While many companies and manufacturers have existing quality management systems and objectives, advanced product quality planning (APQP) can further enhance product quality, manufacturing efficiency, and customer relations. First introduced in the 1980s in the American automotive industry as a tool to ensure consistent quality from suppliers, APQP has evolved into a robust series of standards for manufacturers across a number of different industries. Companies that have adopted APQP practices have a clearer understanding of customers' wants and needs and can plan accordingly to meet customer expectations. To take advantage of APQP, companies must first understand what APQP is, and familiarize themselves with its standards, audit requirements, and benefits. This article will further discuss APQP certification, relevant definitions, audit requirements, and the benefits of following the process.
What Is an APQP Certification?
APQP (advanced product quality planning) certification is an earned accreditation granted by the Automotive Industry Action Group (AIAG), a non-profit organization comprising thousands of automotive OEMs (original equipment manufacturers) and suppliers globally. Achieving APQP certification show that a company complies with APQP standards and requirements. APQP is one of the five core tools that make up the more comprehensive IATF (International Automotive Task Force) 19649 standard.
APQP certification requires companies to satisfy stringent requirements related to the establishment and adherence to product quality planning guidelines. Adhering to the APQP process helps minimize the risks of product and manufacturing failures, leading to improved quality control, better customer relations, and faster time to market.
For Which Industries and Companies Is APQP Relevant?
APQP largely applies to automotive OEMs and their suppliers. Large OEMs such as General Motors, Toyota, and Volkswagen, and Tier 1 manufacturers use APQP to standardize new product designs. However, since new product designs largely stem from tier-2 and tier-3 suppliers, many of these manufacturers must also adhere to APQP practices. So while many Tier 2 and Tier 3 suppliers do not solely conduct business within the automotive industry, they must also familiarize themselves with APQP.
The Five Phases of APQP
A foundational piece of APQP is the emphasis on customer and manufacturer collaboration. Throughout each stage of the APQP certification process, the two parties are in constant communication to ensure that products and processes are designed with optimal quality and efficiency in mind. There are five well-structured phases of APQP that help manufacturers design and manufacture high-quality products for their customers. The five phases of the APQP are listed below:
- Planning: This phase encompasses scope definition and identification of key stakeholders. Additionally, a large emphasis is placed on customer requirements and expectations. During this phase, manufacturers should collect all the necessary data needed to develop new products per customer requirements.
- Product Design: This stage includes a feasibility study, identification of possible materials for use, and an evaluation of designs using prototypes. Quality tools such as FMEA (failure mode and effects analysis) are used to assess potential failures and their downstream effects. This phase ultimately results in a design that satisfies all the customer’s requirements.
- Process Design: Process design usually occurs simultaneously with product design. During this phase, the focus is placed on designing and developing the processes needed to manufacture products based on customer specifications, quality requirements, manufacturing efficiencies, and cost. This phase usually results in manufacturing process flow documentation, FMEA of processes, and identification of packaging requirements.
- Validation of Product and Process Design: After the product and process design are completed, validation of those designs is conducted. This phase also happens simultaneously with phases 2 and 3 as new products and processes are designed, tested, and verified. During this stage, production trial runs are completed, products are tested based on customer specifications, and necessary adjustments are made to both product and process design.
- Assessment and Launch: The final phase of APQP consists of conducting a final evaluation of designed products and processes. This helps reduce process variations and gets manufacturers in the mindset of continuous improvement. At the end of this stage, full-scale production is underway.
What Are the APQP Audit Criteria?
The APQP audit criteria are used to judge a manufacturer’s ability to establish a standardized holistic method for product development, and their ability to stick to it. Manufacturers first complete internal audits of their own processes to verify compliance with APQP standards. Then, a third party completes an audit to verify compliance. Some common APQP audit criteria are listed below:
- Scope definition, creation of schedule, and identification of major stakeholders.
- Risk assessment.
- Documentation requirements related to product and process requirements.
- Product design and development plans including process flow diagrams and testing plans.
- Product and process validation methods.
- Feedback collection and methods for corrective actions.
