Metal Parts Manufacturing - How to Make Custom Metal Parts
Engineers and designers need to understand a part’s materials, manufacturing processes, and use cases to determine appropriate methods for creating them. This is an overview of 8 different manufacturing processes you can utilize to create custom metal parts.
Metal parts are unique to individual industries and applications. Engineers and designers need to understand a part’s materials, manufacturing processes, and use cases to determine appropriate methods for creating them.
How metal parts are made can vary significantly. Each process has its own strengths, compatible materials, and trade-offs. A deeper understanding of the range of production methods will improve this decision-making process. This is an overview of 8 different manufacturing processes you can utilize to create custom metal parts. These are:
- CNC milling and CNC turning
- Extrusion
- Metal casting
- Die casting
- Metal injection molding
- Forging
- Sheet metal and stamping
- Metal 3D printing
1. CNC Milling and Turning
There are two main types of CNC machining technologies. CNC mills are automated cutting machines. They cut away unwanted material with a rotating spindle head. Turning spins material against a stationary tool to remove material into the desired shape. They work well with a range of materials, including plastic, aluminum, stainless steel, and titanium.
How CNC Machining and Turning Works
CNC turning involves the use of either CNC lathes or multi-axis CNC turning centers. Manufacturers use CNC lathes to turn materials for cylindrical and concentric features on parts. Live tooling lathes incorporate end mill cutting tools and drills to produce off-axis features without the need to change platforms. Specialized CNC-lathes, often called Swiss machines, are designed to produce small parts with complex features quickly by combining multiple tools and spindles within the machine.
A typical lathe will rotate the part on a central axis to remove features by engaging rigid cutting tools. Other features performed by a lathe include the creation of internal and external threads, creating flanged features, O-ring grooves, and knurled textures.
CNC lathes and CNC mills have different axis configurations. CNC lathes are typically 3- or 4-axis machines with a single spindle. 3-axis CNC machining works materials on X, Y, and Z axes, removing shavings along these three directions. 4-axis tools incorporate movements outside of concentric features on lathes and a tilt on mills. Lathes are ideal for circular parts and are more operationally intensive for irregular shapes and sharp edges, the reverse for mills.
More modern CNC technologies support up to 5 axes. These tools add tilt and rotation to traditional X, Y, and Z axes, enabling precise cutting for more detailed parts. 5-axis machining is also more efficient as it can create more part features in a single operation. Mills are available in several configurations, often employing 3-, 4-, and 5-axes.
