Injection molding and blow molding are both high production volume manufacturing technologies that form plastic into many different shapes and sizes. Injection molding is used for complex solid components whereas blow molding is used for thin-walled hollow parts.
Injection molding forces plastic into a mold under high pressure. Blow molding, on the other hand, expands a hollow tube of plastic into a mold using compressed air. Blow molding is generally cheaper than injection molding. This is because blow molded products are less complex, and therefore the required tooling is cheaper. In addition, injection molding requires heavy-duty hydraulic rams to inject the plastic raw material and to keep the mold from leaking plastic during the injection phase. This article will compare blow molding vs. injection molding in terms of the manufacturing process, materials used, and production rates.
Blow Molding Definition and Comparison to Injection Molding
Blow molding is a process used to create hollow plastic products such as bottles or containers. The most commonly used plastic for blow molding is HDPE (High-Density Polyethylene), although most thermoplastics can be blow molded. Inspired by the techniques used in the ancient art of glass blowing, Enoch Ferngren and William Kopitke invented plastic blow molding in 1938. The next big step in the development of blow molding was the introduction of HDPE in the 1950s. In the 1970s, PET was added to the list of materials that could successfully be blow molded. Both of these materials were significantly easier to process than the earliest materials tried, and the performance characteristics of the end products were also improved.
Blow molding machines work by extruding a tube of softened plastic called a parison. The parison is enclosed and sealed inside by the two halves of the mold. Pressurized air is pumped into the parison, and the softened plastic expands to match the shape of the mold. The flash at the split line of the mold is trimmed after the formed part is released. This excess material is then recycled back into the process.
Blow molding is preferred to injection molding for parts with thin walls, such as bottles, fuel tanks, and consumer product casings. Thin-walled parts are not easily injection molded. The blow molding process can be seen below:
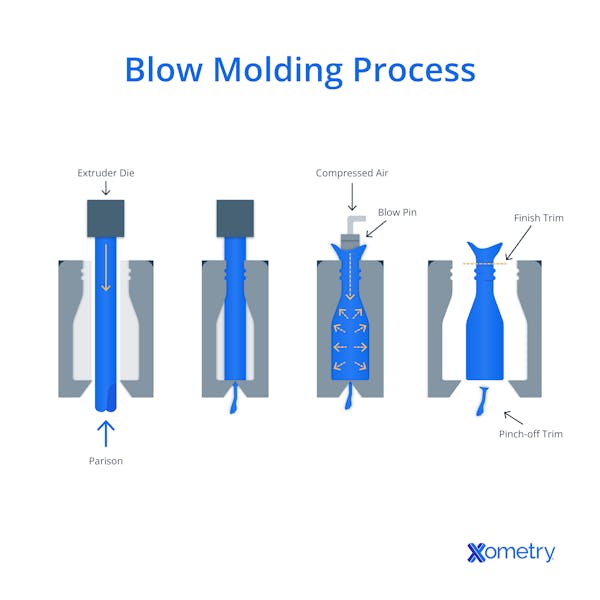
What are the Advantages of Blow Molding Compared to Injection Molding?
Listed below are some advantages of blow molding compared with injection molding:
- Blow molding can produce single-component hollow containers which would be impossible to make with injection molding.
- Blow molding is less expensive than injection molding. Blow molding is performed at lower pressures than injection molding, allowing the use of less expensive tooling and equipment.
What are the Disadvantages of Blow Molding Compared to Injection Molding?
Listed below are some disadvantages of blow molding vs. injection molding:
- Blow molding is only applicable to thin-walled hollow parts. That being the case, it is limited to such applications. It cannot be used for thick-walled products.
- The parison needs to be trimmed off at the top and the bottom of the part after blow molding. Injection molding typically requires no post-processing.
Injection Molding Definition and Comparison to Blow Molding
Injection molding machines work by injecting molten thermoplastic into a two-part mold. The first injection molding machine was developed in 1872 by John Wesley Hyatt. This machine was used to mass produce items like buttons. The first screw injection molding machine, which is what modern machines are based on, was built in 1946 by James Watson Hendry.
The process works by melting plastic resin pellets inside a barrel. The barrel contains a screw with a shaft whose diameter increases along its length. As the screw rotates, the plastic is forced into an incrementally smaller area. This compression is the primary mechanism responsible for melting the plastic. The barrel is also heated to further aid the melting process. Once enough plastic to fill the mold has melted, the screw retracts. The screw is then pushed forward to force the plastic into the mold at very high pressures.
Injection molds are made from at least two parts. They are held together with hydraulic rams so that the high-pressure plastic injected into the mold cannot escape from the parting line. The mold has cooling channels that cool the part enough so that it can be ejected from the mold without damaging it.