The APQP Audit and Accreditation Process
To become APQP-certified, companies must satisfy stringent requirements related to the documentation and processes used during new product development. The audit and accreditation process begins when a company decides to implement APQP practices across its processes. Then, a company will conduct new product development in compliance with the standard practices within the five phases of the APQP. Next, a manufacturer will conduct an internal audit to verify that the standards of the APQP are satisfied. Lastly, an external audit is conducted. From there, the auditor determines whether the manufacturer can become accredited with APQP certification.
What Are the Benefits of an APQP Certification?
There are numerous benefits of APQP certification — from faster time to market, to reduced likelihood of manufacturing errors, to improved customer satisfaction. The benefits of APQP certification are listed and described below:
- Improved Product Quality: APQP focuses on product quality across the entire supply chain from the moment an idea is conceived to its introduction to mass manufacturing. By emphasizing the voice of the customer, standardizing workflows for design and development, and prioritizing proper planning, APQP leads to drastically improved product quality.
- Faster Time to Market: Because APQP places an emphasis on product quality planning —- from inception and initial design to prototyping and production trial runs — manufacturers can achieve faster time to market for new products. Manufacturers, design houses, and customers are in constant communication throughout the entire design process. This ensures that new products are made correctly and rapidly with little error.
- Reduced Likelihood of Manufacturing Errors: Quality is prioritized throughout the entire design of a new product or process and during the series manufacture of products. Since communication between customers and manufacturers is a foundational piece of APQP, customer quality expectations are clearly expressed every step of the way, and manufacturers can tailor their processes accordingly.
- Increased Manufacturing Efficiency: APQP requires manufacturers to put procedures in place to plan for and follow through on each stage of the design, development, and mass manufacture of products. Consequently, the focus on planning and quality in both products and processes leads to increased manufacturing efficiency and shorter product and process development times.
When Are APQP Certifications Required?
While APQP certification is not necessarily required, it is highly recommended for all Tier 1 automotive manufacturers globally. APQP is a requirement established in the IATF 16949 standard which is based on the broader ISO 9001 standard and standardizes quality management systems for automotive manufacturers. Many OEMs require IATF 16949 certification and consequently APQP compliance as a condition of doing business. Additionally, while it is not required for non-Tier 1 automotive suppliers, it is recommended, since it shows customers that a manufacturer respects the product and service quality expectations set in the IATF 16949 standard.
What Accrediting Body Issues APQP Certifications?
The Automotive Industry Action Group (AIAG) issues APQP certifications. The “Big 3” American automotive manufacturers (General Motors, Ford, and Chrysler) first developed the APQP in the late 1980s to standardize the methods by which new automotive products and processes were developed and released into the market. Since then, AIAG has grown to a collection of over 4,000 automotive OEMs and suppliers around the world.
Certifications and Accreditations Similar to APQP
APQP is a comprehensive and robust quality management tool used to enhance productivity and product quality while simultaneously improving customer relations. While there are many different approaches that can be taken to introduce new products, none are as thorough as APQP.
Summary
This article presented the APQP certification, explained it, and discussed its various applications. To learn more about certifications, contact a Xometry representative.
Xometry provides a wide range of manufacturing capabilities and other value-added services for all of your prototyping and production needs. Visit our website to learn more or to request a free, no-obligation quote.
Disclaimer
The content appearing on this webpage is for informational purposes only. Xometry makes no representation or warranty of any kind, be it expressed or implied, as to the accuracy, completeness, or validity of the information. Any performance parameters, geometric tolerances, specific design features, quality and types of materials, or processes should not be inferred to represent what will be delivered by third-party suppliers or manufacturers through Xometry’s network. Buyers seeking quotes for parts are responsible for defining the specific requirements for those parts. Please refer to our terms and conditions for more information.
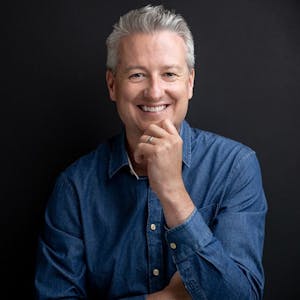