CNC stands for Computer Numeric Controlled, and operators control CNC mills and lathes with G-Code—a programming language that provides machine-movement instructions. Modern programming instructions are created through computer-aided manufacturing (CAM) software. This code instructs the machine where to move the tool head. It also controls its speed and feeds, which are rotation, cut depth, and workpiece movement. The G-Code complexity depends on the machine’s number of axes and the toolsets used.
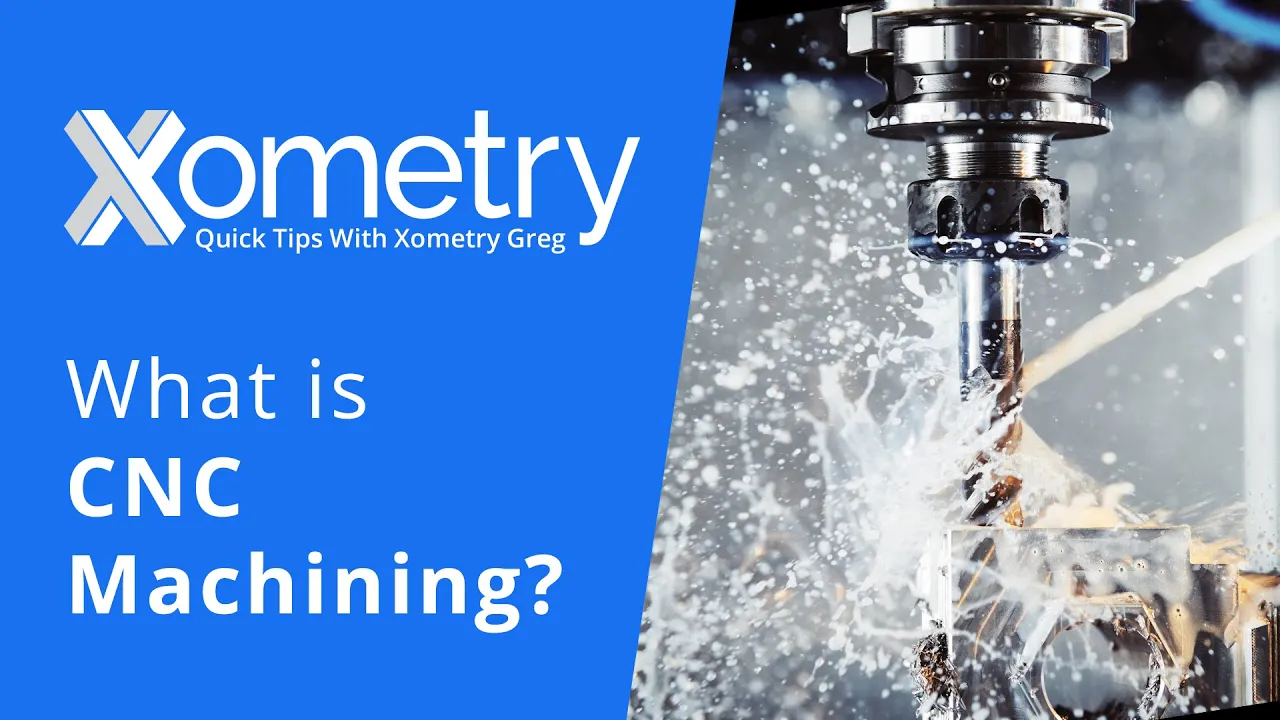
CNC Materials
CNC mills and CNC lathes work well with similar materials. These include aluminum, brass, bronze, copper, steel, stainless steel, titanium, and zinc alloys. These tools also work well with plastic and composites such as acetal, ABS, G-10, and performance materials like PEEK or PTFE.
CNC Use Cases and Industries
CNC mills are the workhorses of the manufacturing world since they are both precise and repeatable. This means they are ideal for rapid prototyping and low- to high-volume production. Their versatility with materials makes them ideal for almost any job.
CNC lathes are similarly versatile. Production with lathes also requires fewer setups for hands-free operations, which makes them efficient options for a range of use cases. The shape of the part and specified tolerances typically determines which of the two methods to use—with parts with concentric features requiring lathes and angular pieces requiring milling.
Industries that use CNC machining include:
- Aerospace and defense
- Automotive
- Consumer products
- Electronics
- Industrial
- Medical and dental
- Robotics
Visit our CNC Milling Service and CNC Turning Service pages for more information about stock, finishes, applications, and other process advantages.
Unsure Which Manufacturing Process to Use? Get our Free White Paper Today.
2. Extrusion
Extrusion involves pushing heated metal or plastic through a die. In practice, it resembles squeezing a tube of toothpaste. The die creates a net shape, such as a tube, L-structure, or more complex features. Metal part extrusion typically requires post finishing, such as cutting, drilling, or machining. It’s ideal for high volumes of parts that require constant cross-sections.
That’s because extrusion profiles can be almost any shape with a continuous cross-section. A great example is framing for windows, with multiple features to secure different panes in the assembly. They can even be hollow, such as square, round, or hexagonal tubing. Manufacturers determine its form when creating the shape of the die.
How Extrusion Works
The three types of extrusion are hot extrusion, cold extrusion, and friction. Hot extrusion involves high temperatures to keep work material from hardening. Cold extrusion involves near room temperatures, which provides some advantages over hot extrusion. The material may be stronger, have less oxidation, or have closer tolerances. Finally, friction extrusion involves the use of force to push the charge against the die.
Extrusion Materials
Extrusion materials can be either plastics or metals. Roughly 80% of extruded metal parts are aluminum alloy. Meanwhile, polyethylene is most common in plastic extrusions.