Injection molding can achieve high production volumes unmatched by any other plastic processing technique. It can easily produce millions of parts per machine annually. Injection molding can create complex parts. It is used for everything from gears to garden chairs. Injection molding is better than blow molding for the high-volume production of complex plastic parts. To learn more, see our guide on the Molding Manufacturing Process.
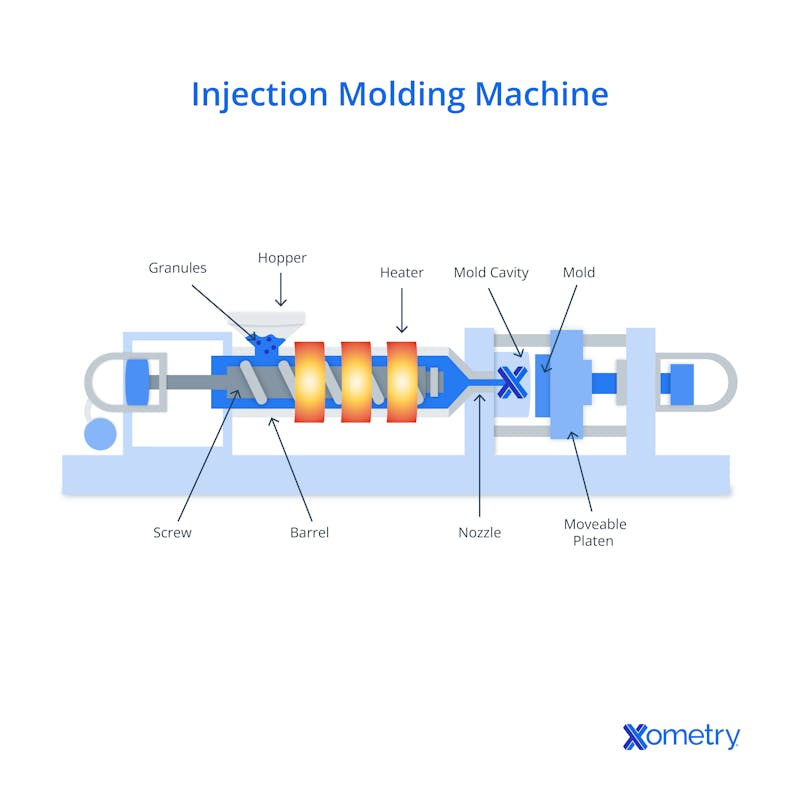
What are the Advantages of Injection Molding Compared to Blow Molding?
Listed below are some advantages of injection molding vs blow molding:
- Injection molding is suitable for high-volume production of complex parts.
- Injection molding produces complex, high-strength parts that are suitable for engineering applications. Blow molding can only produce hollow, thin-walled parts and containers.
What are the Disadvantages of Injection Molding Compared to Blow Molding?
Listed below are some disadvantages of injection molding compared to blow molding:
- Injection molds are very expensive to manufacture for the following reasons: tight tolerances, complex cooling channels, incorporation of multiple moving mold cores for complex parts, and handling very high injection and clamping pressures. The molds also need to be wear resistant.
- Injection molding cannot produce hollow parts like drinking bottles due to geometry constraints. Injection molding is also not well suited to thin-walled parts.
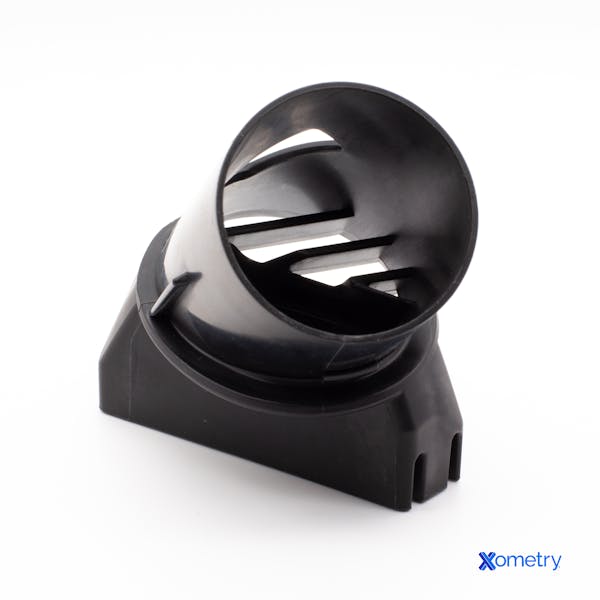
Attribute | Blow Molding | Injection Molding |
---|---|---|
Attribute Can produce thin-walled, hollow parts | Blow Molding Yes | Injection Molding No |
Attribute Typical tooling cost per part number | Blow Molding $1,000 to $100,000 | Injection Molding $10,000 to $1,000,000 |
Attribute No post-processing needed | Blow Molding No | Injection Molding Yes |
Attribute Can produce precision parts for engineering applications | Blow Molding No | Injection Molding Yes |
Attribute Materials that can be molded | Blow Molding Thermoplastics
Thermoplastic elastomers | Injection Molding Thermoplastics,
Thermosets, Thermoplastic elastomers, Thermoplastic polyurethane,
Metal powder in a plastic matrix |
Blow molding produces thin-walled hollow parts, while injection molding produces parts with complex features. Injection molding can also use a wider range of raw materials.
