Two manufacturing methods that are prevalent in most industrial manufacturing processes are injection molding and vacuum forming. Factors such as material choice, speed and scale of production, and cost of machinery affect the decision of which method to employ for certain applications. Injection molding works by injecting a melted thermoplastic material into a mold. Afterward, the material cools down – and the plastic part is formed. In vacuum forming, heat is applied to the thermoplastic material until it becomes soft (not melted). This material is then stretched across a surface bearing the details of the required design.
The injection molding tool is more expensive to set up compared to its vacuum forming counterpart. However, when the speed of production is taken into account, vacuum forming is often the preferred choice. The reason is that the mold in injection molding takes a large chunk of time to complete. One benefit of injection molding is that it allows for greater complexity in designs; that is, more intricate shapes can be formed; whereas vacuum forming allows for design flexibility. This article will compare injection molding vs. vacuum forming – their processes, advantages, disadvantages, and alternatives.
Injection Molding Definition and Comparison to Vacuum Forming
Injection molding is a plastic forming process that involves the liquefaction or melting of pellets of thermoplastic or polymer material. The resulting substance is then forced or injected through a pressurized nozzle into a mold cavity where it takes shape. Afterward, the injected material cools down, solidifies, and is finally ejected. The year 1872 saw the creation of the first injection molding device. This was the brainchild of John and Isaiah Hyatt who used it in the production of small items such as combs, and buttons. Apart from its many benefits, injection molding is capable of larger production runs compared to vacuum forming. For more information, see our article on what is injection molding.
What are the Advantages of Injection Molding Compared to Vacuum Forming?
Some of the advantages of injection molding over vacuum forming are:
- Injection molding can produce more intricate designs than vacuum forming.
- Fully automated processes can be achieved with injection molding.
What are the Disadvantages of Injection Molding Compared to Vacuum Forming?
Some of the disadvantages of injection molding over vacuum forming are:
- Injection molding is not a convenient tool for large-scale designs. This is where vacuum forming comes into its own: the tool is relatively easy to design and production parts can be scaled up to a preferred size.
- The setup or tooling costs for injection molding are on the high side compared to vacuum forming.
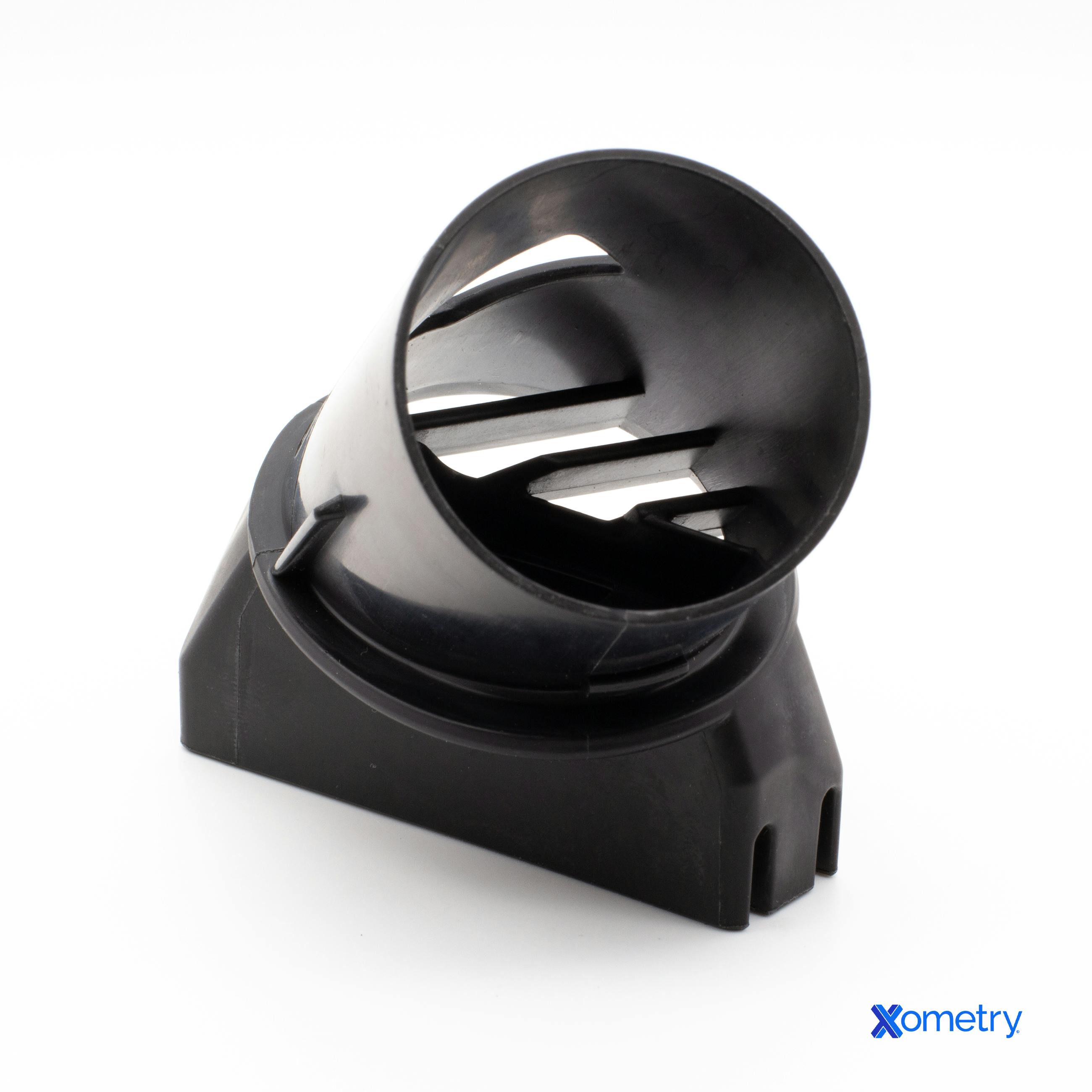
Vacuum Forming Definition and Comparison to Injection Molding
Vacuum forming, also referred to as thermoforming, is a production method that employs the use of a vacuum to stretch a heated sheet (malleable thermoplastic) across the surface area of a mold. After cooling to a considerable extent, the plastic hardens and the resulting item is taken out and trimmed to the exact shape. The production of the first reel-fed vacuum forming machine dates back to 1938. It was masterminded by the Klaus B Strauch Company. Vacuum forming is preferred over injection molding when a low number of production parts are required – typically less than 3,000.
What are the Advantages of Vacuum Forming Compared to Injection Molding?
Some of the advantages that make vacuum forming a preferred alternative compared to injection molding are:
- Vacuum forming allows for easy flexibility in designs compared to injection molding.
- When the rapid prototyping of designs is required, vacuum forming is the best choice.
What are the Disadvantages of Vacuum Forming Compared to Injection Molding?
The disadvantages of vacuum forming compared to injection molding are:
- From a design standpoint, vacuum forming comes behind injection molding. Injection molding produces parts with greater detail than vacuum forming.
- It is not a cost-efficient method for large production of parts.
Attribute | Injection Molding | Vacuum Forming |
---|---|---|
Attribute Better suited for intricate designs | Injection Molding Yes | Vacuum Forming No |
Attribute Allows for larger designs of parts | Injection Molding No | Vacuum Forming Yes |
Attribute Larger production runs | Injection Molding Yes | Vacuum Forming No |
Attribute Poor design flexibility | Injection Molding Yes | Vacuum Forming No |
Attribute Lower tooling cost | Injection Molding No | Vacuum Forming Yes |
More accurate and intricate designs can be achieved with injection molding. However, vacuum forming is better suited for designs that may require changes at specific times.
Injection Molding vs. Vacuum Forming: Lead Cost Comparison
The mold-creation process makes it very expensive to set up an injection molding machine. This is not the case with vacuum forming, which has a low tooling cost.