Use Cases and Industries
Extrusion is a simple process compared to other methods. Its tooling costs are 80% to 90% less than injection molding and die casting. Extrusion provides smoother surfaces for paints and finishes as well. This makes extrusion ideal for precision and cosmetic parts. Flooring, windows, and railing are ideal applications. Automotive and aerospace components are ideal for extrusion as well.
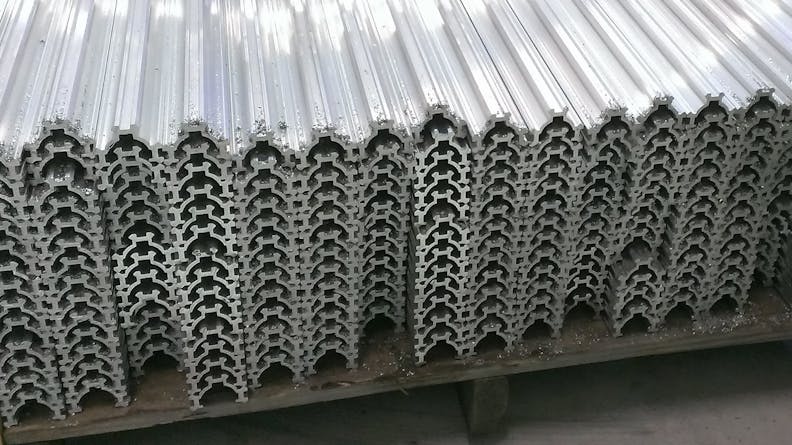
Extruded Aluminum Parts
3. Metal Casting
Metal casting is a long-standing manufacturing process. It involves pouring liquid metal into a mold. The liquid metal hardens in the form of the desired shape. It is then cooled and extracted from the mold.
Modern metal casting is precise, automated, and uses advanced tools. But its principles remain the same. Its wide use is a testament to the success of this method.
How It Works
The metal casting process begins with patternmaking. Patterns create part-shaped voids in the mold prior to pouring in the liquid metal. Modern patternmaking methods use precise calculations to achieve the desired shape. This can include scaling to account for shrinkage as well as having an excess material thickness in preparation for post CNC finishing.
In many cases, the mold is destroyed during the casting process. This is a planned step when sand casting, where a cast formed from sand is broken apart to reveal the finished part. New sand casting molds are easy to make, and sand is often reclaimed to create new molds.
Metal casting may also involve the use of wax in a process called investment casting. Manufacturers start by building a wax model of the final product. The wax is covered in layers of ceramic before the wax is heated and removed. The ceramic shapes the mold, its interior imprinted with a pattern shaped by the wax.
Each of these two techniques has benefits. Sand casting is a simpler process, for example, and easy to repeat. Investment casting requires more preparation but may perform better when creating intricate parts. Sand casting is often more costly; investment casting requires more labor to change a given design. Manufacturers must determine the best process given their budget and labor limitations, and the qualities they want for their parts.
Metal Casting Materials
Metal casting is a versatile process. It supports parts from any metal stock that can achieve liquid form. That’s why engineers across industries use a range of materials in metal casting. Aluminum, magnesium, and copper alloys are among the most common. But manufacturers also use zinc, steel, and other metals.
Casting Use Cases and Industries
Nearly every commercially produced mechanical device today uses some form of casting. In serial production, casting typically outperforms CNC machining on costs and throughput. Metal casting can achieve high tolerance structural components for a variety of use cases. Washing machines, automobiles, and metal pipes all use metal casting.
4. Die Casting
Die casting is ideal for high volumes of complex metal parts. Die casting uses steel molds and low-melting-point metals as materials. Engineers utilize die casting for sophisticated projects where accuracy, reliability, and production-level throughput are critical. Die casting uses reusable hard tooling similar to the injection molding process, giving parts smoother surface finishes while maintaining low cost in mass quantities.
How It Works
In die casting, liquid metal is forced into a mold via high-hydraulic or pneumatic pressure. This differs from traditional metal casting where the metal is poured. Manufacturers favor die casting when making parts with intricate details. The use of pressure makes creating intricacies more effective.