Blow Molding vs. Injection Molding: Lead Cost Comparison
Injection molding and blow molding are used for different types of applications. However, blow molding tends to be cheaper than injection molding due to the cheaper tooling, equipment costs, and lower energy requirements, i.e. injection molding operates at high injection pressures.
Blow Molding vs. Injection Molding: Speed Comparison
Blow molding and injection molding can both produce high volumes of parts, especially in parts that are made in parallel. Both technologies are limited, however, by how quickly the plastic can be cooled to the temperature required to be able to eject parts from the mold without damaging them. Depending on the material, the size of the part, and the effectiveness of the cooling system, parts can be produced in seconds or minutes.
Blow Molding vs. Injection Molding: Volume Comparison
Blow molding and injection molding are both high production-volume manufacturing technologies. Blow molds are inexpensive. Because of that, many molds can be built and used to carry out "parallel production," compensating for slow cycle times, and allowing large-volume production. Injection molds are significantly more expensive. Producing multiple molds for parallel production is cost prohibitive. However, multi-cavity molds are possible to reduce costs while increasing production capacity. Both technologies are capable of producing millions of parts per machine annually.
Blow Molding vs. Injection Molding: Materials Comparison
Both blow molding and injection molding can make use of most thermoplastics. Polyethylene is widely used for blow molding applications due to its useful mechanical and chemical properties as well as its ease of manufacture.
Injection molding can make use of a wide range of polymers, including thermoplastics, thermoplastic elastomers, and thermoplastic polyurethane. Even metal powder bound in a polymer matrix can be injection molded.
Common FAQs on Blow Molding and Injection Molding
What are the Mutual Alternatives to the Blow Molding and Injection Molding?
Injection molding and blow molding are different from each other. However, listed below are some mutual alternatives:
- Vacuum Forming: Vacuum forming can produce thin-walled parts by sucking a soft plastic sheet over a form. Vacuum forming can produce large hollow parts.
- 3D Printing: While 3D printing is a low production volume technology, it is capable of producing complex parts.
What are the Similarities Between Blow Molding and Injection Molding?
Listed below are some similarities between blow molding and injection molding:
- Both injection molding and blow molding make use of thermoplastics in order to produce parts.
- Injection molding and blow molding are both high-volume production technologies that can easily produce millions of parts per year.
What are the Other Comparisons for Blow Molding Besides Injection Molding?
Below is an alternative to blow molding:
- Blow Molding vs. Rotomolding: Rotomolding is a process used to manufacture hollow, thin-walled components. The raw material is placed inside a mold, is heated, and is spun along multiple axes to evenly distribute the polymer into the mold
What are the Other Comparisons for Injection Molding Besides Blow Molding?
An alternative to injection molding is:
- Injection Molding vs. Casting: Injection molding is unmatched in terms of cost and production volume. However, casting polymers is a possible alternative, especially with low production volumes. Polyurethane and thermoplastics, like castable nylon, can be used. The process involves heating the liquid material and then pouring it into the mold. Castable plastics have relatively low viscosities. Casting is just injection molding with no pressure applied.
Summary
Xometry provides a wide range of manufacturing capabilities including CNC machining, 3D printing, injection molding, laser cutting, and sheet metal fabrication. Get your instant quote today.
Disclaimer
The content appearing on this webpage is for informational purposes only. Xometry makes no representation or warranty of any kind, be it expressed or implied, as to the accuracy, completeness, or validity of the information. Any performance parameters, geometric tolerances, specific design features, quality and types of materials, or processes should not be inferred to represent what will be delivered by third-party suppliers or manufacturers through Xometry’s network. Buyers seeking quotes for parts are responsible for defining the specific requirements for those parts. Please refer to our terms and conditions for more information.
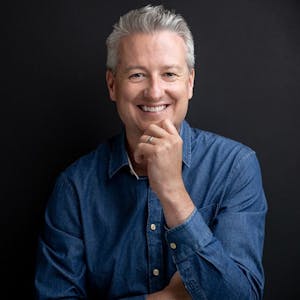