As a process that can make complex, lightweight, yet durable plastic products, it’s little wonder why reaction injection molding (RIM) is so widely used for making parts for many industries, including automotive, electronics, marine, medical, aerospace, and consumer goods. Let’s learn more about it.
What is Reaction Injection Molding?
RIM is a manufacturing process for making single-part products with many complex features like ribs, bosses, curves, and undercuts. It offers design freedom and flexibility and produces parts with excellent strength-to-weight ratios. RIM can make parts with mixed large and small wall thicknesses, complex and large undercuts, foam core inserts, and very large moldings—features that are much harder to achieve with many other manufacturing methods (although sometimes very large parts could produce challenges in fill/cure processes).
RIM parts have excellent cosmetic finishes straight from the mold, though they can also be coated, painted, or textured if needed. Unless the detail is very fine (in which case it could be hard to reliably reproduce), RIM has no problem with complex designs. The parts are strong, resilient, and mechanically, chemically, and environmentally durable (as long as you’ve chosen the right material for the intended application).
RIM parts are among the toughest large plastic components and can have very long functional life expectancies. For example, aircraft interiors in commercial planes—which generally show cosmetic wear and tear but are still serviceable—are commonly kept in service for 5–15 years, depending on the policies of the airline. RIM car parts can be expected to last as long as the car does (sometimes longer), which is around 7–15 years.
Setup costs are high but significantly lower than injection molding. However, once production starts, per-part costs remain low. Large parts with integrated inserts can serve multiple purposes and be made from relatively low-cost materials. It’s quick, too! The only real qualm is that the tools used in the process aren’t as durable as they could be, so they are fairly easy to damage. Below are just a few of the parts that can be made via RIM.
Automotive | Electronics | Marine | Medical | Aerospace | Consumer Goods |
---|---|---|---|---|---|
Automotive Body kits and spoilers | Electronics Enclosures | Marine Fenders | Medical Equipment enclosures | Aerospace Interior/exterior parts | Consumer Goods Furniture |
Automotive Body and door panels | Electronics Housings | Marine Engine housings | Medical Device housings | Aerospace Armrests | Consumer Goods Appliances |
Automotive Instrument panels, dashboards | Electronics Structural components | Marine Seating | Medical Orthopedic aids | Aerospace Overhead storage bins | Consumer Goods Tool handles |
Automotive Interior trims | Electronics - | Marine Storage Bins | Medical Patient comfort parts | Aerospace Cabin panels and ducts | Consumer Goods Sports equipment |
Parts Manufactured with Reaction Injection Molding
Type of Material | Characteristics/Benefits | Examples | Applications |
---|---|---|---|
Type of Material Polyamides | Characteristics/Benefits Low viscosity during processing makes high-molecular-weight nylon, elastomer-modified for improved flexibility, high strength and stiffness/toughness balance, good fatigue- and abrasion-resistance, good paintability, and is thermoplastic once molded so allowing for recycling | Examples Nyrim® (nylon 6) | Applications Car and industrial parts, protective casings |
Type of Material Fiber Composites | Characteristics/Benefits Uses pre-formed mats of glass or carbon fiber for reinforcement, low-viscosity precursors fully encapsulate fibers, enhanced strength, stiffness, and durability, reduced weight while keeping the structural integrity | Examples Glass/carbon fiber composites | Applications Automotive panels, aerospace parts, and structural components needing high strength-to-weight ratio |
Type of Material Polyurethanes (PU) | Characteristics/Benefits Highly versatile, customizable hardness, flexibility, and impact resistance, excellent chemical resistance and thermal stability, can provide high-quality surface finishes, can easily be colored, painted, or textured | Examples Rigid/flexible PU foam, structural PU composites | Applications Vehicle bumpers, medical device housings, industrial equipment enclosures |
Type of Material Silicone | Characteristics/Benefits Highly resistant to extreme temperatures and chemicals, high elongation and flexibility, good electrical insulation, good biocompatibility for medical applications | Examples Liquid silicone rubber (LSR) | Applications Medical implants and seals, electrical insulators, high-temp industrial parts |
Type of Material Polyester | Characteristics/Benefits Cost-effective, customizable properties, good strength, durable, resistant to impact, chemicals, mechanical stress, and abrasion, dimensionally stable | Examples Unsaturated polyester resins, thermoset polyester composites | Applications Car components, construction materials, marine applications |
Materials Suitable for Reaction Injection Molding
How it Works
RIM uses the simultaneous injection of two or more reactive liquid components into a mold cavity. These liquid (monomer) components, typically a polyol (resin) and an isocyanate (hardener), are precisely metered, thoroughly homogenized, and mixed in a specialized mixing head, then injected into the cavity of a mold at low pressure (up to 10 MPa). The mold is typically made of two halves but could have more sections for undercuts and other more complex details. During and after injection, the liquid components will go through an exothermic reaction, which may include degassing/foaming.
In some cases, a monomer component contains dissolved gas that expands during polymerization, creating a closed-cell foam instead of a solid structure. The mixture then solidifies inside the cavity in a process that goes by relatively quickly—cycle times are commonly just 30–60 seconds long. The thickest part sections that it is practical to manufacture by RIM are generally reported as half an inch thick. Having said that, localized thickening and occasional parts are molded to thicknesses approaching 5 inches without major difficulties.