Hot-chamber, or “gooseneck,” die casting is the most popular method. “Gooseneck” describes the shape of the metal feed system that delivers molten metal to the die mold. Manufacturers use cold-chamber die casting to limit machine corrosion. This method involves ladling molten metal into the injection system instead. In each of these methods, the process is similar to plastic injection molding where the steel tool is closed and the part material flows into the mold cavity to harden in the form of the part. Once hardened, the tool opens up and the part is either dropped mechanically or manually removed.
Die Casting Materials
Die casting manufacturers often specialize in individual materials, including aluminum, zinc, or magnesium. This is because the feedstock is molten metal juxtaposed to the dedicated die casting machine. Roughly 80% of die-casted parts are made of aluminum. Zinc alloy, another low-melting temperature metal, is also a common material used in die casting.
Use Cases and Industries
Die-casted parts are versatile. They are strong and resistant to high temperatures. They also feature smooth or textured surfaces. Die casting favors high production volumes, where it typically can outcompete CNC and investment casting. This supports a wide range of paints, plating, and finishes. Still, die casting is ideal for use with high-impact, high-stress equipment where strength is essential.
Contact Xometry's support team to inquire about Xometry's die casting services.
5. Metal Injection Molding
Injection molding is most common for creating plastic parts. But manufacturers use injection molding services for metal parts as well. It is cost-efficient for large-scale projects, even with high precision. Although it is ideal for projects that require small parts, metal injection molding, or MIM, can be used for parts of any size.
How It Works
Unlike die casting, metal injection molding uses a feed of polymer-metal mix, where the melted plastic allows the material to flow when heated. The material is also pressurized during this process. The machine injects the liquid material into the mold. The material cools and takes the form of the mold to make the part.
After molding, the parts are in a “green state,” meaning that they are in the right shape but are very fragile. A post-sintering process completely ablates the plastic, leaving only fused metal behind. During this furnace process, typically done in a vacuum furnace, the part shrinks a considerable amount.
MIM Materials
Metal injection molding can be used with metals common to other manufacturing processes. However, the process requires those metals to be powdered and blended with the polymer for injection. In this way, parts can be quickly shaped and produced in large production batches.
Use Cases and Industries
Metal injection molding resembles plastic injection molding processes for creating parts. But the high-pressure nature of injection molding adds key benefits. It is effective for parts with small, complex details. This would be too costly for standard CNC machining processes at scale. That’s why metal injection molding is ideal for the medical, aerospace, automotive, and defense industries.
Injection molding tooling can be used longer than die casting and other metal manufacturing methods, allowing higher counts of parts before replacement or maintenance. MIM typically outcompete die casting on smaller parts in serial production or where finer part detail is required. This makes it suitable for repetitive processes at scale. It provides manufacturers greater flexibility in terms of strength and unique characteristics as well.
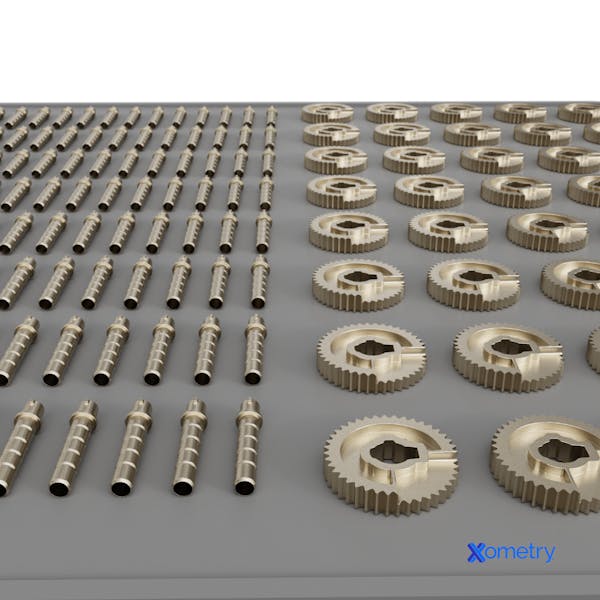
6. Forging
Like metal casting, forging has been used for centuries. It is the process of heating and shaping metal parts by force. The familiar image of a blacksmith and anvil comes to mind. Today, forging is widely used in automated industrial processes.
