also reusable for thousands of shots, with little to no preparation between shots. Depending on tooling quality and pressure of fill, die casting can range from lower precision than well-executed plaster casting to comparable quality results and potentially better in extreme cases.
To learn more, see our guide on the Different Casting Methods.
What Is the Importance of Plaster Casting in Manufacturing?
Plaster casting offers an essentially low-technology route to deliver high-technology results. This relies heavily on good pattern execution, skilled layout for flow and investment, and good control of fill conditions. The cost is slightly lower than refractory investment casting, but the quality of results is comparable. So, it is a somewhat lower cost and lower setup complexity method for achieving excellent, low-temperature metal part casting. The process is also better adapted to moderate-volume production than sand casting. It offers better quality parts in accuracy, the finesse of detail, and surface finish.
What Are the Uses of Plaster Casting?
Plaster casting is a high-precision manufacturing method that is ideally suited to manufacturing higher value and complex components in low-melting-point alloys. It finds application across many industry sectors in which a convergence of higher cost tolerance, complex geometry, fine-featured parts, and relatively low manufacturing volumes converge. This is applicable across medical and aerospace products, complex industrial equipment, satellite manufacture, artwork making, and competitive sporting/race equipment.
What Is the Quality of Plaster Casting Products?
“Quality” is a term that is open to interpretation, depending on the required outcomes and critical features. Plaster casting products, when produced properly, are generally high-quality products. Typical plaster casting surface finish is 0.9–1.0 Ra. For reference, pressure die casting delivers 0.8–0.9 Ra. Typical wall thicknesses of 1.5 mm are commonly achieved. Local sections over short distances of 0.5 mm are feasible in lower-melt-viscosity charge metals. Precision and repeatability in small parts of better than 0.1 mm are feasible with tight process control. Yield in a well-operated process should approach 100%. The manufacturing rate can be as high as 10 parts per hour of labor, although this is likely only in an ongoing and well-established production process.
How Long Do Plaster Casting Products Last?
Plaster cast parts are as durable as the design, usage, and material permit. Where the part is made in an application-appropriate material, metal parts can have a service life of decades. Jewelry and weapons that are thousands of years old can still be seen as serviceable! Where the applied loads exceed the design capacity of the part, rapid or fatigue fracture is likely to occur at any time. Where chemical conditions exceed the reactive resilience of the metal, either by acidic, alkali, or oxidative attack, use life will be foreshortened.
Can Plaster Casting Be Used To Make Jewelry?
Yes, the process is ideally suited to the finesse required for jewelry. In particular, the process cost is relatively high but results that are essentially unachievable by other means can be delivered by plaster casting. This can primarily be a result of: very fine features, or high repeatability in moderate production runs, or geometry that simply cannot be practically made by any other means.
Can Plaster Casting Be Used To Make Dental and Medical Equipment?
Yes. Plaster casting is ideally suited to the one-off production of dental implants, bridges, and other unique and patient-adapted parts. This is particularly true of precious metal (gold) components. Gold offers the biocompatibility required for patient contact and the low melting point that the process requires. Plaster casting is not capable, however, of making the high-strength and deeply implanted stainless steel and titanium alloy joint and spinal components that are often required in surgery.
How To Make a Plaster Mold?
Once a pattern with sprue, feeders, and gas vents has been created, creating a plaster mold for metal casting involves a series of steps. The process below describes a single component cast preparation:
- Set up the mold frame or flask around the pattern. It should be large enough to contain the pattern and allow space for sufficient thickness of the investment material.
- Follow the package instructions to mix the plaster with water. Use a clean container and stir thoroughly to ensure smooth consistency.
- Pour the mixed smooth and fluid plaster into the flask around the pattern. Minimize air bubbles by pouring smoothly and moderately, without a splash.
- Use a vibrating table or tool to gently vibrate the flask. This helps cause air trapped in the plaster and attached to the pattern to rise to the surface, producing a smoother and more complete cavity.
- Allow the plaster to harden. This may require several hours or longer, depending on the specific plaster material used and the section thickness.
- Place the cured mold in a furnace/oven to burn out the pattern.
- Before casting, preheat the mold in the furnace to ensure it's at or above the temperature of the charge you will be pouring into it.
Is the Plastic/Wax Pattern Reusable?
No, the nature of the process is that a seamless investment cast cavity is formed around the pattern/wax/plastic. The single-use pattern is then burned out of the cavity.
What Is the Step-by-Step Process of Plaster Casting?
Listed below is the step-by-step process of plaster casting:
1. Design the Tooling and Engineering
Parts must be prototyped either as cast or 3D printed wax. the addition of sprues, flow channels, support members, and vent pathways can also be included as an integrated and connected network.
2. Create the Tooling
Support the wax master within a pot or container known as a flask. The sprue should be at the upper edge of the flask so that the pour point remains open in the tool. With the master supported, fill the flask with the plaster mixture. The mixture should be made at a viscosity that is appropriate to allow all trapped bubbles to rise easily, but not so wet as to form a bad mold. With the flask filled with liquid plaster, some vibration is generally beneficial. This frees up stuck air bubbles and allows the plaster to fill and consolidate around the master. With the plaster cast and cured, remove the flask. Bake the cast to dry it out fully. Then raise the temperature to the level required to burn/vaporize the wax to leave the cavity empty and open.
3. Pour the Metal
The casting process involves preheating the hardened plaster mold to approximately the temperature of the intended liquid metal charge. The metal is then poured in a slow and steady stream to avoid entraining air in the flowing metal. The charged cast is then left to cool to a temperature that allows handling.