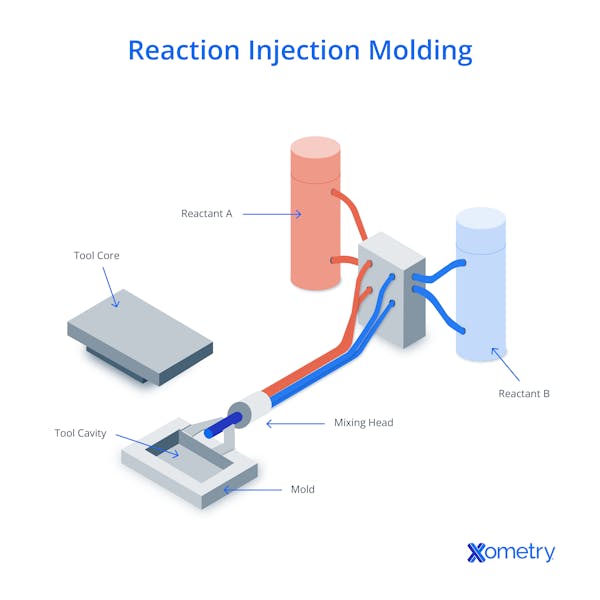
Type | Description | Process | Best For |
---|---|---|---|
Type RIM | Description Standard RIM process using liquid precursors | Process Low-viscosity liquid components are mixed and injected into a mold, where they chemically react and solidify | Best For Lightweight, durable parts with complex geometries for automotive, medical, industrial, and consumer |
Type SRIM | Description RIM with added structural reinforcement (e.g., glass or carbon fibers) for increased strength, stiffness, and deformation resistance | Process Similar to RIM, but structural reinforcements are placed in the mold before injection | Best For Large, high-strength structural parts (e.g., automotive panels, aerospace, industrial equipment) |
Type RRIM | Description RIM with short-strand reinforcing materials (e.g., chopped glass or carbon fibers) mixed into the liquid resin for enhanced durability and impact resistance | Process Reinforcing agents are mixed into the resin before injection for uniform distribution | Best For Same range of industries and applications as RIM and SRIM, mainly for parts with higher strength, stiffness, or resilience |
Types of Reaction Injection Molding
Equipment
A RIM machine, or RIM press, consists of six key systems:
- A hopper or bin system for storing the pre-mixed chemicals.
- A metering and mixing system that precisely meters and homogenizes the liquid components in the correct ratio.
- An injection system (usually a hydraulic or electrically-driven piston) pumps the mixed liquid into the mold cavity.
- A heating system to keep the liquid components at the proper temperature.
- A mold clamping system (hydraulic, pneumatic, or mechanical screw) that aligns the mold halves, keeps the mold in place, and resists the injection pressure during the process.
A PLC or CNC-type control system that monitors and regulates machine parameters, i.e., fluid volume/ratio, temperature, pressure, injection time, and mixing ratios.
FAQs on Reaction Injection Molding
RIM vs. injection molding—what’s the difference?
While both RIM and injection molding are used to make plastic parts, they differ quite a bit in materials, process conditions, and applications. RIM uses liquid reactive polymers (e.g., polyurethane, epoxy, silicone) that chemically solidify, while injection molding uses melted thermoplastics that harden upon cooling. RIM operates at low pressure (<10 MPa) and moderate temperatures (60–120°C), but injection molding needs high pressure (up to several hundred MPa) and high temperatures (up to 400°C).
In addition, RIM molds are made from aluminum or composites, which are cheaper and faster to make. Injection molding, on the other hand, requires more durable, expensive molds to withstand extreme pressures and temperatures. These typically cost 10–20 times more. That said, injection molding is great for high-volume, fast-cycle production, while RIM is better for low-volume runs, prototyping, and complex designs.
Does RIM and injection molding use the same equipment?
No, RIM and injection molding use entirely different equipment. RIM machines are highly specialized equipment designed specifically for the RIM process, and aren’t suited to any other task. They are quite different from conventional injection molding machines and more closely related to epoxy resin mix/metering systems for potting applications.
How Xometry Can Help
For any more information or personalized advice on reaction injection molding or similar processes, reach out to one of our representatives. Xometry provides a wide range of manufacturing capabilities including CNC machining, 3D printing, injection molding, laser cutting, and sheet metal fabrication. You can get started today by uploading your designs to the Xometry Instant Quoting Engine®!
Disclaimer
The content appearing on this webpage is for informational purposes only. Xometry makes no representation or warranty of any kind, be it expressed or implied, as to the accuracy, completeness, or validity of the information. Any performance parameters, geometric tolerances, specific design features, quality and types of materials, or processes should not be inferred to represent what will be delivered by third-party suppliers or manufacturers through Xometry’s network. Buyers seeking quotes for parts are responsible for defining the specific requirements for those parts. Please refer to our terms and conditions for more information.
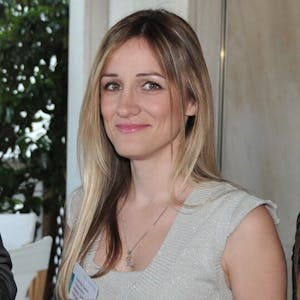