How It Works
Modern forging uses high-impact machines to shape metals into desirable results. Forging produces less waste than other methods, which makes it more cost-effective for practical applications.
Forged parts are often stronger than parts from other methods. That’s because forging takes advantage of the natural grain of its materials. Materials do not need to be reduced to liquids when molded in a forge, just heated to a malleable state.
Forging Materials
Stainless steel is among the most common forged materials. Aluminum and bronze are also common forging materials.
Use Cases and Industries
Forging is ideal for any number of industries. Its benefits and limitations make it an ideal process to use alongside other manufacturing materials. Forged tools, such as hammers or wrenches, are common examples of end-use, lifelong components made with this method. Manufacturers should identify use cases where the advantages of forging contribute to better business and production results.
7. Sheet Metal and Stamping
Sheet metal fabrication involves cutting parts from metal sheets. The blanked sheets may then be processed through brakes and die presses to create angular bends and forms, building a 3-dimensional structure. Sheet metal services feature stamping to produce these parts at rapid paces. In fact, stamping is faster than any other metal-working process.
How It Works
Stamping machines cut and bend parts out of sheet metal. Workers feed stamping presses a cut or coil of sheet metal. The machine straightens the metal as it is fed into the press. Strategic application of force allows manufacturers to adapt the shape of parts. Bending applies force at an angle, for example, creating a desired angle in the part. Manufacturers use press brakes for this process, which are available in different sizes and lengths to accommodate the needs of the manufacturer. Sheet metal parts can be welded or riveted to create structural elements. Press-fit inserts, such as PEM inserts, can add mating features like bosses, threads, and more without the need of custom machining.
Sheet Metal Materials
Sheet metal is often made of aluminum, copper, or steel. Sheet metal also has a wide variety of finishes. This includes anodizing, plating, powder coating, and painting.
Use Cases and Industries
Stamping makes sheet metal fabrication highly scalable for any industry. It is ideal for high volumes and low unit costs. High-volume, functional parts like enclosures, chassis and brackets often feature sheet metals.
But the tooling cost for stamping is often higher than with other processes. Still, manufacturers create hundreds of millions of parts in the appliance, electronic, and automotive industries each year. Sheet metal and stamping are uniquely optimal for robotics.
Visit our Sheet Metal Fabrication Service page for more information about stock, finishes, applications, and other process advantages.
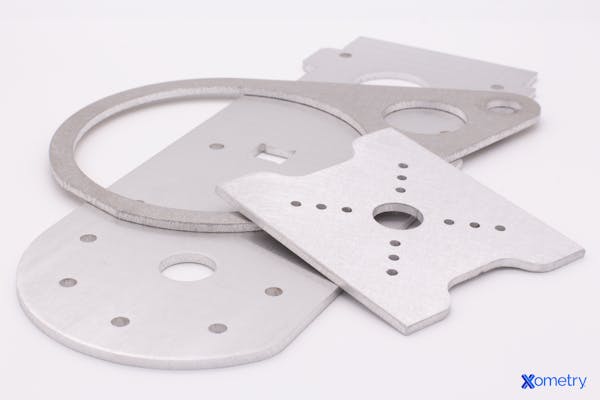
8. Metal 3D Printing
Metal 3D printing services use precise lasers to create metal parts. It is ideal for experimentation and low-volume, high-value parts, but is not as scalable as many of the other metal processes listed. That’s why it is often used for prototypes, as well as substitutes for low-volume casting.
How It Works
3D printing, also known as additive manufacturing, fuses metal in a controlled environment via an energy source. With direct metal laser sintering (DMLS), metal powder is fused layer-by-layer using a laser in an inert environment. Metal binder jetting 3D prints metal parts in a 2-stage process, using an inkjet to bond metal together to a green stage before a secondary furnace process solidifies the metal. Binder jetting can make a metal composite, such as bronze and steel, or a single-alloy, depending on the needs. Metal 3D printing is unique in that it can produce all-in-one assemblies and geometries with inaccessible areas using standard tooling. An example of inaccessible features with traditional processes is building lattice-like structures on a part. This is not possible with traditional molding or casting techniques. Techniques that come close would nonetheless require more time and complexity to produce a single unit.