4. Extract the Cast Parts
With the casting cooled, the plaster can be broken up and cleared from the metal casting. This must be done without damaging or distorting the part.
5. Clean the Parts
Feeder and gas passage elements of the metal casting must then be cut off and any surface imperfections corrected as far as possible.
6. Perform Machining Tasks
Any precision machining that may be required will then have to be performed on the part. Post-machining tasks such as surface finishing or polishing will follow.
What Are the Metals Used for Plaster Casting?
Plaster casting is best suited to relatively low-melting-point metals and their alloys such as:
1. Zinc
Zinc is a low-melting-point element (420 °C) with a low viscosity when molten. This property allows it to fill thin sections and fine details. Various alloys contain zinc and benefit from its properties—brass (around 900 °C), and ZAMAK alloys (385 °C) among others. Zinc alloys are used for relatively small engineering components, benefitting from the ability to mold the thinnest sections.
To learn more, see our guide on ZInc Metal.
2. Copper Alloys
Copper has a fairly high melting point (1,084 °C), while its alloys have both lower and higher melting points—brass, bronze (977 °C), and cupronickel (1,200 °C). Copper alloys serve extensively in electrical and water handling equipment and in decorative objects of higher value, often plated with higher-value metals.
3. Aluminum
Aluminum is available in various alloys, with a range of properties. The pure metal melts at 659 °C and commercial alloys range from 453 to 666 °C. Aluminum alloys are widely employed in automotive and aerospace applications in which lightness, strength, and relatively low material cost are beneficial.
To learn more, see our guide on Raw Aluminum.
4. Magnesium
Magnesium is among the lowest density engineering metals. The pure metal melts at 650 °C, while alloys range from 360 to 650 °C. Magnesium alloys are harder to handle and cast for good quality, but provide the highest strength-to-weight ratio for applications in which weight is the critical factor.
What Are the Advantages of Plaster Casting?
Plaster casting offers several advantages including:
- Can reliably reproduce intricate details and complex shapes with high precision when well executed.
- Can deliver excellent surface finish, reducing the need for labor-intensive post-processing.
- Can be used with a wide range of lower temperature metals and alloys such as aluminum, bronze, magnesium, ZAMAK, brass, precious metals, and lead alloys such as pewter.
- Plaster is low cost, so the process suffers less material cost, particularly whenever the plaster is crushed and reused.
- It is cost-effective for small to medium production runs. It doesn't require expensive tooling, and the skills can be acquired with experience and moderate study.
- Designers have the freedom to create complex and customized parts without many of the geometric or fine detail limitations of other casting methods.
What Are the Disadvantages of Plaster Casting?
Plaster casting’s disadvantages are listed below:
- Is poorly suited to high-melting-point alloys such as stainless steel or titanium.
- The plaster investment mold is quite fragile compared to some other mold types.
- Is poorly suited to parts weighing more than 30–40 kg in the extreme, and creating large investment molds requires skill and care.
- Is labor-intensive and requires considerable skill, compared with some other casting methods.
- The investment mold is destroyed by demolding, so for each new pour a new mold must be created.
- While plaster casting can deliver a great surface finish, the consistency of this will vary with mold quality and post-processing after casting.
- There is a risk of porosity or trapped air in the final cast parts. The feed can become airlocked if the fill pathways are not appropriately laid out.
- An unsuitable choice for high-strength or high-performance metal alloys. The casting cavities are not sufficiently robust to tolerate the very high temperatures involved.
- While the surface finish and cast quality can be very good, parts produced through the process still require additional post-processing steps such as grinding, polishing, or machining.
Is Plaster Casting Expensive?
Plaster casting is a high-cost-per-part process in comparison with sand casting. It is both demanding of greater skill and considerably more labor intensive. It is lower cost than refractory-based investment casting and, for small production runs it is considerably lower cost per part than any of the die-casting process variants.
Is Plaster Casting Worth It?
Yes, whenever high precision or good surface finish out of the mold is required, plaster casting is a powerful and capable process. Although the effort per part can be relatively high, the ability to deliver very high-quality and repeatable components in moderate volumes is a valuable asset. For appropriate parts in achievable materials, with complex geometries and fine details that must be reproduced, plaster casting is a capable and widely utilized process that delivers economically competitive outcomes.
Summary
This article presented plaster casting, explained it, and discussed its various applications and advantages. To learn more about plaster casting, contact a Xometry representative.
Xometry provides a wide range of manufacturing capabilities, including casting and other value-added services for all of your prototyping and production needs. Visit our website to learn more or to request a free, no-obligation quote.
Disclaimer
The content appearing on this webpage is for informational purposes only. Xometry makes no representation or warranty of any kind, be it expressed or implied, as to the accuracy, completeness, or validity of the information. Any performance parameters, geometric tolerances, specific design features, quality and types of materials, or processes should not be inferred to represent what will be delivered by third-party suppliers or manufacturers through Xometry’s network. Buyers seeking quotes for parts are responsible for defining the specific requirements for those parts. Please refer to our terms and conditions for more information.
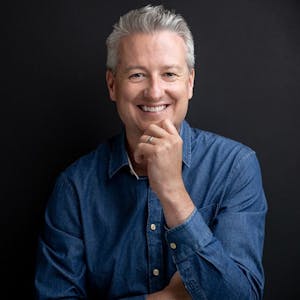