Injection Molding vs. Vacuum Forming: Speed Comparison
Injection molding has a higher lead time compared to vacuum forming. This makes vacuum forming the best choice for rapid prototyping of designs; it is a more convenient time-to-market manufacturing method. The lead times of injection molding and vacuum forming are anywhere between 12–16 and 6–8 weeks respectively.
Injection Molding vs. Vacuum Forming: Volume Comparison
Injection molding shines when it comes to high-volume production. It is more viable to use injection molding in the production of a large number of parts. The reason is that when production parts get to a value above 3,000 it becomes expensive to use a vacuum forming machine. This is due to the relatively short life span of molds used in vacuum forming, some of which deteriorate due to the frequent heating/cooling and the forces involved during production.
Injection Molding vs. Vacuum Forming: Materials Comparison
Injection molding allows a wider range of materials compared to vacuum forming, supporting a variety of materials such as: chemical-resistant plastics, biodegradable plastics, thermoplastic rubber, and antistatic plastic. Vacuum forming on the other hand works with a limited range of materials (sheets) which include ultraviolet-stable PETG (polyethylene terephthalate glycol), PP (polypropylene), and PVC (polyvinyl chloride).
What are the Mutual Alternatives to Injection Molding and Vacuum Forming?
An alternative to injection molding and vacuum forming is 3D printing, which is a method of creating objects by the successive addition of layers of the 3D model as represented on a computer. 3D printing bears a resemblance to injection molding when it comes to design complexity. They are both used to produce intricate designs. However, when the rapid prototyping of designs is of high importance, either 3D printing or vacuum forming will do.
Common FAQs About Injection Molding vs. Vacuum Forming
What are the Similarities Between Injection Molding and Vacuum Forming?
Injection molding and vacuum forming have some similarities which make either of them suitable for the same applications:
- In both cases, heat is applied. For injection molding, the thermoplastics are heated until they melt, while those of vacuum forming are heated until they become malleable (soft).
- Both processes use thermoplastics in the production of parts for the end users.
What are the Other Comparisons for Injection Molding Besides Vacuum Forming?
Apart from vacuum forming, another comparison for injection molding is:
- Injection Molding vs. CNC Machining: CNC machining is a subtractive manufacturing method that involves the removal of parts (through cutting tools operating at a high speed) from a block of material (workpiece) until the final object is formed. Like injection molding, CNC machining can also produce parts rapidly and can process many of the same materials.
What are the other Comparisons for Vacuum Forming besides Injection Molding?
Apart from injection molding, another comparison for vacuum forming is:
- Vacuum Forming vs. Pressure Forming: Like vacuum forming, pressure forming is a common plastic thermoforming manufacturing technique. In both processes, a thermoplastic sheet is secured and heated in an oven. The difference, however, is in the method of applying pressure/vacuum to transform the heated plastic sheet into the desired part.
Summary
This article presented injection molding vs. vacuum forming, explained each of them, and discussed how each of them work and their differences. To learn more about injection molding and vacuum forming, contact a Xometry representative.
Xometry provides a wide range of manufacturing capabilities and other value-added services for all of your prototyping and production needs. Visit our website to learn more or to request a free, no-obligation quote.
Disclaimer
The content appearing on this webpage is for informational purposes only. Xometry makes no representation or warranty of any kind, be it expressed or implied, as to the accuracy, completeness, or validity of the information. Any performance parameters, geometric tolerances, specific design features, quality and types of materials, or processes should not be inferred to represent what will be delivered by third-party suppliers or manufacturers through Xometry’s network. Buyers seeking quotes for parts are responsible for defining the specific requirements for those parts. Please refer to our terms and conditions for more information.
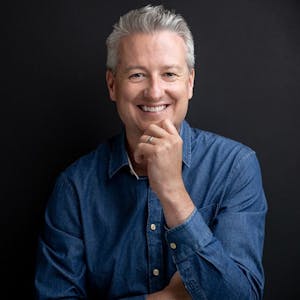