Metal 3D Printing Materials
The typical stock material for metal 3D printing is atomized powder, but can sometimes be sheet or wire-fed. The printer follows a data path created using a 3D CAD file of the part. Common metal materials include powder in stainless steel, titanium, Inconel, copper, or aluminum materials.
Materials used in metal 3D printers often come from powder metallurgy. Adoption of new materials for metal 3D printers requires significant research to build a robust, and repeatable method of building parts without failure or defects. This means the material choices currently available for metal 3D printing are narrow compared to machining, metal casting, and other fabrication methods.
Use Cases and Industries
Despite its limits, metal 3D printing has near-universal applications. Due to direct digital manufacturing, 3D printed parts can often be produced quickly in low volumes without tooling expenses. Engineers can experiment with 3D printing to preface the production of just about any part, as well as design part features that are specific to applications like lightweight mechanical aerospace components.
Visit our Direct Metal Laser Sintering (DMLS) page or our metal 3d printing service page to learn more about optimizing manufacturing processes with Metal 3D printing.
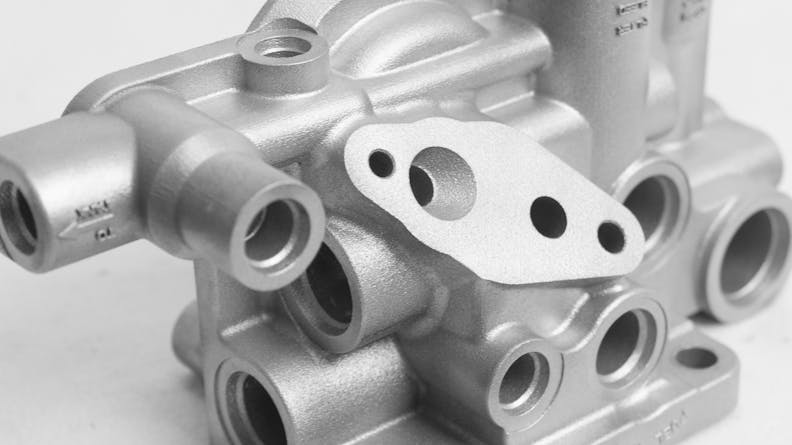
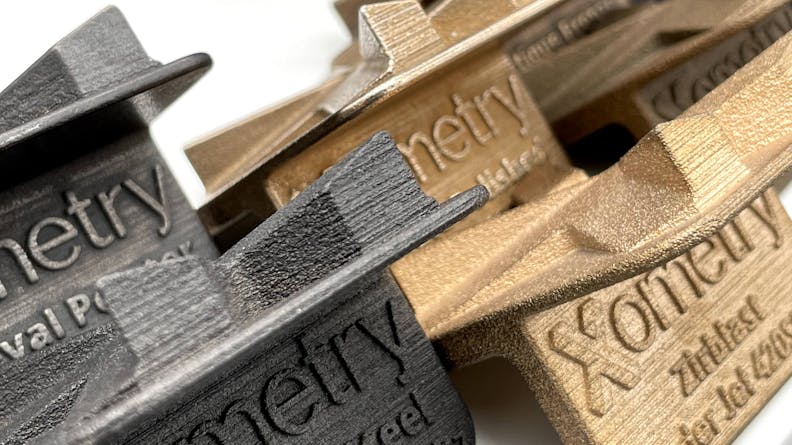
Metal 3D printed parts via laser sintering and binder jetting
Meet All Your Manufacturing Needs with Xometry
How can you order parts in the right manufacturing process? Xometry provides a wide range of manufacturing services for your project. Our manufacturing as a service (MaaS) model is ideal for just about any modern use case.
Xometry supports over a dozen processes through our Supplier Network of professional manufacturers. These include CNC machining services, sheet metal services, and even metal 3D printing services. We use AI-powered instant quoting technology to help you get market-accurate prices and lead times on custom parts, and also offer turnkey materials and supplies, support tooling for your parts, and finishing services for parts from any source. Get a quote today and discover how we can support your diverse manufacturing needs.

